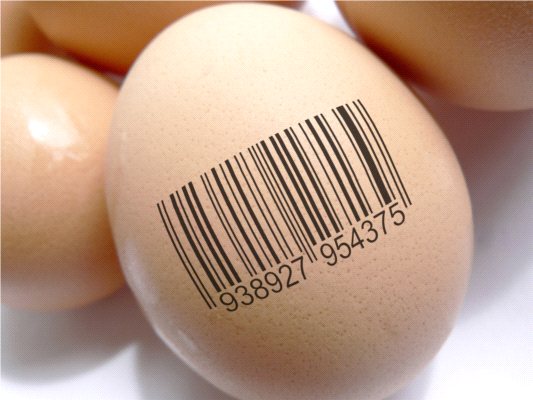
Identyfikowalny produkt
Informacja o procesach produkcyjnych i dystrybucyjnych jest bezcennym kapitałem każdego przedsiębiorstwa. Budować go pozwalają urządzenia automatycznej identyfikacji oparte o systemy RRP lub MES. Producenci i dostawcy urządzeń mobilnych nieustannie wprowadzają na rynek...
Wymagania konsumenta i konkurencja na rynku doprowadziły produkcję, logistykę i dystrybucję do punktu, w którym konieczne stały się inwestycje w nowoczesne technologie IT. Jednym z narzędzi współczesnych procesów wytwórczych są technologie automatycznej identyfikacji. Bez niej wzrost efektywności przepływu i produkcji towarów nie jest dalej możliwy. Dodatkowym czynnikiem wymuszającym inwestycje jest unifikacja standardów przepływu i wymiany danych w całym łańcuchu dostaw. Dodatkowo, tendencja przenoszenia produkcji do państw o tańszej sile roboczej zwiększyła ryzyko wystąpienia niepożądanych sytuacji w łańcuchach dostaw, co zrodziło potrzebę większej kontroli produkowanych i przewożonych towarów. Firmy zrozumiały, że bez permanentnej innowacyjnej zmiany wykluczone staje się utrzymanie wysokiej konkurencyjności. – Nowe technologie to nie tylko inwestycje i koszty. Prawidłowe wdrożenia przekładają się na innowacyjność i coraz większą efektywność, a tym samym na wymierne oszczędności. To determinuje stały wzrost popytu na tego typu urządzenia – potwierdza Katarzyna Muszyńska, sales manager w Wincor Nixdorf.
Producenci i dostawcy technologii automatycznej identyfikacji przyciągają klientów coraz bardziej wydajnymi i funkcjonalnymi rozwiązaniami mobilnymi
Producenci i dostawcy technologii automatycznej identyfikacji, rozumiejąc te aspekty logistyki produkcji, przyciągają klientów coraz bardziej wydajnymi i funkcjonalnymi rozwiązaniami mobilnymi. – Kody kreskowe jedno- i dwuwymiarowe w obecnych czasach stały się jednym z istotnych elementów wspomagających funkcjonowanie systemów zarządzania produkcją oraz całym zapleczem produkcyjnym – podkreśla Patryk Kalita, specjalista Print&Apply w Sato.
Różny klient
Wdrożenie technologii automatycznej identyfikacji stało się więc wymogiem czasów. Kody kreskowe to ogólnoświatowy standard, unifikacja oznaczeń wymusiła zmiany w sposobie myślenia firm produkcyjnych. – Czy można wyobrazić sobie dziś na przykład supermarket bez czytników kodów kreskowych, za pomocą których klient może zweryfikować cenę produktu, lub kasy bez drukarek drukujących paragony lub bez skanera, za pomocą którego kasjerka odczytuje cenę? – zadaje pytanie Patryk Kalita.
