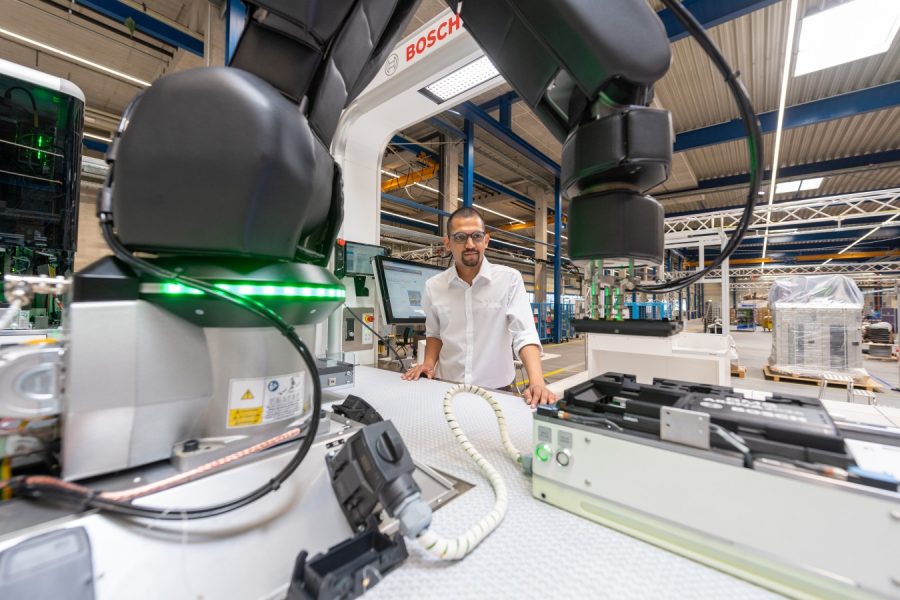
Dziesięć lat Przemysłu 4.0
Koncepcja Przemysłu 4.0 dojrzewa. To, co Bosch w 2011 roku przedstawił na Targach w Hanowerze jako pionierski projekt, zyskało popularność na całym świecie. Celem była integracja i połączenie procesów produkcyjnych w komunikującą się sieć, a rezultatem miała być możliwość produkcji niestandardowych elementów nawet w małych ilościach w sposób ekonomicznie opłacalny. Dziś pionierzy szukają kolejnych możliwości Przemysłu 4.0, ale w całym sektorze produkcji tempo zmian nie jest rewolucyjne.
Od 2012 roku firma Bosch systematycznie wprowadza fabryki – własne i swoich klientów – w nową erę przemysłową. W ostatnich dziesięciu latach firma wygenerowała ponad cztery miliardy euro obrotu w obszarze rozwiązań Przemysłu 4.0. Tylko w roku 2020 sprzedaż Bosch w tej dziedzinie osiągnęła poziom ponad 700 milionów euro.
– Wcześnie zauważyliśmy potencjał, jaki drzemie w Przemyśle 4.0 i zostaliśmy pionierami tej dziedziny. Dziś widzimy pozytywne rezultaty tych działań – mówi Rolf Najork, członek zarządu spółki Bosch odpowiedzialny za technologie przemysłowe. Wykorzystanie Przemysłu 4.0 we własnych zakładach produkcyjnych również przynosi efekty. Bosch integruje inteligentne oprogramowanie do sterowania produkcją, monitorowania oraz logistyki na jednej platformie produkcyjnej. Łączą się one w jedną bazę danych, dzięki czemu zadania, takie jak analiza produkcji i przewidywanie usterek z wykorzystaniem AI, są prostsze i bardziej efektywne. Wdrażanie nowej platformy produkcyjno-logistycznej Bosch rozpocznie się pod koniec 2021 roku.
– Około 240 naszych zakładów otrzyma standaryzowany „Zestaw narzędziowy do Przemysłu 4.0”, który można rozszerzać i wdrażać według potrzeb – mówi Najork. Firma Bosch uważa, że w ciągu najbliższych pięciu lat platforma przyniesie jej oszczędności na poziomie prawie jednego miliarda euro, przy inwestycji na poziomie ok. 400 milionów euro. Podczas tegorocznych, cyfrowych Targów w Hanowerze firma Bosch zaprezentowała fabrykę przyszłości: technologicznie elastyczną, inteligentnie połączoną, ekologicznie zrównoważoną i efektywną ekonomicznie.
