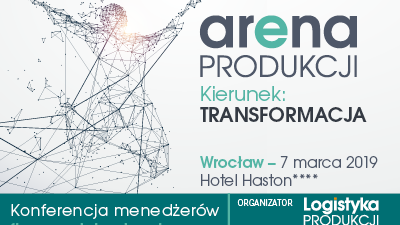
Wszystkie odcienie transformacji
Kierunek:Transformacja – takie hasło przyświecało szóstej edycji konferencji Arena Produkcji. Szerokie grono menedżerów i specjalistów, którzy skorzystali z zaproszenia na wydarzenie, nie mogło być zawiedzione wizytą w Wrocławiu. 11 wystąpień praktyków i ekspertów, inspirujący warsztat oraz tętniąca życiem strefa networkingu pozwoliły wszystkim znaleźć coś dla siebie.
Program wydarzenia zakładał poszukiwanie odpowiedzi na pytania o to, jak zmieniają się firmy produkcyjne, w którym obszarze warto dokonać transformacji i jakie korzyści można odnieść, wkraczając na ścieżkę zmiany. W trakcie konferencji rozmawialiśmy o transformacji organizacyjnej, procesowej jak i technologicznej, Jak zwykle okazało się, że te trzy obszary przenikają się i nie można mówić o zmianie jednego z nich w oderwaniu od całego ekosystemu firmy produkcyjnej.
Doskonałość w Getinge
Konferencję rozpoczęło obszerne i pełne inspiracji wystąpienia Macieja Koca. Dyrektor produkcji w Getinge IC Production Poland mówił o tym, jak zakład w podpoznańskich Plewiskach wdrożył program Manufacturing Excellence. Firma Getinge działa w obszarze produkcji sprzętu dla placówek medycznych, zaś zakład w Plewiskach, funkcjonujący od 2014 roku należy do dywizji „Surgical Workflows” i specjalizuje się w produkcji sterylizatorów. W obiekcie o powierzchni 7.7 tys.m.kw. pracuje 166 osób, prócz produkcji w Plewiskach znajduje się m.in. komórka odpowiadająca za globalną obsługę zgłoszeń reklamacyjnych.
Program Manufacturing Excellence został zapoczątkowany w III kwartale 2017 roku i objął 10 fabryk Getinge. Projekt zakładał rozpoczęcie wdrożenia od 1 linii pilotażowej w każdym zakładzie, realizację kwartalnych szkoleń i powołanie stanowiska Lean Champion, zaś za jego realizację wspólnie odpowiadali dyrektorzy fabryki i produkcji w zakładzie. Cele programu są bardzo ambitne – do 2020 roku zakładane jest m.in zmniejszenie ilości reklamacji o 40 proc., zredukowanie czasów dostawy o 30 proc, wzrost produktywności o 20 proc., czy redukcja zapasów w fabrykach o 40 proc.
Realizację programu podzielono na dwa obszary – proces i ludzie. Wdrożenie rozpoczęło się od sięgnięcia po najpowszechniej wykorzystywane narzędzie lean management: mapowanie strumienia wartości. Po zbadaniu stanu obecnego uznano, że istnieje wyraźny potencjał do skrócenia lead time. Usprawnienie procesów miało też zapewnić wprowadzenie kontrolowanych buforów, dużym krokiem w przód okazało się wyeliminowanie nadmiernej biurokracji, np. w kwestii ilości podpisów w dokumentacji ISO. Za jeden z większych sukcesów w obszarze usprawniania procesów należy uznać nowy model planowania i realizacji produkcji i zgranie czasu taktu z pracą szwedzkich dostawców.
W obszarze pracowniczym ważnym krokiem było z kolei stworzenie nowego modelu struktury organizacyjnej, obejmującej poziomy pracownicy i brygadziści, brygadziści i kierownicy oraz kierownicy i dyrektorzy. Realizacja spotkań z podziałem na te poziomy znacząco skróciła ich czas, jak też usprawniła komunikację. Rotacja pracowników między stanowiskami okazała się doskonałym sposobem na zwiększenie ich zaangażowania i odpowiedzialności. Co oczywiste, w ramach projektu realizowany jest też program zgłaszania sugestii pracowniczych.
