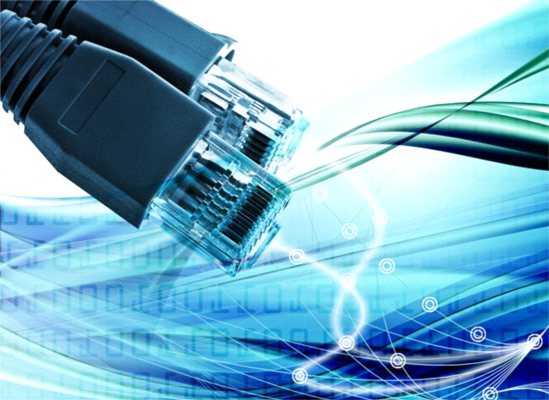
Oprogramowanie dla branży produkcyjnej
W epoce cyfrowej i trudno wyobrazić sobie, aby jakakolwiek firma była w stanie funkcjonować, nie korzystając z systemów informatycznych. Bez wsparcia specjalistycznego oprogramowania, działalność przedsiębiorstw byłaby znacznie trudniejsza, zaś wiele zadań, dziś powszechnie...
Najprostsze rozwiązanie
Oferta rozwiązań informatycznych dla firm jest niezwykle szeroka. Twórcy oprogramowania starają się, aby ich produkty były możliwie uniwersalne i sprawdzały się w przedsiębiorstwach o różnym charakterze. Możliwości standardowych rozwiązań szybko przestają być jednak wystarczające i aby poprawiać wydajność firmy, należy sięgnąć po specjalistyczne rozwiązania.
Menedżerowie zarządzający firmami produkcyjnymi są w stanie w pewnym stopniu korzystać z powszechnie spotykanych aplikacji. Oczywiście, najprostszym rozwiązaniem jest arkusz kalkulacyjny. Jego wielką zaletą jest uniwersalność, zaimplementowane funkcjonalności sprawdzą się zarówno w magazynie, dziale kadr, administracji jak i przy planowaniu produkcji. Nowo zatrudniani pracownicy zazwyczaj potrafią posługiwać się tym narzędziem. Ograniczenie arkusza kalkulacyjnego dość szybko wychodzą jednak na jaw. Pomimo wyższej ceny, zaawansowane oprogramowanie dla firm produkcyjnych szybko wykazuje swoją przewagę.
Popularny ERP
Podstawowym i najczęściej wdrażanym w przedsiębiorstwach produkcyjnych rozwiązaniem są systemy ERP (Enterprise Resource Planning). Do wyboru jest spora ilość takich produktów, cechują się one dodatkowo modułową strukturą i posiadają spore możliwości rozbudowy i dopasowania funkcjonalności do potrzeb klienta. Najprostsze wersje systemów ERP oferują funkcje księgowo-magazynowo-sprzedażowe, pozwalając głównie na rozliczenie kosztów produkcji i sprzedaży.
Optymalizacja produkcji na bazie tylko tak podstawowych danych wymaga w takiej sytuacji żmudnego analizowania raportów. Firmy produkcyjne decydują się zatem na dodatkowe oprogramowanie (często w postaci kolejnych modułów istniejącego systemu ERP), pozwalające na planowanie i nadzorowanie produkcji. Systemy MRP II (Manufacturing Resource Planning) ułatwiają optymalizację wykorzystywanych do produkcji zasobów (materiałów, maszyn, ludzi itp.) i dostosowywać te zasoby do planów produkcyjnych – czyli pozwalają zarządzającym zmniejszać koszty produkcji.
Rozszerzone funkcjonalności systemów ERP umożliwiają m.in. uporządkowanie procesu produkcyjnego, rejestrację braków i odpadów oraz efektywną kontrolę jakości, automatyczną rejestrację pomiarów czasów Tpz i Tj inwentaryzację produkcji w toku. tworzenie szerokiego spektrum raportów i analiz oraz elastyczne planowanie produkcji. Moduły te, występujące w zaawansowanych systemach ERP, zbliżają je już funkcjonalnością do systemów MES.
Produkcja pod kontrolą
Typowym rozwiązaniem dla obszaru ściśle produkcyjnego są systemy typu MES (Manufacturing Execution System). Umożliwiają one stałe monitorowanie produkcji i zarządzanie zachodzącymi w niej zmianami. Systemy MES traktowane są jako łącznik między poziomem produkcyjnym a biznesowym przedsiębiorstwa. Ich działanie wychodzi poza zbieranie danych – przekształcane są one do postaci, umożliwiające osobom kierującym produkcją łatwą analizę sytuacji i szybką reakcją.
Systemy MES umożliwiają znaczną poprawę wydajności procesu, ułatwiają też zmianę profilu produkcji oraz dostosowywanie się do nowych standardów. Operatorzy wykorzystują je jako wsparcie w zakresie podejmowania decyzji, oprogramowanie przekazuje natychmiastowy sygnał zwrotny o stopniu realizacji produkcji i pozwala reagować na bieżąco na nieprawidłowości pojawiające się w czasie procesu produkcyjnego.
