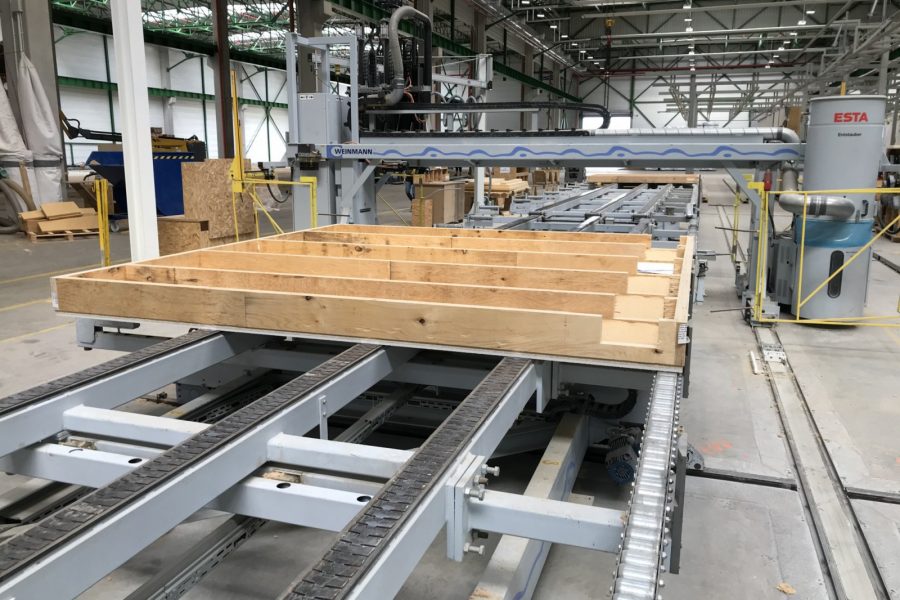
Prefabrykacja w służbie zdrowia
Z wykonanych w Czarnkowie elementów prefabrykowanych, jeszcze w tym roku w dużych miastach w Polsce, w ekspresowym tempie zostanie zmontowanych kilka obiektów przychodni medycznych. Realizacja tego ambitnego projektu będzie możliwa dzięki uruchomieniu w zakładzie Steico w Czarnkowie trzeciej linii do prefabrykacji. Zdaniem firmy, branża budownictwa drewnianego w Polsce już teraz rośnie w tempie 30 proc. rocznie i nie wyklucza dalszych inwestycji.
– W technologii prefabrykacji nie mamy obecnie żadnych ograniczeń, jeśli chodzi o bezpieczeństwo pożarowe, natomiast w przypadku wysokości budynku to na rynku polskim możemy realizować każdą inwestycję do wysokości pięciu kondygnacji – wyjaśnia Marcin Zboroń, dyrektor ds. rozwoju i kontaktów biznesowych w Steico sp. z o.o. – Nie ma limitu w kwestii kubatury i powierzchni realizowanej inwestycji, dlatego podejmujemy się wszystkich zleceń.
Wyzwanie w czasach pandemii
Takim podjętym przez Steico „wyzwaniem” będzie wykonanie prefabrykowanych elementów, z których zrealizowane zostaną budynki placówek medycznych. W Polsce powstało już wiele obiektów użyteczności publicznej w technologii prefabrykowanego szkieletu drewnianego, są szkoły i żłobki; po raz pierwszy zrealizowane zostaną przychodnie. Inwestor, doświadczony przedsiębiorca z branży budowlanej, od początku był przekonany do atutów prefabrykowanego budownictwa drewnianego. Kluczowym argumentem okazała się jedna z najważniejszych zalet technologii – krótki czas realizacji ambitnego projektu.
