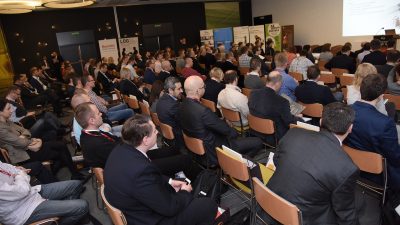
Opadły już emocje po drugiej edycji konferencji Manufacturing Summit. Organizatorzy spotkania, Wydawnictwo Eurologistics i czasopismo Logistyka Produkcji, zadbali o atrakcyjny program, dzięki któremu na liście uczestników znalazło się ponad dwieście pozycji. Z czystym sumieniem możemy stwierdzić, że goście wydarzenia opuszczali je w pełni usatysfakcjonowani.
Bez wątpienia kluczowym tematem konferencji był Przemysł 4.0 – temu zagadnieniu poświęcone było wystąpienie gościa specjalnego, Lucasa Wintjesa z Bosch Rexroth, pojawiało się ono także w innych prezentacjach. Nie brakło jednak także innych ciekawych wystąpień – sporo miejsca poświęcono automatyzacji, prezentowane były studia przypadków, zagadnienia związane z planowaniem produkcji czy planowaniem popytu. Podsumowanie konferencji stanowiła zaś debata poświęcona kondycji działających w Polsce firm produkcyjnych.
Doskonalenie procesów w Arjohuntleigh
Konferencję rozpoczęło ciekawe wystąpienie Macieja Koca, dyrektora ds. optymalizacji procesów w Arjohuntleigh Polska. Prelegent opowiadał o tym jak producent specjalistycznego sprzętu medycznego wykorzystuje takie metodologie jak Lean Manufacturing czy MTM w optymalizacji procesów produkcyjnych i magazynowych.
Arjohuntleigh, należące do Gettinge Group, oferuje rozwiązania dla pacjentów z ograniczoną mobilnością. Łóżka, materace przeciwodleżynowe czy podnośniki mają zapewnić chorym komfort i bezpieczeństwo. Arjohuntleigh Polska posiada fabrykę w Komornikach pod Poznaniem, a portfolio produktów tego zakładu jest sukcesywnie powiększane. Na produkcji pracuje 460, a w biurach 170 osób. Fabryka posiada powierzchnią 16,3 tys. m. kw.
Głównym celem prowadzenia optymalizacji procesów produkcyjnych i magazynowych była standaryzacja pracy i eliminacja marnotrawstwa. Prelegent podkreślił, optymalizacja nie byłaby możliwa bez możliwości pomiaru jej efektów. W Arjohuntleigh dane zapewnia coroczny Lean assessment. Dokładnie przestawione zostały składowe procesów, które są ocenianie oraz możliwe do osiągnięcia poziomy.
Dokładna ocena procesu produkcyjnego związana jest z przeprowadzeniem mapowania strumienia wartości. Określone zostały źródła marnotrawstwa i wyodrębniono te, które można wyeliminować. Pan Koc zdradził, że na tym etapie wykorzystywano analizę wideo oraz analizę czasów. Pomiary umożliwiły przeprowadzenie balansowania stanowisk. Kolejnym krokiem było stworzenie standardów pracy.
Drugim zagadnieniem, które omówił prelegent, stanowiła optymalizacja procesów optymalizacji logistyki wewnętrznej, prowadzona dwutorowo z wykorzystaniem narzędzi Lean oraz MTM. Przeprowadzone analizy miały lepiej planować zasoby potrzebne do obsłużenia poszczególnych linii oraz optymalizować operacje magazynowe związane z przygotowaniem komponentów.
Główne etapy tego projektu stanowiły mapowanie dróg transportowych, przygotowanie danych źródłowych, tworzenie tabel transportowych w oparciu o standardy MTM, oraz obliczenie zapotrzebowania na środki transportu i personel. W podsumowaniu prelegent wskazał korzyści, wynikające z przeprowadzonej optymalizacji.
