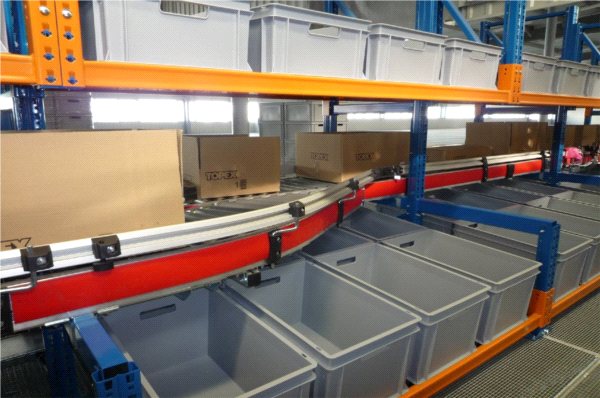
SOFTLAB ERP usprawnia kompletację
Sprawnie funkcjonujący system IT, przy odpowiednim wykorzystaniu posiadanej przez przedsiębiorstwo wiedzy logistycznej, może przynieść firmie realne korzyści. Topex zdecydował się na wdrożenie systemu ERP firmy Asseco Business Solutions, dla wsparcia swoich procesów
Projekt realizowano w nowym, centralnym magazynie firmy Topex. Budowa obiektu była inwestycją długoterminową, dającą firmie pełne możliwości wyboru implementowanych technologii magazynowych. Grupa projektowa, tworząc ramy inwestycyjne, wzięła pod uwagę dotychczasową specyfikę działalności i organizacji logistycznej firmy. Uwzględniono to, że przedsiębiorstwo wykorzystuje trzy różne kanały dystrybucyjne: tradycyjny, nowoczesny oraz eksportowy, co miało decydujące znaczenie przy powstawaniu części magazynowej projektu. Podstawowym wskaźnikiem oceny wariantów był współczynnik NPV (Net Present Value) w horyzoncie następnych 15 lat. W ramach realizowanego projektu, we wdrażanym systemie Asseco SOFTLAB ERP firmy Asseco Business Solutions, Topex zastosował własne, innowacyjne rozwiązania w zakresie optymalizacji pracochłonności procesów. Na realizację projektu przedsiębiorstwo otrzymało wsparcie z Unii Europejskiej, w ramach Programu Operacyjnego Innowacyjna Gospodarka.
Analiza projektu
Przy projektowaniu firma zmierzyła się z problemem biegunowo zróżnicowanego towaru pod względem wymiarów, wagi i właściwości. Powstała potrzeba, znalezienia sprawnych rozwiązań i funkcjonalności równocześnie dla zróżnicowanych gabarytowo towarów, takich jak: nasadki klucza, wiertła 1mm, okulary, łaty murarskie, żurawie warsztatowe i naboje gazowe do imadeł, kowadła. W związku z tym przeprowadzono analizę na podstawie, której wyznaczono magazynowi do spełnienia parametry, uwzględniając szeroki asortyment firmy. Za górną granicę szerokości asortymentu przyjęto ok. 10 000 SKU, przy wydajności magazynu 25 000 linii podczas ośmiogodzinnego dnia pracy i założeniu niższych kosztów magazynowych oraz jednostkowych na linię asortymentową przy zamówieniu.
System pozwala konsolidować kilka zamówień na wczesnym etapie
W oparciu o posiadane doświadczenie Topex wiedział, że pracochłonność procesów intralogistycznych osiąga swoje maksimum w trakcie trwania kompletacji magazynowej. W projekcie wyszczególniono towary poddane procesowi tradycyjnemu oraz nowoczesnemu (dla sieci, gdzie wymagane jest przepakowywanie towaru). Dzięki zdobytej wiedzy, firma, chcąc zmniejszyć koszty jednostkowe w nowym magazynie, skupiła się na optymalizacji dwóch obszarów: pakowni i kompletacji.
Kategoryzacja towarów
Zróżnicowanie towarów znajdujących się w magazynie, wykluczało zastosowanie wyłącznie automatyki, która uwzględniałaby kategoryzację składowanych produktów. Aby wydzielić procesy logistyczne, towary podzielono na trzy grupy, według dwóch jednoczesnych kryteriów: gabarytowego, z granicą powyżej 1150 mm (pomiędzy 1150 mm a wymiarami pojemnika w automatyce oraz towary mieszczące się w pojemniku stosowanym na liniach kompletacyjnych), objętości linii z granicą ok.10 litrów ( najczęściej pobieranym towarom, które zostały zakwalifikowane do automatyki przydzielono także miejsca pobrania w strefie „pełno kartonowej” do obsługi linii o objętości przekraczającej graniczną objętość linii).