Pionierskie prace
Na Targach w Hanowerze w 2011 r. zaprezentowano ideę fabryki, która przełamywała konwencje. To nie ludzie mieli dostosować się do maszyn, lecz na odwrót. W tej wizji produkty miały być zaangażowane w proces wytwarzania samych siebie, a także komunikować się z ludźmi oraz maszynami. Były to narodziny Przemysłu 4.0 – a firma Bosch jest jednym z jego ojców-założycieli. Jednocześnie stało się oczywiste, że potrzebna jest współpraca wielu firm, aby wdrożyć założenia tej koncepcji w fabrykach na całym świecie.
– Jedyny sposób na wykorzystanie pełnego potencjału Przemysłu 4.0 to współpraca na arenie międzynarodowej. Ludzie i maszyny muszą „porozumiewać się w jednym języku”. Wymaga to wspólnych, międzynarodowych standardów uzgodnionych między firmami – mówi Najork. Razem z innymi przedsiębiorstwami firma Bosch opracowywała OPC Unified Architecture – język maszynowy dla Przemysłu 4.0, który standaryzuje dostęp do urządzeń i systemów oraz umożliwia wymianę danych w sposób niezależny od producentów. Współpraca wzmogła się też z organizacjami, takimi jak Plattform Industrie 4.0 oraz Industrial Internet Consortium. Sojusze stały się nieodłączną częścią Przemysłu 4.0.
Status quo
Dziś zainteresowanie Przemysłem 4.0 nadal jest wysokie, lecz wciąż zbyt mało przedsiębiorstw przygotowuje się do wdrożenia Przemysłu 4.0 w konsekwentny sposób. – Projekty pilotażowe to dobry sposób na to, aby wypróbować nowe technologie i pomysły. Nadszedł jednak czas, by przyspieszyć: musimy sprawić, żeby Przemysł 4.0 stał się normą – mówi Najork. – Przemysł 4.0 nie jest celem samym w sobie. To sposób na zachowanie konkurencyjności. W przyszłości bez cyfryzacji nic nie będzie możliwe” – dodaje. Projekty firmy Bosch przynoszą wymierne korzyści: rozwiązania połączone w sieć zwiększają wydajność pracy nawet o 25 procent, a dostępność maszyn nawet o 15 procent. Ograniczają natomiast koszty utrzymania nawet o 25 procent.
– Jeśli chcemy wykorzystać potencjał Przemysłu 4.0, musimy porzucić odizolowane rozwiązania. Systemy, które działają wyłącznie w swoich własnych granicach hamują postęp – mówi Najork. W zakładach Bosch jest już ponad 120 000 maszyn i 250 000 połączonych urządzeń, takich jak zintegrowane kamery i roboty. Samych sterowników maszyn połączonych za pośrednictwem oprogramowania Nexeed dla Przemysłu 4.0 opracowanego przez firmę Bosch Connected Industry jest około 22 000. Ten założony w 2018 roku dział dostarczył oprogramowanie już ponad połowie zakładów firmy Bosch oraz ponad 2000 linii produkcyjnych. Około 100 klientów międzynarodowych również polega na Nexeed, w tym BMW, Sick i Trumpf. Sprzęt i oprogramowanie stają się sobie coraz bliższe. Na Targach Hanowerskich spółka Bosch Rexroth zaprezentowała swoją platformę CtrlX Automation, otwartą technologię sterowania działająca w paśmie 5G. – Sprawienie, by rozwój odbywał się z udziałem innych, daje nam możliwość tworzenia efektów sieciowych i pozwala ideom nabrać wiatru w żagle – dodaje Najork.
Nowe technologie
– Skupiamy się na wykorzystywaniu i łączeniu zalet różnych technologii. Bosch staje się firmą z obszaru AIoT. Składamy sztuczną inteligencję (AI) oraz Internet rzeczy (IoT) w jedną całość – mówi Najork.
W Hanowerze Bosch prezentuje Balancing Energy Network, system zarządzania energią oparty na AI, który optymalizuje jej wykorzystanie w fabrykach. Oprogramowanie ma też potencjał, by pomóc w zmniejszeniu negatywnego wpływu na środowisko większych kompleksów budynków różnego rodzaju, takich jak szpitale, centra handlowe czy hale sportowe.