Systemy MES obejmują szereg obszarów funkcjonalnych, takich jak zarządzanie wykonywaniem produkcji, zarządzanie wydajnością, śledzenie produkcji i jej genealogia, zarządzanie jakością, gromadzenie i akwizycja danych, zarządzanie obiegiem dokumentów, zarządzanie alokacją zasobów, zarządzanie zasobami ludzkimi, zarządzanie ruchem, harmonogramowanie produkcji i rozdział zadań produkcyjnych. Obszary te często występują w formie modułów dostępnych w oprogramowaniu.
Zaawansowane planowanie
Zaawansowanym rozwiązaniem, stosowanym przez firmy produkcyjne patrzące na swoją działalność przez pryzmat całego łańcucha dostaw, są systemy klasy APS (Advanced Planning and Scheduling). Zmienne wymagania klientów wpływają na konieczność modyfikacji harmonogramu produkcji. Oprogramowanie APS, oparte na systemach ERP, znacząco ułatwia harmonogramowanie, dzięki tworzeniu zaawansowanych planów i symulacji, pozwalających na znalezienie optymalnego rozwiązania.
Systemy APS przy planowaniu produkcji uwzględniają jednocześnie plany dystrybucyjne. Automatycznie uwzględniane są możliwości wszystkich zasobów, terminy czynności okresowych czy kalendarze pracy. Oprogramowanie jest w stanie ustalić okres dostępności zasobów i ocenić ich alternatywne konfiguracje.
Dla utrzymania ruchu
Działy utrzymania ruchu powszechnie korzystają z oprogramowania CMMS (Computerized Maintenance Management System), systemów informatycznych gromadzących informacje na temat eksploatacji oraz wspomagający zarządzanie pracą maszyn. CMMS ułatwia planowanie i przeprowadzanie konserwacji i remontów urządzeń, przekazuje pracownikom informacje o niezbędnych czynnościach i ostrzega o nadchodzących terminach przeglądów. Przechowywane w systemie informacje na temat awarii mogą wskazać na słabe punkty w parku maszynowym.
Coraz popularniejsze stają się też systemy EAM (Enterprise Asset Management), obejmujące oprócz funkcjonalności CMMS (wspomagającego zarządzanie UR, planowanie pracy itp.) również szczegóły dotyczące rejestru wyposażenia, inwestycji, bezpieczeństwa, dokumentacji technicznej, gospodarki magazynowej i zakupów, zarządzania podwykonawcami itd.
Konieczna integracja
Lista systemów, spotykanych w nowoczesnych firmach produkcyjnych, stale rośnie. Są to m.in. narzędzia wspierające zarządzanie cyklem życia produktu (PLM), systemy nadzorujące przebieg procesów technologicznych (SCADA), narzędzia analityczne Business Intelligence. czy też oczywiście systemy CAD, służące do projektowanie wyrobów i oprogramowanie pozwalające na sterowanie obrabiarkami CNC.
Rozwój przedsiębiorstwa i idące za nim stopniowe inwestycje sprawiają, iż w firmie pojawia się z czasem coraz większa ilość oprogramowania, funkcjonującego w różnych obszarach. Niesie to za sobą ryzyko powstania kilku równoległych baz danych, z których każda jest istotna dla sprawnego funkcjonowania przedsiębiorstwa. Na szczęście producenci dbają o to, aby nowo implementowane rozwiązania mogły zostać zintegrowane z oprogramowaniem już funkcjonującym w firmie. Dzięki temu np. dane z systemu CMMS importowane są do systemu ERP, pochodzącego od innego dostawcy. Firmy coraz częściej żądają także możliwości integracji z systemami, stosowanymi przez dostawców.
Przyszłość systemów dla firm produkcyjnych najprawdopodobniej będzie powiązana z ogólnymi tendencjami w branży informatycznej. Już teraz widoczna jest coraz szersza obecność aplikacji mobilnych, umożliwiających dostęp do systemów działających w firmie z dowolnego miejsca. Dzięki temu kierownik produkcji może sprawdzić i posiłkować się aktualnymi wskaźnikami przebywając na hali produkcyjnej, a także kontrolować sytuację w fabryce podczas wyjazdu. Należy także spodziewać się rozwoju działań w chmurze.
Głos rynku
Oferta wyspecjalizowanego oprogramowania dla branży produkcyjnej jest coraz szersza. Aby ją zaprezentować, oddaliśmy głos dostawcom systemów, obecnych na polskich rynku. Wypowiedzi ich przedstawicieli przygotowaliśmy, pytając o to jakie rozwiązania są niezbędne w firmie produkcyjnej, jak zmieniają się wymagania klientów, co sprawia trudności przy wdrażaniu nowego oprogramowania czy też od czego należy rozpocząć informatyzację firmy.
Dariusz Kuśmierek, zastępca dyrektora Działu Produkcji Systemów ERP, Asseco Business Solutions S.A.
Niezbędne dla poprawy wydajności fabryk jest w pierwszej kolejności zdefiniowanie i realizowanie procedur, pozwalających zapewnić ciągłość, wysoką jakość i opłacalność produkcji. Systemy informatyczne mogą ten proces znacząco ułatwić i uporządkować, natomiast warto zdawać sobie sprawę, że w zależności od specyfiki produkcji w danym przedsiębiorstwie, różna będzie natura najbardziej palących problemów, a zatem także inne priorytety wprowadzania poszczególnych rozwiązań informatycznych. Utrzymującym się od lat trendem jest m.in. automatyzacja wszelkich powtarzalnych procesów. Z tego też względu z każdym rokiem obserwujemy coraz większe wykorzystanie automatyki magazynowej i produkcyjnej, a także wykorzystanie sterowników PLC. Coraz bardziej powszechne jest również wprowadzanie czytników RFID i kodów kreskowych do obsługi procesów produkcyjnych.
