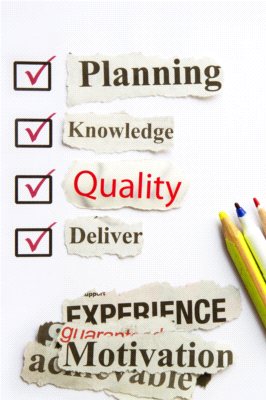
Advanced Product Quality Planning
Jakkolwiek procedury i fazy APQP dotyczą jakości, niezawodności, funkcjonalności dostarczanych końcowemu odbiorcy produktów, to wywierają również zauważalny wpływ na procesy przemieszczania we wszystkich fazach łańcucha dostaw.Współpraca producenta z dostawcami, a także...
Współpraca producenta z dostawcami, a także odbiorcami w zakresie jakości produkowanych wyrobów nie jest zagadnieniem nieznanym partnerom utrzymującym wielostronne kontakty biznesowe. Często jednak występuje ona w stadium szczątkowym, przejawiającym się realizacją procedur reklamacyjnych materiałów, półproduktów, które, ze względu na zbyt niskie parametry jakościowe uniemożliwiające produkcję jakościowo dobrych, akceptowanych przez odbiorców wyrobów finalnych, powinny być zwrócone dostawcy. Pojawia się korekta faktury, wydłuża się termin płatności, być może zaczyna się poszukiwanie nowych dostawców.
Korzyści wzajemnych powiązań dostawców
Ustanowienie wzajemnie korzystnych powiązań między organizacją i jej dostawcami podnosi zdolność do generowania zysków – to jedna z ośmiu zasad, którymi należy kierować się w realizacji celów, jakie stawia przed sobą system zarządzania jakością w oparciu o standard ISO 9000:2000.
Egzekwowanie procedur ISO serii 9000 wymaga od producenta prowadzenia audytów dostawców, a także ich dostawców. Dbałość o jakość produkowanych wyrobów zaczyna się już w przedsiębiorstwie dostawcy, z tą tylko różnicą, że jest to działanie wymuszane przez producenta, a nie świadome działania podejmowane przez wczesną część łańcucha dostaw, czyli wszystkie ogniwa po stronie zaopatrzenia i produkcji.
Orientacja na klienta
Przedsiębiorstwa są zależne od swoich klientów/odbiorców, z czego wynika konieczność identyfikowania się i rozumienia ich aktualnych i przyszłych potrzeb. Przedsiębiorstwo winno nie tylko spełniać oczekiwania swoich odbiorców, ale również podejmować działania pozwalające wykraczać poza tradycyjne pole potrzeb klientów – to również jedna z zasad tworzących podstawy ww. sytemu ISO.
Nie da się ukryć, że system zaawansowanego planowania jakości produktu (APQP) wywiera widoczny wpływ na działania logistyki w sferze zaopatrzenia, logistyki produkcji, a także dystrybucji. To przecież pracownicy działu zakupów zajmują się marketingiem zakupów, szukają dostawców spełniających oczekiwania, jakie, mając na uwadze potrzeby przyszłych odbiorców, artykułują projektanci wyrobów gotowych. To tu pojawiają się plany prowadzenia audytów dostawców i poddostawców.
Zero zwrotów i reklamacji
Dobrze jest, gdy w dbanie o jakość produktu finalnego zaangażowani są wszyscy wytwórcy i podwykonawcy, a nie tylko sam producent. Zagwarantuje to mniej reklamacji i zwrotów, a to już wiele – to „czysty” interes nie tylko dla producenta, ale i dostawców, a wszystko z myślą o spełnianiu oczekiwań odbiorców i ich lojalności. Ten typ dbałości o jakość dotyczy przede wszystkim branż montażowych, czego przykładem jest branża motoryzacyjna.
Warto się tutaj pochylić nad TPS, czyli Toyota Production System – to nie gdzie indziej, a właśnie w Toyocie wymagania co do jakości dostaw, obok ich niezawodności, są priorytetem współpracy partnerów biznesowych.