Dzięki nowym rozwiązaniom technologicznym interakcje ludzi i maszyn staną się w przyszłości bezpieczniejsze i bardziej wydajne: technologia 5G oferuje niezawodną bezprzewodową wymianę danych niemal w czasie rzeczywistym. Firma Bosch pod koniec 2020 r. uruchomiła pierwszą sieć kampusową 5G w wiodącym zakładzie Przemysłu 4.0 w Stuttgarcie-Feuerbach. Aktualnie aplikacje oparte na technologii 5G testowane są w dziesięciu zakładach na całym świecie. Firma Bosch wyposaża też swoje produkty w możliwość obsługi technologii 5G.
Daleko za pionierami
Bosch jako pionier, który może testować własne rozwiązania we własnych fabrykach, przeciera szlaki Przemysłu 4.0. Po 10 latach trudno znaleźć na świecie wiele firm, które z pełni korzystają z jego możliwości – nie mówiąc już o Polsce. W ostatnich miesiącach wpływ na sytuację miała też pandemia koronawirusa, choć w długofalowej perspektywie może ona przyśpieszyć proces cyfryzacji fabryk.
– Niewiele fabryk na świecie wdrożyło wielką ósemkę Przemysłu 4.0, czyli metody kojarzone z nowoczesną technologią, metodami zarządzania produkcją czy komunikowaniem się maszyn bez udziału człowieka. Bieżące wdrożenia przystopowały ze względu na obawę przed inwestycją, zatrzymaniem projektów, zamknięciem fabryk. Z drugiej strony pandemia pozwoliła zobaczyć, jak przystępne są cyfrowe technologie, które są siłą napędową Przemysłu 4.0. W związku z tym łatwiej będzie nam podejmować decyzje o wdrożeniach tego typu technologii – mówi Mikołaj Dramowicz, prezes zarządu DATAPAX.
Mimo spowolnienia procesów wdrożeniowych z zakresu Przemysłu 4.0 automatyzacja i cyfryzacja procesów przemysłowych wydaje się przyszłością gospodarki uprzemysłowionej. Z raportu „Przemysł 4.0 w Polsce – rewolucja czy ewolucja” opracowanego przez analityków z firmy Deloitte wynika, że dla 86 proc. menedżerów wyższego stopnia wdrażanie nowych technologii będzie mieć kluczowe znaczenie dla uzyskania przewagi rynkowej nad konkurencją.
Badanie sugeruje, że największą przeszkodą na drodze do wdrożenia transformacji cyfrowej jest brak wiedzy na temat tego, w jaki sposób ją przeprowadzić oraz które technologie powinny stanowić podstawę nowej infrastruktury informatycznej, na co zwróciło uwagę 41 proc. respondentów. Ponadto aż 61 proc. badanych przyznało, że firma musi dokonać zmian personalnych bądź nauczyć pracowników nowych umiejętności, zanim przeprowadzi cyfrową transformację.
– W Polsce w dużej części firm, szczególnie z sektora MŚP, głównym narzędziem do zarządzania jest Excel. Do tej pory te firmy nie były otwarte na nowe technologie. Oczywiście firmy międzynarodowe, które budują nowe oddziały, przodują i stosują bardzo nowoczesne rozwiązania, więc jesteśmy na dobrej drodze. Szukamy metod na usprawnianie, ale do Przemysłu 4.0 jeszcze nam daleko – ocenia ekspert.
Przede wszystkim czujniki
O konieczności usprawnienia metod wdrażania systemów inteligentnych przekonują również przedstawiciele hubu technologicznego działającego pod egidą Krakowskiego Parku Technologicznego. Zespół hub4industry stworzył kompleksowy program wsparcia dla przedsiębiorstw zainteresowanych wdrożeniem rozwiązań z zakresu Przemysłu 4.0. W tym celu zbudowano showroom Fabryki Przyszłości, w którym firmy mogą sprawdzić, jak konkretne technologie sprawdzają się w praktyce. Hub realizuje także pilotażowe projekty wdrożeniowe i prowadzi działania edukacyjne w zakresie wykorzystania technologii Przemysłu 4.0
– Najchętniej wprowadzane technologie z Przemysłu 4.0 przede wszystkim opierają się na internecie rzeczy. W przemyśle są to różnego rodzaju czujniki na maszynach, które mogą informować o tym, co się dzieje z parkiem maszynowym, czy są jakieś awarie i je przewidywać. Jest też analiza danych z wykorzystaniem sztucznej inteligencji w firmach produkcyjnych, żeby móc podjąć sensowną decyzję i wyszukać w gąszczu informacji te sensowne i wartościowe. Internet rzeczy i analiza danych poprzez sztuczną inteligencję przodują dlatego, że są najbardziej dostępne, najłatwiej nam je zrozumieć i są najprostsze we wdrożeniu – wyjaśnia Mikołaj Dramowicz.
