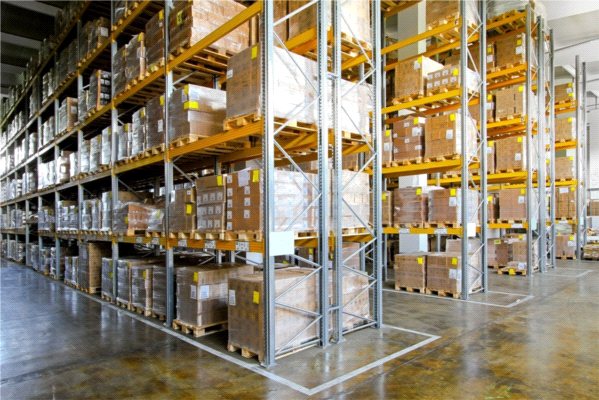
Bezpieczne składowanie
Bezpieczeństwo w łańcuchu dostaw, to problem, który istnieje od zawsze, i który zapewne szybko nie zniknie. Wszyscy ci, którzy ze względu na rodzaj prowadzonej działalności w łańcuchu przemieszczania dóbr stykają się z tym zagadnieniem, bo wymaga tego partner biznesowy lub...
Dotyczy to przede wszystkim operatorów logistycznych i przewoźników działających w branży high tech., farmaceutycznej, czy dóbr luksusowych, a więc wszędzie tam, gdzie z utratą wartości uczestnicy łańcucha dostaw muszą liczyć się najbardziej.
Rozważania na temat powyższych kwestii skutkują pojawieniem się szeregu pytań. Czy bezpieczeństwo łańcucha dostaw to tylko brak kradzieży, brak uszkodzeń, ubytków przewożonych towarów? Czy dotyczyć może tylko i wyłącznie towarów zaliczanych do obszaru wysokiego ryzyka, czyli takich, które są narażone na kradzież? Gdzie szukać granicy wartości, która może świadczyć o tym, że to jest właśnie taki towar? Czy uzyskiwanie certyfikatów potwierdzających spełnienie wymogów normy ISO 28000, czy też TAPA (Technology Asset Protection Association – Związek Ochrony Aktywów Technologicznych) pozwala operatorowi logistycznemu z przekonaniem stwierdzić, w łańcuchu nie ma kradzieży? Czy tak dobieramy dostawców i przewoźników oraz na tyle dobrze chronimy przechowywany towar, że ten proceder u nas nie ma miejsca. Czy nie dochodzi do zdarzeń, które potwierdzą potrzebę rygorystycznego przestrzegania wymogów norm, ale też właściwego doboru personel i osiągnięcie właściwej efektywności zarządzania pracownikami odpowiedzialnymi za bezpieczeństwo w kolejnych ogniwach łańcucha dostaw?
Norma ISO 28000:2007 określa wymagania systemu zarządzania bezpieczeństwem, z uwzględnieniem krytycznych aspektów dla zapewnienia bezpieczeństwa w łańcuchu dostaw. Te aspekty uwzględniają zarządzanie finansami, produkcją i informacją, ale również urządzeniami do pakowania, magazynowania i transportu dóbr.
Zadania operatora kontraktowego
Branża zaawansowanych technologii jest branżą szczególną, po pierwsze ze względu na wysoki poziom stosowanych rozwiązań, a przede wszystkim z powodu szybko zmieniającego się zapotrzebowania oraz ciągle postępującego zróżnicowania oferty dla odbiorców. Współpraca z takim wytwórcą wymaga od dostawców wysokiego poziomu elastyczności dotyczącej samych komponentów i podzespołów oraz niezawodności w ich dostarczaniu. Niebagatelną rolę w tym procesie odgrywają operatorzy logistyczni przejmujący obowiązek dostarczania do fabryk niezbędnych rodzajów podzespołów, w wymaganej ilości i czasie. Często obowiązek zadośćuczynienia tym wymogom spoczywa na samych dostawcach, mających dostęp do procesu planowania producenta. Ogniwem spajającym zamówienia (potrzeby) producentów, oraz dostawy są operatorzy kontraktowi, czyli te ogniwa łańcucha dostaw, które charakteryzują się wysoce specjalistycznym know how w zakresie umiejętności przyjmowania, składowania, kompletowania i wydawania, czyli wszystkich faz procesu magazynowania dóbr o wysokim stopniu przetworzenia i wysokiej wartości, Często wykonują też czynności związane z przygotowaniem podzespołów, oferując usługi produkcyjno – usługowe (co-manufacturing) w swojej strukturze organizacyjnej. Nie znajdziemy ich u operatorów, dla których nie jest istotny rodzaj usług świadczonych dla różnego rodzaju branż, a jedynie handlingowa ilość „przerzuconego” towaru w jednostce czasu.
