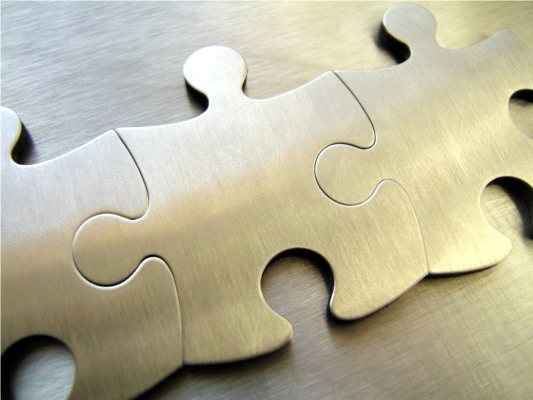
Logika a logistyka
Doskonale pamiętam mój pierwszy kontakt z organizacją produkcji w jednej z polskich fabryk. Po studiach politechnicznych trafiłem do fabryki obrabiarek, gdzie produkowano te maszyny i nie mogłem nadziwić się braku logiki w procesie produkcji.Z pewnością wielu absolwentów
Z pewnością wielu absolwentów studiów ma podobne doświadczenia związane z produkcją. Takie sytuacje mogą być jednakże najlepszym nauczycielem, ponieważ skłaniają do eksperymentowania. Ważne jest jest kreatywne podejście do zastanej sytuacji oraz zdolność do analizowania procesów, które uzasadniają sens zastosowania logiki w procesie produkcji. Bliskoznaczne terminy, takie jak logika czy logistyka, niezależnie od okresu, w którym były używane, zawsze miały konotacje związane z myśleniem.
Logistyka produkcji to termin, który w sposób uświadomiony i nieuświadomiony istnieje od momentu, w którym człowiek cokolwiek zaczął wytwarzać w różnej skali: na własne potrzeby i na użytek innych.
Produkcja a logika
Generalnie przecież produkcję można utożsamiać z działalnością człowieka rozłożoną w czasie, polegającą na lepszym czy gorszym wykorzystywaniu dostępnych zasobów ludzkich i materialnych w celu osiągnięcia efektu w postaci określonych produktów.
Ciekawie na temat produkcji wypowiedział sie guru zarządzania P. Drucker, który stwierdził, że „produkcja to nie zastosowanie maszyn czy narzędzi do przetwarzania materiałów, ale zastosowanie logiki w procesie pracy”. Z perspektywy moich wieloletnich doświadczeń śmiało mogę potwierdzić tę tezę.
Produkcja to nie zastosowanie maszyn czy narzędzi do przetwarzania materiałów, ale zastosowanie logiki w procesie pracy.
Zadaniem logistyki produkcji jest zapewnienie optymalnego przepływu materiałów i informacji w procesie produkcji. Zadanie to nie jest wcale łatwe, a wraz z upływem czasu staje się coraz bardziej złożone i trudne ze względu na rosnące potrzeby ludzi, intensyfikujące konkurencyjność i efektywność na rynku.
Logistyka produkcji nie zajmuje się technologią procesów produkcji, chociaż jest ona ściśle z nią związana, zajmuje się natomiast sprawną organizacją całego procesu produkcji i jego otoczenia. Jej zadaniem jest planowanie, organizowanie i kontrola przepływu surowców, materiałów, części i elementów kooperacyjnych podczas procesu produkcyjnego, począwszy od składów zaopatrzeniowych, poprzez pośrednie magazyny wydziałowe i stanowiskowe, aż do końcowych magazynów wyrobów gotowych i zbytu.
