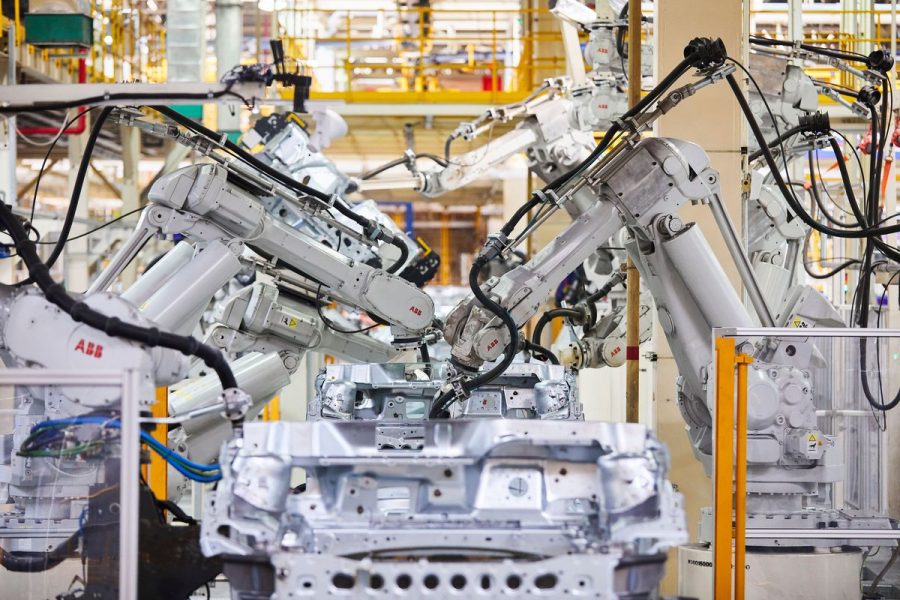
Przemysł zwalnia – na jak długo?
Gdy gospodarka jest rozpędzona, pieniądze wydaje się łatwo. Mało kto przejmuje się kosztami. Takie podejście ulega radykalnej zmianie, gdy pojawia się widmo spowolnienia. Przemysł nad Wisłą już wyhamowuje, wszyscy zastanawiają się już nie czy, ale kiedy i na jak długo się zatrzyma.
Po miesiącach szybkiego i niczym nieskrępowanego rozwoju przyszło rozczarowanie. Jak podał GUS, w ostatnim miesiącu ubiegłego roku produkcja przemysłowa w ujęciu rocznym była wyższa o zaledwie 1 proc. Nic dziwnego, że zaczęły pojawiać się pytania o recesję. – Scenariusze mogą być różne. Spowolnienie może być krótkie i płytkie, ale też może potrwać dłużej. Na dziś to wróżenie z fusów, ale pod uwagę trzeba brać różne warianty – zauważa Aleksander Faleńczyk z PSI Polska, która dostarcza systemy IT dla produkcji i logistyki. – Dla wielu firm to szok, bo mimo globalnych zawirowań, przemysł rozwijał się nieprzerwanie. Dziś następuje nieoczekiwana korekta, która podobnie jak w przypadku firm technologicznych za oceanem, zmusza do zmiany myślenia – zwraca uwagę Aleksander Faleńczyk, Dyrektor Sprzedaży, Systemy dla Produkcji, PSI Polska.
Jak trwoga to do… technologii
Co druga firma z sektora MŚP, pytana na zlecenie Siemens Financial Services, najbardziej obawia się rosnących kosztów energii. To, co niedawno w bilansie kosztów stanowiło zaledwie kilka procent i nie miało znaczącego wpływu na końcową cenę produkowanych wyrobów, zaczęło stawać się balastem. – Widzimy, że nagły wzrost rachunków za media a w szczegóności za prąd sprowokował przedsiębiorców do zmiany nastawienia i poszukiwania sposobów optymalizacji kosztów. Szczególnie że energia to tylko jedna z pozycji budżetowych, które w firmach produkcyjnych istotnie wzrosły. Nie możemy zapominać o kosztach wynikających z nieoptymalnych przezbrojeń czy rosnących cen materiałów i wynagrodzeń pracowników. Paradoksalnie stale idące w górę koszty mogą być zachętą do uporządkowania obszarów produkcyjnych i okołoprodukcyjnych – uważa Aleksander Faleńczyk.