Firmy produkcyjne stają jedynie przed dylematem wyboru dostawcy technologii najlepiej spełniającej kryterium potrzeb przedsiębiorstwa. Zdarzają się oczywiście klienci z silnym zapleczem informatycznym, potrzebujący jedynie kilku porad w sprawie planowanego wdrożenia. – Są firmy, które podczas spotkania z konsultantem oczekują informacji o nowych technologiach i możliwościach ich wykorzystania, ale są też przedsiębiorstwa, które mają już problem rozpoznany i przeanalizowany i potrzebują jedynie wsparcia przy implementacji rozwiązania – wyjaśnia Remigiusz Kaczewski, menedżer ds. sprzedaży w SKK.
Wdrożenie technologii automatycznej identyfikacji stało się więc wymogiem czasów
Z drugiej strony producenci technologii automatycznej identyfikacji natrafiają na klientów, którzy potrzebują kompleksowej usługi obejmującej audyt, rozpoznanie problemu i implementację. Zdarza się, że takie firmy w swoim wyborze kierują się często najniższą ceną zakupu. Jest to krótkowzroczna inwestycja, gdyż np. w przypadku drukarek sprzęt niższej jakości wymaga częstszego serwisowania i wymiany drogich głowic. – Technologia nigdy nie jest barierą – liczy się natomiast koszt. Kiedyś taką barierą był pobór prądu czy duże rozmiary urządzeń. Dziś czytniki są małe, energooszczędne i na tyle inteligentne, że potrafią same edytować kod (np. dodawać dowolnie definiowane sufiksy czy prefiksy) – stwierdza Patryk Kalita.
Mimo niestabilnej sytuacji rynkowej większość firm dostarczających na rynek urządzenia do automatycznej identyfikacji osiąga regularny wzrost sprzedaży. Turbulencje rynkowe odbijają się jednak na kontaktach i realizowanych projektach. Czasem firmy wstrzymują zaplanowane wcześniej inwestycje lub przedłużają niemal w nieskończoność proces decyzyjny. – Aktualna sytuacja gospodarcza odbija się echem na podejmowanych przez producentów decyzjach. Bardzo często zarządy wstrzymują inwestycje ze względu na gwałtowne skoki walut czy zmiany przepisów – mówi Remigiusz Kaczewski i dodaje: – Czasami problemem jest przestarzały park maszynowy, który nie pozwala na automatyczne zbieranie parametrów technologicznych. Na szczęście jednak to się już zmienia i polskie firmy coraz częściej dysponują maszynami, które nie ustępują tym posiadanym przez firmy zachodnie.
Szkolenie użytkownika
Przed rozpoczęciem wdrożenia należy pamiętać prostą prawdę, że nawet najlepszy system i narzędzia IT mogą natrafić na barierę ludzką. Pracownicy niższego szczebla mogą dostrzegać w nowej technologii zagrożenie, gdyż nierzadko w ich oczach optymalizacja przepływu towarów może doprowadzić do zwolnień lub przeniesień. Dodatkowo terminal stanowi dla pracownika element kontroli wykonywanej przez niego pracy. – Niejednokrotnie zdarza się, że pracownicy nie chcą lub mają duży problem z zaakceptowaniem zmian, jakie wprowadza pracodawca. Wdrożenie nowych rozwiązań kojarzone jest niejednokrotnie ze zwolnieniami – podkreśla Piotr Rudnicki, specjalista ds. sprzedaży w firmie Koncept-L. Remigiusz Kaczewski dodaje: – Jeszcze kilka lat temu terminal stanowił dla wielu pracowników urządzenie, do którego podchodzili z niechęcią lub obawą. Traktowali to jako narzędzie, które ma pomóc pracodawcy w rozliczaniu ich z pracy. Poza tym zawsze był strach przed nową technologią czy uszkodzeniem urządzenia. Czasami zdarzały się celowe uszkodzenia terminali lub po prostu narzekania, że system wolno działa. Dziś wygląda to już trochę inaczej. Pracownicy są przyzwyczajeni do nowych technologii, mają świadomość, że tego typu rozwiązania mają im pomagać w pracy.
