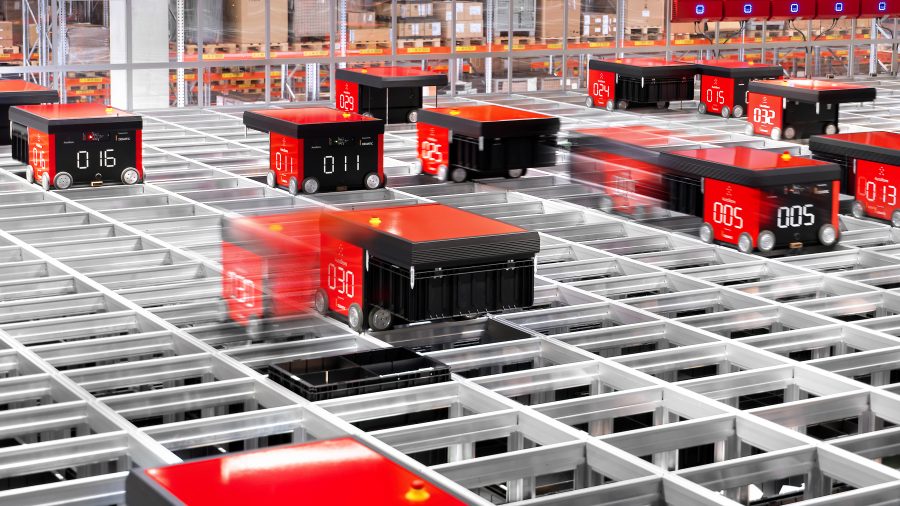
Kiedy automatyzacja ma sens?
Dzięki zautomatyzowanym procesom można zwiększyć wydajność magazynu, zmniejszyć liczbę błędów i skrócić czas dostawy. Ale kiedy automatyka się opłaca? Firma Bito szuka odpowiedzi na pytanie o to, czy warto sięgać po w pełni automatyczne rozwiązania.
W dobie branżowego standardu 4.0 wiele firm musi myśleć o logistyce i automatyzacji magazynu. Każdy przedsiębiorca powinien najpierw zadać sobie pytania: „Czego oczekuję od automatyzacji?” oraz „Czy automatyzacja magazynu w każdym przypadku ma sens?” Według Gabler Wirtschaftslexikon celem zautomatyzowanego magazynu jest „zwiększenie efektywności ekonomicznej magazynowania poprzez zwiększenie rotacji zapasów, zmniejszenie zapasów i poprawę wykorzystania obiektów magazynowych, jak również skrócenie czasu dostawy poprzez szybsze pobieranie”. Warunkiem wstępnym jest działający w oparciu o IT system zarządzania magazynem (WMS) z interfejsami do sterowania systemami przenośnikowymi oraz gospodarką materiałową i/lub system ERP”.
Ręczny czy automatyczny?
W intralogistyce przedsiębiorstw rozróżnia się zazwyczaj pomiędzy magazynami ręcznymi i zautomatyzowanymi. Granice tych dwóch pojęć są płynne. Istnieją również magazyny półautomatyczne. Wykorzystują one niektóre z dostępnych na rynku automatycznych rozwiązań magazynowych oraz system zarządzania magazynem (WMS). Nie ma stałych standardów pozwalających stwierdzić, czy magazyn jest zautomatyzowany czy półautomatyczny. Zatem pierwsze pytanie, jakie należy sobie zadać, to czy automatyzacja jest w ogóle potrzebna. Jakie są zalety i wady magazynu ręcznego? Kiedy jest on użyteczny?
Magazyn ręczny ma kilka zalet:
· Często można go łatwo skalować. Na przykład w przypadku wystąpienia szczytów sezonowych mogą być zatrudniani pracownicy tymczasowi. Magazyn można zatem elastycznie dostosowywać.
· Procesy są często mniej złożone, łatwiejsze do zrozumienia i zarządzania.
· Ludzie są zaangażowani w procesy i mogą wnieść swoje umiejętności poznawcze i praktyczne doświadczenie.
