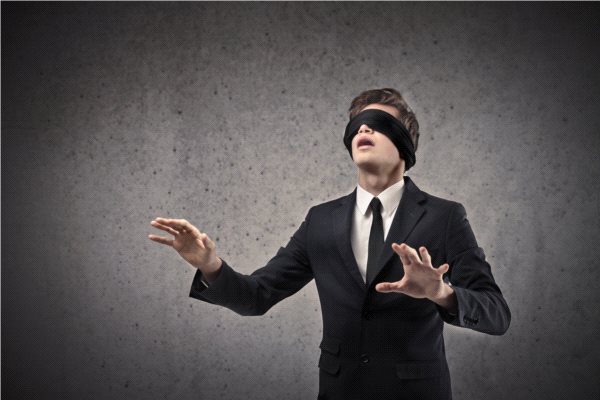
Poka-yoke a jakość
Shigeo Shingo przedstawił koncepcję poka-yoke w 1961 r., kiedy był inżynierem przemysłowym w Toyota Motor Corp. Początkowo stosowanym terminem było baka-yoke, co można było tłumaczyć potocznie jako idiotoodporność.W 1963 r. pracownica Arakawa Body Co. odmówiła stosowania...
W 1963 r. pracownica Arakawa Body Co. odmówiła stosowania narzędzi baki-yoke w jej miejscu pracy, ze względu na niehonorową i obraźliwą konotację tego terminu. W związku z tym termin został zmieniony na poka-yoke, co oznacza korektę błędu.
Co to jest poka-yoke?
Poka-yoke to udoskonalenie procesu produkcji mające na celu zapobieżenie występowaniu określonego defektu. Jest to system usprawniający procesy, który zapobiega wypadkom, promuje bezpieczeństwo pracy, a zarazem zapobiega uszkodzeniom produktów i awariom maszyn. Narzędzie poka-yoke to mechanizmy używane do wyeliminowanie pomyłek w całym procesie. W idealnej sytuacji, wdrożone poka-joke zapewniają zaistnienie odpowiednich warunków przed wykonaniem kolejnego kroku procesu, zapobiegając powstawaniu defektów. Tam, gdzie to nie jest możliwe, poka-yoke wykonuje funkcję „detektywistyczną”, eliminując w ten sposób defekty tak szybko, jak to możliwe.
Wiele osób myśli o poka-yoke jako wyłącznikach krańcowych, optycznych systemach kontroli, prowadnicach lub automatycznych odcięciach zasilania, które powinny być opracowane przez dział techniczny. To bardzo ograniczone podejście. Mechanizmy te mogą być elektryczne, mechaniczne – ale też proceduralne, wizualne, ludzkie lub w jakiejkolwiek innej formie, która uniemożliwia nieprawidłowe wykonanie danego etapu procesu. Poka-yoke może być również wdrażane w obszarach innych niż produkcja, takich jak sprzedaż, zaopatrzenie, zakupy lub badania i rozwój, gdzie koszt błędów jest znacznie wyższy niż na hali produkcyjnej. W rzeczywistości zapobieganie defektom lub wykrywanie i usuwanie defektów ma szerokie zastosowanie w większości organizacji.
Błąd to w myśl tej koncepcji wykonanie zabronionego działania, niepoprawne wykonanie wymaganego działania lub błędna interpretacja informacji niezbędnych do prawidłowego wykonania działania. Istotą poka-yoke jest zastosowanie funkcji, procesu lub projektu, aby zapobiec wytwarzaniu niezgodnego ze specyfikacją wyjściową produktu.
Fizyczne zapobieganie błędom polega na instalowaniu komponentów, takich jak urządzenia lub czujniki, w celu wyeliminowanie warunków, które mogą prowadzić do błędu. Operacyjne zapobieganie błędów polega z kolei na wprowadzaniu modyfikacji lub instalowaniu urządzeń, które wzmacniają prawidłową sekwencję procedur. Najgłębszym wdrożeniem idei poka-yoke jest stworzenie kultury identyfikowania sytuacji, które powodują defekty i zapobieganie im dzięku zaangażowaniu i wysokiej świadomości pracowników.
