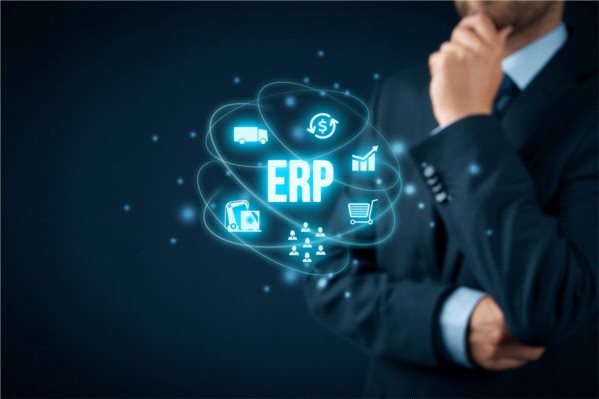
Nowoczesne technologie w magazynach
Sektor logistyczny czerpie pełnymi garściami z nowoczesnych rozwiań technologicznych, które pozwalają usprawnić funkcjonowanie magazynów, ale nie tylko. Potwierdzają to dane firmy IDC dotyczące inwestycji w rozwiązania Internetu Rzeczy. Tylko w tym roku w regionie Europy...
Rynkowe prognozy dla sektora logistycznego są jednoznaczne; branża produkcyjna będzie jednym z największych beneficjentów rozwiązań IoT. Według IDC tylko w tym roku wydatki na Internet Rzeczy osiągną wartość 11,2 mld dolarów. To ponad 15% więcej niż przed rokiem. Taki poziom wzrostu mówi nam, że to w bliskiej przyszłości magazyny będą wypełnione po brzegi nie tylko towarem, ale i zaawansowaną technologią. Czujniki, sensory, skanery, kamery itp. potrafią poprzez sieć przekazywać dane operacyjne do centralnego systemu zarządzania, jakim jest ERP. Biorą udział w procesach, nie tylko zastępując czynności wykonywane dotychczas przez ludzi, ale w dużej mierze realizują zadania, które wcześniej nie były znane. Spójrzmy jak już dziś wygląda to na konkretnych przykładach.
Magazyn z automatu
Gdy mówimy o nowoczesnych technologiach w magazynach, zazwyczaj wyobrażamy sobie w pełni zautomatyzowany skład paletowy, gdzie całość operacji realizowana jest przez zaprogramowane układnice. Wózki widłowe podwożą lub odbierają palety z miejsc podawczych, a zarządzanie magazynem odbywa się autonomicznie poprzez oprogramowanie sterowników oraz aplikację do nadrzędnego systemu sterowania. ERP współpracuje z takim automatem, przygotowując informacje o paletach podjeżdżających do okna podawczego oraz poprzez wysyłanie dyspozycji wydania. Dyspozycje są następnie zamieniane na zadania wydania konkretnych palet według przyjętych kryteriów na przykład według zasady First Expired First Out. Czasem systemy ERP biorą większy udział w zarządzaniu takim magazynem. Przejmują sterowanie operacjami oraz wizualizują rozkład i obciążenie magazynu. Nie tylko magazyny paletowe podlegają automatyzacji. W przypadku procesów kompletacji czasem spotykamy rozwiązania oparte o zautomatyzowany przepływ pojemników. W takich magazynach wydzielone są strefy wybierania, czyli tzw. strefy pickingu oraz strefy uzupełniania, w których pojemniki uzupełniane są zapasem pobieranym z miejsc paletowych. W takich magazynach występuje gęste ułożenie tysięcy zasobników, które wyglądają jak szufladki regału. Celem zastosowania magazynu pojemnikowego jest optymalizacja procesu kompletacji. Jest to alternatywa dla klasycznych regałów, w których kompletacja odbywa się na poziomach dostępnych dla magazynierów. Tutaj strefa kompletacji jest zautomatyzowana.
Pracownicy wspierani są poprzez różne technologie, takie jak „pick by light”, ułatwiające skompletowanie prawidłowych ilości i minimalizujące ryzyko pomyłek. Dyspozycje pochodzące z systemu ERP są kolejkowane i grupowane według identycznych asortymentów, aby zminimalizować rotację pojemników w przypadku wydań tego samego asortymentu.