Tempo rozwoju technologii wymusza na firmach produkcyjnych wprowadzanie co jakiś okres aktualizacji systemowo-sprzętowych
Nierzadko bariery związane są z niechęcią przyswajania nowych technologii. Producenci świadomi tych czynników dopasowują wdrożeniowe szkolenia do poziomu wiedzy pracowników, którzy w przyszłości będą używać zakupionych narzędzi. – To, co jednych ciekawi, innych przeraża. O ile dostanie nowego gadżetu w postaci długopisu czy plecaka ucieszy każdego, o tyle otrzymanie nowego telefonu komórkowego czy terminala już wiąże się z nauką (m.in. nowego menu) itd. – wyjaśnia Krzysztof Zakrzewski, inżynier sprzedaży w BCS Polska. Terminale przeważnie nie są trudne w obsłudze i operator po krótkim czasie z łatwością może sobie z nimi poradzić.
Jeśli chodzi o przygotowanie wdrożenia, trudno mówić o jednym standardzie. Każdy projekt przynosi cenne doświadczenie, które owocuje skróconym czasem kolejnych implementacji, pozwala uniknąć pułapek dzięki zastosowaniu sprawdzonych rozwiązań. Dostawcy rozwiązań mobilnych podkreślają indywidualny charakter każdego wdrożenia. Jednak istnieją etapy, bez których skuteczne wdrożenie jest niezwykle utrudnione. – Proces, mimo że dość skomplikowany, można podzielić na kilka etapów, takich jak: analiza przedwdrożeniowa, przygotowanie systemu poprzez prace konfiguracyjne i programistyczne, szkolenia użytkowników, testy aplikacji, uruchomienie, stabilizacja po uruchomieniu – wymienia Jacek Lisowski z-ca dyrektora ds. sprzedaży i wdrożeń w Asseco BP ERP.
Wsparcie powdrożeniowe
Ukończone wdrożenie nigdy nie powinno być momentem zamrożenia systemu. Tempo rozwoju technologii wymusza na firmach produkcyjnych wprowadzanie co jakiś okres aktualizacji systemowo-sprzętowych. Ponadto tylko z perspektywy czasu można ocenić funkcjonalność danego systemu w specyficznych warunkach danej firmy. Dlatego producenci i dostawcy technologii automatycznej identyfikacji oferują szerokie pakiety powdrożeniowe obejmujące regularne audyty m.in. sieci radiowych, poziomów zabezpieczeń, serwis gwarancyjny, konserwację sprzętu, wsparcie w wypadku awarii, itd. Poszczególni dostawcy proponują swoim klientom sezonowe szkolenia m.in. z obsługi sprzętu. – Jednym z najbardziej interesujących dla klientów produktów SKK jest Zintegrowany Pakiet Serwisowy 4×3, który proponujemy już od kilku lat. W ramach tego pakietu klienci mają 3-letnią gwarancję na urządzenia, 3 dni na naprawę urządzenia, 3 dni na rozwiązanie problemu sprzętowego i 3 dni na rozwiązanie problemu z oprogramowaniem – mówi Remigiusz Kaczewski. Podobne wsparcie powdrożeniowe proponuje swoim klientom BCS Polska: Oferujemy 3 rodzaje wsparcia, o wyborze zawsze decyduje klient. Pierwszy rodzaj wsparcia stanowi tradycyjna gwarancja, drugim jest kontrakt serwisowy odpowiadający formie polisy ubezpieczeniowej na wypadek awarii, głównie dotyczy sprzętu, trzeci to gotowość serwisowa i zabezpieczenie sprzętu zastępczego, potwierdzone stosowną umową utrzymania.
