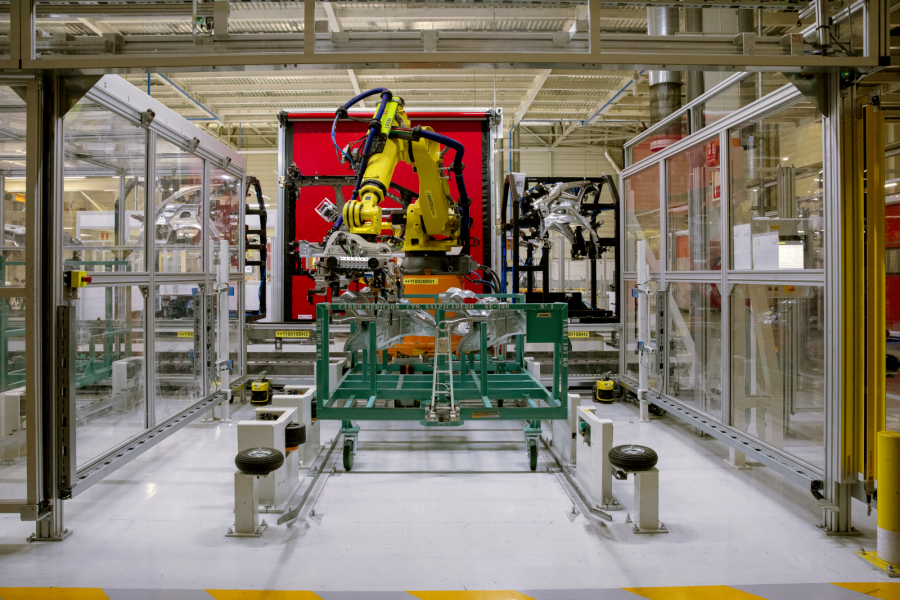
Droga do precyzji
SEAT S.A. w macierzystym zakładzie w Martorell nieustannie wprowadza nowe technologie, które pomagają producentowi samochodów w poprawie wydajności i jakości. Zupełną nowością jest innowacyjny system pomiarowy, który przeniósł procesy kontroli jakości na nowy poziom. Hiszpańska marka rozwija się też w obszarze robotyzacji, wprowadzając nowe maszyny i opracowując dla nich systemy predykcyjne.
W zakładach pod Barceloną od niedawna działa innowacyjny system pomiarowy. Program ma zapewnić precyzję dziesiętnych części milimetra przy tworzeniu bezpieczniejszych i wygodniejszych samochodów. Zastosowanie technologii fotogrametrii pozwoli na zbadanie nawet 210 000 000 punktów dziennie. Rozwiązania fotogrametryczne są obecnie stosowane na linii montażowej SEAT-a Leona i CUPRY Formentora.
SEAT jest pierwszym producentem samochodów, który wdrożył bezdotykowy pomiar karoserii na masową skalę. Dotąd kontrola w zakładach hiszpańskiej marki odbywała się w trybie półręcznym. Punktem zwrotnym w zwiększeniu wydajności procesu po dotarciu samochodu na linię produkcyjną okazało się zastosowanie innowacyjnej, zautomatyzowanej technologii bezkontaktowej.
– Fotogrametria to optyczna technologia pomiarowa, która pozwala nam uchwycić na zdjęciach miliony punktów danej powierzchni, oznaczając głębokość i grubość każdej przestrzeni – wyjaśnia Pedro Vallejo, szef działu technologii pomiarowych SEAT. – Zebrane punkty są rejestrowane na kolorowej mapie, która wskazuje nawet najmniejsze odchylenia od normy.
Jak to działa?
Zestawy części karoserii samochodów są losowo wybierane z linii montażowej i dokładnie sprawdzane podczas każdej zmiany produkcyjnej. Zautomatyzowane systemy transportują te komponenty do obiektów pomiarowych. Tam wyposażone w kamery maszyny zajmujące przestrzeń 1500 metrów sześciennych rozpoczynają kontrolę, aby wszystkie pojazdy opuszczające linię produkcyjną miały odpowiednie wymiary. Dzięki temu procesowi wszelkie odchylenia można szybko ponownie skalibrować.