W ramach podsumowania prelegent pokazał, jak zmieniły się podstawowe wskaźniki od momentu wdrożenia programu. Najlepszym dowodem uznania jest jednak fakt, iż fabryka w Plewiskach wygrała wewnętrzny plebiscyt Getinge na najlepszy zakład dywizji w 2018 roku.
Projektowanie przyszłości
Działy projektowania i produkcji często funkcjonują w firmach produkcyjnych w dość mocnej izolacji, co w oczywisty sposób przekłada się na płynność funkcjonowania przedsiębiorstwa. Nowe technologie pozwalają jednak przełamać tę barierę, zbliżając i tworząc synergię między projektowaniem a produkcją. Na Arenie Produkcji mówił o tym Przemysław Sokołowski, Technical Specialist w firmie Autodesk Polska.
Pan Przemysław postanowił przestawić koncepcję Generative Design, która została wykorzystania w najnowszych rozwiązaniach Autodesku – potentata w branży oprogramowania wspierającego procesy projektowania. Pan Przemysław zwrócił uwagę na to, że pojawianie się coraz bardziej innowacyjnych produktów, wzrost produktywności i zmiany w samych procesach produkcyjnych wymuszają zupełne inne podejście do przygotowywania nowych produktów.
Autodesk Generative Design to technologia eksplorowania projektu. Równocześnie generuje ona wiele rozwiązań CAD uwzględniających rzeczywiste ograniczenia technologiczne i narzucone kryteria optymalizacyjne. Na podstawie zadanych wytycznych, program generuje wiele sprawdzonych wariantów produktu, zgodnych z procesem produkcji. W ten sposób projektant otrzymuje kilka praktycznych rozwiązań danego problemu projektowego i może wybrać to, które będzie najkorzystniejsze z punktu widzenia inżynieryjnego, finansowego jak i organizacyjnego.
Pan Przemysław zaprezentował kilka praktycznych przykładów tworzenia i wyboru optymalnych projektów. Genrative Design wykorzystuje m.in. General Motors, dzięki technologii druku 3D tworząc prostsze i bardziej wytrzymałe detale. Z kolei w firmie Claudius Peters Genrative Design pozwolił znaleźć kompromis między idealnymi projektami, których ze względu na gabaryty nie można wykonać metodą druku 3D, a możliwościami tradycyjnych technologii.
Intralogistyka bez barier
Michał Rosenstrauch reprezentujący firmę SSI SCHÄFER zaprezentował gościom Areny Produkcji przykłady zastosowań zaawansowanych rozwiązań intralogistycznych, wspierających działalność fabryk i magazynów. Prócz prelekcji, duże zainteresowanie wzbudziła ekspozycja firmy, na której można było bliżej przyjrzeć się systemowi WEASEL.
SSI SCHÄFER dostarcza wszystkie rozwiązania z jednego, najlepszego źródła – własnych fabryk. Szeroka paleta obejmuje zróżnicowane produkty – od systemów transportu do systemów sterowania, rozwiązań programistycznych i systemów przenośnikowych. Największe zainteresowanie zakładów produkcyjnych budzi aktualnie właśnie system WEASEL, oparty na pojazdach AGV.
Nie wymaga on żadnych wygrodzeń czy barier, może pracować na ograniczonej przestrzeni, zapewniając ciągłość dróg transportowych. WAESEL zapewnia transport towarów umożliwiając sekwencjonowanie, konsolidację i zmiany strumieni przepływów z różnych stref magazynowania i produkcji. Daje też możliwość dopasowywania obsługi do potrzeb dnia i zapewnienia koniecznej wydajności. Akumulatory wózków WEASEL wystarczą na cały dzień pracy, pojazd jest też w stanie powrócić samodzielnie do stacji ładowania.
Pan Michał omówił także możliwości automatycznych systemów składowania części i potencjał ich wykorzystywania w utrzymaniu ruchu. Wśród mniej powszechnych zalet regałów windowych wskazać można autoryzację dostępu – a zatem pobranie przez pracownika bardzo drogiego narzędzia pod koniec zmiany może dać podstawy do zbadania potencjalnych nieprawidłowości.
