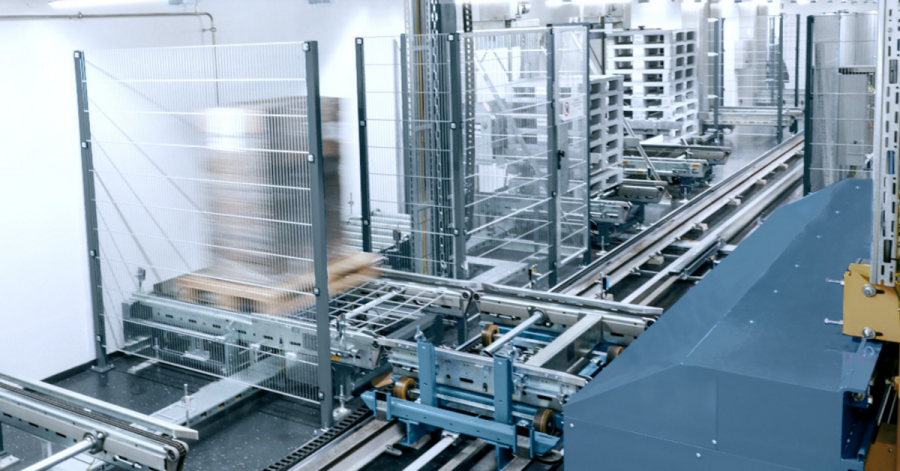
Wyzwania logistyki farmaceutycznej
Automatyzacja: czynniki krytyczne
W logistyce farmaceutycznej procesy takie jak projektowanie, rozbudowa i modernizacja zautomatyzowanych magazynów wymagają gruntownej znajomości wymogów branży. Zawarte są one w zbiorach reguł np. GMP, GDP lub GAMP 5 w których zdefiniowano techniczne procedury odbiorów oraz przepisy sanitarne, klimatyzacyjne i termiczne. Podczas wybierania odpowiednich dostawców sprzętu i oprogramowania ważne jest, aby nie tylko bazować na samych współczynnikach wydajności, ale również posiadać możliwie kompleksową wiedzę na temat wszystkich modułów wydajności.
W przemyśle farmaceutycznym kontrola jakości odgrywa kluczową rolę, ponieważ każdy błąd ma bezpośredni wpływ na zdrowie konsumentów. Producenci leków muszą gwarantować przestrzeganie wytycznych nie tylko we własnej produkcji, lecz również wzdłuż całego łańcucha dostaw. Filarem tej gwarancji są przewodniki GMP, GDP oraz GAMP 5. Ten ostatni dotyczy przede wszystkim systemów zautomatyzowanych i uznawany jest za standardowy pakiet walidacyjny dla systemów komputerowych w przemyśle farmaceutycznym. GMP oznacza „Good Manufacturing Practice” i został powołany do życia analogicznie do GDP (Good Distribution Practice).
Higiena: czyste i gładkie powierzchnie
W przemyśle farmaceutycznym produkcja często odbywa się w standardzie pomieszczeń czystych, co wpływa także na logistykę przed i poprodukcyjną. Pomieszczenie czyste to takie miejsce pracy, w którym obowiązują wyjątkowo wysokie wymagania dotyczące otoczenia i pracowników. W pomieszczeniu czystym powietrze powinno zawierać jak najmniej cząstek, co pozwala uniknąć zanieczyszczeń i szkód produkcyjnych. Palety, które są transportowane przez automatyczne systemy przenośnikowe z obszaru przyjęcia towaru lub wysokiego regału do produkcji, docierają do obszarów krytycznych przez śluzy podciśnieniowe. Cząsteczki kurzu usuwa się tam za pomocą urządzeń odciągowych, co minimalizuje ryzyko zanieczyszczenia.
Przykład: w serbskim centrum dystrybucyjnym PharmaSwiss w Belgradzie pomieszczenia czyste zostały w sposób bezpieczny i czysty oddzielone od tzw. obszarów szarych i czarnych (potencjalnie zanieczyszczonych) za pomocą zintegrowanych bram szybkobieżnych. Nośniki ładunku w obszarze dostawy są całkowicie automatycznie wymieniane na bezpieczne pod względem higienicznym palety z tworzywa sztucznego. W pełni zautomatyzowany magazyn wysokiego składowania został wykonany przez firmę Kardex Mlog. Na najmniejszej możliwej powierzchni zabudowy o wysokości 24 metrów oferuje on miejsce na 4840 palet.
Kliknij tutaj by dowiedzieć się więcej na temat projektu PharmaSwiss
Wysoką wydajność można również osiągnąć dzięki magazynom czystym, które są umiejscawiane pomiędzy magazynem wysokiego składowania a produkcją. Firma Boehringer Ingelheim microParts GmbH zrealizowała taką koncepcję na potrzeby produkcji nebulizatorów do leków w warunkach pomieszczeń czystych. Dwunawowy magazyn wysokiego składowania z 1800 miejscami składowania uzupełniono tutaj o magazyn czysty w postaci systemu z belką podnoszącą o nazwie Kardex MTower. W systemie Kardex MTower załadunek i wyładunek jednostek odbywają się za pomocą pionowo przesuwanej belki podnoszącej, na której poziomo porusza się wózek transferowy. Jednostka ładunkowa jest obsługiwana za pomocą zamontowanych na wózku transferowym wideł teleskopowych. Do budowy użyto wyłącznie materiałów niezawierających silikonu oraz stali szlachetnej.
