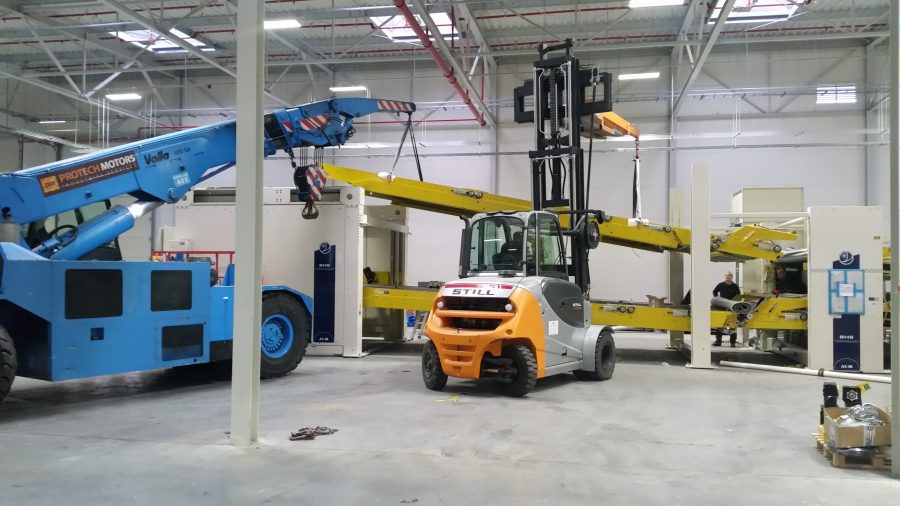
Zarządzanie relokacją zakładu produkcyjnego
Z Robertem Samczykiem, prezesem spółki Protech Motors, rozmawiamy o tym, jak należy przygotować się do procesu relokacji produkcji oraz jakie problemy mogą się pojawić podczas takiej przeprowadzki.
Czy migracje zakładów produkcyjnych są tak powszechne jak miało to miejsce jeszcze w pierwszych latach XXI wieku?
Rzeczywiście to były lata kiedy relokacje były chlebem powszednim wielu firm.
Tania siła robocza szczególnie w krajach
azjatyckich, niższe wymagania dotyczące ochrony środowiska, tańsza energia – to
wszystko powodowało zwrot w kierunku Chin, Tajwanu czy Kambodży. Dziś podobnie
toczy się walka o redukcję kosztów wytwórczych, ale pole bitwy toczy się często
w Europie. Producenci stawiają na wykwalifikowanych pracowników, stabilną
sytuację polityczną, transparentność produkcji – bo wiele firm różnych branż
prowadzi szeroko zakrojone działania CSR oparte na ochronie środowiska i
zrównoważonej produkcji.
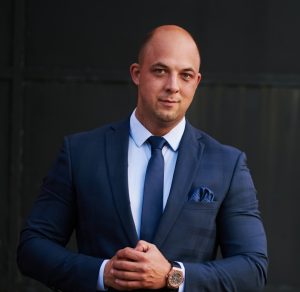
To gdzie szuka
się oszczędności?
Wiele krajów czy regionów stara się przyciągnąć przemysł tworząc preferencyjne
warunki do prowadzenia biznesu: są to min. ulgi podatkowe, bogata infrastruktura,
z której mogą korzystać nowe zakłady czy chłonność danego rynku – czyli szybsza
spedycja towarów dzięki doskonałemu zapleczu logistycznemu. Ale wszystko zawsze
jest dobrze skalkulowane pod rozwój firmy. Rachunek ekonomiczny, na który
składa się szereg czynników wskazujących na opłacalność produkcji w jednym czy
drugim miejscu najczęściej decyduje o przeniesieniu zakładu produkcyjnego z
dotychczasowego adresu.
Jak wygląda logistyka związana z relokacją, czy wszystkie zakłady przenosi się tak samo?
Oczywiste różnice wynikają z branży w jakiej funkcjonuje dany producent. Zakład chemiczny będzie różnił się od wytwórcy silników samolotowych, a ten od producenta makaronu. Planowanie przeprowadzki w dużej mierze zależy od produktu finalnego lub materiału, z jakiego powstaje. W swoim parku maszynowym fabryka może posiadać mniejsze lub większe maszyny, pojedyncze urządzenia lub też linie produkcyjne. Te z kolei mogą być manualne lub zautomatyzowane. Zakład może w swoim procesie produkcyjnym korzystać z maszyn wtryskowych jeśli produkt jest np. plastikowy, z maszyn obróbczych CNC lub pras jeśli produkt jest metalowy itd. Mimo tych różnic wiele jest podobieństw logistycznych przy każdej relokacji. Każda relokacja, którą miałem możliwość zarządzać prowadzona była na żywym organizmie – na pracującym zakładzie. Żaden producent przecież nie pozwoli sobie na nawet najmniejszą przerwę w produkcji. A biorąc pod uwagę wielkość fabryki lub ilość urządzeń czy też linii produkcyjnych w parku maszynowym, takie przeniesienie może trwać nawet rok lub dłużej.