Przedsiębiorcy poza tym cenią sobie rozwiązania wspomagające kluczowe obszary związane z organizacją produkcji i pozwalają na lepsze planowanie, harmonogramowanie oraz kontrolę jakości, umożliwiają wygodne przechowywanie oraz sprawną dystrybucję wyprodukowanego towaru, zarządzanie sprzętem własnym lub obcym, utrzymanie parku maszynowego oraz wpływają na obniżenie kosztów zarządzania produkcją.
Klienci zainteresowani są niezmiennie tymi rozwiązaniami, które pozwalają im realizować produkcję w sposób opłacalny i terminowy (najchętniej w trybie Just-In-Time), przy zachowaniu jak najwyższej jakości. Natomiast wciąż pojawiają się rozwiązania, które pozwalają te cele coraz lepiej realizować. Stosowane rozwiązania mogą się również różnić w poszczególnych sektorach branży produkcyjnej.
Przykładowo zapewnienie ciągłości i terminowości produkcji w przypadku przedsiębiorstw realizujących długoterminowe kontrakty produkcji towarów powtarzalnych może być wsparte poprzez procedury obsługi aktualizowanych cyklicznie zamówień produkcyjnych (tzw. forecastów). Z kolei w przypadku produkcji niepowtarzalnej, realizowanej na indywidualne zamówienie klienta, kluczowe będą mechanizmy prototypowania i kosztorysowania nowych produktów.
W ostatnim czasie wzbogaciliśmy nasz system Asseco Softlab ERP o rozwiązania zaawansowanego ofertowania. Szereg ciekawych funkcjonalności zostało zaimplementowanych w modułach prototypowania i harmonogramowania produkcji, jak również stworzyliśmy bogate mechanizmy integracyjne, pozwalające na elastyczne udostępnianie funkcjonalności systemu w bogatej infrastrukturze informatycznej.
Arkadiusz Rodak, specjalista ds. systemów MES, ASTOR
Wdrożenie systemów IT w warstwie produkcyjnej najlepiej zacząć od systemów odpowiedzialnych za automatyczne gromadzenie danych z maszyn i urządzeń oraz umożliwiających wizualizację wybranych parametrów – tzw. oprogramowania SCADA . W kolejnym kroku lub równolegle do wdrożenia systemu SCADA warto przemysłową bazę danych klasy Historian umożliwiający gromadzenie danych historycznych oraz prowadzenie analiz dotyczących zarchiwizowanych parametrów. Przedsiębiorstwa zautomatyzowane, posiadające rozwiniętą infrastrukturę IT w zakresie systemów monitorowania i wizualizacji procesów, są gotowe na wdrożenie systemów efektywnościowych klasy MES.
Rozwiązaniem, którego wdrożenie pozwala na realne poniesienie wydajności fabryki jest oprogramowanie Wonderware MES. System umożliwia automatyczne gromadzenie informacji o przestojach oraz wyliczanie na bieżąco wartości wskaźnika OEE wraz z jego składowymi (dostępnością, wydajnością i jakością), eliminując pomyłki wynikające z pomiarów i wyliczeń wykonywanych ręcznie.
Platforma Systemowa Wonderware jest otwartym systemem monitorowania i wizualizacji produkcji, która może komunikować się z dowolnym innym otwartym oprogramowaniem przemysłowym, z zewnętrznymi bazami danych oraz systemami klasy ERP. Wraz z licencją oprogramowania producent dostarcza bogatą bibliotekę driverów komunikacyjnych pozwalających na integrację z systemami sterowania praktycznie dowolnego producenta.
Aby odciążyć pracowników od natłoku informacji, producenci oprogramowania wizualizacyjnego dostarczają narzędzia, które umożliwiają tworzenie ergonomicznych, prostych, a zarazem wysoce funkcjonalnych ekranów wizualizacyjnych, raportów i interfejsów wprowadzania danych.
Kolejnym bardzo dobrze widocznym trendem jest umożliwianie pracownikom produkcyjnym na dowolnym szczeblu (od operatorom, po kadrze karę kierowniczą), dostępu do danych produkcyjnych z poziomu urządzeń mobilnych – takich jak tablety i smartfony oraz stacji roboczych oddalonych czasem o dziesiątki kilometrów od fabryki.
Kluczowi producenci oprogramowania przemysłowego (np. firma Wonderware) bardzo duży nacisk kładą na kwestie bezpieczeństwa. Stosowanie bezpiecznych szyfrowanych protokołów podczas przesyłania danych z systemów produkcyjnych na urządzenia mobilne, integracja z Microsoft Active Directory oraz wirtualizacja systemów IT to aktualne trendy pozwalające na maksymalizację bezpieczeństwa danych gromadzonych i przetwarzanych przez systemy produkcyjne.
Aleksander Faleńczyk, menedżer ds. Kontraktów, BPSC S.A.