Podejścia do zapobiegania błędom
W poka-yoke wskazuje się dwa poziomy zapobiegania błędom. Prewencja, czyli zapobieganie błędom podczas tworzenia defektów, oraz wykrywanie, czyli ujawnienie defektów i natychmiastowe działania korygujące, które mają zapobiec powstaniu ich większej ilości.
Wada jest wynikiem wszelkich odchyleń od specyfikacji produktu, które mogą prowadzić do niezadowolenia klienta. Definiując ją można wyróżnić sytuacje, gdy produkt odbiega od specyfikacji produkcji lub projektu, lub też takie gdy produkt nie spełnia wymagań wewnętrznych firmy albo oczekiwań klienta. Błąd to jakiekolwiek zauważone odchylenie od określonego procesu produkcyjnego. Warto zauważyć, że błąd w procesie może nie spowodować wady produktu, lecz pojawienie się wady nie jest możliwe bez wystąpienia błędu w procesie.
Powszeche praktykowane jest dzisiaj wdrażnie programów zero defektów. Jest to oparta na interdyscyplinarnych zespołach strategia doskonalenia zakładu, która koncentruje się na procesach produkcyjnych i operacjach. Sprawdzanie błędów ma na celu zapobieganie błędom i odchyleniom od standardów wszystkich typów, które mogą mieć wpływ na jakość, bezpieczeństwo, koszty produkcji i zadowolenie klienta. Poka-yoke jest podstawowym narzędziem, wykorzystywanych w programach zero defektów.
FMEA w projektowaniu i produkcji
FMEA (Failure Mode Effects Analysis) jest techniką analityczną stosowaną przez projektantów produktów lub procesów jako środek zapewniający, że w możliwym zakresie uwzględniono potencjalne awarie i błędy oraz i związane z nimi przyczyny. W obsarze badań i rozwoju, projekt produktu musi zostać ulepszony w oparciu o wyniki badania FMEA. Zakładane korekty błędów powinny zostać zidentyfikowane i zintegrowane z projektem.
Z kolei wszystkie kwestie związane z produkcją i procesem są traktowane priorytetowo, aby zwiększyć możliwości pozytywnego odbioru firmy przez klienta i poprawić zwrot z inwestycji. Najczęstszym narzędziem służącym do identyfikacji i priorytetyzacji problemów jest tu procesowe FMEA. Metodę FMEA procesu stosuje się w zespole wielospecjalistycznym, aby odpowiedzieć na wszystkie pytania związane z procesem i określić wyniki w postaci liczby priorytetowej ryzyka (RPN). Narzędzie to pomaga zespołowi zadać kluczowe pytania w celu zidentyfikowania i wdrożenia odpowiedniego zabezpieczenia przed błędami.
Podstawowa technika mająca na celu zapobieganie błędom to projektowanie dla produkcji, czyli projekowanie wyrobów tak, aby nie można było ich nieprawidłowo wyprodukować lub zmontować. Technika ta może być również wykorzystana do uproszczenia projektu, a zatem zmniejszenia jego kosztu produktu. Samo poka-yoke w produkcji zapewnia prawidłowe ustawienie, uzupełnia program jakości w obszarze pominiętym lub niemożliwym do uwzględnienia na etapie projektu.
Błędy są nieuniknione
Wdrażając programy zapobieganie defektom w miejacach pracy, niezbędne jest zrozumienie ludzkich ograniczeń. Limity te obejmują:
- Wzrok: ludzie mają ograniczoną zdolność odróżniania szczegółów, kolorów lub dopasowania widzenia do oświetlenia.
- Słuch: poszczególne górne i dolne progi słyszenia zmieniają się, gdy dodaje się szum tła.
- Zdolność powtarzania: Wydajność mięśniowa i skupienie maleją wraz ze wzrostem częstości powtórzeń.
Należy bezwględnie przyjąć do wiadomości, że pomyłki są nieuniknione i stanowią część ludzkiej natury. Niewielu pracowników popełnia błędy celowo; najczęściej dążą raczej do zapobiegania im. Programy zapobieganie defektom zmieniają środowisko pracy w celu zmniejszenia możliwości wystąpienia błędów ludzkich.