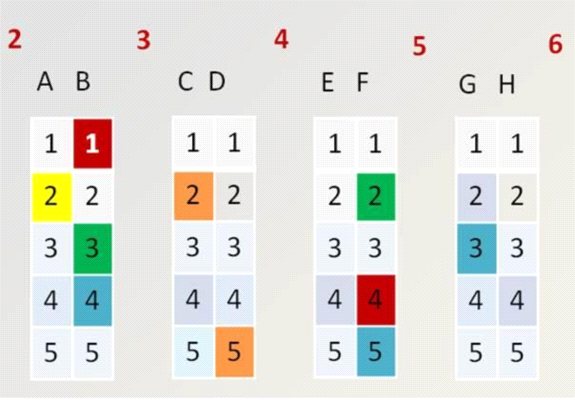
Uczący się system
Systemy IT do zarządzania magazynem ciągle się rozwijają, umożliwiając stosowanie przeróżnych strategii wydania towaru. I nie chodzi tutaj o fakt zastosowania kodów kreskowych i eliminację dokumentów papierowych, bo to już przestaje być celem wdrożenia nawet w małych magazynach...
Jeszcze 10 lat temu w Polsce pokutowało stwierdzenie, że głównym zadaniem systemu WMS jest elektroniczna rejestracja zdarzeń w magazynie, czyli praca z kodami kreskowymi. W istocie, wiele oferowanych wówczas systemów do magazynów pracowało właśnie w ten sposób i wydawało się, że jest to wystarczające. Pracownicy magazynowi pracowali na terminalach, ale tak naprawdę to oni lub kierownik magazynu musieli decydować o tym, co mają robić i kiedy. Wybierając na terminalu odpowiedni proces pracownik musiał niekiedy podjąć decyzję, jaki dokument wydania wybrać, aby zacząć pracę. Tak naprawdę systemy IT pracujące w taki sposób trudno jest nazwać systemami do zarządzania magazynem. Bardziej adekwatną nazwą dla takich rozwiązań jest system do rejestracji lub system ewidencyjny. Dla wielu małych magazynów, w którym pracuje kilku pracowników, taki system prawdopodobnie będzie wystarczający, ale w przypadku większych magazynów pozostaje jeszcze duży obszar do zoptymalizowania.
Kompletacja
Zaawansowane systemy do zarządzania magazynem pracują inaczej. Pracownik magazynowy nie podejmuje decyzji dotyczącej np. wyboru dokumentu wydania. Tak naprawdę nie wie on, dla jakiego klienta realizowana jest zbiórka towaru. Jemu ta informacja jest niepotrzebna. Zadaniem pracownika magazynowego jest efektywna, bezbłędna praca i wykonywanie zadań przydzielanych w odpowiednim momencie przez system WMS. Dzięki podejściu zadaniowemu możliwe jest zastosowanie wielu rodzajów organizacji procesu kompletacji. Przykładem jest możliwość rozdzielania zamówienia na wiele obszarów pracy, np. osobno na obszar kompletacji na antresoli i obszar kompletacji z regałów paletowych. Z kolei organizacja przebiegu kompletacji, czyli tzw. załatwianie może być jednostopniowe (wg zleceń) lub wielostopniowe (wg artykułów). Możliwa jest również komasacja zleceń, czyli możliwość kompletacji towarów z różnych zleceń w jednym cyklu kompletacyjnym. Pracując na dokumentach, a nie na zadaniach, nie jest możliwe uruchomienie tak wielu różnych organizacji kompletacji. Optymalizacja kończy się najczęściej na określeniu optymalnej drogi zbiórki towaru.
Puste przebiegi
Praca na zadaniach nie wyczerpuje możliwości systemów WMS. System może sprawnie przydzielać zadania pracownikom, ale nadal nie zagospodaruje on w pełni czasu dla wszystkich pracowników. Każdy z nich pracuje bowiem w ramach danego procesu. Pracownik odkładający palety do regałów będzie pracował na zadaniach przesunięć, osoba kompletująca towar na zadaniach kompletacji, natomiast wózkowy uzupełniając towar z zapasu do miejsc kompletacyjnych nie dostanie innych zadań niż właśnie zadania uzupełnień. Teoretycznie wydaje się, że taka praca jest optymalna, natomiast statystyki mówią zupełnie co innego. Okazuje się, że 50-60% czasu pracy w magazynie to tzw. puste przebiegi, czyli praca nieefektywna. Coś jest wykonywane, ale nie przynosi to żadnej korzyści. Przykładem jest fakt, że większość cykli transportowych wózków widłowych jest wykonywana z pustymi widłami. Jak można zminimalizować te puste przebiegi?
