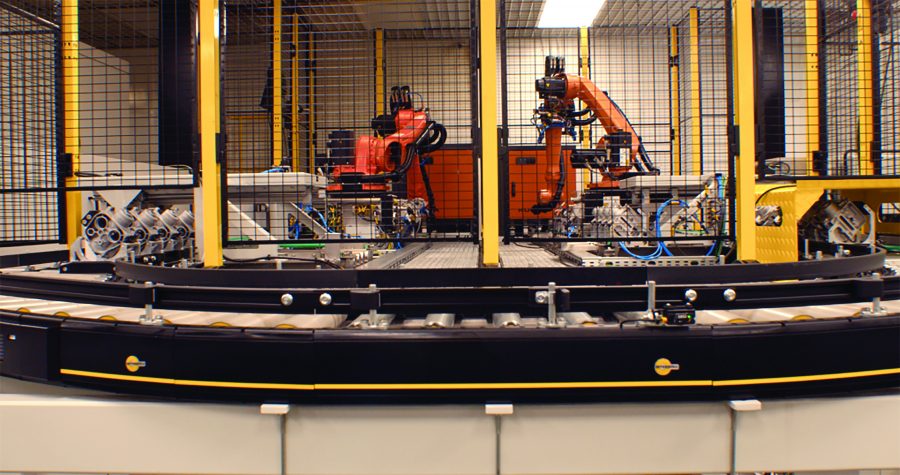
Automatyzacja w zakładzie ZF w Gliwicach
ZF specjalizuje się w dostarczaniu zaawansowanych technologicznie rozwiązań dla producentów samochodów. Wdrożenie automatyzacji linii produkcyjnej elektrycznego wspomagania hamulcowego w zlokalizowanym w Gliwicach zakładzie pozwoliło poprawić stabilność procesów. Dzięki większej powtarzalności operacji i obniżeniu ryzyka błędu ludzkiego podczas produkcji możliwe było zwiększenie standardów jakości wyrobów i uzyskanie wyższej wydajności.
Dostarczając wysokiej klasy zintegrowane systemy układu wspomagania hamowania, ZF musi sprostać rosnącym wymaganiom i konkurencji w branży. Wiąże się to z koniecznością zapewniania coraz większej funkcjonalności oferowanych wyrobów oraz automatyzacją produkcji, pozwalającą osiągnąć wymaganą jakość.
Oferujemy kompleksowe rozwiązania dla producentów pojazdów oraz dostawców usług transportowych w czterech obszarach technologicznych, takich jak sterowanie ruchem pojazdów, zintegrowane bezpieczeństwo, zautomatyzowana jazda oraz elektromobilność. Technologia ZF umożliwia pojazdom „widzenie, myślenie i działanie” (ang. „see, think, act”) – mówi Wojciech Jasiński, starszy automatyk obróbki maszynowej w ZF.
Dlaczego automatyzacja?
Realizując produkcję dla wymagającego sektora motoryzacyjnego, ZF dąży do stałego doskonalenia wytwarzania i poprawy jakości wyrobów końcowych. W 2017 roku powstała w gliwickim zakładzie koncepcja wprowadzenia automatyzacji linii, mająca na celu zwiększenie produkcji i poprawę jakości.
Jednym z najważniejszych elementów wdrożenia miało być wprowadzenie systemu traceability zapewniającego pełne śledzenie części w procesie produkcyjnym i wyeliminowanie ryzyka błędów – wspomina Wojciech Jasiński.
Do realizacji tego celu konieczne było automatyczne znakowanie i nadawanie unikalnych numerów seryjnych zgodnie ze standardem ZF. Przed wdrożeniem operator musiał każdą część pojedynczo wkładać do znakowarki laserowej, co łącznie zajmowało około 40 sekund. Automatyzacja i zastosowanie lasera miały zredukować ten czas do jedynie sześciu sekund w pełnym cyklu.
Celem automatyzacji była także poprawa efektywności i podniesienie wskaźników produkcyjnych poprzez wykonanie tej samej pracy przy użyciu dziewięciu maszyn obsługiwanych przez mniejszą liczbę operatorów w trójzmianowym systemie pracy. Kolejnym spodziewanym efektem miała być poprawa jakości wynikająca ze zwiększenia sterylności procesów produkcyjnych.
Zachowanie wysokich standardów czystości części jest priorytetem w produkcji elektrycznych układów wspomagania, gdyż nawet najmniejsze zanieczyszczenia mogą prowadzić do zwarcia układów PCB. Sama myjnia komponentów wymagała zwiększenia wydajności oraz niezawodności procesów. Nasz wybór padł na myjnię tunelową, w której mycie i suszenie podzielone jest na kilka etapów. Myjnia ta zapewnia uzyskanie takiego samego czasu cyklu pracy przy liczbie maszyn zredukowanej do dziewięciu – mówi Wojciech Jasiński.