Według analityków z firmy MarketsandMarkets wartość globalnego rynku Przemysłu 4.0 w 2019 roku wyniosła 71,7 mld dol. Przewiduje się, że do 2024 roku wzrośnie do 156,6 mld dol. przy średniorocznym tempie wzrostu na poziomie 16,9 proc.
5G to fundament
Po 10 latach wiemy już dobrze, że Przemysł 4.0 nie może być wdrożony bez istnienia odpowiedniej infrastruktury teleinformatycznej. Sieć 5G, która rozwija się równolegle z koncepcją Czwartej Rewolucji Przemysłowej, postrzegana jest jako fundament, na którym stać będą inteligentne fabryki.
– Przemysł 4.0, sieci 5G to są hasła, które można nazwać medialnymi, marketingowymi. Ale one oznaczają zupełnie nowy sposób pracy, produkcji i komunikowania się. Zmieni się wszystko, zmieni sposób pracy, prawdopodobnie nie będziemy zobligowani zegarkiem tak jak dzisiaj. Prawdopodobnie w ciągu 30 lat przestaniemy wykonywać jakiekolwiek nużące, wymagające wysiłku fizycznego prace. To sobie dzisiaj trudno wyobrazić, ale tempo zmian jest ogromne i to powinniśmy uwzględnić już w systemach edukacji – mówi Jarosław Tworek, wiceprezes Krajowej Izby Gospodarczej Elektroniki i Telekomunikacji.
Jednym z motorów napędowych zmian, których jesteśmy dziś świadkami, są dyrektywy Unii Europejskiej poświęcone przyszłościowym technologiom informatycznym. Zgodnie z wytycznymi Komisji Europejskiej do 2020 roku każde państwo członkowskie powinno stworzyć infrastrukturę 5G co najmniej w jednym dużym mieście. W Polsce elementem realizacji tych założeń jest wdrożenie megaustawy komunikacyjnej, która wprowadzi m.in. niższe opłaty związane z rozbudową infrastruktury 5G.
To pierwszy krok na drodze do napędzenia rynku nowych technologii. Parlament Europejski opracował także Konwencję o udzielaniu patentów europejskich, która ma umożliwić patentowanie rozwiązań informatycznych. Nowe wytyczne, realizowane za pośrednictwem zrewidowanej przez rząd ustawy o Prawie własności przemysłowej, ułatwi polskim firmom ochronę własności intelektualnej związanej z rozwiązaniami chmurowymi, systemami autonomicznymi czy sztuczną inteligencją. Zwiększy także ich konkurencyjność na rynku europejskim.
– Sieć 5G jest punktem startu. Tak jak punktem powszechnego uprzemysłowienia i produkcji masowej, takim punktem startu było wynalezienie elektryczności i możliwość prowadzenia dość powszechnej masowej automatyzacji w produkcji, tak w przypadku sieci 5G będzie taka podstawa infrastrukturalna rozwoju społeczeństwa opartego na informacji. Będzie to podstawa funkcjonowania wszystkich wynalazków wyposażonych w element inteligentny – twierdzi ekspert.
A gdzie kadry?
W czwartej rewolucji technologicznej równie ważne co nowe technologie (takie jak Big Data, wirtualna i rozszerzona rzeczywistość, sztuczna inteligencja, blockchain, chmura, IoT, druk 3D czy nowe generacje robotów przemysłowych) są też kompetentne kadry. Potwierdza to badanie Deloitte, z którego wynika, że blisko połowa (43 proc.) menedżerów właśnie zasoby ludzkie i talenty uznała za główny czynnik napędzający innowacje cyfrowe w ich przedsiębiorstwach.
– Nie wystarczy zakup najnowszej linii produkcyjnej czy wdrożenie kobotów w fabryce, jeśli pracownikom zabraknie kompetencji do wykorzystania potencjału, jakie dają najnowsze rozwiązania technologiczne – podkreśla Dawid Solak, członek zarządu Platformy Przemysłu Przyszłości. – W badaniach najczęściej wskazywane są dwie bariery związane z transformacją. Pierwsza to brak właściwiej kultury organizacyjnej przedsiębiorstwa, a druga to właśnie brak odpowiednich kompetencji. Firmy często nie dysponują kadrami z wiedzą na temat niezbędnych technologii i procesów.
Artykuł ukazał się w czasopiśmie Eurologistics nr 3/2021