Co z kwestią bezpieczeństwa pracowników?
Dla nas – firmy wchodzącej do obcego zakładu zagadnienie bezpieczeństwa jest priorytetem. Planujemy pracę naszej załogi oraz pracowników klienta tak, aby wyeliminować każde zagrożenie wynikające z naszych działań. Dlatego zanim przystąpimy do realizacji, przygotowujemy wraz z klientem harmonogram, który jasno i szczegółowo określa które maszyny, w jakiej kolejności oraz w jakim czasie będą przenoszone. Im bardziej dokładny plan, tym sprawniejsze wykonanie usługi co za tym idzie jest bezpieczniejsze i zajmuje ono mniej czasu.
A jak wygląda samo
przenoszenie pracującego zakładu?
Przed
rozpoczęciem prac sprawdzamy poprawność działania maszyny czy też linii produkcyjnej,
weryfikujemy geometrię urządzeń jeśli jest wymagana, sprawdzamy cykle
produkcyjne itd. Następnie automatyk ściąga kopię zapasową programu. Kolejnym
krokiem jest odłączenie napięcia, a następnie mediów od maszyn (instalacji
elektrycznej, hydraulicznej, sprężonego powietrza i dodatkowych jeśli są np. podającej
surowiec jak np. w przypadku maszyn wtryskowych).
Później następuje demontaż na linii produkcyjnej. Na tym etapie bardzo ważne jest dokładne oznaczenie kabli i elementów maszyn co pozwoli uniknąć pomyłek oraz zaoszczędzi sporo czasu podczas montażu. Następnym etapem jest wyprowadzenie maszyn lub elementów linii z hali załadunek na samochody i transport do nowej lokalizacji gdzie następuje analogicznie ich rozładunek, wprowadzenie na hale i posadzenie urządzeń zgodnie z planem usytuowania przekazanym wcześniej przez klienta. Zazwyczaj jest tak, że w przypadku linii produkcyjnych relokujemy kolejno pojedynczo linię po linii. Natomiast jeżeli chodzi o maszyny to w zależności od ich gabarytów oraz planów produkcyjnych klienta możemy przenosić po kilka urządzeń.
Relokacje takie wymagają transportu ponadnormatywnego, którego logistyka nie jest prosta.
Oczywiście, jeśli maszyny lub elementy linii produkcyjnej wymagają ze względu na swój rozmiar lub wagę transportu ponadnormatywnego jesteśmy zobowiązani do wystąpienia wcześniej o stosowne zezwolenia do Generalnej Dyrekcji Dróg Krajowych i Autostrad. Taki konwój też odbywa się na określonych zasadach – prowadzony przez pilota, jedzie trasą oraz w terminie wyznaczonym w zezwoleniu przez powyższy organ administracji państwowej.
Czy widać różnice w wymaganiach odnośnie relokacji w zależności od kraju pochodzenia danej firmy?