Automatyzacja nie ominęła również magazynów przyprodukcyjnych. Tutaj spotykamy rozwiązania dostosowane do danej branży oraz do gabarytów półproduktów. Beneficjentem są często firmy realizujące konstrukcje stalowe. Mam tu na myśli magazyny blach oraz dłużyc w postaci rur, profili stalowych oraz aluminiowych. Logika sterowania takim magazynem przez system ERP jest podobna do poprzednio opisanych z tą różnicą, że operacjami steruje przypływ zlecenia produkcyjnego. Często takie magazyny są zintegrowane z linią produkcyjną. Na stanowiskach operatorzy rejestrują w systemie ERP poszczególne operacje technologiczne oraz przepływ materiału, dając na odpowiednim etapie magazynowi rzetelne informacje o zawartości nośników przyjmowanych na skład, tworząc bufor przyprodukcyjny.
Zgromadzone informacje są na bieżąco wykorzystywanej aktualizowane przy pobieraniu asortymentu do dalszej obróbki. Często wykorzystuje się zautomatyzowane szafy magazynowe – systemy półek służące do przechowania drobnych elementów oraz narzędzi. Integracja systemu ERP z takim magazynem jest najczęściej realizowana w modelu, w którym to pracownik odgrywa kluczową rolę. Ma to ułatwić mu wykonywanie zadań, aby mógł on w trybie „na żądanie” realizować operacje wejścia-wyjścia, wykorzystując interfejs w postaci urządzenia mobilnego lub ekranu dotykowego.
Inne technologie stosowane w coraz większym zakresie dotyczą wykorzystania czujników, skanerów kodów kreskowych czy też bramek RFID. Te technologie wspierają typowe procesy logistyczne, ale również występują na halach produkcyjnych. W przypadku firm dysponujących własną flotą transportową coraz częściej akcentowana jest potrzeba optymalizacji procesów logistycznych i kontroli ich realizacji. Tutaj z pomocą przychodzą systemy ERP wyposażone w technologie mapowe oraz mobilne systemy
dla kierowców. Przy wykorzystaniu takich narzędzi możliwa jest minimalizacja kosztów transportu, kontrola dowozu i statusu przesyłek oraz zarządzanie opakowaniami zwrotnymi.
Sprytny magazyn – jak to działa?
Jednym z bardziej interesujących wdrożeń, które zrodziły się w BPSC, jest wdrożenie w obszarze intralogistyki, czyli logistyki magazynowej, w firmie produkcyjnej z branży farmaceutycznej. Zaprojektowaliśmy i stworzyliśmy system zarządzania jednostkami magazynowymi (produktami, surowcami), który opiera się wyłącznie na informacjach elektronicznych. Od samego początku, gdy dana jednostka pojawia się w firmie, jest pod nieustanną kontrolą i obserwacją. Monitoring rozpoczynał się w chwili pojawienia się produktu i trwał przez cały okres jego przebywania w firmie, nie wyłączając takich miejsc jak np. laboratorium. Obserwacja była prowadzona na wszystkich etapach, aż do momentu, gdy gotowy wyrób, poprzez ciąg komunikacyjny, trafiał do magazynu.
Na etapie zakupów strefa obsługi dostaw identyfikuje i znakuje jednostki, wiąże je z ewidencją dokumentową i dokonuje kontroli ilościowej. Koniec tego etapu oznacza początek kolejnego, którym jest transport jednostek do kolejnego miejsca, np. wspomnianego wcześniej laboratorium. Tam rejestrowany jest pobór próbki oraz przebieg i wynik badania. Ich rezultat wpływa na status dostarczanej partii i determinuje zadania transportowe dla pozostałych jednostek.