Zastosowana technologia i koncepcja wdrożenia automatyzacji
Rozważając wybór dostawcy technologii i rozwiązań automatyzujących linię produkcyjną, brano pod uwagę przede wszystkim zdolność do wdrożenia koncepcji, ale także kreatywność proponowanych koncepcji inżynierskich. Ostatecznie, w wyniku procesu wyboru dostawcy zdecydowano się na rozwiązania oferowane przez firmę NOYEN.
Najbardziej w nasze wymagania wpisała się firma NOYEN. Już na etapie ofertowania zauważyliśmy otwartość i elastyczność naszego partnera, co sobie zawsze bardzo cenimy. Mieliśmy świadomość, że w trakcie trwania projektu będzie następowało wiele zmian, które tej elastyczności będą wymagały. Obustronne pomysły zaowocowały stanem, jaki mamy na tę chwilę. W czasie planowania rozwiązań staraliśmy się także przewidzieć, co jeszcze będziemy chcieli zrealizować w przyszłości i zapewnić w projekcie możliwość rozbudowy – wspomina Wojciech Jasiński.
Podczas projektowania przez firmę NOYEN zautomatyzowanej linii myjącej wykorzystane zostały rozwiązania Siemensa: Solid Edge do modelowania 3D, Teamcenter do przepływu dokumentacji oraz TIA Portal.
Z satysfakcją odnotowaliśmy fakt, że zastosowana technologia Siemensa, zarówno na poziomie hardware (SIMATIC S7-1500F, przemysłowy komputer panelowy SIMATIC IPC, urządzenia sieciowe SCALANCE), jak i software (Teamcenter oraz TIA Portal), przyczyniła się do sprawniejszej pracy projektantów oraz inżynierów automatyków NOYEN, a w efekcie osiągnięto zamierzoną optymalizację produkcji w zakładzie ZF. Branża, w jakiej działa ZF należy do najbardziej konkurencyjnych i jednocześnie wymagających, jeżeli chodzi o jakość – mówi Maciej Gryczewski, odpowiedzialny za współpracę z producentami maszyn w firmie Siemens.
Pierwszy element instalacji – myjnia – zamówiony został już w lutym 2018 r. W zautomatyzowanej linii wykorzystana została myjnia z serii NOYEN Ekspert zapewniająca wymaganą wysoką klasę czystości. Następnie dostarczane były: system paletyzacji, myjka do przekładek, system transportu wraz z automatyzacją pierwszej obrabiarki i automatycznym znakowanie kodu DMC na odlewach.
Projekt rozpoczął się od dostarczenia maszyny myjącej z systemem palet. Później system został rozbudowany o paletyzację i myjnię do opakowań. W kolejnym etapie zautomatyzowany został system transportu i znakowania laserowego części – mówi Rafał Włosek, Senior Technical Advisor Engineer z firmy NOYEN.
Automatyzacja pierwszej obrabiarki odebrana została w połowie 2020 r.
Zautomatyzowana, modułowa linia produkcyjna
W ramach procesu produkcji wykonywany jest załadunek, obróbka detali, transport do myjni, mycie i odmuchiwanie, kontrola jakości oraz znakowanie wyrobu. Istotnym etapem procesu jest oczyszczanie detali z zanieczyszczeń. Po zakończeniu mycia, paletki przemieszczane są do systemu paletyzacji, gdzie mogą być pakowane równolegle dwie referencje detali. Układ paletyzacji wyposażony został w system kontroli jakości. Za pomocą profilomierza sprawdzane są punkty charakterystyczne. Jeśli kontrola jakości przebiegnie pomyślnie, wówczas detale trafiają do czystych opakowań. System paletyzacji układa opakowania jedno na drugim, przy czym liczba warstw jest programowalna. Wprawdzie wymiana stosów paletek odbywa się ręcznie, jednak rozwiązanie to zostało przystosowane do obsługi za pomocą robotów AGV, co pozwoli na wdrożenie ich w przyszłości. Sterowanie całej linii realizowane jest poprzez zaawansowany sterownik SIMATIC S7-1500F. Wizualizacja procesu oraz wprowadzanie nastaw jest możliwe dzięki komputerowi panelowemu SIMATIC panel PC. Wymiana danych pomiędzy poszczególnymi urządzeniami automatyki bazuje na standardzie Profinet, w warstwie fizycznej wykorzystywane są urządzenia sieciowe SCALANCE.
Podczas wdrożenia do najważniejszych wyzwań należało m.in. zapewnienie możliwości rozbudowy i modułowości. Ta część realizacji, dotycząca działu obróbki, stanowiła najistotniejszą część projektu.
Układ od początku miał być modułowy, złożony z elementów i podzielony na stacje. Na linii musieliśmy przewidzieć możliwość instalacji dodatkowych urządzeń, takich jak systemy pomiarowe. Automatyzacja nie mogła blokować dostępu do obrabiarek CNC, a w przypadku pracy manualnej operator musiał mieć zapewnioną właściwą przestrzeń pracy – mówi Rafał Włosek.
W projekcie należało także zadbać, by automatyzacja nie blokowała wymiany narzędzi i stołów mocujących w obrabiarkach. Sama linia działa obecnie w taki sposób, aby można było wyłączyć każdą z obrabiarek bez zakłócania produkcji. Posiada ona także możliwość wprowadzania części produkowanych manualnie.