Rewolucja w komunikacji na hali produkcyjnej
Daniel Oszczęda, dyrektor ds. marketingu i jakości Balluff, pochylił się nad korzyściami wynikającymi ze stosowanie zaawansowanych rozwiązań automatyki. Balluff juz od 50 lat jest obecny w tej branży, dzięki czemu prelegent mógł opierać się na przykładach udanych wdrożeń.
Już podczas tego wystąpienia po raz pierwszy pojawiło się hasło Przemysł 4.0. Balluff wykazuje dużą aktywność w propagowaniu tej idei, a pan Oszcząda na początku wystąpienia wskazał na jej założenia i oczekiwania, jakie producenci mają wobec kierunków jej wdrażania. Wspomniał też o dużych światowych markach, którzy w swoich działaniach już dopasowują się pod potrzeby klientów dzięki wysokiej personalizacji produktów i elastyczności procesów.
Głównym tematem wystąpienia były dwie technologie. IO-Link, rewolucyjne rozwiązania w zakresie komunikacji w hali produkcyjnej, ma zapewnić jeden standard i umożliwić integrację czujników oraz systemów zarządzających na różnych poziomach sterowania i wdrażania. Dzięki wdrożeniu IO-Link, informacje z czujników będą mogły bezpośrednio trafiać do systemów PLC, SCADA, MES i ERP, co zapewni błyskawiczny dostęp do dokładnych danych i w oczywisty sposób podniesie jakość zarządzania produkcją. Dzięki połączeniom sieciowym możliwa będzie np. automatyczne przezbrojenie wszystkich maszyn w momencie przejścia na produkcję innej wersji wyrobu. IO-Link da także możliwość szybkiej identyfikacji miejsca awarii w systemach sterowania.
Prelegent mówił także o tym jak daleko posunął się Balluf w wykorzystywaniu technologii RFID. Goście konferencji dobrze znali ją z procesów magazynowych. Tymczasem systemy Tool ID i Mold ID wykorzystują ją do monitoringu narzędzi skrawających oraz form odlewniczych i wskazują moment, w którym należy przeprowadzić serwis. Dzięki temu producenci mogą uniknąć związanych z produkcją wadliwych wyrobów.
Zażegnać konflikt w fabryce
O tym, jak działy utrzymania ruchu mogą wykorzystywać elementy systemu MES do zapewnienia ciągłości pracy parku maszynowego mówił Pavel Arno, konsultant z firmy Quantum Software. Prelegent przypomniał dobrze znany konflikt między działami produkcji i UR oraz sposoby na jego zażegnanie.
Nieprzewidziane awarie, przekładanie planowanych serwisów z powodu pilnych zleceń produkcyjnych i brak danych na temat remontów budzą ciągłe animozje między kierownikami produkcji, kierownikami UR i planistami. Brak narzędzia do komunikacji i standardów współpracy może spowodować chaos na hali, ponieważ każdy z uczestników procesu produkcyjnego ma własne oczekiwania.
Decyzje komórki UR przekładają się na wywiązywanie się produkcji i działu planowania ze swoich zadań i dlatego kierownik UR musi mieć wsparcie systemu analitycznego w podejmowaniu odpowiednich decyzji, często wiążących się ze znacznymi wydatkami. Choć systemy klasy MES przede wszystkim integrują poziom sprzętowy (SCADA, HMI, PLC) z poziomem biznesowym (ERP) firmy produkcyjnej, oraz często są przeznaczone do zaawansowanego planowania produkcji (moduł APS) i śledzenia realizacji produkcji w czasie rzeczywistym, mogą być też wyposażone w dodatkowe funkcjonalności.