Wśród definicji logistyki znajdujemy definicję stowarzyszenia krajowych towarzystw logistycznych w Europie – European Logistics Association (ELA) brzmiącą następująco: „Logistyka jest pojęciem obejmującym organizację, planowanie, kontrolę i realizację przepływu towarów od ich wytworzenia i nabycia, przez produkcję i dystrybucję, aż do finalnego odbiorcy, w celu zaspokojenia wymagań rynku,…”
W definicji tej bez trudu znajdujemy miejsce logistyki produkcji (…od ich wytworzenia i nabycia, przez produkcję i dystrybucję…), będącej również odniesieniem do procesów magazynowania w łańcuchu dostaw dóbr wysokiej wartości przywołanego poniżej działania operatora logistycznego.
Fakt niebywałej dbałości o bezpieczeństwo przechowywanych dóbr wynika z konieczności zapewnienia nieprzerwanych dostaw podzespołów do montażu wyrobów gotowych, szczególnie w sytuacji operatorów kontraktowych, związanych długoterminowymi umowami z partnerami biznesowymi z branży, w której bezpieczeństwo jest priorytetem. Występuje błyskawiczna odpowiedź na złożone zamówienie, bezbłędne sformowanie jednostek ładunkowych, brak jest jakichkolwiek ubytków (zaginięć) spowodowanych realizacją procedur magazynowania.
Case study
Poniżej prezentujemy przykład działania jednego z operatorów logistycznych w branży, gdzie wymóg dbałości o bezpieczeństwo przechowywanych towarów jest zadaniem priorytetowym. Jest to warunek konieczny funkcjonowania takiego operatora – bo to przecież operator kontraktowy.
Operator ten działa w branży EMS (Electronics Manufacturing Services). Struktury organizacyjne są poziome – brak szczebli pośrednich zarządzania – dzięki czemu uzyskuje się maksymalne skracanie procesów decyzyjnych. Firma nie świadczy usług transportowych jak robią to typowi operatorzy logistyczni. Podstawowym jej zadaniem jest świadczenie usług magazynowania ze szczególnym naciskiem na bezpieczeństwo przyjmowanych, przechowywanych i wysyłanych podzespołów, które trafiają do producenta wyrobów finalnych.
Zarządzanie zapasami opiera się na jednym z modeli VMI (Vendor Managed Inventory), w którym dostawcy realizują dostawy podzespołów dla współpracującego w ramach kontraktu operatora logistycznego, a ten dopiero na zamówienie producenta końcowego dokonuje kompletacji i realizuje konieczne wysyłki. Właścicielem przechowywanych zapasów są ich dostawcy. Dostawcy mają wgląd w plan producenta nie utrzymującego służb zaopatrzenia. Producent płaci dopiero po użyciu podzespołów do produkcji. Jest to dla niego bardzo wygodne, ponieważ „nie ma lepszej gwarancji dostawy na czas, niż czekający w magazynie zapas potrzebny do produkcji”.
Jak w firmie realizowane są zagadnienia bezpieczeństwa wyrobów?
W przedsiębiorstwie funkcjonuje system ISO 28000:2007, który jak się okazuje nie jest czymś powszechnym w odróżnieniu od np. ISO 9000, dość powiedzieć, że do niedawna brakowało jeszcze wystarczającej liczby audytorów; w tym konkretnym przypadku skorzystano z usług firmy Lloyd’s Register Quality Assurance.
Bezpieczeństwo przechowywanych wyrobów realizowane jest w trojaki sposób:
- po pierwsze – rekrutacja pracowników, której proces średnio trwa pół roku, tzn. jest to czas, w którym pracownik ma szansę na zawarcie stałej umowy o pracę
- po drugie – ciągła inwentaryzacja przechowywanych, przyjmowanych i wydawanych podzespołów
- po trzecie – fizyczna ochrona – system kamer, bramek dostępowych, a wreszcie cały zestaw procedur związanych z poruszaniem się pracowników po terenie firmy, z ich uprawnieniami dostępu do konkretnych stref, to wreszcie profesjonalna ochrona zewnętrznej firmy świadczącej usługi fizycznej i technicznej ochrony.
