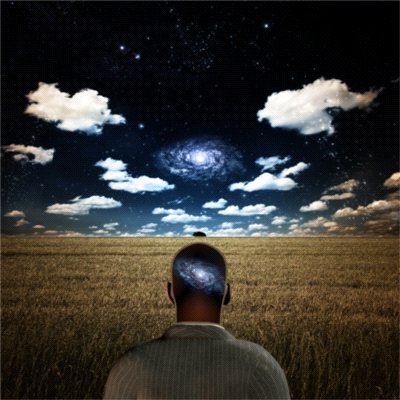
Największe innowacje w logistyce
Wydawca i redaktor naczelny Supply Chain Digest, Dan Gilmore, cały ubiegły rok pracował nad zebraniem dziesięciu największych innowacji w historii łańcucha dostaw.Zadanie, które sobie wyznaczył, wcale nie było takie łatwe. Okazało się bowiem, że trudno jest jednoznacznie...
Zadanie, które sobie wyznaczył, wcale nie było takie łatwe. Okazało się bowiem, że trudno jest jednoznacznie stwierdzić, kto jest autorem przełomowych innowacji łańcucha dostaw. Większość z nich powstawała równocześnie w różnych miejscach na świecie. Postanowiliśmy zaprezentować rezultat jego pracy, nie zważając na fakt, że autor funkcjonuje w amerykańskich realiach i jego punkt widzenia może się różnić od opinii na ten temat uznanych autorytetów łańcucha dostaw w Europie.
1. System Produkcji Toyoty (TPS) Podejście Toyoty do produkcji samochodów, nierozerwalnie związane z bezwzględnie stosowaną kontrolą jakości, zrewolucjonizowało branżę motoryzacyjną. Filozofia łańcucha dostaw Just on time stała się wzorem dla producentów na całym świecie, i to nie tylko w przemyśle motoryzacyjnym. Autorem systemu jest Taichi Ohano wraz z zespołem. TPS dał podwaliny współczesnej koncepcji Lean manufacturing i praktyce łańcucha dostaw.
2. P&G’- nieustanne uzupełnianie towarów Do 1987 roku zamawianie towarów do sklepów odbywało się według tego, co ustalili między sobą menedżerowie sprzedaży w fabrykach i zaopatrzeniowcy w sklepach. Tak było do momentu, kiedy Procter & Gamble zakupił w IBM aplikację nieustannego uzupełniania towarów, która pozwoliła odwrócić system zamówień i dopasować go do przewidywanej wielkości sprzedaży w sklepach detalicznych. W 1988 roku odbyło się słynne spotkanie CEO z Procter & Gamble z Samem Waltonem, które zaowocowało stworzeniem programu CR (Continuous Replenishment), który wywarł ogromny wpływ na łańcuch dostaw i ostatecznie doprowadził do stworzenia aplikacji ECR (Effective Consumer Response) i CPFR (Continuous Planning Forcasting and Replenishment). Celem efektywnego uzupełniania zapasów jest stworzenie systemu dystrybucyjnego, w którym produkcja sterowana jest przez popyt klientów w punkcie sprzedaży. Konsument powinien być zaopatrywany we właściwy produkt, we właściwym miejscu, we właściwym czasie, we właściwej ilości i jakości.
3. Kontener do przewożenia towarów na statkach Choć trudno to sobie wyobrazić, to do połowy lat 50-tych nie było standardów obowiązujących w transporcie towarów drogą morską. Większość ładunków była ekspediowana na różnorakich platformach, co w konsekwencji obniżało efektywność łańcucha dostaw. Malcolm McLean, logistyk i wizjoner łańcucha dostaw, zainwestował cały swój majątek w przebudowę tankowca na pierwszy w świecie kontenerowiec. W 1956 roku statek o nazwie Ideal X wypłynął w swój pierwszy rejs z ładunkiem 35-stopowych kontenerów z portu w Newark w New Jersey. Od tego czasu nastąpiła prawdziwa eksplozja przewożenia towarów na statkach w kontenerach.
4. Optymalna wielkość zamówienia (Economic Order Quantity – EOQ) to matematyczny modelem zarządzania zapasami w łańcuchu dostaw. Metoda ta definiuje optymalną wartość (ilość) zamówienia, tak aby zminimalizować koszty zmienne. Koncepcja została opracowana przez Ford Whitman Harris i zaprezentowana w 1913 roku, a później dopracowana w artykule opublikowanym w 1934 roku w Harvard Business Review, w którym określono ile powinno się zamówić, tak aby koszty obsługi zamówienia były optymalne w stosunku do kosztów finansowania oraz magazynowania. Współcześnie koncepcja ta leży u podstaw wielu decyzji podejmowany w łańcuchu dostaw.