– Ma to związek z sytuacją epidemiologiczną. Inwestor zdecydował, że jest to ostatni moment, kiedy taką sieć przychodni należałoby w Polsce uruchomić. Dzięki temu, że budynki będą realizowane w systemie prefabrykacji, jest szansa, że jesienią, kiedy spodziewana jest druga fala epidemii, będą już funkcjonowały 2–3 obiekty. Docelowo przewidziane jest 15 budynków na terenie całego kraju – zdradza Marcin Zboroń.
Prefabrykacja nie tylko zwiększa wydajność procesu inwestycyjnego, usprawniając prace budowlane, ale pozwala wdrożyć nowoczesne rozwiązania i spełnić niezbędne wymogi czy to w zakresie energooszczędności i komfortu użytkowników, czy trwałości, bezpieczeństwa a nawet specyficznych wymogów stawianych wyspecjalizowanym obiektom.
– System dla przegród zewnętrznych i przegród dachowych, opracowany przy zaangażowaniu naszych technologów wspólnie z inwestorem, wymagał takich rozwiązań, aby przy zapewnieniu pełnej szczelności budynku, zachowały one równocześnie parametry otwartości dyfuzyjnej – tłumaczy dyrektor Zboroń. – Czyli, żeby budynki mogły oddychać, żeby mogły funkcjonować przez cały rok przy niskich i wysokich temperaturach, zapewniając odpowiedni klimat wewnątrz, a jednocześnie, aby niesprzyjające środowisko wewnątrz budynku, wynikające z jego specyfiki, nie wpływało na jego trwałość i jakość.
Zamówienia zawiodły, linie produkcyjne pędzą
U podłoża decyzji o podjęciu się usługi komplementacji elementów do produkcji domów drewnianych, czyli przejęciu od partnerskich firm wykonawczych części procesu realizacji inwestycji polegającej na prefabrykacji elementów gotowych, leżał prognozowany wówczas wzrost zamówień publicznych. W ciągu trzech lat, które były potrzebne na realizację procesu inwestycyjnego, sytuacja na rynku całkowicie się zmieniła – skala zamówień publicznych wynosi zaledwie ok. 20 budynków rocznie, czyli 10 proc. tego, czego oczekiwano. Mimo to w Czarnkowie uruchomiona została właśnie trzecia linia do prefabrykacji i – podobnie jak dwie poprzednie – już pracuje przy pełnym obłożeniu – zapewnia Marcin Zboroń.
To efekt niesamowitego rozwoju rynku komercyjnego. Aż 80 proc. zamówień, realizowanych w nowoczesnym zakładzie w Czarnkowie na dwóch liniach automatycznych i jednej manualnej, dotyczy domów indywidualnych. Gotowe do montażu elementy, są przygotowywane zarówno na zlecenie partnerów wykonawczych, współpracujących z firmą Steico, jak i deweloperów, którzy realizują inwestycje polegające na budowie domów bliźniaczych i szeregowych.
Moce produkcyjne nowoczesnego zakładu prefabrykacji w Czarnkowie pozwalają wyprodukować gotowe elementy do zrealizowania ok. 350 budynków wolnostojących o powierzchni użytkowej ok. 130 m. kw.. Dodatkowo, na linii ruchomej, tzw. motylkowej, obsługiwanej manualnie, można wykonać ok. 500 kompletnych dachów o powierzchni ok. 300 m.kw.. Od grudnia będą również realizowane inwestycje z kompletną stolarką budowlaną, czyli z zamontowanymi drzwiami i oknami.
– To, że uruchomiliśmy trzecią linię produkcyjną wynika z tego, że zamówień jest cały czas więcej, niż wynosi nasz potencjał produkcyjny. W przypadku materiałów drewnopochodnych dla budownictwa szkieletowego odnotowaliśmy wzrost rok do roku o około 35 proc.. W przypadku prefabrykacji nie mamy jeszcze punktu odniesienia dla własnych linii, natomiast dynamika polskiego rynku prefabrykowanego budownictwa drewnianego szacowana jest na poziomie kilkadziesiąt procent – mówi Marcin Zboroń.