W firmie korzysta się z uznanych w świecie jakości sprawdzonych rozwiązań, a mianowicie stosowane są praktyki 5S, a także zasady filozofii Kaizen, co pozwala utrzymywać na wysokim poziomie realizację zadań partnera biznesowego.
Jak wyglądają działania operacyjne?
Firma pracuje na powierzchni 20 tysięcy m2. Dysponuje 40 tysiącami miejsc paletowych. Nie jest to liczba skończona. Producent nadal się rozwija, więc i operator w ślad za nim musi nadążać, pojawiają się nowi dostawcy, powiększa się liczba pozycji materiałowych (kilkadziesiąt tysięcy).
Składowane towary podzielone są na dwie części, jedna w której składowanie realizowane jest w otwartej przestrzeni i druga tzw. „high value” – o wysokiej cenności – składowanie odbywa się w wydzielonej, wygrodzonej i strzeżonej strefie przez dodatkowy system ochrony, w tym pracowników ochrony.
W strefie przyjęcia do dyspozycji jest 14 bram, tyle samo w strefie wydań. Każdy pojawiający się transport z podzespołami posiada swój unikalny numer, który zostaje nadany po otrzymaniu awizacji o jego nadejściu. Numer ten powiązany jest z ilością i rodzajem przewożonego towaru, oraz danymi środka transportowego i kierowcy. Pierwsza kontrola i identyfikacja transportu realizowana jest przed wjazdem na teren firmy – sprawdzana jest tożsamość kierowcy, dane pojazdu, oraz ten właśnie numer, który jest wprowadzany do systemu przez pracownika ochrony i od tej pory wiadomo jaki transport się pojawił, jaką przydzielić mu bramę i czas do rozładunku.
Każda brama obsługiwana jest przez pracownika z uprawnieniami do otwierania aut celnych. Następuje proces rozładunku. Bramie przyporządkowane jest pole odkładcze, mające swoją lokalizację w systemie zarządzania magazynem, zresztą jak każde inne miejsce, gdzie można składować paletowe jednostki ładunkowe. Każda z palet ma swój niepowtarzalny kod przyporządkowany przez dostawcę. Pracownik ma obowiązek zeskanować ten numer, jak również etykietę każdego opakowania znajdującego się na palecie, następnie nadaje mu numer wewnętrzny, i dopiero jeśli nie ma żadnych wątpliwości, co do kompletności i całości opakowań dostawa (po ponownym zabezpieczeniu każdej palety) ma prawo pojawić się na regale dostawcy – towar składowany jest wg stałych miejsc tzn. każdy dostawca ma swój regał, czy określoną liczbę miejsc paletowych przeznaczonych właśnie na jego produkty.
Po przyjęciu w systemie podzespoły są widziane przez producenta, który może już składać zamówienia.
Ostre procedury
W przypadku stwierdzenia uszkodzenia opakowania, wzywany jest pracownik ochrony, a także pojawia się pracownik inżynieryjny będący przedstawicielem dostawcy i to on decyduje co dalej z podzespołami w takim opakowaniu się dzieje. Fakt ten rejestrowany jest w systemie informatycznym, raport wraz ze zdjęciem jest przesyłany także do dostawcy.
W procesach magazynowania, czyli wszystkich czynnościach związanych z przyjęciem i realizacją wysyłek nie ma dokumentów papierowych, wszystkie etapy tych procedur pojawiają się jedynie na ekranach skanerów i komputerów. Każda zmiana lokalizacji drogą radiową natychmiast przekazywana jest do systemu.
We wszystkich strefach przepływu, czyli na przyjęciu, w strefie składowania, kompletacji i wydania obowiązuje zasada pracy tylko z fabrycznie zamkniętymi opakowaniami – to są wymogi procedur związanych z zachowaniem bezpieczeństwa wyrobów w procesie przepływu. Zamówienia od producenta – kontraktowego partnera – pojawiają się co dwie godziny, w ciągu 90 minut kompletuje się wysyłki, ładuje i podstawia pod bramy producenta. Średnio wysyłanych jest 100 -120 palet co 2 godziny. Rzadko zdarza się wysyłać palety jednorodne, więc każda paleta jest konsolidowana z różnego rodzaju podzespołów przechowywanych na wielu paletach. W trakcie kompletowania wysyłki każde odstępstwo, problem ze znalezieniem odpowiedniego opakowania jest rejestrowane, łącznie z przyczyną i czasem, a następnie tworzony jest raport.
