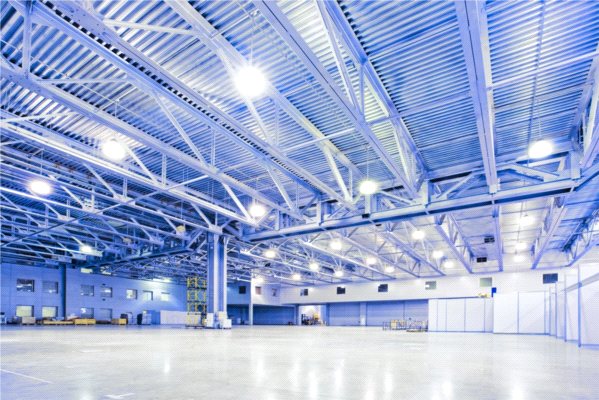
Reindustrializacja Europy – szanse i bariery
Powoli spełniają się sny o reindustrializacji Europy. Coraz więcej firm decyduje się na przeniesienie produkcji z Azji na Stary Kontynent. Dla nas to spora szansa, bo polskie fabryki należą do najnowocześniejszych w Europie, a koszty pracy pozostają konkurencyjne. Barier do...
Szył szlafroki w garażu, a teraz jest najbogatszym człowiekiem świata. Kto? Amancio Ortega, hiszpański magnat branży odzieżowej i twórca Inditexu czyli właściciel marki Zara. Swój sukces zawdzięcza nie tylko odważnej koncepcji, ale także temu, że większość swoich towarów wytwarza w Hiszpanii, a nie w dalekiej Azji, co zdecydowanie skraca łańcuch dostaw.
Z ziemi chińskiej do Polski
Podobnym tropem chce podążać coraz więcej firm z branży odzieżowej, przenosząc produkcję do Europy. Jager – brytyjska marka odzieżowa ze 129 – letnim doświadczeniem, zakończyła produkcję „na wyspach” piętnaście lat temu. Teraz planuje przywrócić część produkcji z zamiarem przyśpieszenia procesu wprowadzania towarów na sklepowe półki oraz zwiększenia jakości produktów. Był to także ważny argument dla firmy STEIFF, która już w 2008 r., w trosce o jakość, przywróciła całość procesów produkcyjnych do Niemiec.
Przykłady spływające z różnych miejsc na świecie pokazują, że pomysłów na przenoszenie czy budowę fabryk na lokalnym gruncie nie brakuje. Co więcej, w większości są one podparte sensowną argumentacją. Firma Hitachi Rail Europe z siedzibą w Londynie otworzyła we wrześniu fabrykę pojazdów szynowych w miejscowości Newton Aycliffe. Media nazwały tę strategiczną decyzję firmy powrotem prawdziwej produkcji szynowej do Wielkiej Brytanii. Fabrykę każdego miesiąca opuszczać będzie 35 pojazdów a zatrudnienie w niej znajdzie 730 osób. Motorola – marka będąca w posiadaniu Google – zapowiedziała otwarcie fabryki w teksańskim Fort Worth, gdzie planuje produkować Moto X – urządzenie, które jako pierwsze w historii firmy wytwarzane będzie jedynie na terenie USA. Wraz z zakładem powstanie dwa tysiące miejsc pracy. To ważny argument przemawiający za lokalną produkcją, choć nie jedyny. Rob Bamforth, główny analityk Quocirca, przyznając słuszność planom Motoroli, podzielił się krótkim i treściwym komentarzem: – Jeśli produkujesz urządzenia tam, gdzie następnie mają być sprzedawane, nie muszą one płynąć przez połowę świata.
Jeśli produkujesz urządzenia tam, gdzie następnie mają być sprzedawane, nie muszą one płynąć przez połowę świata.