Od dłuższego czasu obserwujemy rosnące zainteresowanie zintegrowanym oprogramowaniem biznesowym w segmencie średnich przedsiębiorstw, szczególnie tych rozwijających się bardzo szybko. Często potrzeby rozwojowe w obszarze IT dotyczą suplementowania już wykorzystywanego systemu o te obszary funkcjonalne, które do tej pory nie były objęte zaawansowanym oprogramowaniem. Taka rzeczywistość sprawia, że nasze rozwiązania w coraz mniejszym stopniu zamykają się w ściśle określonych ramach standardu – ERP czy ERPII – choć oczywiście nasz system spełnia te standardy. Dziś patrzymy na to raczej przez pryzmat kompleksowej mapy IT przedsiębiorstwa oraz „pustych miejsc” na niej, które wymagają takiego wypełnienia, które zapewni zachowanie integracji danych w ramach całości.
Co warte podkreślenia, systematycznie rośnie zainteresowanie aplikacjami w pełni dostosowanymi do wymagań nie tylko danego sektora, ale wręcz konkretnej firmy. Na bazie modułów systemu Impuls EVO oraz rozwiązań partnerskich stworzyliśmy sprofilowaną ofertę rozwiązań branżowych: dla przedsiębiorstw produkcyjnych, przemysłu motoryzacyjnego, drzewnego i meblarskiego, spożywczego, odzieżowego, branży utilities, a także dystrybucji, budownictwa oraz nauki i edukacji.
W okresie ostatniego spowolnienia gospodarczego można było rzeczywiście zaobserwować niewielki spadek inwestycji w systemy informatyczne, z drugiej strony w obliczu spowolnienia gospodarczego część firm inwestowała więcej niż oczekiwali analitycy. To przede wszystkim małe i średnie przedsiębiorstwa, które już teraz wolumenowo są największym odbiorcą systemów ERP. To spółki dobrze zarządzane, szybko rozwijające się i mające spore potrzeby w zakresie informatyzacji.
Przez wiele lat wdrożenie „dużego” systemu IT danego producenta w praktyce skazywało przedsiębiorstwo na korzystanie z jego rozwiązań. Łączenie systemów od różnych dostawców było oczywiście możliwe, w praktyce okazywało się w wielu przypadkach trudne, czasochłonne i kosztowne. Dzisiejszy rynek systemów informatycznych przypomina półkę w supermarkecie. Klient chce wybierać najlepsze produkty z danego segmentu a zadaniem dostawcy rozwiązań jest mu to w jak największym stopniu umożliwić. Elastyczność i otwartość na specyficzne oczekiwania poszczególnych branż w naszym przypadku oznacza z jednej strony na oferowanie rozwiązań dedykowanych zintegrowanych z podstawową funkcjonalnością ERP, z drugiej na integracji systemu Impuls EVO ze specjalistycznym oprogramowaniem, oferowanym przez partnerów, z którymi współpracujemy.
Andrzej Wąs, senior business consultant, IFS Poland
Rozwiązania informatyczne dla firmy produkcyjnej obejmują bardzo szeroki zakres produktów. W zasadzie każda komórka przedsiębiorstwa potrzebuje odpowiednich narzędzi, a oferowane systemy dodatkowo różnią się w zależności od branży. Inne znajdują zastosowanie w produkcji na magazyn (MTS), inne w produkcji na zamówienie (MTO), inne w firmie projektującej na zamówienie. Rozwiązania te obejmują nie tylko klasyczne systemy, takie jak ERP (Enterprise Resource Planning) czy CRM (Customer Relationship Management), ale również narzędzia wspierające zarządzanie cyklem życia produktu (PLM), rozwiązania do zarządzania majątkiem przedsiębiorstwa (EAM), systemy CAD/CAM itp. Systemy te mogą pochodzić od różnych dostawców, stąd często może zachodzić potrzeba ich integracji.
Bez nowoczesnych systemów informatycznych poprawa wydajności nie jest możliwa. Narzędzia IT dostarczają informacji, które są niezbędne do podejmowania właściwych decyzji. Przykładem takiego rozwiązania jest IFS Max OEE. Zapewnia ono wielowymiarową analizę pracy urządzeń w takich wymiarach, jak wydajność, jakość i dostępność urządzeń. Dane te mogą być wykorzystywane zarówno przez zarząd, inżyniera procesu, jak i operatora linii produkcyjnej. System wspomaga decyzje podejmowane zarówno w krótkim horyzoncie przez operatora, jak i odległym przez zarząd np. w celu właściwego zaplanowania inwestycji.
Zainteresowaniem cieszą się rozwiązania do optymalizacji pracy zarówno w obszarze produkcji, jak i remontów. Standardowe moduły obsługujące np. sprzedaż, zaopatrzenie czy fakturowanie nie stanowią już czynnika istotnego w wyborze systemu informatycznego – traktowane są jako oczywistość. Klienci oczekują rozwiązań, które będą ich wspierać w nowych obszarach. Jednym z nich jest rozwiązanie CSR (społeczna odpowiedzialność biznesu), zapewniające m.in. raportowanie środowiskowe (ślad ekologiczny), zapewnienie jakości (zgodność z normami, audyty, raportowanie niezgodności) oraz działania zaradcze (NCR i CAPA), kontrolę eksportu czy też BHP.