Skompletowana paleta jest weryfikowana, jeśli wszystko jest w porządku zostaje dopuszczona do załadunku, jeśli nie, paleta jest wycofywana i następuje procedura wyjaśniania i korygowania. Auto jest zamykane i plombowane, zamknięcie sprawdza również ochrona a kierowca ma wyznaczony czas na dotarcie pod rampę producenta. Uprawniony pracownik operatora logistycznego uczestniczy w przyjmowaniu wysyłki u producenta, kontrolując proces i pomagając w bezbłędnym dostarczeniu właściwych podzespołów na linie montażowe.
Innym z elementów bezpieczeństwa, a także zachowania wysokich standardów kompletacji są procedury inwentaryzacyjne. W firmie działa zespół inwentaryzacyjny, którego zadaniem jest prowadzenie inwentaryzacji w sposób ciągły, wg różnych procedur. Towary strefy wysokiej cenności liczone są codziennie. Inwentaryzacja prowadzona jest według dostawców, według asortymentu czy też miejsca składowania – wyrywkowo, gniazdami regałów. Cały magazyn też jest kontrolowany – w przedziale 26 dni sprawdzana jest każda lokalizacja. Dostawcy o działaniach zespołu inwentaryzacyjnego informowani są na bieżąco drogą elektroniczną. Przy tak rozległym asortymencie błędy wychwytywane przez inwentaryzatorów usprawniają i przyspieszają proces komisjonowania wysyłek.
Dodatkowe strefy
Zachowaniu wysokiej sprawności w zakresie bezpieczeństwa jakościowego jak i ilościowego przechowywanych podzespołów służą także działania w strefach nie związanych bezpośrednio z procesem magazynowania, a wynikającymi z charakteru branży w jakiej działa producent.
Pierwsza z nich to strefa Value Add – jest to miejsce, gdzie realizowane są usługi dodające wartości. To właśnie tutaj następuje sprawdzanie podzespołów, ich zewnętrznego stanu, poprawności oznakowania, dokonywany jest wstępny montaż niektórych elementów, zdejmowane są folie ochronne. Oprócz usług i czynności wykonywanych rutynowo, bez potrzeby zlecania przez kogokolwiek (dostawców podzespołów i producenta) realizowane są zadania zlecane dodatkowo przez dostawców. W sytuacji, gdy spodziewana jest dostawa, lub podzespoły są już przyjęte, w przypadku otrzymania od ich dostawcy sygnału, że coś jest nie tak, sprawdzana jest cała partia.
Druga z nich to strefa Analiz Technicznych. Jest to miejsce w którym pracownicy inżynieryjni dostawców dokonują analizy i kontroli parametrów podzespołów, których jakość i poprawność działania została zakwestionowana na liniach montażowych producenta. To tu następuje ich weryfikacja i kwalifikowanie do trzech grup dalszego postępowania. Albo zakwestionowana partia (np. po naprawie) trafia z powrotem na regały do zwykłego wykorzystania w procesie produkcji, albo jest odsyłana do dostawcy. Trzecia grupa to podzespoły i części dla których najwłaściwszym postępowaniem jest przekazanie do utylizacji.
Wyjątkowy w działalności operatora jest sposób współpracy z organami celnymi. Rozwiązania tego typu funkcjonują w innych krajach, ale w Polsce są to nieliczne przypadki. Jeżeli chodzi o podstawowe uwarunkowania prawne i praktykę działalności firmy, jest ona składem celnym typu E. Oznacza to, że towary objęte procedurą składu celnego nie muszą być składowane w miejscu określonym jako skład celny, lecz w pomieszczeniach nadających się do składowania, należących do posiadacza pozwolenia.