– Na zdjęciach widzimy 100% linii geometrycznych pojazdu, zarówno wewnętrznych, jak i zewnętrznych, co gwarantuje natychmiastowe wykrycie wszelkich zmian – tłumaczy Paco Triguero, kierownik działu pomiarów części wewnętrznych w firmie SEAT.
Punkty na mapie karoserii
Na karoserię składa się suma różnych zmontowanych części, dlatego jej pomiary muszą zachować wyjątkową dokładność. Maszyny wykorzystujące technikę fotogrametrii wykonują łącznie od 200 do 300 zdjęć każdego elementu karoserii oraz 1000 całego jej szkieletu, co odpowiada pomiarowi 98 milionów szczegółów całego podwozia. To aż 9000 zdjęć i do 210 milionów analizowanych punktów dziennie. Wprowadzone rozwiązanie oszczędza do 90% czasu na pomiar w porównaniu z konwencjonalnymi metodami dotykowymi, co w znaczącym stopniu wpływa na wydajność całego procesu produkcyjnego. Wcześniej inżynierowie dokonywali pomiaru trzech karoserii dziennie, zaś przy zastosowaniu nowoczesnej metody optycznej mogą sprawdzić około 30 dziennie.
Technologiczny kamień milowy
Wykorzystanie przez SEAT-a jest działaniem pionierskim w branży motoryzacyjnej, zapewniającym poprawę wydajności pomiarów na linii produkcyjnej pod względem szybkości i precyzji. Z kolei dzięki synchronizacji mechanizmu z systemami Big Data duża ilość informacji pozyskiwanych obecnie za pomocą fotogrametrii będzie w przyszłości wykorzystywana do wykrywania niepożądanych sytuacji na produkcji jeszcze przed ich wystąpieniem.
– Jesteśmy pierwszym producentem samochodów, który wprowadził na taką skalę ciągły, bezkontaktowy i zautomatyzowany pomiar karoserii. Udało nam się uzyskać pewność, że samochód schodzący z linii produkcyjnej będzie miał ten sam poziom jakości przez cały okres życia serii niczym doskonały prototyp – podsumowuje Pedro Vallejo.
Gigantyczne roboty
Ponad 2,5 metra wysokości i 3 tony wagi – takimi wymiarami może pochwalić się nowy, gigantyczny robot z zakładów produkcyjnych SEAT-a w Martorell. Największa maszyna w historii hiszpańskiej fabryki dołącza do ponad 2200 innych urządzeń, które tworzą najnowsze modele samochodów. Nowy robot odpowiedzialny jest za montaż najcięższych części pojazdów z precyzją co do milimetra, a dzięki jego pracy czas powstawania komlpetnej karoserii wynosi jedynie 68 sekund.
Wiele części, z których buduje się samochody, same w sobie ważą setki kilogramów. Kiedy przychodzi czas na ich złożenie, waga łączna wszystkich elementów dodatkowo się mnoży. Nowa maszyna z fabryki w Martorell jest odpowiedzialna za montaż trzech najcięższych bocznych elementów karoserii, które ważą prawie 400 kilogramów.
– Aby przetransportować i zmontować najmniej poręczne części samochodu tak, by jego konstrukcja była jak najbardziej precyzyjna, musieliśmy użyć większego robota – wyjaśnia Miguel Pozanco, kierownik ds. robotyki w firmie SEAT.
Karoseria w minutę
W fabryce w Martorell znajdują się dwa takie gigantyczne roboty o ładowności do 400 kilogramów. Dzięki pracy 2200 maszyn i wykwalifikowanej załogi liczącej 1700 pracowników jedna kompletna karoseria powstaje co 68 sekund. Roboty ułatwiają proces montażu pojazdu i zmniejszają zajmowaną przez linię produkcyjną powierzchnię. – Montują kluczowe sekcje pojazdu np. elementy boczne karoserii. Ze względu na to, że mogą podnosić większy ciężar, są w stanie wykonać dwie operacje jednocześnie, przez co wydajność pracy przy jednoczesnym zachowaniu jej jakości jest wyższa – tłumaczy Pozanco.