Technologia systemu IFS Applications i dostępne narzędzia umożliwiają wydajne i łatwe połączenie systemu z rozwiązaniami innych producentów. Wykorzystywana jest architektura SOA, a jako platforma może służyć interfejs komunikacyjny BizApi. Przykładem jest OPC adapter (otwarty standard komunikacyjny stosowany w automatyce przemysłowej). IFS działa jako klient OPC i łączy się do jednego lub więcej serwerów po stronie automatyki (np. SCADA). Możliwe jest także korzystanie z zewnętrznych programów, np. finansowo-księgowych lub kadrowo-płacowych.
Witold Kruk-Ołpiński sales manager – produkcja, logistyka, transport publiczny, PSI Polska
W mojej opinii żadne nowoczesne przedsiębiorstwo produkcyjne nie może obyć się bez kilku kluczowych systemów IT- ERP, MES, CMMS. Dostawców tych rozwiązań na polskim rynku jest mnóstwo, jak zatem dokonać właściwego wyboru? Podczas wyboru odpowiedniego rozwiązania ERP dla naszej organizacji powinniśmy skupić się na kilku kluczowych aspektach. Musimy przede wszystkim zadać sobie jedno bardzo ważne pytanie: Jak widzę swoją firmę za pięć , dziesięć lat? Odpowiedź umożliwi nam dobranie odpowiedniego dla naszego przedsiębiorstwa rozwiązania.
Pamiętajmy, że system nie tylko na początku powinien spełniać wszystkie nasze wymagania funkcjonalne, ale powinien dawać możliwość rozwoju firmy. Ważne jest, aby stawiać na rozwiązania sprawdzone, znane i o ugruntowanej pozycji na rynku. Jeżeli już na początku, system będzie miał braki w pewnych obszarach, to wraz z upływem czasu i wzrostem naszych potrzeb będziemy coraz bardziej niezadowoleni ze swojej decyzji. Dlatego tak istotne jest, by system był stworzony w sposób modułowy dzięki czemu klient nie musi od razu kupować wszystkich elementów systemu, a jedynie te, które na danym etapie rozwoju przedsiębiorstwa są mu potrzebne do optymalnego realizowania procesów.
Kolejnym bardzo istotnym kryterium doboru, jest branża, w której działa nasza organizacja i system ERP, który planujemy zakupić. Szukajmy rozwiązań stworzonych z myślą o naszym charakterze działalności Często pomijanym a bardzo istotnym aspektem jest lokalny serwis, wsparcie techniczne oraz doświadczenie konsultantów.
Proces doboru rozwiązania MES jest równie istotny. Musimy przede wszystkim zastanowić się do czego ma nam ten system służyć i w jaki sposób może wspierać naszą pracę. Podczas wyboru dostawcy rozwiązania MES bardzo istotne jest aby produkt mógł być zintegrowany z dowolnym systemem ERP oraz pozostałym środowiskiem IT organizacji- choćby systemem CMMS.
PSI cały czas rozwija swoje port folio produktowe dla poszczególnych branż, w chwili obecnej wśród dostawców Automotive dość mocno promujemy rozwiązanie PSIpenta Just In Sequence. Optymalizuje ono kluczowe procesy planowania, zarządza dostawą tak, aby części montażowe dostarczane były bezpośrednio na linię produkcyjną. System harmonogramowania Just in Sequence PSIpenta może być wykorzystany zarówno w formie rozszerzenia standardowego rozwiązania PEC, jak również jako samodzielny moduł zintegrowany z istniejącym środowiskiem systemowym.
Maciej Wojtkowiak – specjalista do spraw systemów produkcyjnych, Quantum Software
Główne cele jakie rynek wyznacza przed firmami z branży IT, tworzącymi oprogramowanie dla firm produkcyjnych, jest przede wszystkim usprawnienie produkcji w zakresie przepływu surowców, kontroli jakości, harmonogramowania oraz planowania zadań i operacji. Systemy, które posiadają takie funkcje, dają możliwość szybkiej reakcji na zmiany popytu na produkty, spadku jakości czy też opóźnień, w zakładanym planie produkcji. Przepływ większości informacji odbywa się przy użyciu paneli operatorskich, komputerów oraz tabletów, co znaczne zmniejsza ilość dokumentów drukowanych, ma wypływ na redukcję kosztów oraz jest bardziej ekologiczne (mniejsze zużycie papieru i tonerów). Lepsze planowanie powoduje, że lepiej wykorzystujemy zasoby (ludzkie oraz sprzętowe), a wydajność naszej fabryki rośnie.
W ostatnich lata widać wzrost zainteresowania systemami klasy MES/APS oraz systemami zapewniającymi zasilanie surowcami w trybie JIT. Taka konfiguracja oprogramowania powoduje, że można dobrze zaplanować działania firmy, zmniejszyć zapasy, skrócić lead time, prawić jakość oraz zwiększyć zadowolenie klientów.
Quantum Software w swoim portfolio posiada szeroki wachlarz produktów dla całego SCE. Powodzeniem cieszą się systemy z grupy „zarządzanie, kontrola i planowanie produkcji”. Klienci coraz bardziej stawiają na rozwiązania działające w czasie rzeczywistym, z możliwością obsługi na różnych urządzeniach, niezależnie od posiadanego systemu operacyjnego (Windows, Android, Linux czy OSx).