Odbiór od analityków jest również osobnym zadaniem. Wózki transportu pośredniego dowożą jednostki do miejsc podawczych magazynu i dają wsad zadaniowy dla kolejnego ogniwa w tym łańcuchu – dla wózków systemowych, lokujących jednostki w gniazdach magazynu. Te zaś są sterowane automatycznie przez system ERP. Operator z poziomu ekranu dotykowego uruchamia kolejne zadania, a pojazd wykonuje czynności rozlokowania. System ERP balansuje rozkład towarów w magazynie tak, aby proces wydania mógł być realizowany możliwie najszybciej. Po wykonaniu swojego zadania wózek systemowy generuje potwierdzenie do systemu ERP. Odwrotny proces przebiega w sytuacji pobrania jednostek na zlecenie produkcji. Wszystkie procedury są prowadzone odwrotnie: od strefy magazynowej aż po produkcję. Procesy dodatkowe, do których możemy zaliczyć np. przepakowania, dekompletacje czy inwentaryzacje również przebiegają zadaniowo z użyciem komunikatów elektronicznych.
Na podstawie opisanych rozwiązań prowadzona jest cała gospodarka wyrobami gotowymi. To rozwiązanie było oparte o zastosowanie zawansowanych rozwiązań technologicznych i mobilności urządzeń oraz ich pracy w trybie online we wspólnej sieci informatycznej. Informacje były również wykorzystywane w celu zachowania procedur bezpieczeństwa. System ERP, w tym wypadku Impuls EVO, śledził nie tylko partie dostawowe czy produkcyjne, ale dosłownie każdą pojedynczą jednostkę magazynową, wymuszając jej przejście przez wymagane procedury kontrolne. Informacje napływające do ERP pozwalały zmniejszać ryzyko wypadków w magazynie. Mając wiedzę o lokalizacji personelu oraz o lokalizacji wózków transportowych, system sterował zadaniami w taki sposób, aby zminimalizować ryzyko wypadku lub potrącenia.
Koncentracja na ERP
Dziś przed logistyką stawiane są nowe wyzwania, które są połączone z koniecznością szybkiej i sprawnej adaptacji do zmian w środowisku biznesowym. Koordynacja łańcucha dostaw jest jednym z kluczowych elementów sprawnie funkcjonującego przedsiębiorstwa.
Współczesna logistyka musi być gotowa nie tylko na integrację z różnymi działami firmy, ale też z partnerami biznesowymi. Stąd też znaczenie systemów klasy ERP będzie rosło – to one umożliwią pozyskanie wartościowych informacji i danych, które pomagają w usprawnianiu systemów logistycznych.
Komentarze
Wojciech Szmulczyński, dyrektor handlowy, STILL Polska
Współcześnie wciąż jeszcze dość rzadko mamy w logistyce do czynienia z całkowitą automatyzacją – częściej podlegają jej pojedyncze zadania i przeznaczone do ich wykonywania obiekty. W związku z tym równolegle rozwijają się obecnie dwie odmienne koncepcje.
W pierwszej z nich magazyny to całkowicie bezobsługowe obiekty, w których zadania transportu, sortowania, składowania i pobierania realizowane są przez maszyny na podstawie informacji z centralnego systemu WMS czy ERP – w oparciu o technologie kodów kreskowych lub RFID. W ekstremalnych przypadkach, gdy niemal cała powierzchnia magazynu zajęta jest przez regały wysokiego składowania, wózki widłowe nie znajdują zastosowania lub są wykorzystywane pomocniczo. Nie ma tu alejek roboczych, którymi mogłyby poruszać się z ładunkiem, a towary są przemieszczane przy użyciu przenośników czy ruchomych platform.
W drugim modelu zautomatyzowane systemy wózków widłowych wykorzystywane są jako narzędzie pozwalające zwiększyć wydajność i bezpieczeństwo ludzkiej pracy. Rozwiązania takie jak podążający za pickerem iGo neo CX 20, czy samodzielnie lokalizujący odpowiednie stanowisko paletowe MX-X z systemem OptiSpeed 4.0 pozwalają ograniczyć liczbę powtarzalnych ruchów i poprawić ergonomię pracy. Do operatora należą wówczas wymagające dużej precyzji zadania manualne, jak np. pobieranie i kompletacja niespaletyzowanych ładunków.
