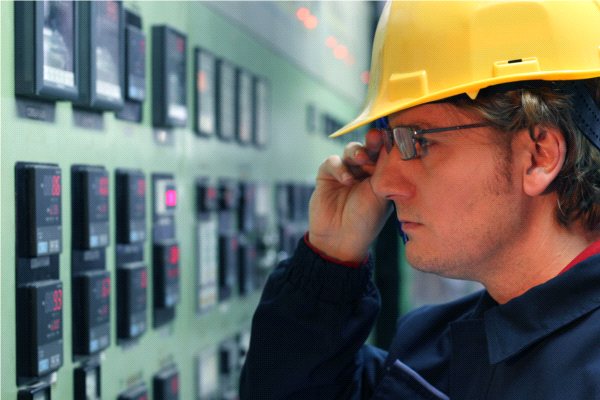
CMMS na drodze do TPM
Dziś nikt w fabryce nie wyobraża sobie pracy bez CMMS z wynikami Yield i Availablity na poziomie 98 procent przy produkcji 24 godziny na dobę. A od kiedy zespół wszedł głębiej w metodologię Lean - TPM, współpraca Działu Utrzymania Ruchu i Działu Produkcji praktycznie zatarła...
Była wiosna 2004, gdy ogłoszono coroczne wyniki benchmarkingu fabryk Grupy. Gdyby nie ostatnia blokada suszarni, nasz zakład zająłby pierwsze miejsce po raz trzeci z rzędu, co byłoby osiągnięciem bez precedensu. Zabrakło setnych części procenta Yield (uzysk produkcyjny – stosunek produkcji bez wad do całej produkcji) oraz Availability (dostępność maszyn dla produkcji, tutaj dostępność linii produkcyjnej czyli całej fabryki – stosunek rzeczywistego czasu produkcji do czasu planowanego produkcji) i tym razem laur zwycięzcy przypadł innej fabryce z Grupy.
Początki bez wsparcia
W 1998 roku nikt z naszego zakładu nie myślał o rywalizacji z ponad setką fabryk światowego konglomeratu. Moja kariera w firmie rozpoczęła się w drugiej fazie budowy fabryki płyt kartonowo-gipsowych. Większość prac budowlanych była już wykonana i zbliżała się faza dostaw i instalacji urządzeń. Równolegle należało rekrutować pracowników do powstającej fabryki – a w moim przypadku do powstającego działu utrzymania ruchu.
Jeśli uczyć się na błędach, to znacznie taniej na cudzych
Szczęśliwie strategia inwestora obejmowała szkolenia w jego zagranicznych fabrykach, zarówno dla kadry zarządzającej, jak i szeregowych pracowników produkcji. Stratedzy inwestora nie mieli dobrego mniemania o umiejętnościach specjalistów od gipsu w nowo powstającej fabryce, postanowili więc zatrudnić „gipsowych” laików, a następnie wyszkolić ich po swojemu.
Pod koniec XX w. w wielu fabrykach Grupy standardem był CMMS jako element wpierający organizację utrzymania ruchu. W odróżnieniu od fabryk zachodnich standardem w nowej fabryce był brak tego typu oprogramowania. Można było znaleźć w Polsce zakłady realizujące planowe utrzymanie ruchu, ale w oparciu o system papierowych rejestrów, co ograniczało ilość urządzeń objętych systemem oraz zwiększało liczbę etatów biurowych, a tym samym podnosiło koszty.
Potrzebny CMMS
W owym czasie posiadałem już doświadczenie w organizowaniu od podstaw utrzymania ruchu w dwóch mniejszych fabrykach oraz wiedzę o systemach CMMS, ponieważ wcześniej pracowałem w działach IT. Tym razem w trakcie szkoleń mogłem podpatrzeć zastosowanie CMMS w praktyce i podyskutować z użytkownikami systemu, zarówno z kierownikami i specjalistami, jak i robotnikami liniowymi. Te nowe doświadczenia, jak i prosta obserwacja liczby maszyn (obiektów), które powinny zostać objęte planowaną obsługą techniczną – w fabryce zbliżała się ona do 1000 – zachęcały do rozważenia implementacji CMMS w nowo powstałej fabryce.
Wprowadzanie danych rozpoczęto od tych maszyn, o których wiedziano, że będą potrzebowały częstej obsługi
Po własnej analizie, biorąc pod uwagę również wymogi niezawodnościowe i fakt, że prawie cała fabryka płyt kartonowo-gipsowych to jedna linia produkcyjna, a awaria jednego elementu linii zatrzymuje całość, na uruchomienie której potrzeba minimum pół godziny, doszedłem do wniosku, że w nowej fabryce nie ma co marzyć o sukcesie bez właściwie wdrożonego CMMS. Własna analiza to jednak za mało, żeby przekonać inwestora do dodatkowych wydatków przy i tak przekroczonym budżecie budowy.
Współpraca pod warunkami
Dyskusja z kierownikiem projektu budowy fabryki była długa i wieloetapowa. Szczęśliwym zbiegiem okoliczności znana z doskonałego CMMS amerykańska firma software’owa (Datastream – USA z systemem MP2 „Massachusetts Power-Station” opartym na bazie danych Microsoft’u) postanowiła wejść na polski rynek i poszukiwała okazji do pilotowego wdrożenia. Można było uzyskać spory upust przy zakupie 10 licencji, o ile znalazłaby się u klienta kompetentna osoba wspierająca reklamę oprogramowania prelekcjami o jego udanym wdrożeniu.
Środki były ograniczone, co nie dawało szansy na solidne wsparcie przez zewnętrznego konsultanta w trakcie wdrożenia. W tych warunkach wdrożenie musiało zostać przeprowadzone samodzielnie wspólnie z nowo powstałym zespołem utrzymania ruchu.
