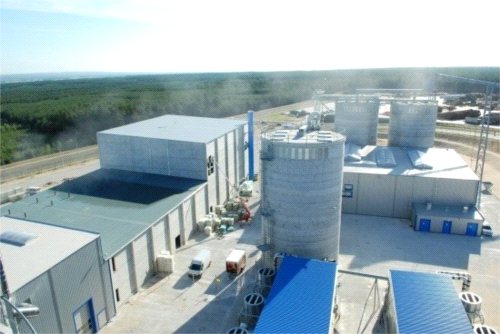
Fabryka Stelmetu w ekologicznej czołówce
Fabryka firmy Stelmet zlokalizowana w Zielonej Górze znalazła się w czołówce światowych zakładów pod względem ekologiczności i efektywności produkcji. W procesie wytwarzania pelletu do atmosfery emitowane jest jedynie 1,15 miligramów pyłów - przy normie 400 mg/m³.
Polska fabryka biopaliwa – pelletu jest przykładem przemysłu, który nie dewastuje środowiska naturalnego. Wynika to z zastosowania innowacyjnych technologii, między innymi filtrów kominowych i nowatorskiego rozwiązania – układu kondensacyjnego, dzięki któremu do atmosfery trafia praktycznie sama para wodna. Jednocześnie zakład z części ciepła powstającego przy produkcji pelletu wytwarza na własne potrzeby zieloną energię elektryczną, czym dopełnia swój proekologiczny charakter.
Fabryka Stelmetu w Zielonej Górze jest jednym z głównych europejskich producentów ekologicznego paliwa używanego do wytwarzania energii cieplnej w domowych piecach i kotłowniach. Przy budowie zakładu produkcyjnego pellet, którego koszt wynosił około 50 mln złotych korzystano z wzorców ekologicznych fabryk działających w Europie Zachodniej. Zastosowano w nim rozwiązania, które automatyzują pracę i pozwalają na zarządzanie całym cyklem produkcyjnym przez kilku wykwalifikowanych pracowników z poziomu centralnej konsoli. Dzięki temu roczna produkcja pelletu wynosi blisko 144 tys. ton, ponadto Stelmet od roku 2008 do chwili obecnej odnotował blisko 60 proc. wzrost produkcji.
– Firma Stelmet wpisuje się w ekologiczny trend nie tylko z powodu charakteru wytwarzanego produktu – biopaliwa, lecz dodatkowo przez inwestycje wpływające na ochronę środowiska naturalnego i zwiększanie efektywności energetycznej – komentuje Przemysław Bieńkowski Wiceprezes Zarządu firmy STELMET sp. z o.o. S.K.A. Ostatnio wdrożony układ kondensacji spalin pozwala na obniżenie emisję pyłów 40 proc. poniżej dopuszczalnej normy, dzięki czemu z komina do atmosfera emitowana jest praktycznie sama para wodna – dodaje.
Cały proces wytwarzania pelletu dzieli się na 3 etapy: rozdrabnianie, suszenie i granulowanie. Poprzedza go moment dostarczenia surowca do fabryki: produkty uboczne (wióry i trociny) powstające przy produkcji drewnianej architektury ogrodowej są dostarczane do fabryki za pomocą specjalnej taśmy.
Zastosowanie w procesie produkcji układu kondensacyjnego przyczynia się do ochrony środowiska naturalnego i poprawy wydajności produkcyjnej. Dzięki zastosowaniu innowacyjnego rozwiązania do atmosfery jest emitowana praktycznie sama para wodna – 1,15 mg/m³ przy normach 400 mg/m³ do 2015 roku i 100 mg/m³ od roku 2016. Dodatkowo spaliny, które w tradycyjnych fabrykach oddawane są do atmosfery poprzez system kominowy zwiększają efektywność energetyczną fabryki. Wdrożenie w fabryce Stelmet układu kondensacji spalin pozwoliło na 29 proc. zwiększenie produkcji poprzez efektywne spalanie biomasy, a także uzyskanie od 25 proc. do 60 proc. więcej ciepła.
Ponadto firma, część ciepła powstającego na potrzeby produkcji pellet wykorzystuje do wytwarzania „zielonej energii elektrycznej”, która z kolei może być wykorzystywana w procesie suszenia. Dzięki temu firma uzyskuje niezależność energetyczną i może sprzedawać nadwyżki w postaci zielonych certyfikatów. Jest to możliwe dzięki wykorzystaniu specjalnej turbiny pracującej w kogeneracji z produkcją ciepła z biomasy. Nowoczesne linie produkcyjne gwarantują produkt o stałej i równocześnie wysokiej jakości przy zachowaniu dbałości o środowisko naturalne. Każdy element zakładu i procesu produkcyjnego jest przemyślany, aby maksymalizować efektywność energetyczną i zwiększać moce produkcyjne przez wykorzystywanie wszystkich produktów ubocznych.