Oczywiste istnieje możliwość integracji naszych rozwiązań z systemami innych producentów. Prawie każde wdrożenie systemów z zakresu SCE łączy się z interfejsem wymiany danych z innymi systemami, takimi jak ERP/SCADA/MES/APS/WMS. Występują również połączenia z systemami rejestracji czasu pracy, czy na przykład systemami kontroli dostępu. Szkolenia odbywają się na wcześniej przygotowanym systemie dla klienta, z podziałem na odpowiednie grupy osób, które są odpowiedzialne za dany fragment systemu lub procesu.
Najczęściej trudnością występującą przy wdrożeniach systemów IT jest przyzwyczajenie się do nowych zadań, zmiana sposobu działania pracowników oraz zmiana lub uczenie się nowych ról i reguł. Po latach wdrażania systemów wypracowaliśmy jednak własne efektywne metody, jak zorganizować wdrożenie aby było one szybkie, łatwe i wydajne.
Janusz Mleczko, główny konsultant systemów zarządzania produkcją, Rekord Systemy Informatyczne
Zabrzmi to jak slogan marketingowy ale stwierdzenie o poszukiwaniu przez przedsiębiorstwa produkcyjnych zintegrowanych rozwiązań informatycznych obejmujący całość procesów biznesowych przedsiębiorstwa nadal jest aktualne. Jeżeli wcześniej w przedsiębiorstwach produkcyjnych koncentrowano się na procesach głównych, to po zaspokojeniu oczekiwań użytkowników w tych obszarach obecnie uwaga przenosi się na procesy pomocnicze do tej pory wspomagane przez systemy informatyczne w sposób uproszczony. Obecnie po wdrożeniu rozwiązania zintegrowanego trudno mówić tylko o poprawie wydajności – zasadniczo firmy przenoszą procesy biznesowe w stronę rozwiązań elektronicznych. Jeżeli w procesach logistycznych posługiwanie się komunikatem EDI jest naturalną formą działalności to jeżeli zostanie zaniechanie wdrożenie w tym obszarze to praktycznie tracimy klienta i nie mamy jak poprawiać wydajności przedsiębiorstwa bo nie mamy zleceń wytwarzania.
Głównym problemem ostatnich lat jest odpowiednia i wydajna akwizycja danych. Przedsiębiorstwa produkcyjne wdrażają moduły produkcyjne w celu „opomiarowania” produkcji, ale aby tego dokonać należy w odpowiednio wydajny sposób przygotować bazę wiedzy i zbierać dane z procesu wytwarzania. Tendencją ostatnich lat jest coraz dalej posunięta integracja procesów nie tylko wewnętrznych ale również integracja z systemami odbiorców i dostawców przedsiębiorstwa. Jeżeli w latach 90-tych wdrażając system informatyczny prowadziło się ustalenia tylko z użytkownikiem końcowym, w pierwszej dekadzie w procesach wdrożeniowych brał udział zarząd przedsiębiorstwa to obecnie znacznie poszerzył się krąg koniecznych ustaleń i praktycznie każde wdrożenie odbywa się również we współpracy z firmami zewnętrznymi.
Produkty firmy Rekord Systemy Informatyczne są rozwijane w wielu kierunkach: rozwoju funkcjonalności, zmiany interface oraz zmiany związane z rozwojem aplikacji przeglądarkowych. W ostatnim czasie bardzo mocno zwiększyły się funkcjonalności modułów związanych z kontrolą jakości czy też gospodarki remontowej. W klasycznych i bardzo mocnych modułach REKORD.ERP związanych z przygotowaniem bazy wiedzy o wyrobie module TPP oraz zarządzania produkcją poszerzyliśmy ofertę o narzędzia integracyjne z czołowymi producentami systemów CAD i PDM. Obecnie możliwa jest bardzo głęboka integracja zakładająca dwustronną komunikację pomiędzy systemami ERP i CAD. Wychodząc naprzeciw oczekiwaniom klientów ostatnio do oferty firmy Rekord wszedł panel zgłoszeniowy otwierający kanały kontaktu z firmą poprzez przeglądarkę internetową.
Jolanta Uździcka, dyrektor działu marketingu, Streamsoft
Ważnym jest, aby kadra zarządzająca firmą produkcyjną podeszła do wdrożenia systemu informatycznego klasy ERP jak do inwestycji, a nie do zwykłego programu, który się wgra i już można używać. Potraktowanie wdrożenia systemu ERP jako inwestycji wyeliminuje wiele problemów. Co oznacza takie podejście ? Mianowicie to, że trzeba się do takiego działania przygotować, trzeba je zaplanować, ustalić co jest dla nas kluczowe, jakie korzyści chcemy uzyskać, jaki budżet przeznaczyć, jakie cele chcemy osiągnąć i jak mierzyć ich osiągnięcie oraz jakie problemy rozwiązać, należy wskazać ludzi, którzy w poszczególnych obszarach będą odpowiedzialni za dążenie do sukcesu w zakresie implementacji systemu na grunt swojej firmy.
Ostatni kryzys gospodarczy uświadomił firmom produkcyjnym, że takich inwestycji jak inwestycje w systemy informatyczne nie można odkładać na później. Firma produkcyjna musi w miarę elastycznie reagować na zmiany zachodzące na rynku. Aby reagować na zmiany trzeba mieć spory zakres informacji o tym co jest rentowne, a co nie, które produkty i działania przynoszą nam korzyści, a które generują największe koszty i dlaczego, firma musi wiedzieć w jaki sposób kształtować portfel produktów i usług, aby szybko dopasować się do nowych oczekiwań i szybko zareagować na problemy. Dane zarejestrowane w systemie informatycznym są bogatym źródłem informacji.