Poza tym jeśli praca jest warta wykonania, to jest warta zrobienia dobrze, więc przede wszystkim potrzebny był dobry plan wdrożenia, „rozbijający” całość na etapy.
Przygotowania do wdrożenia
Pierwszy etap stanowiło szkolenie, w którym uczestniczyłem, po którym nastąpiło wieloetapowe i dopasowane do potrzeb każdego z osobna szkolenie kolegów w dziale. Niektórzy startowali od pierwszego kontaktu z komputerem, a inni z wiedzą inżyniera automatyka.
W tym samym czasie pracownicy uporali się ze sprzętem komputerowym i doprowadzili do sytuacji, w której można było zacząć korzystać z systemu z zapewnieniem okresowych kopii zapasowych bazy danych. Okresowe backupy takiej bazy to minimum gwarantujące niezawodne działanie systemu, niezależnie od możliwych awarii jego hardware’u. Udało się ten etap połączyć z fizycznym utworzeniem magazynu części zamiennych i wprowadzeniem danych o pozycjach magazynowych do modułu magazynowego.
CMMS przede wszystkim uwolnił pracowników od mechanicznych czynności planistycznych i pamiętania o wszystkich pracach
Równolegle z magazynem wystartowała rejestracja maszyn (obiektów podlegających obsłudze technicznej). Rekordy dla swoich maszyn zakładali inżynierowie odpowiedzialni za odpowiedni obszar fabryki czy specjalizację. Pracę częściowo ułatwiła firma outsourcingowa, która zorganizowała smarowanie i w ramach swojego kontraktu (wtedy również pionierskiego w Polsce) wprowadziła do swojej bazy danych część maszyn. Pozostało tylko przetransferować dane pomiędzy bazami.
Właściwa motywacja
Niezależnie od tego ułatwienia zdawałem sobie sprawę, że pracownicy będą czuli się przeciążeni nawałem prac zbiegających się z odbiorami urządzeń i uruchomieniem produkcji. Pracownicy potrzebowali więc motywacji do wytężonej pracy. Zadbałem, aby inżynierowie dobrze zrozumieli przyszłą korzyść z funkcjonowania CMMS. Wprowadzanie danych rozpoczęto od tych maszyn, o których wiedziano, że będą potrzebowały częstej obsługi, i zaraz potem każdy z inżynierów mógł zaplanować zadania generujące zlecenia pracy obsługi tychże maszyn. To pozwoliło zasmakować efektów pracy CMMS na bardzo wczesnym etapie wdrożenia, a tym samym szkolić pracowników wykonujących zlecone „przez system” prace i uczyć się na błędach.
Jednocześnie wszyscy szybko przekonali się, że dobrze zdefiniowany obiekt-maszyna z przypisanymi do niego zadaniami oraz z częściami zamiennymi pozwala o sobie „zapomnieć”. To CMMS pamięta o konieczności wykonywania zdefiniowanych prac. Ta wyraźna korzyść i ułatwienie w codziennej pracy inżynierów motywowała do tworzenia następnych obiektów w CMMS i wprowadzania nowych danych.
W ten sposób w miarę wprowadzania następnych maszyn (obiektów) i przypisywania im potrzebnych zadań można było stopniowo zmieniać inżyniera planistę prac (to robi CMMS) w inżyniera analizującego techniczne i ekonomiczne skutki wykonywania tak zaplanowanych prac. Zaraz po rozpoczęciu wprowadzania danych do modułu magazynowego możliwe też stało się wprowadzanie dostawców części i usług do modułu zakupowego.
Cudze sukcesy i błędy
Dzięki zagranicznym szkoleniom mogłem obserwować fabryki, którym nawet prosty CMMS dawał wymierne korzyści – działo się to tam, gdzie pracownicy utrzymania ruchu dobrze rozumieli jego działanie i gdzie oni sami wprowadzali potrzebne dane.
Nadarzyła się okazja zabrać wszystkich pracowników utrzymania ruchu (w dwóch turach) do fabryki, gdzie mogli zobaczyć, jak funkcjonuje taki system, jak generowane są zlecania pracy, jak zorganizowana jest ich cyrkulacja i jak wprowadzane są dane o wykonanych zleceniach pracy.
Miałem też okazję obserwować nieudane wdrożenie – osobno zatrudnieni pracownicy z zewnątrz wprowadzali do systemu dane w całkowitym oderwaniu od rzeczywistych działań pracowników utrzymania ruchu. Doprowadziło to w rezultacie do powstania w pełni uzupełnionej bazy danych, która została oceniona przez pracowników Działu Utrzymania Ruchu jako nieprzydatna i praktycznie zignorowana. To była doskonała lekcja, bo jeśli uczyć się na błędach, to znacznie taniej na cudzych.
Co zmienił CMMS?
CMMS przede wszystkim uwolnił pracowników od mechanicznych czynności planistycznych i pamiętania o wszystkich pracach, zwłaszcza o tych ważnych i najważniejszych, o których zapomnieć nie wolno. Pozwolił dzięki temu myśleć więcej o strategii utrzymania ruchu, pozwolił znaleźć czas na doskonalenie maszyn i działań. W końcu dał szansę na wdrożenie metod Lean-TPM i praktycznego zasmakowania continuous improvement.
Nie przypuszczałem, że kiedykolwiek fabryka zajęłaby pierwsze miejsce w Grupie bez tego systemu. Byłoby dużo więcej codziennych problemów, więcej nerwów, przy dużo gorszych efektach. Na szczęście nie ma światów równoległych i nie wypróbujemy dla fabryki tego drugiego, mniej optymistycznego wariantu bez CMMS.