Kliknij by poznać więcej szczegółów na temat magazynu Boehringer
Już na etapie planowania należy zadbać o to, aby technologia przenośników i regałów była łatwa do czyszczenia. Profile o gładkich i ukosowanych powierzchniach, z jak najmniejszą liczbą otworów, od samego początku zapewniają brak gromadzenia się brudu.
Temperatura: mapowanie we wszystkich strefach
Wrażliwe surowce i produkty farmaceutyczne wymagają często specjalnych warunków klimatycznych. W zależności od etapu produkcji i rodzaju wyrobu, w magazynie wysokiego składowania tworzone są różne strefy temperaturowe.
Na mniejszą skalę sprawdzają się tu również pionowe systemy podnoszenia, takie jak te zastosowane przez Merck KGaA w budynku badawczym w zakładzie w Darmstadt. Kompaktowe systemy podnośnikowe są tam wykorzystywane do udostępniania, przygotowywania i przechowywania substancji farmaceutycznych przeznaczonych do badań oraz do zarządzania nimi. Ze względu na szczególne wymagania, jakie substancje badawcze stawiają warunkom składowania, należało m.in. stworzyć chłodnię i mroźnię składową. Pracownicy laboratorium musieli mieć przy tym dostęp do magazynów chłodniczych z obszaru o temperaturze pokojowej. Rozwiązanie firmy Kardex bazuje na trzech urządzeniach standardowych typu Kardex Shuttle, które zostały zamknięte w izolowanych komorach. Dzięki temu operatorzy mają dostęp do klimatyzowanych magazynów bezpośrednio z obszaru laboratorium, w którym panuje temperatura pokojowa.
Zarządzanie klimatyzacją od samego początku
We wszystkich magazynach farmaceutycznych obowiązuje zasada, że wahania temperatury nie mogą przekraczać określonych limitów. Magazyn o kubaturze 125 m³ można łatwiej utrzymać w stałej temperaturze niż magazyn o objętości kilku tysięcy metrów sześciennych. Ponadto istotną rolę odgrywa poziom zapełnienia magazynu. Ze względu na różne przepływy powietrza mocno załadowany magazyn będzie miał inny profil temperaturowy niż magazyn niemal pusty. Na cyrkulację powietrza wpływa również rozmieszczenie regałów, ścianek działowych, półek i palet. Kolejnym czynnikiem jest rozmieszczenie towaru w obiekcie.
Również pora roku ma oczywiście wpływ na panujące w magazynie temperatury. Należy ponadto uwzględnić otwory konstrukcyjne: bramy na rampach przeładunkowych, drzwi i okna mogą w krótkim czasie zmienić warunki termiczne. To samo dotyczy świetlików w postaci przeszkleń wielkopowierzchniowych i szklanych kopuł. Systemy ogrzewania, wentylacji i klimatyzacji również zmieniają temperaturę – należy je więc koniecznie uwzględnić.
Kwalifikacja sprzętu i oprogramowania
GMP reguluje jednak nie tylko bieżące procesy w produkcji i logistyce, lecz również projektowanie i odbiór nowych systemów. Zadania te obejmują sporządzanie wykazów wymagań i specyfikacji, jak również kwalifikację sprzętu i oprogramowania. Na szczególną uwagę zasługuje tu „Factory Acceptance Test” – w skrócie FAT – test akceptacyjny wymagany w przemyśle farmaceutycznym. Podczas tego wstępnego odbioru klient ogląda elementy instalacji w zakładzie producenta i dokonuje odbioru przynależnej dokumentacji. Identycznie jak w przypadku późniejszego „Site Acceptance Test” (SAT) w miejscu użytkowania, system musi działać również na tym wczesnym etapie.
Spełnienie tego warunku jest utrudnione, gdy sprzęt i oprogramowanie pochodzą od różnych dostawców. W takiej sytuacji przeprowadzenie pełnych testów funkcjonalnych w ramach FAT jest prawie niemożliwe, ponieważ nie można zmontować wszystkich wymaganych komponentów. Z reguły dokonuje się tego dopiero podczas SAT.
Ponadto w celu dokonania wstępnego odbioru klient musi odwiedzić kilku różnych producentów, co jest bardzo czasochłonne i kosztowne. Dlatego też przy wyborze dostawców należy się skupić na takich firmach, które oferują kompletny pakiet usług: od konstrukcji, przez budowę układnic, aż po realizację oprogramowania – wszystko od jednego usługodawcy. Ponadto należy nalegać, by dla danej fazy projektu została powołana centralna osoba kontaktowa, która będzie odpowiedzialna za ogólne kierowanie projektem i koordynowanie go przez cały czas trwania przedsięwzięcia.
Wreszcie przy wyborze odpowiedniego dostawcy należy również uwzględnić dodatkowe usługi, takie jak kalibracja czujników i szkolenie użytkowników. To samo dotyczy stworzenia systemu ewaluacji, który umożliwi przetestowanie wszystkich interfejsów pomiędzy układami sterowania maszynami, systemem zarządzania magazynem i systemem zarządzania towarami lub planowania produkcji.
Wybór dostawców: Na co zwrócić uwagę
Podsumowując: Podczas planowania zautomatyzowanych magazynów dla logistyki farmaceutycznej należy wziąć pod uwagę przede wszystkim trzy czynniki krytyczne. Po pierwsze, obiekt powinien nie tylko umożliwiać przestrzeganie surowych przepisów higienicznych, lecz również ułatwiać je poprzez stosowanie odpowiednich materiałów, prześwitów i powierzchni. W drugiej kolejności należy się skupić na ciągłym zarządzaniu temperaturą oraz skutecznym monitorowaniu różnych stref składowania. Przy wyborze dostawców należy zaś zwrócić uwagę na to, aby wszystkie komponenty pochodziły od jednej firmy.