Tak samo uważa CEO koncernu Adidas – Herbert Heiner. Jego zdaniem przywrócenie produkcji do miejsc reprezentujących główny rynek zbytu czyli głównie Europy i Stanów Zjednoczonych, pozwoli na szybsze dostarczanie nowych kolekcji do sklepów. Adidas prognozuje, że ta strategia zwiększy roczny przychód netto o 15% do 2020 roku i powstrzyma głównych konkurentów od „podkradania” rynkowego udziału w sprzedaży. Odzieżowy potentat testował już zautomatyzowany model produkcji, pozwalający klientom na personalizację ich zakupów. Jego wdrożenie nie byłoby możliwe przy utrzymaniu produkcji w Azji.
Wyjątkiem nie są też polskie firmy. – Obserwujemy rynek i dostrzegamy, że coraz więcej firm chce wytwarzać w kraju. Jeśli parametry jakościowe i ekonomiczne byłyby spełnione, bylibyśmy również zainteresowani – zadeklarowała w rozmowie z Dziennikiem Gazetą Prawną Katarzyna Haska, wiceprezes firmy Etos, do której należy odzieżowa marka Diverse. Według niej przenoszenie produkcji odzieżowej do kraju to początek procesu, który będzie się odbywał etapami.
„Made in” ma znaczenie
Firmy przenoszą swoje zasoby produkcyjne z Azji – w tym głównie z Chin – również z powodu rosnących tam wynagrodzeń – średnio o kilkanaście procent rocznie. Kiedyś miesięczny koszt utrzymania szwaczki w chińskim zakładzie, który jest w stanie spełnić normy jakościowe, wynosił 200–300 dol., teraz wynosi już co najmniej 500 dol. Wysokie są tez koszty transportu towarów na główne rynki zbytu. To co skutecznie „zwabiało” na Daleki Wschód europejskich czy amerykańskich producentów dziś nie ma już tak dużego znaczenia. Start-upowe przedsiębiorstwo z Californii ET Water Systems doświadczyło tego na własnej skórze. Właściciel przedsięwzięcia od razu zdecydował się na budowę fabryki w Chinach. Bardzo szybko zaczął jednak odnotowywać straty z powodu transportu zabierającego zbyt wiele czasu, co w przypadku wyrafinowanych urządzeń biznesowych, mających uchodzić za bardzo innowacyjne, okazało się zabójcze. Z rewolucją niestety nie zdążył, także jakość samej produkcji pozostawiała wiele do życzenia. Gdy dopiero po upływie pięciu lat porównał koszty produkcji miejscowej i chińskiej, okazało się, że inwestycja w kalifornijską fabrykę byłaby zaledwie 10% droższa.
Prezes włoskiej marki Piquardo, producenta wyrobów skórzanych przyznał, że lokalizowanie fabryk w Chinach jest rozwiązaniem przeznaczonym dla produkcji wielkoformatowej. Jego firma wytwarza mniejsze ilości towarów i zróżnicowany asortyment więc produkuje w Europie. Za bardzo istotny uważa też fakt, że metka „Made in Italy” potrafi bardzo skutecznie przekonać klienta, że produkty są wykonane w dużo wyższej jakości.
Europa potrzebuje reindustrializacji
Za reindustrializacją przemawia też aspekt gospodarczy. Czym grozi uzależnienie od chińskich fabryk pokazuje przykład metali ziem rzadkich. Te surowce niezbędne dla nowoczesnych technologii wykorzystywanych np. w energetyce czy produkcji elektrycznych samochodów, wytwarzane są na poważną skalę jedynie w Chinach. – Chińczycy zaś mówią, że chętnie je sprzedadzą, ale chcą najpierw wybudowania w Chinach fabryki przetwarzającej te surowce. A nie w Europie – tłumaczył europoseł Adam Gierek.
Nic więc dziwnego, że w reindustrializację zaangażowała się Komisja Europejska. Zgodnie ze strategią przyjętą w 2012 r., udział przemysłu w europejskim PKB ma do 2020 r. wynieść 20 procent. To o ponad 4% niż obecnie. W polskim PKB ogólny udział przemysłu wynosi 18% co jest wynikiem mieszczącym się powyżej europejskiej średniej. Mankamentem jest jednak kierunek, w jakim produkcja podąża. W ogólnym zestawieniu podsumowującym działalność przemysłową, opublikowanym przed trzema laty, KE zaklasyfikowała Polskę do najniższej, trzeciej kategorii tzw. krajów doganiających kraje wysoce uprzemysłowione. Do tej grupy przydzielono również takie państwa jak Czechy, Bułgaria, Węgry, Litwa, Łotwa, Słowacja czy Rumunia. Na czele zestawienia uplasowały się m.in. Niemcy, Francja, Belgia, Austria, Wielka Brytania czy Szwecja.
