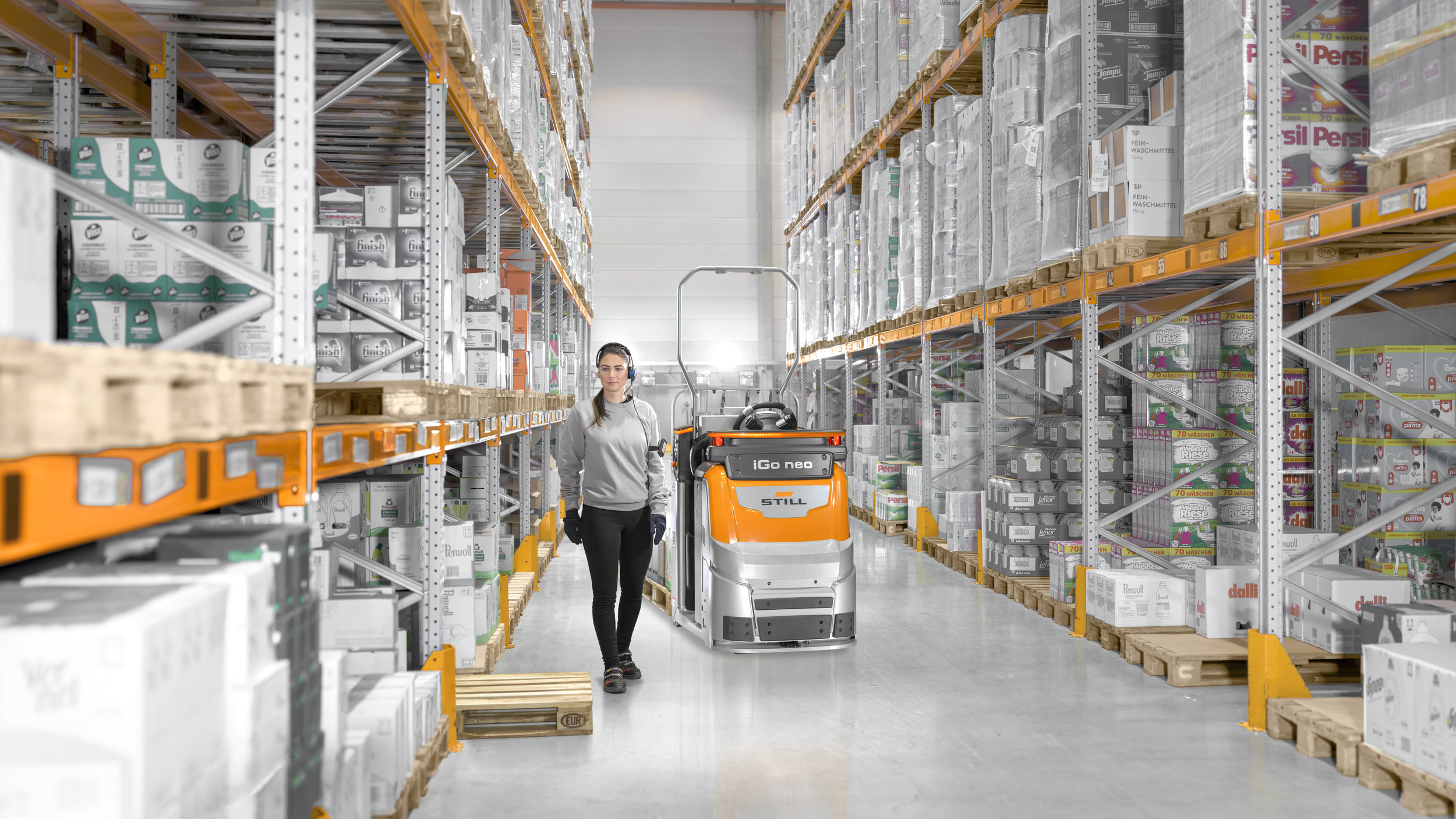
O ile rośnie wydajność pickera przy wsparciu robota?
Kompletacja to z jednej strony coraz ważniejszy, a z drugiej – jeden z najtrudniejszych w całkowitej automatyzacji procesów intralogistycznych. Dlatego też na popularności zyskują cyfrowe i robotyczne systemy wsparcia pickerów. Ile można dzięki nim zaoszczędzić?