Ze względu na ciągłe dążenie do likwidacji przejawu największego marnotrawstwa, jakim obok marnotrawstwa czasu są nadmierne zapasy, oraz ze względu na pracę w myśl nowoczesnego pojęcia marketingu „wyczuj i reaguj”, a nie starego „wyprodukuj i sprzedaj”, wszyscy uczestnicy lewej strony łańcucha dostaw zmuszeni są do ciągłego doskonalenia działań, których efektem jest stuprocentowa jakość dostarczanych materiałów i podzespołów. W tym systemie nie ma czasu na dokonywanie rozliczeń reklamacyjnych, negocjowanie wysokości korekt faktur, dokonywanie zwrotów, szukanie nowych dostawców. To się po prostu nie zdarza, gdyż to się nie opłaca.
Jakość w produkcie
Nie można już polegać na masowej kontroli jako sposobie zapewnienia jakości. Należy przede wszystkim zawrzeć jakość w samym produkcie i dążyć do tego, by statystyczne potwierdzenie jakości stało się częścią procesu wytwórczego i sprzedaży. Nie znaczy to, że należy zlikwidować kontrolę jakości, jednak postawienie dużej liczby brakarzy nie zapewni wysokiej jakości. Masową kontrolę jakości, której celem jest wykrywanie już powstałych wad, należy zastąpić tworzeniem jakości od początku.
Należy skończyć ze zwyczajem stosowania wyłącznie kryterium cenowego. Zamiast tego firmy powinny zastosować inne istotne wskaźniki jakości. Organizacje musza zacząć się starać zminimalizować koszt całkowity, a nie tylko koszt początkowy (nie wystarczy kupować tanie materiały – musi się dać z nich zrobić dobry wyrób). Dążyć do tego, by każdy element dostarczał jeden dostawca na zasadzie długotrwałej współpracy opartej na zaufaniu i lojalności.
Jedność online
Cena nie jest ważna aż do chwili, gdy się ją powiąże z jakością zakupu. Narzędzia statystyczne są firmom bardzo potrzebne do oceny jakości kupowanych części i jakości pracy dostawców. Generał Motors korzysta z technik komputerowych do utrzymywania bliskich związków ze swoimi dostawcami. Koncern i jego dostawcy działają jak jedna firma. GM przyłączył dostawców do swojej wewnętrznej organizacji za pomocą sieci komputerowych. I chociaż GM oraz jego dostawcy są nadal odrębnymi przedsiębiorstwami, dzięki łączom komputerowym stają się w praktyce jedną korporacją.
Wszystkie informacje związane z planami produkcji, a w związku z tym potrzebami materiałowymi są znane dostawcom online. W ten sposób nie tylko jakość uległa poprawie, ale z punktu widzenia logistyki koszty opracowywania zamówień, realizacji dostaw uległy znacznemu obniżeniu, oczywiście nie bez znaczenia jest tu także obniżenie kosztów gromadzenia i utrzymania zapasów, po tej stronie łańcucha dostaw.
To dwie z 14 zasad głoszonych przez twórcę tzw. cyklu ciągłego doskonalenia Edwardsa Deminga amerykańskiego specjalisty statystyka – doskonale wpisujące się w filozofię APQP.
Przykładem relacji opartych na wzajemnym zaufaniu jest wspomniana już Toyota, a także twórcy APQP – amerykańskie koncerny GM, Ford, Chrysler. Być może potrzebą stworzenia takiego systemu dbania o jakość produkowanych aut jest fakt, że „trójca” amerykańskiej potęgi motoryzacji nigdy nie mogła wyprzedzić w rankingach jakości aut Toyoty, produkowanych na rynek amerykański.
