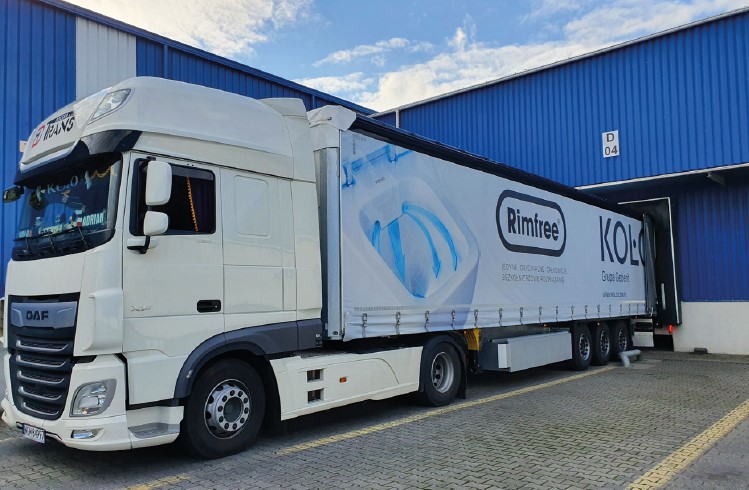
Uporządkowane procesy
O usprawnianiu przepływów i optymalizowaniu procesów magazynowych oraz funkcjonowaniu centrum dystrybucyjnego Geberit w Kole z Grzegorzem Cuptą, dyrektorem logistyki regionu CEE, rozmawia Kinga Wiśniewska.
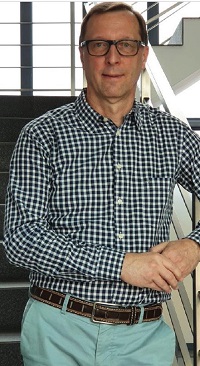
Od niemal 20 lat pracuje Pan w centrum dystrybucji w Kole w jednej lokacji z zakładem ceramicznym. Dzięki długiemu stażowi miał Pan okazję uczestniczyć w zmianach, jakie dokonywały się przez te lata w dystrybucji. Obecnie Geberit ma w Polsce trzy fabryki…
Struktura Geberitu w Polsce obejmuje dwa zakłady ceramiczne – jeden znajduje się w Kole, drugi we Włocławku. W Ozorkowie znajduje się zakład, w którym produkowane są wanny akrylowe i kształtki – elementy połączeniowe do rur, np. kolanka, złączki. Mamy poza tym w Warszawie spółkę sprzedażową, a w Łodzi spółkę serwisową obsługującą pod względem finansowo-księgowym kraje europejskie.
Jaki zasięg ma centrum dystrybucji, którym Pan zarządza?
Śmieję się, że jest to centrum dystrybucji z zasięgiem od morza do morza. Mamy dwa rodzaje potoków towarów, jeden wewnątrz grupy – obsługujemy zakłady produkcyjne, przesyłając ich wyroby do podobnych centrów dystrybucyjnych w innych krajach. Drugi potok to sprzedaż do klientów, odbiorców naszych produktów w regionie. Pod względem sprzedaży obsługujemy klientów od krajów bałtyckich aż po Adriatyk, koniec naszego regionu znajduje się na granicy Grecji i Włoch.
W sąsiedztwie centrum dystrybucji w Kole znajduje się zakład produkcyjny, który obsługujemy w 100%, podobnie całą produkcję we Włocławku. Mamy tam poza tym centrum dystrybucyjne tylko dla potoków wewnątrz grupy – buforujemy towary i przesyłamy je do centrów dystrybucji wewnątrz grupy lub do centrum dystrybucji w Kole. Część produkcji związana ze starym portfolio w Ozorkowie, czyli wyposażenie łazienek – wanny i kabiny prysznicowe, są przesyłane do centrum dystrybucji w Kole, a część tzw. złączkowa wysyłana jest bezpośrednio do zautomatyzowanego centrum dystrybucyjnego w Pfullendorfie w Niemczech.
Ma Pan możliwość spojrzenia z perspektywy czasowej na to, jak przez lata zmieniały się modele i procesy dystrybucji…
Gdy przyszedłem do firmy w 2001 roku, to logistyka, owszem, była zdefiniowana, ale na dość prostym poziomie. Nie było systemu do zarządzania magazynem. Wszystko właściwie opierało się na rejestracji przyjęć i wydań, na papierowych listach przygotowania dostaw. Magazyny, którymi wówczas dysponowaliśmy, były niskie i ciemne. W 2007 roku wybudowaliśmy obiekty, w których obecnie funkcjonujemy, i wdrożyliśmy system zarządzania magazynem oparty o SAP. W 2015 roku zakłady przejął Geberit, który dąży do standaryzacji. W grupie wypracowany został plan wdrożenia we wszystkich centrach dystrybucji systemu zarządzania opartego na rozwiązaniu SAP eWMS. To był dla nas impuls. Pomyślałem, że jeżeli mamy wdrożyć nowy system, w którym są nowe funkcjonalności, warto podjąć wysiłek i przeanalizować rozkład naszego magazynu, produktów, jak i same procesy.