Korzyści z wdrożenia
Dlaczego warto inwestować we wdrożenia nowoczesnych technologii automatycznej identyfikacji? Optymalizacja kosztów procesów produkcyjnych jest priorytetem każdej firmy produkcyjnej. Środkiem do tego jest właściwy przepływ informacji o procesie produkcyjnym oraz właściwy poziom jego kontroli, prowadzący do eliminacji błędów. Posiadając odpowiedni kapitał informacyjny (analizy, raporty) z magazynu, linii produkcyjnej itd. zarządzający produkcją mogą lepiej planować procesy zachodzące wewnątrz zakładu. Bez względu na potrzeby przedsiębiorstwa wdrożenia podkreślają jeden ważny dla produkcji elementarny czynnik: wzrost wydajności. Oznaczony kodem kreskowym lub tagiem RFID produkt jest szybciej identyfikowany i rejestrowany w systemie. Mówi o tym Remigiusz Kaczewski: – Szybsza rejestracja towarów, szybsze raportowanie wykonania zlecenia produkcyjnego to możliwość szybszej reakcji i bardziej elastycznego podejścia do wymagań klienta. Każdy szuka dziś oszczędności, a firmy produkcyjne należą do grona tych, którzy najlepiej umieją liczyć. Oszczędność kilku sekund na jednej operacji może przełożyć się na wielotysięczne zyski w skali roku.
Kontrola każdego etapu produkcji pozwala zidentyfikować newralgiczny moment, w którym nastąpiło obniżenie jakości produktu
Na wzrost wydajności składa się wcześniej wspomniany pożytek w formie minimalizacji niepożądanych sytuacji. Kontrola każdego etapu produkcji pozwala zidentyfikować newralgiczny moment, w którym nastąpiło obniżenie jakości produktu. – System dostarcza dodatkowych informacji, które gwarantują bardziej wydajne planowanie. Dane, jakie uzyskujemy za pomocą terminali przenośnych, spływają w czasie rzeczywistym. W przypadku wystąpienia problemu lub usterki jesteśmy w stanie skrócić czas reakcji o 30-40 procent, ograniczając tym samym potencjalne koszty – wyjaśnia Piotr Rudnicki.
Szybka identyfikacja wad produkcyjnych zapobiega powielaniu uszkodzonej partii produktów, pozwala również zwiększyć efektywność pracujących maszyn. Wdrożenia z pewnością przynoszą wymierne korzyści w skali całego przedsiębiorstwa, bez względu na cel, dla osiągnięcia którego rozpoczęto projekt wdrożeniowy. – Jedne firmy chcą wyeliminować reklamacje, inne chcą podnieść wskaźnik wydajności OEE (Overall Equipment Effectiveness – czyli całkowita wydajność maszyn i urządzeń), jeszcze inne mieć porządek na magazynie. Szybsza rejestracja umożliwia np. identyfikację „wąskich gardeł”, co pozwala na podjęcie działań, które w efekcie udrożnią ten etap produkcji, pozwalając na jej przyspieszenie lub zwiększenie. Wzrost wydajności maszyn i podniesienie wskaźnika OEE umożliwia wdrożenie systemu typu MES. Rejestruje on mikroprzestoje maszyn i klasyfikuje je do określonych grup. Dzięki temu wiemy, że maszyna zamiast pracować np. sześć godzin, pracuje tylko cztery, bo operator przez dwie godziny dziennie czeka na dostawę surowców – wyjaśnia Remigiusz Kaczewski.
RFID w kolejce
Obok kodów kreskowych dużym zainteresowaniem w ostatnich czasach cieszyła się technologia radiowej identyfikacji. Jednak w ostatnim czasie RFID traciła na popularności. Początkowy entuzjazm przygasł z powodu wysokich kosztów implementacji technologii. Cena pojedynczego taga radiowego spadnie w przypadku zwiększenia popytu i wzmożenia ilości implementacji w zakładach produkcyjnych. RFID bez względu na koszt daje firmie wiele możliwości kontroli, optymalizacji czasu pracy, inwentaryzacji, zapisu genealogii produktu. – Znakowanie na etapie produkcji pozwala na śledzenie produktu od momentu wprowadzenia oznaczenia poprzez poszczególne etapy produkcji aż po gotowy wyrób – mówi Katarzyna Muszyńska.