Przeplatanie zadań
Odpowiedzią są systemy takie jak Astro WMS, które potrafią robić tzw. przeplatanie zadań (ang. tasking to leaving lub task interleaving). Pracownik magazynowy odkładając paletę z obszaru doków do obszaru składowania może – w drodze powrotnej po kolejną paletę z przyjęć – wydać inną paletę odkładając ją do obszaru doków. Z kolei pracownik uzupełniający obszar kompletacji z obszaru zapasów może przy okazji wykonać przesunięcie porządkowe. Decyduje o tym system WMS na podstawie priorytetów zadań, nadawanych automatycznie tworząc wówczas tzw. multicykle. Dzięki takiemu podejściu, według wielu niezależnych badań, można uzyskać wzrost produktywności w magazynie od 10 do nawet 40%. Dla średnich i większych magazynów są to oszczędności ogromne, które przekładają się bezpośrednio np. na całkowite koszty wytworzenia produktu, gdzie koszty logistyczne stanowią zazwyczaj od kilku do kilkunastu procent.
Priorytety wydań
Organizacja kompletacji w systemach WMS wygląda różnie, jeśli chodzi o jej parametryzowanie. Niektóre systemy WMS wymagają „uszycia” procesów ściśle pod wymagania klienta, w innych systemach WMS możliwa jest konfiguracja, którą później może zmienić użytkownik tego systemu, co przekłada się na niższe koszty eksploatacji systemu (brak modyfikacji). Jaką organizację kompletacji więc wybrać? Co, jeśli okaże się ona nietrafna? Jak zachowa się system WMS w przypadku spiętrzeń?
Dla wydań pełnopaletowych odpowiedzią są tzw. smartaski, czyli adaptacyjne przeplatanie zadań dostępne w zaawansowanym module systemu Astro WSM. Polega ono na dynamicznym wybieraniu strategii kompletacji w zależności m.in. od tego, gdzie dokładnie znajdują się pracownicy magazynowi, jakie są priorytety zadań, oraz od całkowitych czasów transportu towaru. Skąd system WMS wie, jakie są wartości tych czasów? Otóż nie wie, przynajmniej na początku wdrożenia, ponieważ się ich „uczy”. Zbiera on na bieżąco wszystkie wartości czasów przemieszczeń towarów pomiędzy przeróżnymi punktami tworząc „czasową mapę magazynu”. Dzięki temu system WMS wie, jaką paletę wybrać do wydania, aby czas realizacji był jak najszybszy. Najpierw wyszukuje towary do wydania według priorytetu wysyłki. Następnie sprawdza, czy przypadkiem nie ma odpowiedników tych palet w korytarzu roboczym, w którym znajduje się już operator wózka widłowego. Jeśli są, podejmuje decyzję o wydaniu tego towaru, którego całkowity czas wydania jest najmniejszy. Jeśli brak, wybiera towary pierwotnie wyznaczone i sprawdza czasy całkowite przemieszczeń dokonując najlepszego wyboru. Taki sposób kompletacji przynosi według jednego z największych klientów Consafe Logistics dwucyfrowy wzrost produktywności.
50-60% czasu pracy w magazynie to tzw. puste przebiegi, czyli praca nieefektywna
Z kolei w przypadku wydań drobnicowych Astro WMS może pracować w trybie priorytetów wydań lub priorytetów dróg minimalnych, gdzie tryb ten określa system WMS automatycznie na podstawie dostępnego czasu oraz ilości zamówień. Gdy czasu jest mało i należy jak najszybciej zebrać najbardziej priorytetowe zamówienia, wówczas system WMS wyznacza pracownikowi lokalizacje do zbiórki towarów pilnych. W tym przypadku wózek widłowy może pokonywać duże odległości, bo priorytetem jest zbiórka towarów pilnie wymaganych. Z kolei, gdy czasu mamy więcej, system WMS może przełączyć się na tryb minimalizacji przejazdów. Polega to na tym, że system WMS wyszukuje najpierw lokalizacje z towarami najbardziej wymaganymi. Następnie w pobliżu tych lokalizacji wyszukuje towary inne, mniej priorytetowe. Celem jest odwiedzenie jak największej liczby lokalizacji w niedużym obszarze i „zapełnienie wideł”.
To z pewnością nie koniec innowacyjnych metod kompletacji. Nowoczesne systemy WMS prześcigają się w tworzeniu nowych algorytmów, które nie byłyby możliwe do zastosowania z wykorzystaniem kartki i ołówka. Coraz większą rolę odgrywać będą systemy takie jak Astro WMS potrafiące uczyć się i samodoskonalić minimalizując nie tylko koszty operacyjne, ale również czas potrzebny na konfigurację i administrowanie systemem WMS.