Planowanie w duchu Przemysłu 4.0
Marek Jackowski z firmy ORSOFT GmbH szukał w swojej prelekcji odpowiedzi na pytanie jak „Jak stworzyć wydajne i konkurencyjne przedsiębiorstwo wpisujące się w koncepcję Industry 4.0?” Pomogło mu w tym studia przypadku, prezentujące sposoby w jaki producenci rozwiązują problemy biznesowe, wspierając się nowoczesnymi technologiami. ORSOFT GmbH grało w tych projektach znaczącą rolę, gdyż firma nie ogranicza się do statusu dostawcy IT, ale też skupia się na rozwoju swoich usług konsultingowych.
Pierwszy case dotyczył globalnej firmy, produkującej specjalistyczne dodatki do produktów branży FMCG. Miał on na celu przede wszystkim usprawnienie procesów planowania sprzedaży i operacji, z możliwością tworzenia prognoz statystycznych i planowania na bazie tygodniowej. Idealnym rozwiązanie tego problemu jest metodologia Sales&Operational Planning, zaś zaprojektowane cykle planowania zostały wpisane w architekturę działającego w firmie systemu SAP, ze wsparciem rozszerzenia ORSOFT EWB.
Drugie studium przypadku dotyczyło firmy Lisner, która postawiła sobie za zadanie maksymalizację poziomu satysfakcji klienta przy ciągle zmieniającym się zapotrzebowaniu rynku na produkty. Plany produkcyjne miały być dopasowane do ogólnego zapotrzebowania sprzedaży oraz zapotrzebowań lokalnych, kolejnym zadaniem było udoskonalenie zleceń planowanych. W tym przypadku kluczem okazało się lepsze wykorzystywanie dostępnego personelu. Stworzony został scentralizowany model planowania, uwzględniający specyfikę produkcji i sprzedaży zakładu, kierownictwo otrzymuje ponadto wizualizację obciążeń na zmianach produkcyjnych w dłuższym horyzoncie czasowym (tygodnie, miesiące), a analiza wykorzystania personelu dostarcza dane źródłowe do prognozowania potrzeb pracowniczych ze strony agencji pracy tymczasowej.
W końcowej części wystąpienia pan Marek omówił działanie systemu ORSOFT Manufacturing Workbench w obszarze planowania i harmonogramowania produkcji, oraz zalety wynikające w integracji rozwiązań ORSOFT z systemem SAP.
Przepływ i jego transformacja
Dawid Majchrzak, Project Manager w firmie Hilding Anders Polska postanowił zastanowić się nad ideą transformacji przedsiębiorstwa produkcyjnego, za punkt wyjścia przyjmując rolę przepływu w fabrykach. Pan Dawid za pomocą trzech przykładów ze swojej firmy pokazał, jak można dokonać skutecznej transformacji przedsiębiorstwa, odnosząc przy tym mierzalne korzyści biznesowe.
Hilding Anders to działający od 1939 roku producent materacy, sprzedający swoje produkty w 40 krajach świata i posiadający w portfolio 26 marek. Wyroby firmy dostępne są w niemal wszystkich dużych sklepach oferujących wyposażenie wnętrz, zarówno jako marki własne jak i prywatne. Polski zakład działa w Murowanej Goślinie, zajmuje powierzchnię 126 tys. m.kw. (z tego 46 tys. pod dachem) i zatrudnia ponad 800 osób.
Pan Dawid rozpoczął prelekcję od zastanowienia się nad ideą przepływu w przedsiębiorstwach produkcyjnych oraz pokazał, jak modyfikacja wielkości partii produkcyjnej wpływa na lead time, jakość wyrobu i koszty. Następnie przeszedł do omówienia trzech transformacji, jakimi zajmował się w obszarze wydziału, jednostki oraz łańcucha dostaw w swojej firmie,
Pierwsze studium przypadku dotyczyło skrócenia lead time na wydziale produkcji materacy w Murowanej Goślinie. Choć prelegent przyznał, że ceni filozofię Kaizen i ciągłe doskonalenie, w tym przypadku sięgnięto po gruntowną reorganizację, znaną w Lean Manufacturing jako Kaikaku. Podczas projektowania nowego layoutu i procesów szczególny nacisk położono na definicję i organizację wąskich gardeł. Bardzo przydatne okazało się też oprogramowanie, pozwalające symulować nową organizację fabryki. Zastosowanie daleko idącej automatyzacji i systemów RFID, poprawa ergonomii i przede wszystkim poprawiony przepływ spowodowały, że wyniki projektu znacząco przekroczyły założenia – produkcja w toku spadła z 18 do 8 godzin, czas realizacji zlecenia produkcyjnego wynosił między 2 a 6 godzin (zakładano 8), a moce produkcyjne wzrosły o 33 proc przy identycznym spadku ilości roboczogodzin niezbędnych do produkcji wyrobów.