Artur Thomas, menedżer projektów systemowych, Jungheinrich Polska
W dobie logistyki 4.0 nowoczesne rozwiązania gwarantujące maksymalną wydajność i minimalną awaryjność to za mało, aby spełnić wysokie oczekiwania klientów i umożliwić im skuteczne budowanie przewagi rynkowej. Obecnie, obok najwyższej klasy urządzeń, w tym wózków widłowych, istotną rolę odgrywają rozwiązania softwarowe, pozwalające na prostą, szybką i niezawodną integrację z nadrzędnym oprogramowaniem klienta. Aby uszczelnić łańcuch komunikacyjny i ograniczyć możliwość wystąpienia błędów, Jungheinrich od lat proponuje klientom autorskie rozwiązanie w postaci interfejsu logistycznego. Wózek widłowy wraz z tym oprogramowaniem stanowi gotowy do integracji z systemem informatycznym klienta moduł plug&play. Korzyści płynące z takiej integracji to optymalizacja wykorzystania środków transportu, obniżenie kosztów, łatwość przeprowadzania analiz, co z kolei daje solidne podstawy do planowania. Wszystko odbywa się bez konieczności adaptacji oprogramowania klienta, ponieważ interfejs logistyczny Jungheinrich stanowi uniwersalną platformę komunikacyjną współpracującą z większością rozwiązań klasy ERP/WMS/MES funkcjonujących na rynku. Efektem tej współpracy jest usprawnienie realizacji zlecenia transportowego. Dzięki przesłaniu instrukcji transportowej bezpośrednio do wózka, rozwiązanie aktywnie wspomaga operatora w realizacji codziennych zadań: dobiera optymalną trasę przejazdu oraz automatyzuje proces pobrania oraz odkładania ładunku. W praktyce oznacza to, że operator musi jedynie nacisnąć pedał przyspieszenia. Bezpieczeństwo, wydajność i efektywność procesu wspomaganego przez interfejs logistyczny Jungheinrich doceni każdy kierownik nowoczesnego magazynu.
Wojciech Bytner, dyrektor generalny, Georg Utz Sp. z o.o.
Pojemniki plastikowe to niezbędny element każdego automatycznego magazynu. Służą one do magazynowania oraz transportu wewnętrznego produktów oraz kompletacji zamówień. Gwarantują wielokrotną możliwość wykorzystania przez wiele lat, bezpieczeństwo transportu, oszczędność miejsca i łatwość czyszczenia. Są przystosowane do manipulacji przez robota przemysłowego, umożliwiając precyzyjne zamocowanie na automatycznych przenośnikach. Przykładem pojemnika dedykowanego do systemów automatycznych jest EUROTEC z oferty Georg Utz przeznaczony do współpracy we wszystkich popularnych systemach magazynowych. Pojemnik występuje w bardzo wielu wymiarach oraz wariantach dna. Odpowiednio dobrany rodzaj dna do planowego obciążenia pojemnika eliminuje ewentualną możliwość jego wygięcia oraz zapewnia właściwe przemieszczanie na przenośnikach. Pojemnik ten może być dodatkowo wyposażony w specjalne przegrody dzielące na komory dla ułatwienia przechowywania i kompletacji drobnych produktów. Z naszego doświadczenia wynika, że zautomatyzowanie procesów magazynowych czy produkcyjnych pozwala firmie zoptymalizować i lepiej wykorzystać powierzchnię oraz zwiększyć wydajność procesu kompletacji i dystrybucji towarów, poprzez m.in. ograniczenie błędu ludzkiego. W czasach niskiej podaży siły roboczej ważną korzyścią jest też obniżenie kosztów związanych z poszukiwaniem i zatrudnieniem personelu.