Moduł utrzymania ruchu w systemie Qguar MES pozwala efektywnie koordynować współpracę międzywydziałową (planisty, kierownika produkcji oraz kierownika serwisu) w celu utrzymania parku maszynowego na odpowiednim poziomie technicznym, który pozwoli na realistyczne planowanie i wykonanie założonych planów. Prelegent opierając się na przykładach zaprezentował jak wygląda w tym rozwiązaniu proces obsługi zgłoszenia serwisowego i pokazał, jak informacja o awarii wpływa na modyfikację harmonogramu produkcji. Opisał też dodatkowe funkcjonalności modułu UR.
Automatyzacja nie zawsze się sprawdza
Robert Miernik, Management Consultant SIMPLE S.A., zajął się tematem planowania zasobów materiałowych i ludzkich pod realizację procesu produkcyjnego. SIMPLE już od 25 lat zajmuje się tworzeniem systemów klasy ERP, a w gronie klientów spółki znajduje się ponad 600 firm produkcyjnych.
Prelegent na wstępie podkreślił jednak, że aktualnie oferowane rozwiązania nie jest klasycznym systemem ERP. Oprogramowanie SIMPLE udostępnia w czasie rzeczywistym aktualne informacje o stanach magazynowych, przebiegu zleceń produkcyjnych, bieżącej sprzedaży, zakupach i finansach. Dzięki rozbudowanym mechanizmom śledzenia partii, nadawaniu numerów partii i serii oraz numerów badań laboratoryjnych SIMPLE.ERP wspiera systemy zarządzania jakością. Tym samym jego funkcjonalność zbliża się do rozwiązań klasy APS.
SIMPLE.ERP zarządza jednak nie tylko procesami produkcyjnymi, ale i pracownikami. Pan Miernik kładł w swoim wystąpieniu duży nacisk na znacznie zasobów ludzkich w fabryce i odnosząc się do poprzednich prelekcji podkreślił, że automatyzacja nie zawsze się sprawdza, zaś dla rozwoju firmy i poprawy jakości produktów wielkie znaczenie na wiedza pracowników.
Prelegent zaprezentował proces optymalizacji harmonogramu zleceń produkcyjnych z użyciem systemu i jego efekty – skrócenie terminów realizacji, zmniejszenie produkcji w toku oraz poprawę wykorzystania stanowisk. Zwrócił też uwagę na kilka funkcjonalności, jak automatyczne przeplanowanie w razie nieobecności kluczowego pracownika czy możliwość budowy w systemie partii produkcyjnych.
Wzorcowy projekt remontu w Hilding Anders
Wystąpienie Dawida Majchrzaka, Kierownika Działu Technicznego Hilding Anders Polska, okazało się jednym z najciekawszych podczas konferencji. Opisał on przebieg przygotowania i realizacji projektu generalnego remontu fabryki materacy w Murowanej Goślinie. Szereg pytań zadawanych po prelekcji potwierdził duże zainteresowanie uczestników konferencji tym tematem.
Konieczność dokonana remontu wynikała z planu strategicznego firmy Hilding Anders. Fabryka pomimo przejścia na system czterozmianowy była już na granicy swoich możliwości produkcyjnych, tymczasem zamówienia nieustannie rosły i według prognoz w 2015 roku zakład nie byłby w byłby już w stanie zaspokoić zapotrzebowania. Kolejnym wyzwaniem, przed którym stanęli autorzy projektu było rozwiązania problemu przeciążenia głównych dróg transportowych. Zwiększona produkcja wymagała też zapewnienia większej powierzchni na magazyn surowców.
Cele było zwiększenie zdolności produkcyjnych aż o 100%, skrócenie długości dług transportowych o 15-25% i zwiększenie pojemności magazynu surowców o 10-15%. Tak znaczący wzrost wydajności wymagał oczywiście zakupu nowej linii produkcyjnej, ale oczywiście pojawił się problem – gdzie znaleźć na nią miejsce w sytuacji, gdy projekt nie zakłada rozbudowy zakładu? Największym wyzwaniem było jednak uniknięcie ograniczenia zdolności produkcyjnych podczas trwania projektu.