Drugi projekt był konsekwencją pierwszego. Po udanej reorganizacji działu przyszedł czas na przebudowę layotu całej fabryki. Analiza przepływu materiałów w zakładzie wykazała, że ze względu na niezbyt fortunną lokalizację poszczególnych centrów produkcyjnych drogi transportowe są wydłużone, a potoki transportowe nakładają się na siebie. Niepokojące było też duże ryzyko wypadków ze względu na nasilony ruch wózków widłowych w pobliżu obszarów produkcyjnych. Re-inżyniering lay-outu całej firmy obejmował stworzenie dwóch centrów produkcyjnych w miejsce czterech, przebudowę magazynów, stworzenie nowej głównej drogi transportowej i dalszą automatyzację. Po raz kolejne cele projektu zostały zrealizowane z nawiązką, zaś dodatkową niemierzalną wartością były korzyści w obszarze BHP.
Trzecie case study dotyczyło budowy nowego zakładu w Chinach, dedykowanego dostawom dla IKEI. W 2030 roku Chiny będą dla IKEI największym azjatyckim rynkiem, stąd też niezbędne są inwestycje w tym obszarze. Podstawową kwestią był geograficzny dobór lokalizacji fabryki, z uwzględnieniem umiejscowienia sklepów i czasu transportu morskiego. Sam obiekt jako inwestycja typu greenfield dawał duże możliwości aranżacji zakładu. Wybrane zostały 2 layouty, a następnie dokonane zostało porównanie ich funkcjonalności z punktu widzenia przepływu materiałów. Pan Dawid zaprezentował finalną wersję projektu i poszczególne etapy budowy.
Fabryki od krawca
Temat inwestycji w nowe fabryki płynnie kontynuowali Krzysztof Czekalski i Maciej Zawada z firmy Panattoni Europe. Panattoni Europe specjalizuje się w szytych na miarę inwestycjach build-to-suit (BTS) – budowanych na zamówienie indywidualnego klienta. O nich właśnie postanowili pomówić prelegenci, skupiając się na najciekawszych realizacjach realizowanych w ostatnich latach.
Dopasowanie obiektów BTS do potrzeb producenta zaczyna się od kwestii lokalizacji – zakład może być zbudowany na działce należącej do dewelopera lub klienta. Na wstępie tworzony jest też zamysł funkcjonalny, a następnie dobierane są odpowiednie rozwiązania przestrzeni przemysłowej. Dodatkowe elementy wskazywane przez klienta to wielkość powierzchni biurowej – deweloper dba o to, aby spełnione zostały wytyczne dotyczące minimalnej powierzchni nałożonej przepisami zdrowia i bezpieczeństwa, w zależności od liczby pracowników – oraz ilość miejsc parkingowych. Panattoni oferuje możliwość wynajęcia długoterminowego budynku, jak też zbudowanie go dla klienta.
Wśród przykładów realizacji BTS z ostatnich lat zaprezentowane zostały zakłada K-Flex w Wieleninie-Kolonii, Pilkington w Sandomierzu, Ideal Automotive w Świdnicy i Ontex w Radomsku. Szczególnie interesujący był proces współpracy z Pilkington. Producent szkła trzykrotnie rozbudowywał swój zakład razem z Panattoni, każdorazowo sięgając po inną formę współpracy – pierwszą halę wynajęto, druga powstawała w ramach przetargu publicznego, a trzecie była już realizacją na zamówienie z zamiarem kupna.
Pracownik przy kiosku
Samoobsługa pracownicza w ramach kiosku to zabawka czy sposób na zwiększenie efektywności pracowników? Na takie pytanie szukał odpowiedzi Michał Żelichowski, członek zarządu EQ System. Firma, która z roli dostawcy IT ewoluowała w stronę przedsiębiorstwa konsultingowego, wskazującego, jak i gdzie wprowadzać zmiany, żeby miały rzeczywisty wpływ na funkcjonowanie całej firmy, a nie tylko wybranego jej fragmentu, zdaje sobie sprawę, że zarządzanie zasobami ludzkimi wyrasta na największy problem producentów i coraz mocniej porusza go w swoich wystąpieniach.