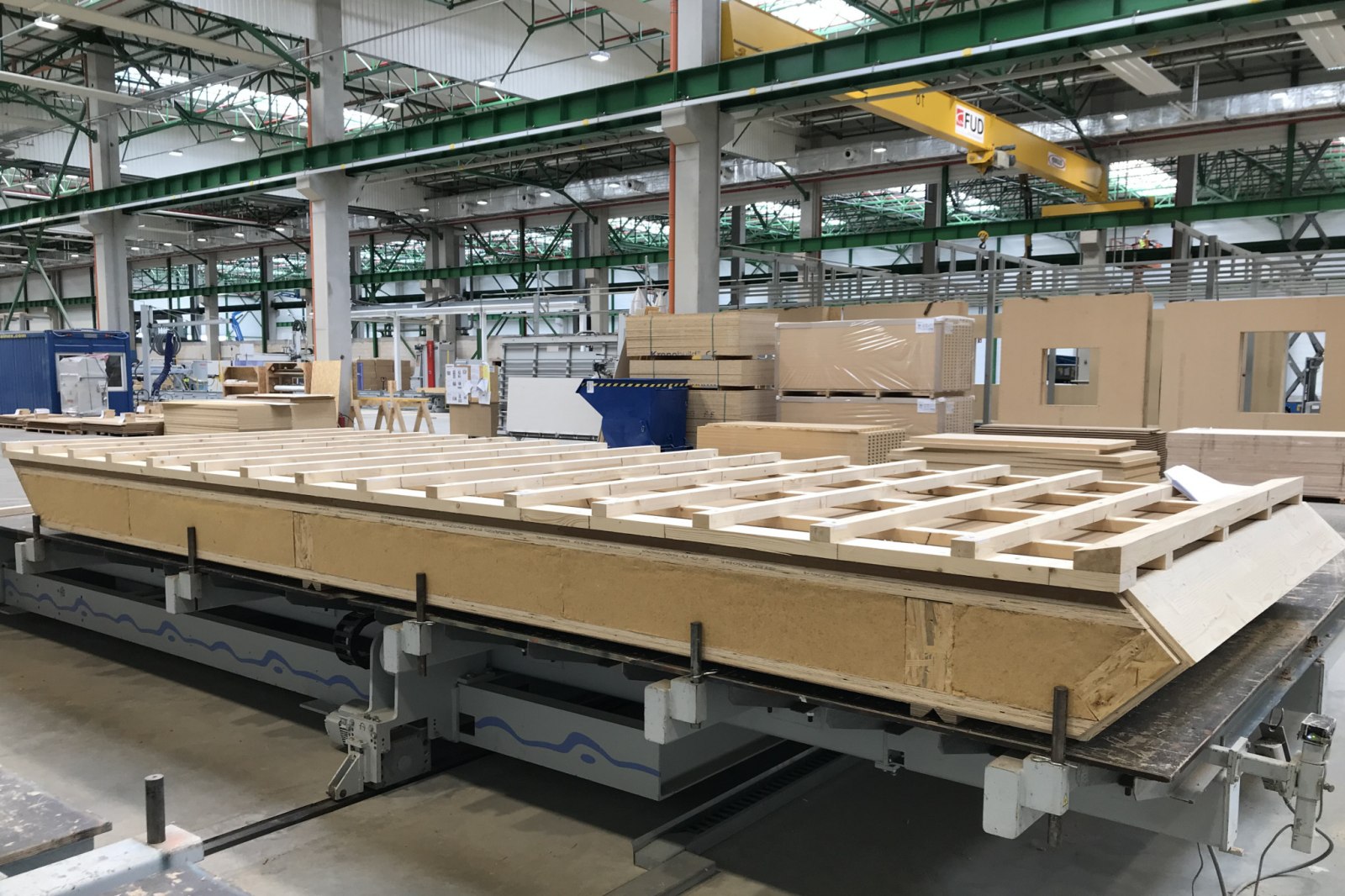
Wsparcie techniczne i merytoryczne
Prócz rozwijanego potencjału techniczno-technologicznego, Steico zbudowało wokół zakładu prefabrykacji sieć partnerską, tworzoną przez profesjonalnych wykonawców budynków w technologii szkieletu drewnianego. Aby zostać jej członkiem, trzeba spełniać rygorystyczne wymogi w zakresie wiedzy i doświadczenia we wznoszeniu budynków w konstrukcji drewnianej. Swoim partnerom, firma zapewnia również dodatkowe wsparcie techniczne i merytoryczne przy realizacji każdego wspólnego projektu.