Jakość świadczy o gotowości
Jedna z siedmiu zasad przewodnich Toyota Motor Corporation brzmi: „Pracować z partnerami gospodarczymi w dziedzinie badań i projektowania, aby osiągnąć stabilny, długoterminowy wzrost, a przy tym stale otwierać się na nowe partnerstwo.”
W strategii JiT, którą jako pierwsza wprowadziła Toyota, jakość ma pierwszorzędne znaczenie. Zapasy spełniające rolę bufora, którego zadaniem była amortyzacja usterek, niedociągnięć, kiepskiej jakości, innych problemów w tej strategii są zminimalizowane, planowanie staje się krótkookresowe. Następuje wdrażanie koncepcji „ssania” – eliminowania z całego systemu przemieszczania wąskich gardeł. Pierwszym celem tego systemu jest usunięcie zaburzeń w produkcji. Firma wdrażająca ten system napotka na poważne problemy, jeśli nie dbała uprzednio o jakość części, materiałów przepływających przez system. Przy braku bezpieczeństwa w postaci zapasów linia produkcyjna zostanie zatrzymana w przypadku wykrycia wadliwej części podzespołu. Fala skutków przeniesie się w dół unieruchamiając cały system produkcji – (Robin Plummer – „Podręcznik zarządzania jakością”, PWN, Warszawa 2002).
Dla kogo APQP?
Od działań wymuszanych procedurami ISO, BRC oraz innymi systemami jakości przechodzimy do etapu świadomego uczestnictwa w kształtowaniu jakości produktu, poczynając od surowców, a kończąc na kolejnych odmianach wyrobów gotowych o funkcjach, użytecznościach, parametrach oczekiwanych przez odbiorców.
Producentów można podzielić na trzy grupy: po pierwsze – firmy, dla których zapewnienie jakości wyrobów zostało wymuszone przez potencjalnych odbiorców – jako warunek współpracy, po drugie – producentów, dla których wdrożenie systemu jest tylko i wyłącznie elementem marketingu – znak wodny na fakturze, certyfikaty na stronie internetowej, oraz przedsiębiorstwa, które są świadome potrzeb zapewnienia jakości swoich wyrobów, bo tego wymagają partnerskie, pełne szacunku kontakty biznesowe. Można z całą odpowiedzialnością stwierdzić, że APQP dotyczy właśnie tej ostatniej grupy przedsiębiorców.
W ramach APQP wymaga się przeprowadzenia dwóch rodzajów analizy: FMEA projektu (w fazie projektowania wyrobu i budowy prototypu) oraz FMEA procesu (w fazie uruchomienia produkcji partii próbnej).
Analiza FMEA
Analiza FMEA jest jedną z metod statystyki opisowej wykorzystywaną w sterowaniu jakością procesów produkcyjnych. Failure Mode and Effect Analysis oznacza „analizę przyczyn i skutków wad”. Początki tej metody sięgają lat 60-tych XX wieku, kiedy FMEA została opracowana przez agencję amerykańską NASA w związku z programem lotów kosmicznych. Metoda spotkała się z ogromnym uznaniem i wkrótce zainteresował się nią przemysł energetyki jądrowej, a także przemysł motoryzacyjny.
Jej stosowanie dzieli się na dwa etapy: konstruowanie – Design FMEA oraz produkcję – Product FMEA. Lata 80-te ubiegłego wieku to okres szerokiego (właściwie wymuszonego) stosowania tej metody również przez dostawców koncernów motoryzacyjnych. Przyczyną pojawienia się FMEA jako metody sterowania jakością był wynik obserwacji błędów w fazach kolejnych etapów produkcji. Około 75 procent wszystkich błędów powstaje w fazie przygotowania produkcji, ale ich wykrywalność na tym etapie jest niestety niewielka i rośnie dopiero w czasie ostatecznej kontroli – funkcjonowania i eksploatacji wyrobu gotowego. Tak późne ujawnianie i usuwanie wad jest niestety kosztownym przedsięwzięciem, a w szczególności, gdy wyrób gotowy jest skomplikowany i stosunkowo drogi, jakim jest np. samochód. Warto zauważyć, że koszty usuwania wcześniej nie wykrytych błędów rosną wykładniczo, osiągając swoje maximum w fazie montażu i eksploatacji. To właśnie analiza FMEA i jej stosowanie odwróciło ten trend, pozwalając na wczesne wykrywanie i eliminowanie błędów. (Tabela 1)
W fazie prac projektowych szuka się wszelkich informacji o możliwych słabych stronach, punktach przyszłego wyrobu. Na tym etapie dokonuje się jeszcze możliwych zmian w przyszłej konstrukcji. Warto zauważyć, że na tym właśnie etapie wykrywania błędów i niedociągnięć wymaga: się od projektantów szerokiej wiedzy w zakresie projektowania, technologii, produkcji, a także eksploatacji.