5. Linia montażowa Forda To zespół stanowisk roboczych (maszynowych, ręcznych lub mieszanych) pogrupowanych według kolejności operacji procesu technologicznego. Na linii produkcyjnej części są łączone w główny produkt o wiele szybciej niż w przypadku produkcji rzemieślniczej. Po raz pierwszy zastosowano ją w 1913 roku w fabryce Forda przy produkcji Modelu T. Wdrożenie to miało kolosalny wpływ nie tylko na procesy produkcyjne w przemyśle motoryzacyjnym, ale także w innych sektorach produkcyjnych. Przy zastosowaniu linii montażowej całkowity czas pracy potrzebny do wyprodukowania jednego samochodu spadł z 12, 5 godziny do 93 minut. Dzięki temu produkcja samochodów następowała w masowej skali, co zmieniło nie tylko łańcuch dostaw, ale także miało wpływ na warunki życia społeczeństwa.
6. Uniwersalny kod produktu Idea znakowania produktów uniwersalnymi kodami zawsze była obecna w łańcuchu dostaw, ale dopiero w 1970 roku firma Logicon opracowała standard zbliżony do uniwersalnego kodu identyfikowania produktów (SKU) poprzez kody kreskowe. Kilka lat później George Laurer dokonał w 1974 roku, w sieci Marsh, pierwszego wdrożenia uniwersalnego kodu produktu. Celem tego wdrożenia było usprawnienie obsługi klientów i gromadzenie danych w punktach sprzedaży. W ten sposób zapoczątkowano prawdziwy ruch na rzecz automatycznej identyfikacji produktów, co miało ogromny wpływ na przepływ informacji w łańcuchu dostaw. Standaryzacją zajmowały się organizacje UCC (Uniform Code Council) w USA oraz ECCC (Electronic Commerce Council of Canada). W wyniku podjęcia działań mających na celu połączenie standardów UPC oraz konkurencyjnego EAN, w 2005 roku organizacje te weszły w skład globalnej organizacji GS1.
7. System śledzenia FedEX Wraz z pojawieniem się kategorii dostarczania paczek ekspresowych swoim klientom firma FedEX zaproponowała w połowie lat 80-tych system komputerowy pozwalający na monitorowanie przesyłek kurierskich w czasie rzeczywistym. Pomysł ten utwierdził zarządzających łańcuchem dostaw w przekonaniu, że nie tylko sama paczka jest ważna, ale także informacja z nią związana, co dało podwaliny współczesnej przejrzystości łańcucha dostaw.
8. Proces planowania dystrybucji W 1970 roku Andre Martin z firmy Abbott Labs w Kanadzie zauważył, że między menedżerami produkcji i zaopatrzenia dochodzi do konfliktów wynikających z braku zasobów do produkcji. Dlatego doszedł do wniosku, że potrzebny jest system planowania procesu produkcji. W tym celu podjął wysiłek stworzenia aplikacji komputerowej DRP, która dała początek obecnym oprogramowaniom planowania łańcucha dostaw na produkcji. DRP przygotowuje dla planowania dystrybucji szczegółowe informacje o sieci logistycznej, o aktualnym stanie magazynu, aby mogło dojść do skoordynowanego planowania i dostawy zasobów.
9. Centralny System Kontroli Transportu 3M W 1982 roku koncern M3, tak jak inne firmy, pozostawiał procesy transportowe w gestii poszczególnych fabryk i centrów dystrybucyjnych. Roy Mayeske, dyrektor operacyjny ds. transportu w M3, wpadł na pomysł centralizacji i planowania transportu. Korzystając z oprogramowania swojego głównego przewoźnika Schneider National, zaadaptował je do potrzeb innych przewoźników i dzięki temu powstał system LCC, który jest obecnie w powszechnym użyciu. System ten oznacza takie podejście do transportu, które pozwala połączyć funkcje planowanie z innymi zasobami w firmie i łączyć je w grupy, przez co zwiększa się efektywność transportu i następuje optymalizacja kosztów.
10. Tayloryzm W końcu XIX wieku wielki Frederick Taylor opisał w sposób naukowy procesy produkcyjne. Na początku lat 80-tych XIX w. wynalazł koncepcję mierzenia czasu w procesie produkcyjnym. Później koncepcja ta została rozwinięta do systemu motywacyjnego na produkcji. Idea ta całkowicie zmieniła w następnych kilku dekadach podejście do procesów produkcyjnych. Zakłada ona maksymalną intensyfikację pracy przy efektywnym wykorzystaniu czasu i obcięciu kosztów. Postuluje także podział procesu technologicznego na czynności proste, przy eliminacji zbędnych nawyków. Tayloryzm wprowadził oparty na chronometrażu (pomiar czasu przy pomocy sekundomierzy) system normowania pracy, który sprzężony jest z systemem wynagradzania.