Podczas naszej poprzedniej konferencji, Manufacturing Summit, pan Michał mówił o automatycznym planowaniu obsady, dzięki połączeniu funkcjonalności systemów APS/WMS i XPRIMER.HRM. Zastosowanie kiosków pracowniczych (lub aplikacji mobilnej) to kolejny krok w doskonaleniu stosowania tej idei na hali produkcyjnej. Kioski pozwalają na szybkie składanie wniosków urlopowych, sprawdzenie grafików pracy, składanie wniosków o różne zaświadczenia czy sprawdzenie listy odbytych szkoleń.
Ponadto na pulpicie głównym użytkownika wyświetla się okienko ogłoszeń, w którym działy kadr lub przełożeni mogą publikować ważne wiadomości dotyczące całej załogi lub też określonej grupy odbiorców. Pan Michał zaprezentował przykład działania systemów kiosków w firmie Bahlsen. Po wdrożeniu zauważony został znaczący wzrost komfortu pracy brygadzistów, którzy nie byli już zasypywani papierkową robotą, pozytywne sygnały wysyłali też pracownicy.
Aby odpowiedzieć na pytanie, czy kioski się opłacają, prelegent dokonał szybkiej symulacji ROI. Jak zwrócił uwagę, choć można dyskutować o realnej opłacalności finansowej rozwiązania, to wykorzystanie zaoszczędzonego czasu na poszukiwanie usprawnień procesowych może dać producentowi sporo korzyści w szerszym horyzoncie czasowym.
Pokonać smog
Tomasz Szczepura z firmy Dachser podjął podczas Areny Produkcji tematykę nieco mniej oczywistą dla gości wydarzenia – walkę ze smogiem w miastach. Choć ten problem nie wydaje się bezpośrednio dotykać fabryk, firmy produkcyjne nie mogą zapominać o tym, że funkcjonują w całym łańcuchu dostaw, a ich produkty trafiają często także do centrów największych metropolii.
Na początku pan Tomasz pokazał, jak bardzo w skali europejskiej i globalnej zanieczyszczone są polskie miasta. Poznaliśmy też źródła emisji smogu oraz charakterystykę najbardziej niebezpiecznych dla ludzkiego zdrowia pyłów.
Jak Dachser walczy ze smogiem? Podstawowe działania w tym obszarze są oczywiste, bowiem wiążą się z jak najlepszym wykorzystaniem środków transportu, co obok korzyści ekologicznych poprawia również rachunek ekonomiczny. Operator logistyczny konsoliduje zatem ładunki, stosuje zaawansowane planowanie tras w obszarach miejskich, udziela się w pracach nad przebudową infrastruktury transportowej, kupuje nowoczesne pojazdy, także na paliwa alternatywne i sięga po nowe koncepcje dostaw.
Ten ostatni punkt był niezwykle ciekawy, zwłaszcza w obliczu pojawiających się coraz szerzej prób zamykania dla ruchu pojazdów spalinowych miast. Przykładowo w Amsterdamie Dachser bada możliwości wykorzystywania łodzi kanałowych w połączeniu w rowerami elektrycznymi i małymi samochodami dostawczymi z napędem elektrycznym. W Maladze z dostawami do zamkniętego dla ruchu centrum dojeżdżają małe holowniki o nazwie El Carito. Dachser bada też użyteczność średniotonażowych ciężarówek elektrycznych w zadaniach dystrybucyjnych, zaś na terenie swoich terminali rozważa używanie w operacjach manewrowych elektrycznych ciągników do naczep.
Zmiana podejścia do kosztów
Krzysztof Szymański, wiceprezes zarządu ABC Akademia, mówił podczas Areny Produkcji o pieniądzach. Ten temat zawsze jest aktualny, choć na kwestie finansów można patrzeć z różnych perspektyw. Pan Krzysztof pojął się przedstawienia zasobowo-procesowego rachunku kosztów (ZPRK) oraz tego jak zmienia on podejście do finansów producenta.