Szacuje się, że kompletacja odpowiada za około 50 proc. kosztów pracy w magazynach, a wraz z rozwojem e-commerce wartość ta może jeszcze wzrosnąć. Jednocześnie całkowita automatyzacja procesów tego typu jest stosunkowo kosztowna i trudna do przeprowadzenia w już funkcjonujących obiektach. Dlatego też duży nacisk kładzie się obecnie na optymalizację procesów ręcznej kompletacji – na przykład poprzez rozwiązania wspierające pickerów w ich pracy i pozwalające zwiększać jej wydajność. Jaką skalę oszczędności można uzyskać dzięki wdrożeniu „autonomicznych partnerów kompletacji”? Sprawdziliśmy na przykładzie STILL OPX iGo neo.
Charakterystyka funkcjonowania STILL OPX iGo neo
OPX iGo neo to wózek do kompletacji poziomej wyposażony w systemy, dzięki którym staje się inteligentnym elementem procesów intralogistycznych. Za sprawą czujników i laserowego układu rozpoznawania otoczenia, pojazd w czasie rzeczywistym analizuje topografię magazynu, usytuowanie regałów, lokalizację użytkownika i innych uczestników ruchu. W efekcie potrafi samoczynnie poruszać się za operatorem, dostosowując się do jego rytmu pracy i całkowicie zwalniając go z konieczności sterowania wózkiem na krótkich trasach. Wózki zajmują przy tym zgodną z preferencjami operatora pozycję do odkładania ładunków na widły, do minimum ograniczając dystans, na którym konieczne jest ich ręczne przenoszenie. Obliczyliśmy, jak duże oszczędności czasu pracy można uzyskać dzięki wdrożeniu rozwiązania tego typu.
O ile autonomiczni partnerzy kompletacji zwiększają wydajność? – szacunkowe obliczenia
Przyjmijmy, że w ciągu jednej godziny pracy picker ma za zadanie pobrać z regałów 100 pozycji składających się na zamówienia klientów. Z uwzględnieniem 15-minutowej przerwy oznacza to 775 pobranych pozycji w ciągu jednej zmiany.
Załóżmy także, że picker ma do dyspozycji wózek do kompletacji i każde powtórzenie czynności pobierania ładunku z regału wymaga dojazdu do miejsca paletowego, opuszczenia kabiny wózka, pobrania ładunku i wejścia z powrotem za kierownicę. Załóżmy, że każdy z tych ruchów – zejście, pobranie i wejście – trwa 5 sekund.
Jeśli więc przez 8 godzin pracy picker pobiera 775 pozycji z zamówień, wychodzenie z kabiny wózka i wchodzenie do niej trwa łącznie 7750 sekund, tj. 129 minut. Przeprowadzone w warunkach centrum dystrybucyjnego pilotażowe testy STILL OPX iGo neo wykazały, że korzystając z tego rozwiązania, liczbę powtórzeń czynności schodzenia z wózka i wchodzenia do niego na powrót można zredukować nawet o 75 proc. (Pozostałe 25 proc. przypadków dotyczy sytuacji, w której ze względu na odległości zasadne jest przejechanie wózkiem dystansu dzielącego kolejne punkty poboru ładunków.) Zamiast 775 zejść i wejść do kabiny trwających łącznie 2 godziny i 9 minut, pozostają 193 powtórzenia tych czynności o łącznym czasie trwania wynoszącym 32 minuty. Oznacza to, że z zastosowaniem autonomicznego partnera kompletacji STILL OPX iGo neo w ciągu zmiany każdy z pickerów zyskuje ponad 1,5 godziny. Czas ten może zostać wykorzystany czy to na zwiększenie liczby pobieranych ładunków, czy to na dodatkową kontrolę poprawności kompletacji – w zależności od tego, jakie parametry funkcjonowania centrum wymagają polepszenia. Wykonanie tej samej pracy w 370 zamiast 465 minut oznacza wzrost wydajności o ponad 20 proc.
– Co istotne w kontekście szacunków czasu uzyskania zwrotu z inwestycji w STILL OPX iGo neo, im lepiej zoptymalizowane są trasy przejazdu między punktami kolejnych poborów ładunku, tym większy potencjał oszczędności. Dobre rozmieszczenie asortymentu na miejscach paletowych umożliwia zmniejszenie odległości pomiędzy przystankami, co przy użyciu iGo neo jest jednoznaczne ze zwiększeniem liczby przypadków, w których operator nie musi wchodzić do wózka – komentuje Dominik Jasiok, Advanced Applications Manager STILL Polska. – Rozwiązania takie jak OPX iGo neo pozwalają więc budować przewagę konkurencyjną w zorientowanych na jak najkrótszy czas kompletacji centrach fulfillment. Wszystko to przy niższych kosztach inwestycji i znacznie mniejszej złożoności wdrożenia niż w przypadku całościowych systemów automatyzacji – konkluduje Jasiok.