Chciał Pan przygotować magazyn do lepszego wykorzystania funkcjonalności nowego systemu.
Tak, ale na co dzień w firmach jest tak, że wszyscy skupiają się na działaniach operacyjnych i często nie ma wolnych zasobów ludzkich, żeby przeprowadzać głębokie analizy. Oczywiście, wykonuje się je, ale w dosyć uproszczony sposób. Zdecydowaliśmy się skorzystać z usług firmy zewnętrznej, która miała doświadczenie, narzędzia i zasoby do przeprowadzenia dogłębnej analizy. Mieliśmy świadomość, że nasze procesy można jeszcze bardziej zoptymalizować, więc wyniki audytu nas nie zaskoczyły. Zdecydowaliśmy się na zoptymalizowanie procesu kompletacji, bo z analizy wynikało, że to proces wymagający szczególnej uwagi.
Jak wyglądała kompletacja przed wprowadzeniem zmian?
Nasze wyroby nie są wdzięcznymi produktami do magazynowania i kompletacji, ponieważ część z nich to produkty ciężkie, duże, gabarytowe. Bo choć na przykład mała umywalka o długości 40 cm jest łatwa w kompletacji, to kabina, która waży 50 kg, ma wysokość 2 m i szerokość 1,20 m, czy narożna wanna, już nie. Stary system bazował na stałych miejscach kompletacji – mieliśmy tylko jedno miejsce przeznaczone dla danego produktu. Potrzebowaliśmy rozwiązania na sytuacje, gdy potrzeba było do skompletowania zamówienia więcej niż jednej palety danego produktu. W 2007 roku, pracując nad wdrożeniem systemu SAP, myśleliśmy, że będziemy pracować w oparciu o bufor – proces uzupełniania miejsca kompletacji będzie przebiegał dwustopniowo, czyli z miejsca składowania do buforu i potem z buforu do miejsca kompletacji, jeśli w miejscu kompletacji będzie stan zero. Proces wyglądał więc w ten sposób: pracownik szedł w miejsce pobrania – stałe dla danego produktu, pobierał go, ale gdy nie było wystarczającej ilości, musiał jechać do buforu po kolejną paletę, przewieźć ją do miejsca kompletacji i uzupełnić brakujące sztuki. Poruszanie się pomiędzy lokalizacjami zajmowało 50% czasu kompletacji.
W jaki sposób zoptymalizowany został ten proces?
Nowy system eWMS umożliwił wdrożenie dynamicznych miejsc kompletacji. System sprawdza dostępność produktów i alokuje palety w różne miejsca kompletacji zgodnie z zapotrzebowaniem. Obecnie, gdy do zrealizowania zamówienia potrzeba więcej sztuk produktu, dostępny jest on w kilku miejscach – proces kompletacji przebiega bez przerwy. Zwolnione miejsce jest w następnym cyklu pobrań uzupełniane innym produktem. Ścieżka kompletacji skróciła się średnio o 27% oraz zlikwidowaliśmy bufor.
Potem uznaliśmy, że skoro mamy dynamiczne miejsca kompletacji, warto stworzyć strategie, podzielić magazyn na strefy i podstrefy. To też było ciekawe wyzwanie.
Jak więc obecnie podzielony jest magazyn?
Jedną z wydzielonych stref zajmują produkty, które dystrybuujemy od naszych kolegów z Niemiec. Mamy dla nich specjalną strefę kompletacji i nie rozmieszczamy ich w magazynie, jak działo się przy korzystaniu z poprzedniego systemu. Druga strefa, to strefa towarów wysoko rotujących, znajdująca się najbliżej miejsca pakowania – raz na kwartał analizujemy rotację i aktualizujemy towary, które powinny się w niej znajdować. Trzecia strefa to strefa produktów tzw. B, które są często pobierane, dalej wolno rotujące produkty C i strefa produktów D, które wychodzą już z oferty. Nie mają one swojego miejsca kompletacji i pobierane są z miejsca składowania. Dla każdej z tych stref opracowaliśmy strategię rozmieszczania, uzupełniania i pobierania.
W centrum tworzymy również zestawy dla klientów. W dziale VAS, czyli usług dodatkowych, tworzymy zestawy, np. kompletując wszystkie produkty potrzebne do zamontowania sprzętu w domu w jeden karton, tzw. all in one; przygotowujemy produkty na specjalne potrzeby, na przykład oklejamy je, pakujemy zgodnie z oczekiwaniami klienta.