To o czym mówi ekspert z firmy PSI Polska, znajduje odbicie w badaniach IFS. Wynika z nich, że dla firm największy priorytet mają inwestycje skupione na automatyzacji procesów biznesowych w produkcji (93 proc.) oraz poprawie procesów magazynowych (50 proc.). Sęk w tym, że kupowanie nowych maszyn jest łatwe, ale doświadczenia pokazują, że szybki zwrot z tego typu inwestycji, to raczej myślenie życzeniowe.
Konieczne oszczędności
Dziś nic nie wskazuje na to, by utrzymujące się wysokie koszty energii i materiałów miały spadać. To sprawi, że presja cenowa będzie się utrzymywać. W efekcie, żeby wyjść relatywnie suchą stopą przez trudniejszy okres, konieczne są oszczędności. Szczególnie w branżach wrażliwych na rynkowe fluktuacje. Do takich z pewnością zaliczyć możemy branżę metalową, w której nie od dziś mówi się o oszczędnościach. To słowo klucz dla większości rodzimych firm, które w obawie przed spowolnieniem w najbliższym czasie będą optymalizować koszty. Niemal ⅔ firm pytanych przez IFS składa takie deklaracje. Jednak, jak powiedział Peter Drucker, jeżeli czegoś nie możesz zmierzyć, to nie możesz też tego poprawić. – Rezerwy są naprawdę duże. Doświadczenia pokazują, że są firmy produkcyjne, w których wydajność dzięki dobrze dobranym narzędziom IT można zwiększyć nie o kilka a o kilkadziesiąt procent. Przykładem jest nie tylko branża metalowa, ale też np. meblarska – tłumaczy Aleksander Faleńczyk z PSI Polska.
Koncentracja na ograniczeniach
Wydawać by się mogło, że identyfikacja kosztów i ich precyzyjne wyliczenie nie powinno stanowić problemu, w końcu to tylko matematyka, ale problem jest. Eksperci zwracają uwagę, że rzeczywistość odbiega od tego, co próbuje się kreować w mediach. – Co prawda wiele firm wdrożyło w ostatnich latach systemy ERP, ale to tylko jeden z elementów Przemysłu 4.0. Duża część obszaru produkcyjnego pozostaje analogowa. Widać to doskonale w obszarze harmonogramowania zleceń produkcyjnych. Brak odpowiednich narzędzi, które wsparłyby przedsiebiorców skutkuje m.in znacznymi stratami związanymi z przezbrojeniem maszyn w efekcie czego firmy tracą czas i nie wykorzystują efektywnie swoich mocy produkcyjnych – mówi Aleksander Faleńczyk z PSI Polska.
Jednocześnie spora część systemów APS wykorzystywanych w polskich przedsiębiorstwach oferuje bardzo ograniczone funkcjonalności. Dzieje się tak, ponieważ były one wdrażane w zupełnie innej sytuacji biznesowej. W tym czasie wiele przedsiębiorstw bardzo się rozwinęło i obecnie potrzebują one wsparcia na zupełnie innym poziomie technologicznym, a i lista wyzwań mocno się zmieniła. Potrzebna jest aktualizacja. – Jedną z pierwszych korzyści, którą dostrzegają klienci po informatyzacji obszaru harmonogramowania, jest poprawa jakości danych. Nagle okazuje się, że produkcja konkretnego wyrobu może być szybsza, niż dotychczas zakładano. Można wytwarzać go też taniej, bo potrafimy zlokalizować wąskie gardła. Dziś oprogramowanie może dokładnie wyliczać na podstawie zmiennych nie tylko czas dostarczenia produktu, ale także wysokość kar za niedotrzymanie zlecenia – tłumaczy ekspert z PSI Polska. – Jeżeli kuleje przepływ półproduktów w zakładzie, to nowa maszyna nie rozwiąże problemu, wręcz może go spotęgować – dodaje.
Doświadczenie producentów z Ameryki i Europy pokazują, że oprogramowania APS może podnieść wydajność produkcji 1/5 i zredukować zużycie surowców aż o połowę. Te wartości pokazują, że jest o co kruszyć kopię.