Modułowość linii produkcyjnych to element koncepcji Industry 4.0. Podział linii montażowej na moduły umożliwia producentom dostosowanie się do zmieniających się potrzeb klienta. W miejsce jednego modułu można dodać inny – lub rozszerzyć linię o nowy moduł funkcyjny, technologiczny czy procesowy – dodaje Maciej Gryczewski.
Obecnie rola operatora ogranicza się do załadunku odlewów na paletę i zapewnienia dostarczania opakowań w sposób płynny, umożliwiający ciągłość produkcji. Jednak człowiek wciąż odgrywa w procesie produkcji ważną rolę, co dotyczy głównie operatorów zajmujących się ustawieniami maszyn CNC.
Zdecydowana większość pracowników dostrzegła w automatyzacji możliwość rozwoju osobistego wiążącego się z unowocześnieniem zakładu. Zadaniem operatorów jest obecnie wykonywanie regularnych pomiarów i korygowanie procesu, a także wymiana zużytych narzędzi. Maszyna ułatwia pracę ludziom, zliczając automatycznie liczbę wykonanych cykli i zatrzymując się w przypadku niedokonania wymiany w określonym czasie – dodaje Wojciech Jasiński.
Korzyści z wdrożenia
Wdrożenie automatyzacji pozwala w pełni kontrolować proces produkcyjny, zapewniając w 100 procentach jego śledzenie – traceability – i przyczyniając się do wzrostu jakości produkcji. Dzięki zmianom w procesie linia wytwarzania może być obecnie obsługiwana w sposób optymalny przez zaledwie jednego operatora, zamiast trzech. Wpłynęło to na obniżenie kosztów produkcji, dzięki czemu ZF jest w stanie oferować swoje produkty – systemy hamulcowe – w bardziej konkurencyjnych cenach. Wraz z automatyzacją poprawiła się również elastyczność produkcji przejawiająca się w uniezależnieniu działania całej linii od pojedynczej awarii. Dzięki wdrożeniu rozwiązania składającego się z jednej maszyny CNC i jednego robota dla każdego stanowiska wszystkie maszyny mogą pracować z obwodem bezpieczeństwa, którego rozpięcie (otwarcie osłon) nie wpływa na pracę pozostałych urządzeń.
Zwiększyła się także wydajność transportu oraz wydajność myjni i stopień czystości opuszczających ją detali. Nowa myjnia gwarantuje spełnienie wysokich wymagań czystości, jakości powierzchni po myciu oraz parametrów dotyczących suszenia. W procesie pakowania dodany został profilometr laserowy, który sprawdza charakterystyczne wymiary każdej części. Kontroluje on między innymi, czy wszystkie operacje zostały wykonane oraz czy nie doszło do uszkodzeń narzędzi.
Zastosowane rozwiązania Product Lifecycle Management (PLM), czyli Siemens Teamcenter, przyczyniły się do licznych korzyści w fazie projektowej wdrożenia. Do najistotniejszych z nich należy zapobieganie ewentualnym błędom w projekcie, co pośrednio sprzyjało jakości instalacji automatyki. Narzędzia PLM umożliwiły też przyspieszenie procesów projektowania oraz ograniczenie kosztów operacyjnych organizacji, a także zapewniły lepszą kontrolę nad projektem w każdej jego fazie.
W wyniku wdrożenia automatyzacji nastąpił wzrost wydajności produkcji. Obecnie wskaźnik OEE (Overall Equipment Effectiveness) dla pracy automatycznej jest wyższy niż przed wdrożeniem. Wynosi on 95%, co stanowi poprawę o 10 punktów procentowych w porównaniu do wcześniejszej pracy manualnej.
Plany na przyszłość
Obecnie realizowany jest etap uruchamiania następnych maszyn w całym systemie oraz planowane są kolejne etapy inwestycji. W fazie koncepcji znajduje się m.in. dodanie do procesu komparatora pomiarowego w obszarze myjni i paletyzacji. Zadaniem robota będzie odkładanie w określonej sekwencji części z poszczególnych wrzecion/gniazd w celu dokładnych pomiarów porównawczych z wzorcowym detalem. Na bazie tych pomiarów planowane jest przesłanie informacji do osób odpowiedzialnych za utrzymanie procesu oraz do działu jakości. W dalszym etapie wdrażania komparator ten będzie mógł sam wysyłać do obrabiarki komendy wprowadzenia korekty określonych wymiarów. Rozważana jest także koncepcja automatyzacji procesu pobierania odlewów z opakowań dostawcy i ich załadunek na paletę transportową. Zostały już przeprowadzone próby w tym zakresie.
Mamy również inne pomysły, które chcielibyśmy zrealizować w niedługim czasie. Sytuacja rynkowa uległa zmianie, Covid-19 pokrzyżował wiele planów, ale nie zamknął wszystkich możliwości. Aspekty finansowe dotyczące inwestycji zawsze są właściwym motywatorem podejmowania nowatorskich projektów, przynoszących wymierne oszczędności – mówi Wojciech Jasiński.