Ten model postępowania został uzupełniony o procedury ułatwiające przepływ towarów. Innowacyjny jest w nim m.in. sposób dystrybucji towarów ze składu. Polega to na tym, że informacja o „wychodzeniu” towarów z magazynu przekazywana jest tylko raz miesiącu. Możliwe jest to dzięki Urzędowi Celnemu, dla którego podstawą rozliczeń są raporty. Operator korzysta z ułatwień określonych w przepisach wspólnotowych i odprawia towary w procedurach uproszczonych na tzw. powiadomieniach zbiorczych. Oznacza to duże zaufanie ze strony państwa. Działając według standardowych zasad operator musiałby wysyłać do urzędu dokumenty wszystkich transakcji zakończenia składu celnego, a przeprowadza się ich kilkanaście tysięcy miesięcznie. Byłoby to strasznie pracochłonne zarówno dla pracowników operatora, jak i celników. Opóźniałoby znacznie proces odprawy, bo bez zgody Urzędu Celnego nie można byłoby manipulować składowanymi towarami i przemieszczać ich poza skład celny. Dzięki uproszczonym zasadom towary zgłaszane są tzw. powiadomieniami zbiorczymi, wysyłanymi pod koniec miesiąca.
Wygodne jest również to, że składowanie towarów poddawanych odprawie celnej nie wymaga posiadania wydzielonej i zamkniętej przestrzeni. Towary o statusie celnym (będące pod dozorem celnym) sąsiadują na regale z towarami unijnymi, o statusie niecelnym, co znacznie ułatwia ich przechowywanie. Ponadto towar może być do tego wydawany 24 godziny na dobę i przez siedem dni w tygodniu. Dostarczany jest błyskawicznie, bo nie spowalniają go procedury. Taki sposób działania jest wygodny również dla Urzędu Celnego. Rozliczenia tego operatora stanowią bowiem dla niego aż 80 do 90 proc. ewidencji (zgłoszeń celnych) – pozostałe firmy z regionu generują pozostałe 10-20 proc.
Przyjęcie każdej dostawy, wysłanie każdej wysyłki, wszystkie problemy jakie się w związku z tym mogą pojawić są rejestrowane, przybierając postać raportów dziennych i tygodniowych, trafiając na biurka kierownictwa operatora logistycznego oraz obsługiwanego producenta, stanowią podstawę działań korygujących. Bieżąca analiza działalności dokonywana jest na podstawie raportów dziennych, obrazujących precyzyjnie przepływ podzespołów. Ponadto bardzo dokładne, szczegółowe dokumenty, obrazujące różne aspekty działalności firmy sporządzane są co dwie godziny w rytm napływających zamówień co jest innowacyjnym i dość rzadko spotykanym działaniem. Konsekwentne egzekwowanie raportowania, będące podstawą podejmowania decyzji w tym korygujących działania, jest oznaką prawidłowo funkcjonującego systemu informacyjnego firmy. Ponadto obowiązek tak szczegółowego raportowania wynika również z wymogów systemów ISO jakie tu funkcjonują, tj. normy ISO: 9000 – zarządzania jakością, 14000 – zarządzania środowiskowego, 18000 – zarządzania BHP, 28000 – zarządzania bezpieczeństwem dostaw.
Zakończenie
Specyfiką działania tego operatora logistycznego jako operatora kontraktowego jest konieczność przestrzegania surowych reguł i procedur w zakresie bezpieczeństwa wyrobów na każdym etapie realizacji zadań związanych z przepływem materiałowym. Fizycznym początkiem procesu jest identyfikacja pojawiającego się w bramie transportu, a finałem bezproblemowe pojawienie się podzespołów na liniach producenta oraz ścisłe rejestrowanie wszystkich odchyleń związanych z błędami w kompletacji, uszkodzeniami opakowań i raportowaniem w tym zakresie.
Procedury te w swojej precyzji i szczegółowości , co do czasu i miejsca oraz przyczyny ich uruchamiania zdecydowanie różnią się od procedur powiedzmy reklamacyjnych mających miejsce w codziennej pracy typowych firm – operatorów logistycznych, w przypadku wystąpienia różnic w dokumentach, uszkodzeń czy ubytków w dostarczanych , czy przyjmowanych przesyłkach.
Wymóg ten realizowany jest nie tylko ze względu na surowe wymagania partnera co do terminowości i kompletności dostaw, cenności przedmiotu działalności, ale także sprostania oczekiwaniom co do prawidłowości dokumentowania przepływów dla władz celnych.
Kolejnym wyróżnikiem, którego nie sposób nie dostrzec to integracja z produkcją, realizowanie wielu czynności czysto produkcyjnych – będących czymś co można nazwać przygotowaniem produkcji, montażem wstępnym – a także czynności kończące proces produkcji, w przypadku określania stopnia przydatności, podzespołów wycofanych z linii produkcyjnych.