SEAT posiada także inne roboty zdolne udźwignąć ciężar do 700 kilogramów, ale w tym przypadku konieczne było zastosowanie nowych rozwiązań. – Istnieje związek między ciężarem, jaki może unieść robot, a jego zasięgiem. Ten gigant jest w stanie unieść 400 kilogramów w promieniu prawie czterech metrów od własnej osi – wyjaśnia szef robotyki w SEAT. To nowość, ponieważ ten robot potrafi przenosić boczne elementy karoserii, tak by można było je ze sobą zespawać. Udało się to osiągnąć dzięki wbudowanej osi liniowej, która umożliwia poruszanie się w promieniu czterech metrów.
Roboty są wyposażone w oprogramowanie monitorujące wszystkie dane eksploatacyjne, takie jak zużycie silnika, temperatura, moment obrotowy i przyspieszenie. – Analizując te dane, możemy przewidzieć wszelkie nieprzewidziane zdarzenia. Innymi słowy, przeprowadzana jest konserwacja predykcyjna, która na bieżąco zapewnia jakość i precyzję – podsumowuje Miguel Pozanco.
Predykcja w konserwacji robotów
Prócz nowego gigarobota, zmiany dotknęły też cały park takich maszyn w fabryce. Centrum rozwoju oprogramowania SEAT:CODE wraz z zespołem produkcyjnym opracowało system konserwacji predykcyjnej dla robotów. Pozwala on z wyprzedzeniem zapobiegać awariom, tak by unikać ewentualnych przerw w produkcji oraz zwiększać jej wydajność. Fabryka SEAT-a w Martorell jest częścią Digital Production Platform, przemysłowej chmury Volkswagena stworzonej wspólnie z Amazon Web Services oraz partnerem integracyjnym Siemensem.
Mechanizm będzie wykorzystywany w ramach konserwacji predykcyjnej chwytaków spawalniczych wybranych robotów. Dzięki informacji generowanej przez roboty, dane z chwytaków będą przetwarzane i analizowane, a następnie wdrożone zostaną algorytmy przewidujące ewentualne awarie. Dzięki tym informacjom zakład produkcyjny SEAT-a będzie mógł uniknąć przerw w produkcji i zwiększyć swoją efektywność.
– Fabryka w Martorell uczestniczy w procesie cyfrowej transformacji, wprowadzając innowacje z wykorzystaniem najnowocześniejszych rozwiązań technologicznych w sektorze motoryzacyjnym. Dzięki nowemu systemowi konserwacji predykcyjnej zrobiliśmy kolejny krok naprzód w realizacji naszej koncepcji Smart Factory, która stanowi potencjał w zakresie produktywności – zaznacza Herbert Steiner, wiceprezes ds. produkcji i logistyki w SEAT S.A.
Przemysłowa chmura
SEAT S.A. jest częścią przemysłowej chmury grupy Volkswagen, stworzonej wspólnie z Amazon Web Services, której zadaniem jest integracja poszczególnych fabryk Grupy Volkswagen. Platforma ta wykorzystuje technologię i usługi Amazon Web Services, lidera w branży chmur przemysłowych i jest gwarantem znaczących możliwości technologicznych. – Dzięki opracowanemu algorytmowi mamy możliwość wykrywania awarii, przewidując w ten sposób ewentualne problemy na kilka dni przed ich wystąpieniem. Dzięki temu możemy jeszcze lepiej analizować nasze procesy, a tym samym być bardziej produktywni. Chcemy stworzyć solidną platformę na poczet przyszłych innowacji – komentuje Carlos Buenosvinos, dyrektor generalny SEAT:CODE.
Digital Production Platform jest globalną platformą przemysłową o różnych zastosowaniach. System łączy fabryki Grupy Volkswagen poprzez digitalizację procesów produkcyjnych i logistycznych. Platforma umożliwia zbieranie i synchronizację danych z maszyn i systemów we wszystkich zakładach w czasie rzeczywistym, a także zapewnia wgląd w procesy produkcyjne. W ten sposób można stworzyć nowe perspektywy dla optymalizacji produkcji i znacznego zwiększenia wydajności w zakładach. Opracowany przez SEAT-a mechanizm, dzięki zintegrowaniu z chmurą, może być rozszerzany i stosowany w innych zakładach Grupy Volkswagen.