Pan Krzysztof na wstępie dokonał porównania tradycyjnego podejścia do kosztów z metodą ZPRK. Międzynarodowa Federacja Księgowych (IFAC) tworząc Model poziomów dojrzałości rachunku kosztów uznała ZPRK za najbardziej zaawansowane rozwiazanie. Przestawienie się na zasobowo – procesowe podejście do rachunku kosztów polecają czołowe organizacje controllingowe i finansowe.
Następnie prelegent pokazał jak w praktyce przejść od rodzajowego do procesowego rachunku kosztów w produkcji. Kluczem jest tu znalezienie odpowiedzi na pytanie jak przyczynowo-skutkowo rozliczyć koszty rodzajowe na procesy. W tym celu tworzone są Centra kosztów zasobów w dziale produkcji. Układ zasobowy kosztów pozwala na poprawne wyodrębnienie kosztów niewykorzystanych zasobów oraz kalkulacje stawek zużycia i wykorzystania zasobów produkcyjnych.
Pan Krzysztof przedstawił działanie systemu Doctor Coster, wspierającego wdrażanie ZPRK. Pokazał też jakie korzyści z wdrożenia nowego podejścia do kosztów odniósł jeden z największych producentów mebli biurowych. Efektami było m.in. uszczegółowienie ewidencji kosztów marketingu; pozyskanie informacji o rentowności klientów, rynków, kolekcji, grup produktowych, a nawet poszczególnych klientów i produktów; czy też skrócenie czasu zamknięcia miesiąca.
Jak korzystamy z druku 3D?
Druk 3D pozostaje technologią, z którą producenci wiążą bardzo duże nadzieje na przyszłość. Karol Kula z firmy 3DGence przyjechał jednak na Arenę Produkcji po to, aby pokazać jak wytwarzanie addytywne jest wykorzystywane przez producentów już dziś. 3DGence, dynamicznie rozwijający się polski producent drukarek 3D, zatrudnia już ponad 90 pracowników i prowadzi operacje na Śląsku.
Pan Karol na wstępie krótko scharakteryzował podstawowe odłamy technologii druku 3D. 3DGence wytwarza drukarki stosujące najpopularniejszą obecnie metodę wytwarzania – warstwowe nakładanie materiału z tworzywa termoplastycznego. O jej popularności decyduje przede wszystkim prostota i niski koszt produkcji – technologie SLS i DMLS, popularnie nazywane metalowym drukiem 3D, dają duże perspektywy na przyszłość, ale zakupu koszt samej drukarki jest aktualnie minimum 10 razy większy.
Jak producenci wykorzystują dziś druk 3D? Badanie przeprowadzone w 2017 roku wskazało, że 22 proc. producentów stosuje już druk 3D w procesie produkcji lub utrzymania ruchu – czyli produkuje tak części zamienne, jak i wszelkiego rodzaju przymiary, uchwyty, elementy okołomontażowe, które pomagają operatorom w pracy na co dzień. 30 proc. badanych traktuje tę technologię przede wszystkim w obszarze opracowywania nowego produktu. Szybko zyskuje też popularność proof on concept, czyli drukowanie małej partii wyrobów i przekazywanie go testów i oceny grupie docelowej. Zaś przykładem stosowania druku 3D w masowej kastomizacji jest oferta MINI – w pojazdach tych można poprosić o wydruk zindywidualizowanych tylnych lamp z dowolnym, krótkim hasłem.
Po raz kolejny prelekcję uzupełniło kilka ciekawych studiów przypadku z naszego podwórka. Firma Geo Globe wykorzystała druk 3D w niezwykle ciekawy sposób – z pomocą 3D Gence wykonywała prototyp tacy transportowej, w celu sprawdzenia poprawności zaprogramowania robotów wykorzystywanych w procesach produkcji. EMTEL, producent sprzętu medycznego, korzystał w wydruków w celu prototypownia produkowanych niskoseryjnie obudów kardiomonitora. Z kolei firma Bocar, produkująca wozy pożarnicze pod zamówienie klientów, szeroko stosuje druk 3D do produkcji haków, uchwytów czy osłon oraz prototypingu.
Wyzwania rynku pracy
Już po raz drugi z rzędu mieliśmy przyjemność gościć na naszej konferencji Tomasza Ślęzaka z Work Service. Dzięki swojej ogromnej wiedzy oraz dużej ilości danych, zbieranych przez Work Service w szeroko zakrojonych badaniach rynku pracy, pan Tomasz mógł szeroko omówić problem braku pracowników w Polsce.
