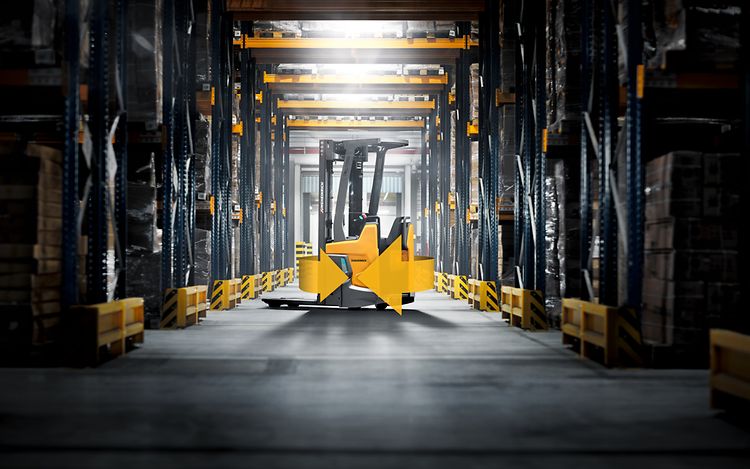
Przyszłość intralogistyki – technologia litowo-jonowa
Rosnąca świadomość ekonomiczna przedsiębiorców, rozwój nowoczesnych technologii oraz troska o środowisko sprawiają, że proekologiczne rozwiązania stają się istotną częścią każdego biznesu. Także w obszarze intralogistyki nastąpił przełom, który zmienił jakość prac wykonywanych w magazynach.
Dzięki wysokiej wydajności oraz nadzwyczajnej wytrzymałości, akumulatory litowo-jonowe wyprzedzają dotychczas stosowane na rynku baterie trakcyjne. Firma Jungheinrich jako pierwsza w branży dostarczyła na rynek serię wózków widłowych z tym nowoczesnym rozwiązaniem. Dziś maszyny z technologią li-ion cieszą się coraz większą popularnością. Jungheinrich jest jedynym producentem, który oferuje maszyny z akumulatorami litowo-jonowymi własnej produkcji, wraz z dedykowanym systemem ładowania. Baterie powstają w fabryce w Norderstedt i po przejściu bardzo restrykcyjnych testów trafiają na rynek.
Akumulatory litowo-jonowe niosą ze sobą wiele korzyści dla użytkownika. To nie tylko bardziej ekologiczna i bezpieczna technologia niż tradycyjne baterie trakcyjne – to także możliwość optymalizacji kosztów. Największą zaletą akumulatorów litowo-jonowych jest ich wyjątkowa wytrzymałość. Tym samym podnoszą wydajność pracy oraz pozwalają uzyskać lepsze zdolności przeładunkowe w magazynie. Co więcej, krótki czas ładowania i możliwość doładowywania sprawia, że wózki są niemal zawsze gotowe do działania, nie powodując przestojów w pracy. Akumulator litowo-jonowy Jungheinrich 24 V osiągnie 100% swojej sprawności zaledwie po 80 minutach doładowywania. Baterie o pojemności 80 V potrzebują do tego tylko 105 minut. Tradycyjne akumulatory kwasowe potrzebują natomiast od 8 do 10 godzin do pełnego naładowania.
Technologia litowo-jonowa od Jungheinrich zadebiutowała w 2011 roku w wózku EJE 122i i od tego czasu firma konsekwentnie ją rozwija. Najnowszym modelem wózka widłowego z tym napędem jest zaprojektowany na nowo model ERC 216zi. To pierwszy akumulatorowy wózek podnośnikowy ze zintegrowanym akumulatorem li-ion i rewolucyjną, niezwykle zwrotną i kompaktową konstrukcją.
Field testy wózków widłowych
Field test to jeden z kluczowych elementów wprowadzenia nowego modelu wózków widłowych Jungheinrich na rynek. W jego trakcie prototypowe modele maszyn sprawdzane są w magazynach klientów firmy, w warunkach realnej pracy z towarem. W przeszłości polityka Jungheinrich zakładała przeprowadzanie ich tylko u partnerów w Niemczech. W 2013 roku, po raz pierwszy w historii firmy odbyły się one za granicą – w Polsce. W 2019 roku odbył się kolejny field test na polskim rynku. Spalinowy wózek przeładunkowy z napędem hydrostatycznym TFG 425s został sprawdzony u klienta w magazynie pod Raciborzem.
Przed rozpoczęciem field testu, przedstawiciele Jungheinrich odbywają rozmowy z klientami w celu identyfikacji potrzeb przedsiębiorców. Ustalają jakie funkcje można dodać lub poprawić, aby nowe wózki pracowały wydajniej. Przeprowadzane są także ankiety, których analiza jest niezwykle istotna dla inżynierów Jungheinrich. Dzięki nim są oni w stanie implementować do wózka takie rozwiązania i technologie, które sprostają nowym oczekiwaniom klientów. Tak powstaje Mocap – makieta nowej maszyny. Po przejściu wewnętrznych badań jest ona bazą do stworzenia prototypu wózka, który zostaje wysłany do partnerów w ramach testów w rzeczywistych warunkach pracy.
Field test Jungheinrich w Raciborzu dotyczył przeładunkowego wózka spalinowego TFG 425s. Model ten jest przeznaczony do pracy na zewnątrz z różnymi towarami i niezależnie od panującej temperatury. Został sprawdzony pod każdym możliwym kątem m.in. stabilności jazdy z ładunkiem, czy ergonomii i bezpieczeństwa pracy operatora. Zweryfikowano także zużycie energii oraz liczbę towarów, które w trakcie testów przewiózł.
Field test TFG 425s potwierdził znaczny wzrost wydajności i produktywności maszyny, wynikający z implementacji nowoczesnych rozwiązań. Zwiększoną efektywność urządzenia oraz zmniejszone zużycie energetyczne udało się osiągnąć poprzez innowacyjne przeniesienie układu napędu hydrostatycznego z silnika na koła. Zaprojektowano także nową ramę wózka, która pozwoliła na wprowadzenie bardziej ergonomicznego stanowiska pracy operatora, co wydłuża czas jego pełnej koncentracji. Wyzwania współczesnej logistyki wymagają najlepszych i sprawdzonych rozwiązań. Dzięki przeprowadzanym field testom, Jungheinrich gwarantuje bezpieczne, ekologiczne i efektywne rozwiązania na miarę potrzeb nowoczesnej intralogistyki.
(Jungheinrich)