Jak pokazują wdrożenia QRM, przeniesienie punktu ciężkości na skrócenie czasu produkcji i dostarczenia produktu do klienta skutkuje też ograniczeniem kosztów.
Komisja jednogłośnie przyznała, że największym wyzwaniem dla Polski będzie na przestrzeni najbliższych lat przejście od klasycznej i rzadko korzystającej z nowoczesnych technologii gospodarki do gospodarki opartej na wiedzy i badaniach. Poparcie dla tej idei wyraził również amerykański dziennikarz Mitchell A. Orenstein, który w magazynie Foreign Affairs napisał: „Polska musi przesunąć się na wyższe pozycje w łańcuchu wartości dodanej rozwijając sektor nowoczesnej technologii (high tech) i eksport produktów i usług wymagających specjalistycznej wiedzy”.
Rzeczywiście, Polska w 2013 roku na badania i rozwój przemysłowych rozwiązań high – tech – przeznaczyła zaledwie 0,7% PKB. Są jednak pozytywne sygnały, wskazujące, że w najbliższym czasie będzie można zmienić taki stan rzeczy. Jednym z nich jest dobrze rozwinięty system oświaty oraz duży współczynnik studiującej młodzieży – drugi najwyższy spośród państw OECD. Nadzieję rozbudzają też innowacyjne, prężne firmy technologiczne a także dobrze zinformatyzowane zakłady produkcyjne.
Technologia w służbie przemysłu
To o tyle ważne, że wykorzystanie nowoczesnych technologii w procesie produkcji jest podstawą Przemysłu 4.0, idei, której celem jest zwiększenie konkurencyjności lokalnego przemysłu. Idea zakłada wytworzenie danego produktu w wirtualnym świecie zanim powstanie on fizycznie. Dzięki temu może być on dowolnie konfigurowany względem potrzeb konkretnego klienta. Przemysł 4.0 ma pozwolić na opłacalne wytwarzanie produktów nawet w pojedynczych sztukach. Nie będzie to możliwe bez wykorzystania zintegrowanych systemów IT.
– W ostatnich latach wiele firm, napędzanych unijnymi funduszami zrealizowało inwestycje w park maszynowy, zmodernizowało infrastrukturę i wdrożyło zaawansowane systemy informatyczne wspierające zarządzanie. Dzięki temu polskie fabryki dysponują nie tylko zapasem mocy produkcyjnych, ale również należą do najnowocześniejszych w Europie. Produkują nie dość, że bardzo dobrze, to również – porównując z wysokorozwiniętymi krajami unijnymi – także relatywnie tanio – przekonuje Andrzej Morawski z BPSC, firmy informatycznej, która do tej pory zrealizowała ponad 600 wdrożeń systemów ERP w firmach produkcyjnych i usługowych.
Na razie barierą w industrializacji jest kwestia kosztów energii wykorzystywanej w przemyśle. Wysokie ceny energii elektrycznej i gazu skutecznie przeszkadzają w przenoszeniu produkcji do Polski. Profesor Jerzy Hausner stwierdził, że bardzo ważnym zadaniem państwa będzie pomoc w stworzeniu dobrze działającego rynku energetycznego, który spowoduje spadek cen energii i zwiększy konkurencyjność polskiego przemysłu. Andrzej Duda w trakcie swojej kampanii wyborczej zapowiedział, że jeśli zwycięży w wyborach podejmie, jak sam określił, najważniejsze na najbliższe lata wyzwanie odbudowy polskiego przemysłu i reindustrializacji kraju tak, aby w przewidywalnym czasie dorównać do średniej poziomu gospodarczego zachodniej Europy. Pozostaje więc trzymać go za słowo.