A problem też jest wielowymiarowy, Wynika on nie tylko z mającej ilości osób zdolnych do pracy (na co wpływa demografia, emigracja czy też obniżenie wieku emerytalnego), ale też z luki kompetencyjnej oraz luki infrastrukturalnej – coraz mizerniejsza sieć transportu publicznego utrudnia dojazdy i zmusza pracodawców do organizacji go na własną rękę.
Polska jest dziś na drugim miejscu pod względem najniższej stopy bezrobocia w całej Unii Europejskiej, co jeszcze kilkanaście lat temu wydawało się niewyobrażalne. Jednak bardziej niepokojący jest inny wskaźnik – poziom aktywności zawodowej mamy jeden z najniższych w UE (21 miejsce na 28 krajów). Porównanie z naszymi sąsiadami uwypukla skalę problemu – w Czechach aktywnych zawodowo jest 75 proc. osób zdolnych do pracy, w Polsce tylko 68 proc. Pan Tomasz podkreślił, że te 7 proc. różnicy, choć w teorii nie wydaje się wielką wartością, w praktyce oznacza przepaść.
Najnowsze dane Work Service pokazały, że powoli wysycha najważniejsze źródło ratunku dla rynku pracy, czyli emigracja z Ukrainy. W 2017 wydano ponad 1.71 mln, pozwoleń na pracę dla Ukraińców, w 2018 już tylko 1.44 mln. Jednocześnie podwoiły się ilości pozwoleń wydanych dla obywateli Nepalu, Białorusi, Indii i Mołdawii, lecz nawet sumując te liczby okazuje się, że nowe rynki pozyskiwania pracowników są nadal ułamkiem tego, co zapewnia nam Ukraina.
Jak zatem radzić sobie w tej trudnej sytuacji? Pan Tomasz w podsumowaniu wystąpienia zachęcał do tego, aby zadbać o zadowolenie i chęć pozostania w pracy dotychczasowego personelu, przygotować strategię employer brandingu, nie lekceważyć potęgi „Word of Mouth” oraz traktować rekrutację jako funkcję sprzedaży i marketingu, a nie tylko HR. Przestrzegł też, że relokacja produkcji nie będzie rozwiązaniem problemu, gdyż pracowników brakuje już wszędzie.
Transformacja w sercach pracowników
Owocny dzień zakończył warsztat, poświęcony budowie zaangażowania pracowników i zwiększania ich lojalności wobec firmy. Prowadziła go Sylwia Janas – menedżer HR z kilkunastoletnim doświadczeniem, aktualnie prowadząca działalność doradczą za pośrednictwem firmy Inspire 4 Results.
Pani Sylwia w umiejętny sposób zachęciła uczestników warsztatu do grupowej pracy. Członkowie grupy wspólnie zastawiali się nad tym, jakie aktywności mogą przedsięwziąć, aby wzmocnić zaangażowanie pracowników. Przedyskutowano pod tym względem szereg obszarów, takich jak misja, wizja i wartości firmy, atmosfera pracy, współpraca między zespołami, rozwój osobisty, komunikacja czy sposób przekazywania feedbacku.
Po wewnętrznej pracy w grupach, przestawiane były propozycje działań, które poddano pod uwagi wszystkich obecnych na sali. Wysoki poziom interakcji, duża ilość celnych komentarzy i wzajemne poszukiwanie rozwiązań było bez wątpienia największą wartością, jaką uczestnicy wynieśli z warsztatu.
Podsumowując całe wydarzenie trudno oprzeć się wrażeniu, że Arena Produkcji dojrzewa i sięga do coraz głębiej położnych źródeł produktywności i dobrych praktyk. Mamy nadzieję, że ten dzień był dla wszystkich uczestników konferencji równie inspirujący jak dla nas i nie możemy doczekać się kolejnego spotkania z Państwem.
Galeria zdjęć do artykułu
Pliki do pobrania
zarejestruj się by uzyskać bezpłatny dostęp do materiałów z konferencji. W ten sposób dbamy o polepszanie jakości naszych usług i dostarczanych do Ciebie materiałów. Rejestracja oznacza akceptację aktualnej polityki prywatności.