Mikołaj Ruta, dyrektor ds. innowacji i R&D, WDX
Zmiany, jakie na gospodarce wymusza Rewolucja 4.0, są olbrzymie. Inwazja nowoczesnych technologii przekształca modele biznesowe, relacje między pracownikami i firmami, a nawet całe branże. Niektóre są łatwe do zaobserwowania, a inne można porównać do budzącego się nagle wulkanu. Przykładem jest Facebook, Uber, Twitter, Booking, czy Pay Pal. Dzięki inteligentnym technologiom biznes może się rozwijać. Rozwój ten jest bardzo dynamiczny, więc jeśli chce się nadążyć lub wyprzedzić konkurencję, należy nieustannie obserwować trendy oraz wdrażać nowe rozwiązania i technologie. W dzisiejszych czasach nie ma branży, która oparłaby się Rewolucji 4.0. Główne gałęzie gospodarki takie jak finanse, transport, usługi, handel, przemysł, czy administracja bez cyfrowych fundamentów nie są w stanie egzystować. Modele biznesowe, które były przez dziesiątki lat modelami stabilnymi i dochodowymi, dzisiaj wymagają przemodelowania i dopasowania do bieżącej sytuacji makroekonomicznej oraz nowych technologii. Wychodząc naprzeciw dynamicznie rozwijającemu się rynkowi, produkty WDX w 100% wpisują się w nowoczesne trendy Industry 4.0. Dzięki m.in. automatycznym regałom, wózkom Radio Shuttle, systemom przenośników i sorterów, czy innowacyjnemu, chronionemu prawem patentowym Systemu Automatycznego Załadunku Q-Loader, gama produktów WDX S.A. stale poszerza się i obejmuje pełen zakres obszaru magazynowego. Proponowane przez naszych ekspertów rozwiązania pozwalają na optymalizację procesów, obniżenie w znaczący sposób kosztów funkcjonowania magazynów, a także oszczędność miejsc pracy i zwiększenie bezpieczeństwa towarów.
Również w klasycznych magazynach można wdrożyć półautomatyczny model pracy, chociażby dzięki zastosowaniu wózków systemowych Crown, które pozwalają na prowadzenie w pętli indukcyjnej oraz funkcji automatycznego pilota prowadzącego wózek do zadanego miejsca w magazynie.
Karolina Tokarz, prezes zarządu, dyrektor naczelny, PROMAG S.A.
Nowoczesny magazyn nie może funkcjonować bez automatycznych rozwiązań do składowania, kompletacji i transportu, które odciążają człowieka od powtarzalnych, monotonnych, a często niebezpiecznych prac. W ramach naszej oferty polecamy klientom m.in. automatyczne regały gęstego składowania AutoMAG Mover, regały obsługiwane przez układnice magazynowe, regały windowe, karuzelowe, wielopoziomowe systemy transportu i komisjonowania oparte na konstrukcjach pomostów, systemy paletyzacji z użyciem robotów przemysłowych zintegrowane z przenośnikami i urządzeniami do pakowania oraz autonomiczne pojazdy.
Rozwiązania te, poza ograniczeniem zatrudnienia, mogą zdecydowanie poprawić wydajność procesów, a co za tym idzie obniżyć koszty jednostkowe produktu. Maszyna, w przeciwieństwie do człowieka, może pracować cały czas, praktycznie 24 godziny na dobę i jest w stanie wykonać w tym samym czasie zdecydowanie więcej operacji, co sprzyja z kolei obniżeniu kosztów pracy, a jednocześnie pozwala poprawić jakość dostaw, przyspieszyć ich terminy itp. Dzięki automatyzacji można też wyeliminować niemal do zera ewentualne błędy w kompletacji produktów. Oferowane przez nas nowoczesne rozwiązania intralogistyczne to także wymierne oszczędności eksploatacyjne. Dzięki automatycznym systemom składowania na tej samej przestrzeni można zmieścić zdecydowanie więcej towarów − magazyn może być więc mniejszy, co ogranicza koszty jego budowy i późniejszego utrzymania. Automatyzacja wymusza wdrożenie w firmie systemu informatycznego, w którym gromadzone są duże ilości danych. Przetwarzanie tych danych za pomocą technologii Big Data pozwala na dokładniejsze planowanie, optymalizację operacji czy lepsze zarządzanie procesami. Z tego wynika jeden wniosek – inwestowanie w nowoczesne rozwiązania magazynowe to obecnie konieczność.