Fazy APQP
1. Planowanie i określenie programu
Podstawowy cel to sprecyzowanie potrzeb i oczekiwań klienta w połączeniu z planowaniem oraz definiowaniem programu jakości. Wiadomym celem każdego programu jest spełnianie oczekiwań odbiorcy po konkurencyjnych kosztach. Wstępny krok fazy to zapewnienie, że potrzeby i oczekiwania odbiorcy są w pełni zrozumiałe.
2. Projektowanie i rozwój wyrobu
Podstawowy cel to wykonanie kompletnej i krytycznej analizy wymagań technicznych. Wyrób zostanie wstępnie zbadany pod kątem jego wykonalności oraz znalezienia potencjalnych problemów, jakie mogą wystąpić w trakcie produkcji. Poprzez określenie „wykonalność wyrobu” rozumiane jest zapewnienie: realizacji przyjętych wielkości produkcji oraz planów ich wykonania; spełnienia wymagań technicznych wyrobu; spełnienia wymagań jakościowych oraz niezawodności wyrobu; nie przekroczenia budżetu inwestycyjnego; realizacji planu rozwoju wyrobu w czasie.
3. Projektowanie i rozwój procesu
Podstawowy cel to ustalenie głównych cech systemu produkcji oraz związanych z nim planów kontroli, zapewniających osiągnięcie ustalonej jakości wyrobów. Rezultatem tych działań ma być zapewnienie efektywnego systemu produkcji spełniającego wymagania, potrzeby i oczekiwania odbiorcy. (Tabela 3)
4. Walidacja wyrobu i procesu
Walidacja procesu produkcji następuje poprzez ewaluację serii próbnej. Podczas produkcji serii próbnej zespół APQP ocenia, czy plan kontroli, i przebieg procesu są przestrzegane, a produkowany wyrób spełnia wymagania. Dodatkowo zespół sprawdza, czy w produkcji seryjnej nie pojawiają się czynniki wymagające podjęcia działań dla zapewnienia jakości wyrobu.
5. Analiza informacji zwrotnych i działania korygujące
Analizie poddaje się informacje pozyskane w trakcie rozwoju projektu. Celem analizy jest wykorzystanie doświadczeń projektu podczas wdrażania nowego dla uniknięcia wcześniej popełnionych błędów.
Perfekcja jakościowa produktu, na jaki oczekuje odbiorca, w zdecydowany sposób wpływa na obniżenie kosztów przepływów materiałowych, m.in. związanych z: opracowywaniem dodatkowych zamówień; stratą czasu na procedury reklamacyjne w relacji odbiorca–producent– dostawca; eliminacją zapasów międzyoperacyjnych – nie ma wadliwych części; koniecznością unieruchamiania produkcji – nie ma wadliwych części.
Partnerskie kontakty biznesowe w relacji producent–dostawca, producent–odbiorca z punktu widzenia producenta jest w dłuższej perspektywie opłacalne dla wszystkich uczestników łańcucha dostaw. Takie traktowanie klientów przekłada się na ich lojalność. Odczuwa to producent, ale czuje także i jego dostawca.