· Ten typ magazynu sprawdza w szczególności w przypadku niewielkiego asortymentu, małej ilości towarów, małej pojemności magazynowej i braku planów rozbudowy. Możliwa jest również łatwa do przeprowadzenia automatyzacja częściowa, np. za pomocą systemów przenośnikowych.
Wady
· Wysokie koszty związane z zatrudnianiem ludzi oraz zmniejszeniem rotacji zapasów lub wydajności pracy w związku z utratą pracowników.
· Częstsze błędy, na przykład podczas ręcznej kompletacji.
Dążenie do poprawy kompletacji zamówień i unikania błędów w ich zestawianiu jest jedną z przyczyn częściowej automatyzacji, np. poprzez automatyczne systemy prowadzenia pojazdów (AGV), a nawet pełną automatyzację magazynu. Dzięki bardziej efektywnej logistyce automatyzacja przekłada się oszczędność kosztów, co oznacza, że wprowadzone rozwiązania mogą zostać zamortyzowane po pewnym czasie. W niektórych branżach, takich jak przemysł motoryzacyjny, stopień automatyzacji jest już bardzo wysoki.
Automatyzacja magazynu w przedsiębiorstwie ma następujące zalety i wady:
Zalety:
· Automatyczny magazyn jest tańszy w eksploatacji niż magazyn ręczny o tak samo wysokiej przepustowości, wielkości i czasie pracy (24/7).
· Jest on zazwyczaj wdrażany w celu zaoszczędzenia kosztów, skrócenia czasu pracy, zwiększenia bezpieczeństwa magazynu, zminimalizowania błędów w zestawieniu zamówień i zwiększenia zadowolenia klienta.
· Ze względu na coraz mniejszą dostępność (wykwalifikowanego) personelu zautomatyzowane magazyny cieszą się coraz większym zainteresowaniem.
Wady:
· W zależności od stopnia automatyzacji koszt inwestycji może być dość wysoki. Jednak ze względu na większą wydajność i oszczędności w kosztach eksploatacji zautomatyzowany magazyn może się po pewnym czasie zwrócić.
· Szczególne wyzwanie stanowi automatyzacja podczas bieżącej eksploatacji zakładu. Aby zapewnić płynne przejście na automatyczną obsługę niezbędne jest rozważne planowanie.
· W wielu przypadkach dostosowanie procesów może być wykonywane tylko przez programistów, którzy często nie mają najlepszego doświadczenia praktycznego w logistyce. W związku z tym możliwości elastycznego dostosowania się do zmienionych procesów w magazynie są ograniczone.
· Skalowanie magazynu automatycznego jest często trudne. System ten jest zazwyczaj zaprojektowany do pracy w sezonowych szczytach i przez to nie jest w pełni wykorzystywany przez resztę roku. Zmniejsza to jego efektywność kosztową.
Wymagania dotyczące (częściowej) automatyzacji
Idealnymi warunkami do automatyzacji magazynu są:
· W miarę możliwości planowana jest praca ciągła (24/7).
· Procesy docelowe muszą być jasne i „zatwierdzone”.
· Jeśli to możliwe, nie powinny występować żadne wahania sezonowe lub powinny być one bardzo małe.
· Musi być zapewniona niezawodność długofalowego planowania w odniesieniu do wymagań dotyczących instalacji magazynowej (opakowania, wielkości partii, przepustowość).
Im bardziej ogólne warunki odbiegają od tego „idealnego magazynu automatycznego”, tym więcej elastycznych i ręcznych procesów należy zintegrować. Jednak coraz częściej pojawiają się rozwiązania magazynowe, które oferują niektóre z zalet magazynów ręcznych. W przypadku systemu Autostore są to skalowalność i możliwość dostosowania do fizycznej struktury magazynu. Ponadto, oferuje on bardzo wysoki poziom wykorzystania przestrzeni i pozwala operatorom na wykorzystanie efektywności kosztowej automatyzacji przy mniejszych ilościach. Magazyny wahadłowe (magazyny kompaktowe) są również łatwo skalowalne i elastycznie rozszerzalne. Zdolność magazynowania i pobierania można zwiększyć poprzez dodanie kolejnych magazynów wahadłowych. Ponadto małe ilości, a także rodzaje artykułów mogą być efektywnie przechowywane w sposób nieselektywny. Oprócz skalowalności AGV oferuje również możliwość elastycznego dostosowania do przepływu materiału.