Sukces reindustrializacji zależeć więc będzie w takim samym stopniu od rządzących, co i zarządzających firmami produkcyjnymi.
Pewną barierą jest też sposób myślenia polskich firm, które koncentrują się przede wszystkim na optymalizacji kosztów produkcji, tymczasem to czas jest kluczowy. Jak pokazują wdrożenia QRM, przeniesienie punktu ciężkości na skrócenie czasu produkcji i dostarczenia produktu do klienta skutkuje też ograniczeniem kosztów. Aby było to możliwe decyzje biznesowe muszą być oparte na szerokiej i dostępnej na bieżąco informacji. Zapewnia to wykorzystanie platform IT gdzie systemy ERP są zintegrowane ze specjalistycznymi rozwiązaniami: MES, WMS, planowaniem produkcji.
– Ta koherencja systemów umożliwia spełnienie wymogów i oczekiwań, jakie wobec systemów informatycznych stawiają dzisiejsze przedsiębiorstwa. Dzięki współpracy systemów klasy ERP z innymi systemami, przedsiębiorca otrzymuje nie tylko zestaw informacji o kontrahencie, produkcie czy też o kolejności zleceń produkcyjnych, ale również o wzajemnych powiązaniach wszystkich tych elementów. Uzyskana w ten sposób wiedza pozwala na podjęcie decyzji biznesowych w jak najwcześniejszej fazie procesu. – tłumaczy Aleksander Faleńczyk, Menedżer ds. Kontraktów w BPSC S.A.
Potrzeba specjalistów
Problemem jest też dostęp do zaplecza specjalistów. Deficyt zatrudnienia tylko w sektorze motoryzacyjnym przekracza już 30%. Problem jest szczególnie odczuwalny w Wielkopolsce czy na Śląsku, gdzie lokowane są największe inwestycje motoryzacyjne. – Obecnie w regionie mamy około 500 otwartych wakatów, od najprostszych produkcyjnych, po wyspecjalizowane i menadżerskie. Kandydatów brakuje na każdym szczeblu. – tłumaczy Agnieszka Kolanowska, Regional Manager w Randstad.
Mimo zrealizowanych w ostatnich latach projektów IT, firmy produkcyjne nie potrafią też optymalizować kosztów produkcji. Z badań przeprowadzonych przez BPSC wynika, że zaledwie co trzecia firma korzysta z mapy umiejętności – kompetencji technicznych. To bardzo przydatne narzędzie dla firm o dużej rotacji pracowników, wielozmianowych i działających w systemie Just in Time, gdzie trzeba bardzo szybko znaleźć zastępstwo w momencie niedyspozycji czy choroby pracownika. – Matryca daje pojęcie o faktycznym poziomie opanowania przez pracownika poszczególnych czynności na linii produkcyjnej czy gnieździe roboczym. Pozwala trafnie dopasowywać pracowników produkcji do gniazd produkcyjnych, planować ich rozwój na podstawie zidentyfikowanych luk umiejętności i podpowiadać kto może przeszkolić pracownika w danym obszarze. Wskazuje też na czynności lub na stanowiska, co do których istnieje poważne ryzyko, że w czasie niespodziewanych nieobecności lub dodatkowych zleceń, mogą one okazać się wąskim gardłem z uwagi na niskie zabezpieczenie w kwalifikacje. – tłumaczy Anna Węgrzyn, wieloletni praktyk HR, kierownik projektu mHR w BPSC.
Najbliższe lata pokażą czy uda się nam wykorzystać szansę. W dużej mierze zależy to od utrzymania konkurencyjności. Jest to o tyle istotne, że kraje Europy Środkowo-Wschodniej będą rywalizować o inwestorów wykorzystując cały arsenał środków. Łącznie ze zwolnieniami podatkowymi i ulgami. Sukces reindustrializacji zależeć więc będzie w takim samym stopniu od rządzących, co i zarządzających firmami produkcyjnymi.