Firmy produkcyjne w ostatnich kilku latach poszukując systemów informatycznych koncentrują swoją uwagę na narzędziach, które umożliwiają planowanie i harmonogramowanie produkcji, zarejestrowanie i kontrolę produkcji w toku (kto, kiedy, ile, czego wykonał), umożliwiają rozliczenie pracowników i uchwycenie kosztów produkcji. Kadra zarządzająca chce wdrażać narzędzia zintegrowane, które będą wykazywały również pewien poziom elastyczności, aby móc odpowiednio zareagować w systemie ERP na zmiany w zamówieniach klientów i zmiany wynikające z dynamiki różnych rynków, na których firmy produkcyjne działają.
W swojej ofercie firma Streamsoft ma dwa systemy ERP. Pierwszy to Streamsoft Prestiż – system z bogatą paletą wielu gotowych funkcjonalności, który można rozbudowywać zgodnie z oczekiwaniami klienta (wtyczki, rozwiązania dedykowane). Drugi system ERP to Streamsoft Verto – system dedykowany, innowacyjny, posiadający szkielet funkcji. Preferencje klientów zmieniają się wraz ze zmianami jakie wymusza rynek, na którym działają. Obserwujemy jak zmienia się nasz system ERP – Streamsoft Prestiż – pod wpływem oczekiwań klientów i jak się rozwija dzięki potrzebom zmian jakie użytkownicy zgłaszają.
Jakub Chylewski, analityk/wdrożeniowiec, FBD
Informatyzacja jest elementem automatyzacji procesów, nie tylko produkcyjnych, ale wszystkich, które regulują lub wspomagają tzw. „codzienne życie„. Istotnym elementem podnoszącym ryzyko i zakres potencjalnych szkód jest czas przetwarzania informacji i podejmowanie decyzji. Wszędzie tam, gdzie człowiek jest najsłabszym ogniwem procesu, a ryzyko i skutki błędu są duże, szuka się rozwiązań o większym stopniu niezawodności. Bezpieczeństwo, jakość, wydajność – oto kierunki rozwoju otoczenia człowieka w obszarze produkcyjnym.
Narzędzia informatyczne są wyznacznikiem postępu i rozwoju cywilizacyjnego. Nie potrzeba zadawać pytania o to czy firma potrzebuje narzędzi informatycznych, to nawet nie jest pytanie o „być czy nie być” fabryki, lecz o zapewnienie istnienia i silnej pozycji gospodarczej kraju w skali świata.
Etapy wdrożeń projektów informatycznych już dawno zostały ustandaryzowane. Tak jak inne standardy, przykładowo PDCA lub 5S. Ostatnim i najtrudniejszy krokiem w całym procesie wdrożenia, jest utrwalenie nowego standardu. Moment , gdy firma wdrożeniowa „wyjeżdża”, pierwszy entuzjazm liderów wdrożenia nieco opada i pozostaje „zwykła codzienność”. Najczęściej, to ta zwykła, codzienna chęć powrotu do „starego”, jest największym zagrożeniem. Póki nie zostaną utrwalone nowe nawyki, zespół wdrożeniowy musi nieustannie monitować zachowanie pracowników w nowym procesie, reagować na każde odstępstwo. Jeśli tego nie uczyni, wówczas niezauważalnie projekt zostanie wypchnięty z obiegu przez dotychczasowe przyzwyczajenia i jedyną przyczyną niepowodzenia będzie fakt próby wdrożenia czegoś nowego.
System SURFBD zadebiutował w 2005 roku. Z jednej strony obecna wersja jest wynikiem ciągłego rozwoju systemu i w tym zakresie wciąż ma „ wspólne korzenie „. Z drugiej strony porównanie pierwszych wersji systemu z obecnym nie ma sensu, gdyż lata rozwoju, opartego przede wszystkim na realizacji potrzeb klienta, spowodowało ogromny skok funkcjonalny, jakościowy i wydajnościowy systemu. Można śmiało powiedzieć, iż każda kolejna wersja systemu oferuje nowe możliwości i nawet dla wieloletnich użytkowników jest „nowym produktem” Istnieje możliwość integracji naszego produktu z innymi systemami. Oprócz standardowego pakietu szkoleń, forma szkolenia i jego zakres dobierany jest w zależności od potrzeb użytkownika. Mogą trwać od kilka godzin do kilka dni.
Wiktoria Piwowarczyk, specjalista ds. sprzedaży, Trax S.A.
Firmie produkcyjnej potrzebne jest przede wszystkim Zintegrowane Rozwiązanie Informatyczne dedykowane konkretnej branży. Bolączką niezinformatyzowanych firm produkcyjnych, jest brak szybkiego dostępu do kluczowych informacji, odczuwalny wyjątkowo dotkliwie, gdy trzeba szybko podejmować decyzje. Dzięki Zintegrowanemu Systemowi Informatycznemu, kluczowe dane – dostępne w trybie on-line są na wyciągnięcie ręki, a kadra zarządzająca, może szybciej podejmować trafne decyzje.