– Zatrudniliśmy 15 osób do działu wsparcia technicznego. To są przede wszystkim konstruktorzy oraz doradcy techniczni, których zadaniem jest wspomaganie architektów i naszych partnerów wykonawczych w opracowaniu projektu wykonawczego – informuje Marcin Zboroń. – Cały projekt warsztatowy bierzemy na siebie i wykonujemy go do każdego projektu osobno, niezależnie od tego, czy jest to projekt powtarzalny, czy gotowy, czy indywidualny.
Rekord w Lubaszu
O tym, że projekt błyskawicznej budowy przychodni nie będzie problemem, dowodzi ostatni przykład realizacji dla prywatnego inwestora. Trzy dni prefabrykowano elementy według otrzymanego projektu, by dwa dni później w Lubaszu stanął gotowy dom jednorodzinny z poddaszem użytkowym. W rekordowym tempie powstał energooszczędny, ekologiczny i zdrowy budynek, a do jego montażu wystarczyły… 3 osoby i dźwig.
W sierpniu zrealizowano w Lubaszu (woj. wielkopolskie) pierwszy w Polsce budynek z systemowych prefabrykatów Steico Dom jednorodzinny o powierzchni parteru 71 m. kw. i z poddaszem użytkowym o powierzchni 50 m. kw. jest wykonany w technologii szkieletu drewnianego w standardzie pasywnym. Do jego realizacji użyte zostały kompletnie sprefabrykowane elementy ścian, stropu i dachu o łącznej powierzchni 480 m. kw.. Wykonane precyzyjnie i zgodnie ze specyfikacją, dzięki zautomatyzowanemu procesowi produkcji odbywającemu się pod stałym nadzorem, gotowe elementy zostały dostarczone na plac budowy, gdzie wystarczyło już tylko je zamontować.
Proces montażu prefabrykatów, na wcześniej przygotowanej płycie fundamentowej, trwał zaledwie dwa dni. Krótki czas realizacji, którego najlepszym przykładem jest chociażby zrealizowana inwestycja w Lubaszu, to jedna z wielu zalet prefabrykacji, dzięki którym metoda cieszy się coraz większą popularnością w naszym kraju. Dzięki temu, że na plac budowy dostarczane są elementy w zaawansowanym stopniu wykończenia, można budować szybciej i wygodniej od tradycyjnej metody murowanej. Wiele prac zostaje uproszczonych, a cały proces inwestycyjny jest w dużym stopniu skrócony. Mechanizacja procesu produkcji gwarantuje wysoką jakość paneli ścian, stropów i dachów, pozwalając wyeliminować błędy, których trudno uniknąć wykonując je na miejscu budowy.
Dom w Lubaszu został zaprojektowany w technologii Steico, w której realizowane są ekologiczne, trwałe i bezpieczne budynki w standardzie energooszczędnym i pasywnym. Prefabrykaty, których użyto do jego wykonania, zostały wytworzone z innowacyjnego i wytrzymałego forniru LVL, belek dwuteowych i płyt drewnopochodnych, z przegrodami wypełnionymi izolacją z włókien drzewnych. Taka konstrukcja pozwala w pełni wykorzystać naturalne walory i właściwości fizyczne drewna.