Powstałe w ten sposób kategorie wymagały od firmy zastosowania w systemie informatycznym trzech oddzielnych procesów kompletacji. Pierwszy z nich przeznaczony był dla towarów drobnych, osiągających 2 500 linii na godzinę, przy 8h pracy, dających 10 m³/h. Pozostałe dla obsługiwania pełnych kartonów oraz ponadgabarytowych linii, osiągających miernik 50 m³/h, przy 500 liniach / godzinę. W związku z tym, proces kompletacji trzeba było zaprojektować z podziałem na strefy, z jednoczesnym uwzględnieniem atomowego progu wydania ze strefy pełnokartonowej, tak żeby system WMS, w zależności od objętości linii, decydował, z której strefy dana linia będzie kompletowana . Takie odfiltrowanie „tłustych” linii, znakomicie upraszcza i usprawnia pracę automatycznej linii kompletacyjnej. Firmie chodziło o maksymalizację wydajności poszczególnych procesów w relacji do nakładów inwestycyjnych, czyli w tym przypadku, do zakresu automatyzacji procesu kompletacji. Pamiętano przy tym, że zbytnie skomplikowanie procesu, może spowodować szereg niekorzystnych oddziaływań. – Zbyt trudny system wymaga, bowiem szkoleń, powoduje natłok zbędnych informacji i kosztuje przedsiębiorcę cenny czas, dlatego radziłbym posłużenie się metodą, jak najlepszego odzwierciedlania w projektowanym systemie specyfiki danego magazynu – wyjaśnia Dariusz Robak, kierownik projektu i zastępca dyrektora logistyki ds. rozwoju w firmie Topex.
Parametryzacja stref
Priorytetowa grupa towarów objętych automatyczną linią kompletacyjną wyniosła ok. 4500 SKU, pozostałą część ok. 5000 SKU objęto kompletacją nieautomatyczną. Do pierwszych z nich, Topex zastosował przepływowe regały rolkowe, kompletacyjne bez rolek oraz półkowe, które zostały umieszczone w odpowiednim oddaleniu od stacji kompletacyjnej. Zgodnie z założeniami projektu, opisany proces kompletacji strefowej wpisano w funkcjonalności wdrażanego systemu Asseco SOFTLAB ERP firmy Asseco. – Systemy Asseco BS umożliwiają pełne odwzorowanie procesów biznesowych klienta zgodnie z jego potrzebami. Integralną częścią każdego wdrożenia jest analiza, podczas której specjaliści Asseco BS wraz z klientem projektują najbardziej efektywne przebiegi procesów, które następnie są implementowane w systemie. Dzięki temu system informatyczny dobrze odzwierciedla rzeczywistość, dając wszystkie niezbędne informacje, a procesy przebiegają zgodnie ze specyfiką przedsiębiorstwa i faktycznymi potrzebami klienta, usprawniając pracę firmy.– powiedział Bogusław Tober project manager marki Asseco SOFTLAB w Asseco Business Solutions.
Nowe funkcjonalności
Implementacja wymagała utworzenia nowych funkcjonalności w systemie Asseco SOFTLAB ERP. Pierwsza z nich decyduje, o doborze zawartości kartonu na linii kompletacji automatycznej. Opcja gwarantuje, że w jednym kartonie nie znajdą się towary, które mogłyby sobie zaszkodzić ze względu na swoją wagę lub kruchość. W tym celu algorytm doboru zawartości kartonu, w zależności od właściwości towaru, dzieli produkty na kompatybilne i niekompatybilne kategorie – tzw. zasada piramidy.
Proces kolejkowania zamówień w magazynie oparto na tzw. mechanizmie tras
Kolejna innowacyjna funkcjonalność to tzw. punkt trasowy, który konsoliduje kilka zamówień na wczesnym etapie, w skutek czego do kompletacji dociera zamówienie już skonsolidowane, obniżając w ten sposób zarówno koszty magazynowe, w tym przede wszystkim koszty kompletacji, jak i koszty transportu. Konsolidacja zamówień na wspólnym nośniku zewnętrznym, wymaga jednak wyraźnej zgody klienta, co także jest odzwierciedlone w systemie.
Proces kolejkowania zamówień w magazynie został oparty na tzw. mechanizmie tras, dzięki któremu magazyn posiada informacje o czasie, w którym dane zamówienie musi być skończone. Opcja kolejkuje operacje magazynowe w sposób automatyczny, pozwalając zdążyć magazynowi na czas, przed zaplanowanym załadunkiem. Mechanizm uwzględnia także obciążenie poszczególnych stref, sprawiając, że pracują równo.
Dariusz Robak zastępca dyrektora logistyki ds. rozwoju w Topex – Umiejętność optymalizowania procesów jest niezbędna podczas projektowania – pozwala zaoszczędzić miliony w procesie budowy i wyposażania w nowoczesne technologie dużych magazynów. Jest także potrzebna w codziennej pracy. Zespół kierowany przeze mnie, otrzymał nagrodę od dziennika Gazeta Prawna, za autorskie aplikacje dotyczące optymalizacji pracochłonności procesów kompletacji. Dynamiczne, podążające za zmieniającą się strukturą sprzedaży zarządzanie towarem w ramach danej strefy i pomiędzy nimi, w tym w szczególności odpowiednie rozlokowanie stałych i dynamicznych miejsc pobrania, przekłada się automatycznie na większą wydajność. Ten proces nieustannej, codziennej optymalizacji prowadzimy na specjalistycznym oprogramowaniu DR WAREHOUSE, wizualizującym stan poprawności rozlokowania miejsc pobrania we wszystkich strefach kompletacji. Dzięki temu nasz magazyn, bazując zarówno na statystyce historycznej, jak i na danych z zamówień jeszcze niezrealizowanych, jest codziennie dostosowywany do przyszłych wyzwań, tak jak bolid F1 jest ustawiany do specyfiki toru, na którym ma się odbyć najbliższy wyścig.