Na pewno przyszłością produkcyjnych systemów IT będzie działanie w chmurze (cloud computing), opierające się na przeniesieniu usług IT (danych oprogramowania lub mocy obliczeniowej) na serwer i umożliwienie stałego dostępu poprzez komputery klienckie. Z chmurą uzyskuje się dostęp do danych, za pomocą połączenia z Internetem i przeglądarki internetowej. Inną tendencją będzie specjalizacja systemów w określonych branżach np. automotive, odlewnictwie, hutnictwie. Oznacza to, że producenci systemów opracowują specjalne dodatki do systemów, dedykowane określonym branżom.
Kluczowym oferowanym przez nas rozwiązaniem jest dedykowany produkcji Zintegrowany System Informatyczny Infor SyteLine – na polski rynek właśnie trafiła jego najnowsza wersja – 9.0. Poza tym istotna jest aplikacja Infor ION – służąca do integrowania różnych systemów informatycznych. Nowością jest również dodatek MES do systemu Infor SyteLine – Shop-Trak. Należy podkreślić, że preferencje klientów, ulegają zmianom i są zależne od ich aktualnych potrzeb. W związku z tym, firma Infor przeznacza ogromne nakłady finansowe na modyfikację i aktualizację swojego oprogramowanie, aby sprostać bieżącym potrzebom klientów.
Polskie przedsiębiorstwa w obliczu kryzysu działały bardzo zachowawczo i redukowały wydatki na inwestycje związane z sektorem IT. Jeżeli firmy decydowały się na zakup oprogramowania, to szukały tańszych rozwiązań, dlatego częstym kryterium wyboru rozwiązania była cena, a nie funkcjonalność. Przekornie powiem, że czas kryzysu był dobrym okresem na inwestycje, ponieważ przy zmniejszonych obciążeniach produkcyjnych, firmy mogły spokojniej przejść przez proces implementacji i przygotować się do pracy z systemem na wzmożonych obrotach.
Największym problemem we wdrażaniu jest zdecydowanie brak standaryzacji procesów biznesowych. Bardzo ciężko jest wdrożyć system, który ma sterować procesami, nie wiedząc, jak owe procesy w firmie przebiegają oraz jak osiągane są wyniki. Znaczącym problemem są także użytkownicy, którzy nie widzą potrzeby realizowania wspólnych celów w firmie.
Wiktor Pabian – dyrektor generalny , ZETO S.A.
W zasadzie trudno sobie dziś wyobrazić funkcjonowanie firmy produkcyjnej bez wdrożonych jakichkolwiek systemów informatycznych. Przynajmniej podstawowe systemy ERP (księgowo-magazynowo-sprzedażowe) w takich firmach istnieją i istnieć muszą. Niemniej jednak zdecydowana większość firm produkcyjnych wdrożyła już, albo zamierza wdrożyć dodatkowe systemy informatyczne ułatwiające pracę, a czasem wręcz umożliwiające prawidłowe funkcjonowanie przedsiębiorstwa. Mam tu na myśli systemy (lub dodatkowe moduły do systemów ERP) obsługujące planowanie produkcji a także nadzorowanie produkcji (systemy MRP II).
W zakładach produkcyjnych istnieje także drugi ważny obszar, który z naszych obserwacji jest dużo mniej zinformatyzowany. Mam tu na myśli obszar samej produkcji. Dla obszaru produkcji dostępne są np. systemy klasy MES – które w dużym uproszczeniu umożliwiają zbieranie w czasie rzeczywistym informacji bezpośrednio z urządzeń produkcyjnych, systemy klasy CMMS – wspierające służby utrzymania ruchu, systemy automatyki i sterowania itp. Można oczywiście zadać sobie pytanie, czy są systemy informatyczne działające na styku obszaru biznesowego i obszaru produkcyjnego – będące tłumaczem języka biznesu na język produkcji i odwrotnie. Wg mojego rozeznania tego systemów na rynku jest bardzo niewiele.
Informatyka wkracza coraz bardziej w obszary produkcyjne, gdyż firmy dostrzegły, że poza obszarem biznesowym istnieje także drugi obszar – obszar produkcji – który także wymaga informatyzacji. Wygląda na to, że producenci oprogramowania MRP/ERP także dostrzegli ten obszar. Dodatkowym trendem jaki daje się zauważyć w firmach produkcyjnych, to fakt dostarczania na produkcję maszyn wyposażonych w coraz bardziej zaawansowaną informatykę, a to docelowo umożliwi być może komunikowanie się systemów biznesowych bezpośrednio z tymi maszynami.
Firma ZETO S.A. jest głównie integratorem rozwiązań informatycznych. Posiadamy w swojej ofercie systemy wypełniające te luki, które nie pokrywają systemy wymienione powyżej. Przykładowo system WIERA, pozwala być interfejsem pomiędzy obszarem biznesu i produkcji. System ten wspiera także metodologie WCM (World Class Manufacturing) – czyli działania zmierzające do poprawy jakości i dążenia do doskonałości w produkcji. Generalnym przesłaniem tego systemu jest wyeliminowanie zapisów papierowych na produkcji i umożliwienie tzw. traceability produkcji. System ma też wbudowane mechanizmy tworzenia i analizowania dowolnych wskaźników.