RFID ma nad tradycyjnymi kodami przewagę szybkości w odczytywaniu danych, pozwala również skanować dane w miejscach niedostępnych dla standardowych terminali. – Najczęściej firmy decydują się na wdrożenie system RFID w celu usprawnienia procesów reklamacyjnych lub kontroli poprawności załadunku – stwierdza Remigiusz Kaczewski. RFID mimo regularnych wdrożeń jest nadal technologią przyszłości, która, jako wciąż nowa technologia, musi przejść okres rynkowej standaryzacji. – Oczywiście klienci pytają o RFID, ale raczej w kontekście możliwości uruchomienia jej w przyszłości. Chcą, aby system był nie tyle na nią gotowy, ile nie blokował ewentualności jej wdrożenia – wyjaśnia Jacek Lisowski.
„Innowacyjność i efektywność” Katarzyna Muszyńska, menedżer sprzedaży Wincor Nixdorf – Ze względu na automatyzację procesów przepływu danych, urządzenia do automatycznej identyfikacji stają się niezbędnym elementem systemu informatycznego. Kody kreskowe pojawiają się praktycznie na każdym etapie łańcucha dostaw, od produkcji po sprzedaż. Chcąc być efektywnym w działaniu, a przez to i konkurencyjnym, trzeba wykorzystywać urządzenia do ich odczytu. Nowe technologie to nie tylko inwestycje i koszty. Prawidłowe wdrożenia przekładają się na innowacyjność i coraz większą efektywność, a tym samym wyraźne oszczędności. To determinuje stały wzrost popytu na tego typu urządzenia. Polski rynek cały czas dojrzewa i świadomość klientów w zakresie marki stale rośnie, tym samym coraz ważniejsze stają się trwałość, niezawodność, ergonomia oraz jakość i szybkość odczytu informacji. W obszarze automatycznej identyfikacji rozwój urządzeń i układów skanujących zmierza obecnie w kierunku zapewnienia coraz to większej dynamiki i szybkości odczytu oraz elastyczności zastosowań.
„Kod kreskowy to wymóg” Patryk Kalita, Print&Apply specialist Sato – Automatyczne znakowanie towarów i unifikacja systemu przepływu danych za pomocą transmisji elektronicznej powodują, że w większości przedsiębiorstw przemysłowych lub handlowych korzystanie z kodów kreskowych stało się nie tylko standardem, ale wręcz wymogiem, bez którego trudno wyobrazić sobie sprawne i efektywne funkcjonowanie firmy. Dzięki wykorzystaniu rozwiązań opartych na automatycznej identyfikacji oraz istnieniu produktów SATO menedżerowie otrzymują narzędzia, dzięki którym mogą precyzyjnie zarządzać procesami produkcyjnymi, łańcuchem dostaw, powierzchnią magazynową towarów, półproduktów oraz surowców przeznaczonych do produkcji. SATO produkuje systemy automatycznej identyfikacji oraz oferuje kompletne rozwiązania dla różnych branż dzięki integracji sprzętu, oprogramowania, dostaw materiałów eksploatacyjnych oraz usług serwisowych. SATO specjalizuje się w oferowaniu rozwiązań związanych z oznaczaniem towarów kodem kreskowym za pomocą etykiet samoprzylepnych, lub innych nośników, jak np. opaski identyfikacyjne do szpitali i innych instytucji służby zdrowia, czy też tekstyliów – branża odzieżowa. Ostatnio coraz większą popularnością i zainteresowaniem klientów cieszą się etykieciarki, tj. automaty do znakowania etykietami produktów na linii produkcyjnej.
„Szerokie korzyści” Krzysztof Zakrzewski, inżynier sprzedaży BCS Polska – Są sektory, które od kilku lat regularnie zwiększają produkcję i nie przestają unowocześniać swoich parków maszynowych czy systemów IT, ale są też takie, które wciąż tną koszty i nie inwestują – to swoisty paradoks, bo systemy IT mają się spłacać z oszczędności dzięki nim uzyskanym. W każdym przedsiębiorstwie są to inne korzyści, gdyż zastosowanie urządzeń nie jest jednakowe. Wspólnym mianownikiem są zaś: poprawa wymiany informacji w firmie, usprawnienie procesów, zmniejszenie nakładu pracy, wzrost zadowolenia klientów i gotowość do realizacji większej ilości zleceń, obsługi nowych klientów. Największym problemem we wdrożeniach, jest chęć wykonania systemu własnymi siłami. Dzieje się tak często w sytuacji, gdy zleceniodawca uznaje system za prosty i implementacja wiąże się z pisaniem własnego oprogramowania.