W wyniku tych wszystkich prac – zdefiniowania na nowo rozmieszczenia w magazynie i procesu kompletacji zyskaliśmy również narzędzia do przeprowadzania szybkiej analizy stanów magazynowych.
Co poleciłby Pan szefom centrów dystrybucji przed wdrożeniem nowych systemów?
Przegląd procesów i ich uproszczenie na tyle, na ile jest to uzasadnione i możliwe. Przegląd jest konieczny, aby potem móc powiedzieć świadomie: OK, to teraz decyduję się na takie, a nie inne rozwiązania. Warto przyjrzeć się wszystkim funkcjonalnościom, bo czasami nie wiemy, czego możemy chcieć od systemu. Nasze centrum dystrybucji jest oparte o tradycyjną technologię, inaczej wygląda to w centrach dystrybucji wykorzystujących w dużym stopniu automatykę.
Procesy w centrum dystrybucji wyrobów ceramicznych wiążą się z wyzwaniami dotyczącymi nie tylko logicznego, ale również fizycznego przeprowadzenia procesów.
Niektóre nasze produkty są ciężkie lub na tyle duże, że muszą być przenoszone przez dwie osoby. Do każdego z nich trzeba przygotować w miarę standardowe i uniwersalne rozwiązanie. Adaptujemy regały pod produkty, które wymagają więcej niż jednego miejsca paletowego wszerz, jak i w głąb regału.
Większość naszych pracowników pracuje u nas od wielu lat. Znają wyroby na tyle, że po numerze wiedzą, co jest potrzebne, żeby dobrze przygotować je do wysyłki. Bazujemy na doświadczeniu pracowników między innymi w procesie kompletacji i budowania palet miksowych. Zdecydowaliśmy, że tego procesu nie oprzemy o system, bo musielibyśmy zasilić go naprawdę wieloma danymi, a i tak optymalizacja nie zawsze byłaby dla nas satysfakcjonująca. Mówię to w oparciu o doświadczenia z centrum dystrybucji w Niemczech. Nasi pracownicy, przepakowując towar z wózka kompletacyjnego na paletę, potrafią tak ułożyć wszystkie produkty, że są doskonale zabezpieczone w transporcie i zajmują jak najmniej palet.
Czy planuje Pan wdrażanie automatycznych rozwiązań? Automatyzacja nie zawsze jest lekiem na całe zło…
Zdecydowanie. Ktoś powiedział: najpierw uporządkuj wszystkie swoje dotychczasowe procesy, a potem dopiero automatyzuj, a nie automatyzuj, a potem myśl, jak je uporządkować. Mamy uporządkowane procesy, może jeszcze nie do końca wszystkie, bo zawsze można jeszcze coś poprawić. Podejmujemy próby automatyzacji. Rozważaliśmy wprowadzenie wózków autonomicznych do odbioru palet z produkcji. Opracowaliśmy taki projekt, ale nie możemy go wdrożyć. Wszystko rozbija się o jedną trywialną rzecz. Nasze palety z produkcji zabezpieczane są folią termokurczliwą, a wózki automatyczne nie obsługują palet z towarami zabezpieczonymi w ten sposób, ponieważ w świetle otworów w palecie jest folia. O to się rozbiliśmy. Póki nie zmienimy, jako organizacja, sposobu zabezpieczania palet, ta automatyzacja będzie trudna, a wręcz niemożliwa. A trudno jest zastąpić obecny sposób zabezpieczania streczowaniem, podczas którego nasze produkty przemieszczają się.
Grupa Geberit posiada automatyczne centrum dystrybucji w Pfullendorfie, w Niemczech – mamy więc skąd czerpać wzorce. Wprowadzamy automatyzację i roboty na produkcji, ale na zaawansowaną automatykę w centrach dystrybucji jeszcze poczekamy. Bez rozbudowy infrastruktury nie da się tego zrobić.
Pozostaje usprawnianie fragmentów procesów…
Tak, oczywiście. To nie jest tak, że wszystkie procesy zautomatyzujemy. Ale z drugiej strony rozwój technologii następuje tak szybko… Teraz staramy się automatyzować fragmenty procesów, szukamy drobnych usprawnień. W oparciu o doświadczenie i informacje uzyskane od naszych pracowników w wyniku obserwacji procesu, jego analizy. Zautomatyzowaliśmy na przykład ręczne księgowanie i potwierdzanie operacji. Zastanawiamy się też między innymi nad wdrożeniem technologii RFID dla operacji wewnątrz grupy.
Dziękuję za rozmowę.