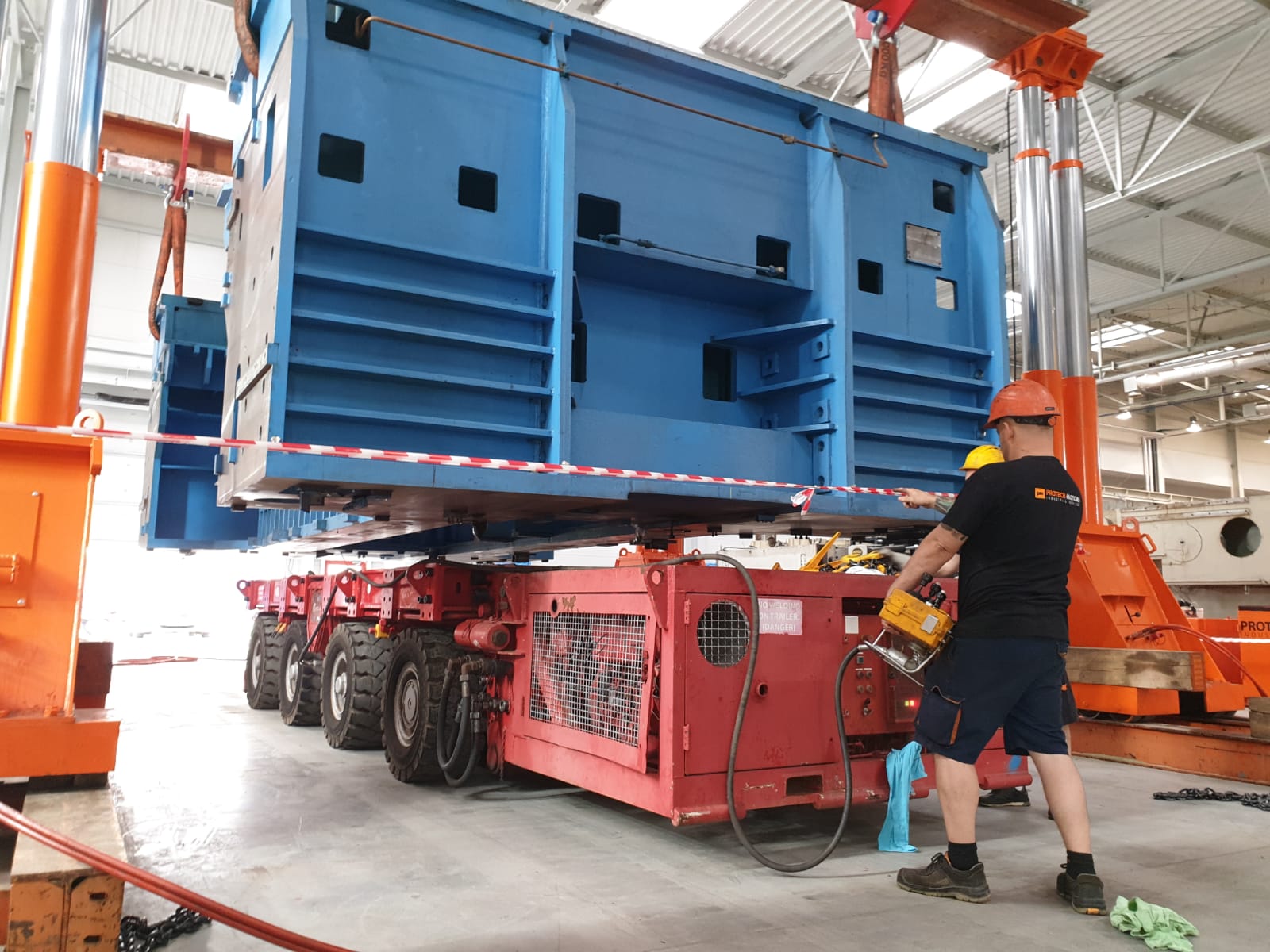
Niekoniecznie w samych wymaganiach, tu wyróżniają się właściwie zakłady produkcyjne pochodzenia francuskiego, mają nieco bardziej zaostrzone przepisy BHP poza tym nie widać wielkich różnic. Co innego jeśli chodzi o organizację pracy czy też trzymanie się wcześniej wspólnie ustalonego harmonogramu. Tu już widać znaczące różnice biorąc po uwagę kraj pochodzenia danego zakładu. Jeśli np. przenosimy maszyny za granicę, ważna jest również znajomość prawa pracy oraz prawa dotyczącego transportu zwłaszcza ponadgabarytowego, ponieważ te także są mniej lub bardziej zróżnicowane w zależności od swojego miejsca na mapie Europy czy też świata.
Jakie czynniki wpływają na podjęcie przez inwestora takiej inwestycji?
Słychać było sygnały, że Polska jako kraj Unii Europejskiej stał się stosunkowo drogi jeżeli chodzi o siłę roboczą, podatki itd. W związku z czym zaczęto zastanawiać się na przeniesieniem części produkcji lub nowe inwestycje na wschodzie Europy. Aczkolwiek obserwując co dzieje się w polskim i europejskim przemyśle nie do końca można potwierdzić tą informacje, ponieważ spora część produkcji jest relokowana właśnie do nas z takich krajów jak Francja, Niemcy, Hiszpania, Belgia czy Włochy. Część tych relokacji jest związana z przeniesieniem całej produkcji danego zakładu ze względu na koszty, inna z jej częścią np. ze względu na lepszy przepływ produkcji lub logistykę czy późniejszą dystrybucję, kolejne z konsolidacją zakładów lub rozwojem produkcji w danym zakładzie i zostaje przygotowywane miejsce pod nowe maszyny lub linie produkcyjne.
Jakie są największe trudności przy przenoszeniu zagranicę zakładu produkcyjnego? Czy są to czynniki techniczne, prawne?
Czasem czynniki prawne są dla nas pewnym ograniczeniem, co najczęściej nieco wydłuża naszą pracę, ale nie jest nam to straszne, ponieważ tak czy inaczej wykonujemy pracę zdecydowanie szybciej od naszych zagranicznych konkurentów. Jako firmie zagranicznej również ciężej jest nam uzyskać pozwolenia na transporty ponadnormatywne o bardzo dużych ciężarach i to zazwyczaj trwa nieco dłużej. Większym utrudnieniem bywa dostępność materiałów potrzebnych do relokacji lub np. części zamiennych podczas awarii. Często, żeby zaoszczędzić czas i/lub pieniądze kupujemy je w Polsce i stąd transportujemy do klienta.
Rozmawiała Ewelina Szymeczko