Jacek Lisowski z-ca dyrektora ds. sprzedaży i wdrożeń Asseco BS ERP – Każda jednostka logistyczna poprzez numer etykiety logistycznej z kodem kreskowym jest identyfikowalna do dalszych procesów magazynowych. Znamy jej zawartość pod kątem indeksu, ilości, daty produkcji czy innych wymaganych parametrów takich jak np. data ważności. Co więcej, urządzenia te pozwalają na automatyczny proces przyjęcia produkcji każdej jednostki logistycznej z procesem oklejenia palety, jej identyfikacji w systemie oraz określenia większości niezbędnych parametrów na podstawie danych zawartych w systemach ERP/WMS. Systemy WMS oparte o terminale radiowe potrafią nadzorować stany na buforach wejściowych z produkcji, co w przypadku np. niewielkiej ilości urządzeń transportujących palety oraz kilku miejsc przyjęć produkcji pozwala między innymi na balansowanie kolejnością transportowania palet z produkcji do miejsc składowania.
„Nie zostać w tyle” Piotr Rudnicki, specjalista ds. sprzedaży Koncept-L – Zwiększenie wydajności przy zmniejszeniu lub przynajmniej utrzymaniu bieżących kosztów, możliwość szybkiego dostosowania się do wymagań odbiorców to jedyny sposób, by firma produkcyjna nie została w tyle. Wyposażenie urządzenia w Bluetooth oraz laserowy skaner kodów kreskowych obsługujący kody 2D gwarantuje bezbłędne wprowadzanie i przechowywanie danych oraz usprawnia zarządzanie procesami logistycznymi: kontrolą zapasów, zarządzaniem produktami, inwentaryzacją, realizacją zamówień. Urządzenia te charakteryzują się wysoką odpornością, wydajnością oraz niezawodnością pracy w ciężkich warunkach. Aktualnie w swojej ofercie posiadamy przemysłowe komputery firmy DLOG oraz cieszące się coraz większym zainteresowaniem terminale danych firmy M3Mobile, w szczególności model MM3. Liderem wśród tych ostatnich pozostaje jednak wciąż firma CipherLab z najnowszym „dzieckiem” – modelem 8200.
„Popularny MES” Remigiusz Kaczewski, menedżer ds. sprzedaży SKK S.A. – Wszystkie firmy dochodząc do pewnego etapu rozwoju inwestują w automatyczną identyfikację, ponieważ widzą korzyści, jakie mogą osiągnąć dzięki takiej inwestycji. Producenci urządzeń AutoID co miesiąc proponują nowe urządzenia, które można wykorzystywać na liniach produkcyjnych. Są to zarówno terminale, programy jak i czytniki przemysłowe. Przykładowo Microscan zaoferował ostatnio zestaw AutoVision, który składa się z czytnika Vision HAWK i inteligentnej kamery przemysłowej Vision MINI z oprogramowaniem, które pozwala w szybki i prosty sposób zbudować aplikacje do odczytu kodów, a nawet rozpoznawania kształtu. Zestaw nie wymaga specjalistycznej wiedzy do budowy stanowiska automatycznego odczytu i rejestracji kodów. Dużą popularnością cieszy się system MES oparty na platformie Wonderware, który w ubiegłym roku wprowadziliśmy do naszej oferty. Zakłady produkcyjne widzą realne korzyści w systemie, który pozwala im mierzyć parametry technologiczne, rejestrować przestoje i inne zdarzenia, które mają miejsce na liniach produkcyjnych. Otwartość systemu i jego modułowa budowa pozwalają na wykorzystanie go w każdym przedsiębiorstwie, a szybka i wydajna baza generuje bardzo szczegółowe raporty.