Case study: automatyzacja przepływu materiałów
Na 5,5 tys. m2 powierzchni operacyjnej firma prowadzi sklepy wysyłkowe, montuje i wysyła ponad 70 tys. produktów dla swoich klientów e-commerce z branży mody, żywności, wyposażenia wnętrz oraz kosmetyków. W zależności od pory roku każdego dnia musi zostać zrealizowanych od 2 tys. do 6 tys. zamówień. Usługodawca wysyła gotowe wyroby do odbiorców końcowych, kompletuje zamówienia, a także montuje pojedyncze wyroby. Działalność firmy w zakresie e-commerce wykazuje duże wahania, ogólnie rzecz biorąc silnie rośnie i jest trudna do zaplanowania. Są to najprawdopodobniej złe warunki dla automatyzacji w technice magazynowej. W celu zmniejszenia liczby błędów i dalszej optymalizacji procesów należy zatem zautomatyzować przepływ materiałów.
W przeszłości produkty były umieszczane pojedynczo w kontenerze KLT podzielonym przez wiszące przegrody i przemieszczanym przez pracowników na wózkach. Teraz pięć transporterów LEO Locative przejmuje długie dystanse, odbierając towary na sześciu stacjach LEO przed regałami i transportując je do stacji montażowych lub wysyłkowych. System działa bez W-LAN i drogiego IT (komputer przepływu materiałów) i jest sterowany za pomocą ścieżki optycznej i znaczników, które są również przymocowane do podłogi. Obecnie za pomocą tabletu można sterować sześcioma miejscami docelowymi. Stop i tym samym cel są definiowane za pomocą odpowiednich znaczników na podłodze. Ogólnie rzecz biorąc, struktury w przepływie materiałów są naprawiane, co pozwala na utrzymanie wysokich standardów w niejednorodnym środowisku handlu elektronicznego.
Case study: regały przepływowe
Pierwsza europejska wegańska hurtownia AVE (Absolute Vegan Empire) z siedzibą w Nabburg w Bawarii od momentu jej założenia w 2001 r. ugruntowała swoją pozycję jako przedsiębiorstwo o międzynarodowym zasięgu, zatrudniające 85 stałych pracowników. Na przestrzeni lat rozwinęła się ścisła sieć podobnie myślących partnerów zewnętrznych.
Ponad 5 tys. aktywnych klientów z całego świata dokonuje zakupów w sklepie AVE. Produkty te są sprzedawane do sieci handlowych i dystrybucyjnych za pośrednictwem sklepu internetowego. Firma oferuje dzisiaj szeroką gamę produktów dla wegańskiego stylu życia obejmującą ponad 900 artykułów dostępnych do sprzedaży hurtowej i ponad 2,5 tys. wegańskich artykułów do handlu online Ze względu na stały rozwój firmy, budowa nowego centrum logistycznego była nieunikniona. Selekcja towarów musi zostać przeprowadzona zgodnie z zasadą FiFo w celu zapewnienia zgodności z najlepszymi terminami przydatności. Ponadto codziennie trzeba obsłużyć do 2 tys. małych zamówień do sklepu internetowego. W ciągu dnia należy zrealizować do 150 zamówień hurtowych.
BITO zainstalowało system regałów przepływowych Flex dla ładunków drobnicowych (SDS) i PRO dla palet (PDS) w wielopoziomowym systemie regałów. PDS służy jako magazyn buforowy w dolnej części systemu regałowego. Małe zamówienia są pobierane z SDS do pojemników zwrotnych MB. Duże zamówienia odbierane są za pomocą elektrycznych ręcznych wózków paletowych.
Zamówienia z magazynu suchego i strefy świeżej żywności są łączone i pakowane po skompletowaniu zamówienia. Zintegrowana stalowa platforma konstrukcyjna umożliwia kompletację zamówień na dwóch poziomach, przy czym system przenośników przednich transportuje pojemniki z pobranym towarem do strefy wysyłkowej. Dzięki rozwiązaniu BITO dostępna przestrzeń magazynowa jest optymalnie wykorzystana, zamówienia są realizowane szybciej, a procesy są doskonale dostosowane do różnych kanałów dystrybucji firmy.