Potrzeba logiki w produkcji
W fabryce obrabiarek, w latach 70-tych, po raz pierwszy doświadczyłem zaskakujących mnie i sprzecznych z przyjętym teoretycznym, powszechnym mniemaniem o sprawnym systemie zapewnienia optymalnego przepływu materiałów i informacji w procesie produkcji obrabiarek zespołowych. To, co wówczas zobaczyłem, utkwiło mi w pamięci na wiele lat. Ten błogi, niczym niezakłócony spokój ludzi na wydziałe montażu obrabiarek zespołowych, którzy do połowy każdego miesiąca nie mieli co montować, a po połowie miesiąca uwijali się jak w ukropie, aby wykonać nałożone na nich zadania. W tej zadziwiającej pustce montażowej pracownicy mogliby spokojnie spędzać urlop poza zakładem pracy i nikomu nie spędzało to snu z powiek poza mną – świeżo upieczonemu magistrowi-inżynierowi budowy maszyn. To zderzenie z rzeczywistością produkcyjną było dla mnie tak szokujące, iż nic dziwnego, że jako nowo mianowany szef wydziału obrabiarek zespołowych i części znormalizowanych intensywnie zacząłem myśleć nad zmianami w systemie planowania, organizowania i kontroli przepływu surowców, materiałów, części i elementów kooperacyjnych w procesie produkcji. Pod lupę wziąłem wszystkie ogniwa uczestniczące w tym procesie, od składów zaopatrzeniowych, poprzez pośrednie magazyny odcinkowe i stanowiskowe, aż do końcowych magazynów wydziału części gotowych do montażu. I… doznałem swoistego olśnienia, które wręcz porażało prostotą rozwiązania problemu notorycznych przestojów wydziału montażu obrabiarek zespołowych. Zaskoczenie było tym większe, że nikt przede mną w fabryce nie skojarzył istniejących przecież ścisłych powiązań pomiędzy technologią montażu a technologią produkcji obrabiarek zepołowych. Zadowolony ze swojego odkrycia rzuciłem się w wir przygotowań związanych z opracowaniem projektu zmian, i to niemałych, bo odnoszących się do większej części fabryki, które należało w pierwszej kolejności opisać oraz wieloaspektowo uzasadnić.
Relacje między procesami
Montaż obrabiarek zespołowych, który jest łączeniem poszczególnych części w całość, nie może następować w sposób chaotyczny, tak jak miało to miejsce do tej pory. Proces montażu musi być zgodny z jego technologią, czyli kolejnością montowania części: od bazowych do tych, które mogły w tym procesie być zastosowane na końcu. Dlatego też pierwsze, co uczyniłem, to podporządkowałem proces produkcji części obrabiarek zespołowych oraz części znormalizowanych technologii montażu obrabiarek.
Rozwiązania, które zaproponowałem, były tak proste i oczywiste, że nie miałem zbyt wiele kłopotów, aby przekonać do nich dyrekcję fabryki. Co ciekawe, najbardziej zainteresowani wprowadzeniem zmian byli pracownicy produkcji i montażu, czyli obydwu wydziałów uczestniczących w produkcji obrabiarek, bo wiedzieli, że skorzysta na tym nie tylko cała fabryka, ale i oni sami.
Nie tylko usprawniłem cały proces produkcji i montażu obrabiarek, ale także zostałem głównym koordynatorem wdrożenia wszystkich zmian w systemie planowania, organizowania i kontroli przepływu surowców, materiałów, części w procesie produkcji i montażu obrabiarek zespołowych.
Logistyka produkcji nie zajmuje się technologią procesów produkcji, chociaż jest ona ściśle z nią związana, zajmuje się natomiast sprawną organizacją całego procesu produkcji i jego otoczenia.
Po zinwentaryzowniu sytuacji i ustaleniu początku tak zwanej „nowej ery” dla fabryki, doprowadziłem do powstania systemu, w którym proces produkcji części obrabiarek zespołowych oraz zespołów znormalizowanych został ściśle powiązany z technologią montażu. Dzięki temu systemowi właściwe surowce i zespoły znormalizowane trafiały do wszystkich stanowisk w gniazdach produkcyjnych i na liniach montażowych. W ten sposób również procesy decyzyjne na różnych odcinakach były pod kontrolą, w czym skutecznie wspierały je zastosowane w tym systemie metody: PERT oraz określanie ścieżki krytycznej dla tych zadań, które nie miały żadnych zapasów czasowych i z tego powodu musiały być realizowane w pierwszej kolejności. Transport wewnętrzny, który również został objęty tym systemem funkcjonował jak sprawny krwioobieg, dostarczający surowców oraz części tam, gdzie były one potrzebne do obróbki, a następnie na montaż. Pracownicy byli zadowoleni, ponieważ to nie oni czekali na robotę, a robota czekała na nich i oczywiście pieniądze, które dzięki takiemu stanowi rzeczy mogli zarobić.
Dzięki temu systemowi właściwe surowce i zespoły znormalizowane trafiały do wszystkich stanowisk w gniazdach produkcyjnych i na liniach montażowych.
Takie ustawienie i powiązanie prosesów spowodowało, że więcej już w fabryce nie dochodziło do przestojów. Stopień zadowolenia ludzi wzrósł diametralnie, efektywność i ekonomiczność producji uległa ogromnej poprawie. I pomyśleć, że to wszystko udało się osiągnąć tylko dlatego, że zastosowano logikę w procesie produkcji.