Wnioski
Automatyka w coraz większym stopniu wkracza do intralogistyki. Wpływa na to nie tylko standard przemysłu 4.0 i wymagana wydajność czy minimalizacja kosztów, lecz tym bardziej przyszły brak wykwalifikowanego personelu. Tutaj nie zawsze trzeba mieć duży, złożony, w pełni automatyczny magazyn. Coraz częściej wybierana jest częściowa automatyzacja lub małe elastyczne rozwiązania, takie jak AGV, systemy wahadłowe lub roboty.
Komentarze
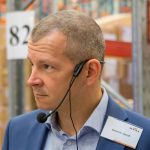
Zainteresowanie automatyzacją procesów transportu wewnętrznego wzrosło w ostatnich latach na tyle, że stała się ona jednym z najważniejszych trendów w intralogistyce. Istotne dla wzrostu jej popularności były rosnące w ostatnich latach koszty pracy, kłopoty ze znalezieniem wykwalifikowanych pracowników, presja na tempo wykonywania zadań transportu wewnętrznego oraz epidemia – zarówno ze względu na spowodowane nią absencje, jak i poszukiwanie przez przedsiębiorstwa rozwiązań, dzięki którym będą w stanie skuteczniej konkurować w post-pandemicznej gospodarce. Nie bez znaczenia jest również rosnąca dostępność rozwiązań automatyzacyjnych oraz coraz szersze spektrum wdrożeń, w których automatyzacja jest opłacalna.
Pomimo że liczba klientów zainteresowanych automatyzacją rośnie, w dziale Advanced Applications STILL Polska do każdego projektu podchodzimy indywidualnie i wybieramy optymalne rozwiązania, pozwalające na zabezpieczenie bieżących i przyszłych potrzeb klienta. Dla każdego z projektów obliczamy ROI. Bardzo często do fazy ofertowania i realizacji przechodzą projekty z okresem zwrotu z inwestycji krótszym niż 3 lata. Dzięki takiemu podejściu, rozbudowanemu know-how i dostępowi do wielu zróżnicowanych rozwiązań, rośnie liczba zadowolonych klientów automatyzacyjnych STILL Polska.
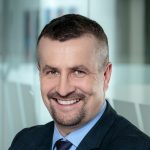
Zainteresowanie automatyzacją procesów logistycznych wśród polskich przedsiębiorstw zdecydowanie rośnie. Coraz częściej kwestie związane z wdrażaniem innowacji stają się częścią i dodatkowo wyróżnionym elementem zapytania ofertowego.
W przypadku klientów z sektora e-commerce automatyzacja jest wręcz koniecznością. Przede wszystkim wiąże się to ze specyfiką i skalą wykonywanych operacji. Chodzi o znacznie większe tempo, rozdrobnienie i złożoność procesów magazynowych, wymagających więcej przestrzeni i zasobów ludzkich.
Kolejnym powodem do wzrostu zainteresowania automatyzacją jest wysoka dynamika zmian, zachodzących na rynku. Już dzisiaj zauważamy wzrost czynszów i cen najmu powierzchni magazynowych, niepewność na rynku pracy. Innowacyjne rozwiązania, pozwalające na optymalizację przestrzeni i procesów kompletacji oraz składowania produktów stają się coraz bardziej uzasadnione ekonomicznie.
Wiele tradycyjnych form automatyzacji oznacza wysokie koszty wdrożenia i relatywnie długie terminy zwrotu z inwestycji. Dlatego czasami trudno jest przejść z etapu rozpatrywania do realnego uruchomienia inwestycji. Mimo deklaratywnego zainteresowania klientów, aspekt finansowy pozostaje decydujący. Zwłaszcza w przypadku klientów z branż charakteryzujących się dużą różnorodnością i sezonowością produktów. W tej sytuacji, naszym zadaniem, jako partnera logistycznego, jest znalezienie optymalnego rozwiązania, które pozwoli z jednej strony nie przepłacić inwestycji, a z drugiej strony spełnić wymagania rynku.
Artykuł ukazał się w czasopiśmie Eurologistics 4/0222