Rozwiązaniem był re-inżyniering layoutu całej firmy. Prelegent zaprezentował wprowadzone zmiany, obejmujące reorganizację i zmniejszenie ilości centrów produkcyjnych, przebudowę magazynów i stworzenie nowej drogi transportowej. Przy okazji tego projektu postanowiono zautomatyzować systemy transportowe materacy i palet.
Gości konferencji dowiedzieli się jak został opracowany harmonogram projektu oraz jak wyglądała jego struktura personalna. Często w takich przypadkach członkowie projektu muszą dzielić swoje dotychczasowe zadania z udziałem w pracach nad remontem. Tymczasem zarząd Hilding Andres pozwolił oddelegować pracowników w całości do prac nad projektem.
Prelegent zaprezentował poszczególne etapy prac oraz wielki sukces wynikający z doskonałego planowania i wielkiego zaangażowania wszystkich członków projektu. Remont został praktycznie zakończony już na trzy miesiące przed planowanym terminem. Choć oficjalnie projekt nie został jeszcze zamknięty, analizy wskazują, że osiągnięte zostaną wszystkie cele.
Jak planuje Organika?
Aleksander Faleńczyk, menedżer ds. kontraktów BPSC oraz Rafał Majka, dyrektor IT w Organika SA przedstawili zaawansowany proces planowania w Grupie Kapitałowej Organika. Jako pierwszy przed gości konferencji pojawił się pan Faleńczyk, który zaprezentował firmę BPSC i wykorzystywany w Organice system impulsEvo.
BPSC, polski dostawca systemów informatycznych, działa od 27 lat i zrealizował już 1500 projektów wdrożeniowych dla 650 przedsiębiorstw. Jak zatem łatwo zauważyć, klienci po udanych wdrożeniach sięgają po kolejne rozwiązania BPSC. Prelegent przedstawił branże, w których można spotkać rozwiązania jego firmy i krótko przedstawił strukturę systemu impulsEvo oraz korzyści wynikające z implementacji systemów ERP.
Więcej czasu spędził przed mikrofonem Rafał Majka, poświęcając go na prezentację zasad harmonogramowania i planowania produkcji w Grupie kapitałowej Organika. Grupa składa się z kilku podmiotów, z których największymi są producent pianki poliuretanowej Organika SA, oraz producent chemii motoryzacyjnej Organika Car SA.
Prelegent związany jest z łódzkim zakładem Organika SA, lecz proces planowania produkcji został zintegrowany w ramach całej grupy. Głównymi celami wdrożenia systemu ERP, zapoczątkowanego w 2009 roku, było zintegrowanie i uporządkowanie informacji dla całej grupy kapitałowej, automatyzacja wymiany informacji w grupie i na zewnątrz oraz optymalizacja planowania – w szczególności wielofirmowego.
Pan Majka zaprezentował schemat modelu planowania w Organice, szerzej omawiając jego trzy najważniejsze elementy – plan produkcji, raport PZM (planowanie zapotrzebowania materiałowego) i harmonogram szczegółowy. Przekazał też swoje wnioski z wdrożenia, podkreślając, ze sam system informatyczny nie pozwoli rozwiązać problemu planowania i firma sama musi zaprojektować model planowania, a IT wykorzystywać do wsparcia jego realizacji. Wystąpienie podsumował dobrze znanym stwierdzeniem – planowanie będzie się sprawdzać tylko wtedy, gdy pozyskamy kompletne i aktualne dane.
UPS dla producentów
Małgorzata Matusiewicz, dyrektor marketingu w Dystrykcie Wschodnim UPS Europe, mówiła o ofercie firmy dla producentów, chcących rozwijać swój biznes i skorzystać z dopracowanych i innowacyjnych rozwiązań logistycznych. Wystąpienie rozpoczęła od krótkiego przedstawienia długiej historii firmy i przypomniała, że to UPS wymyśliło element spotykany dziś powszechnie w transporcie wewnętrznym, czyli taśmociąg.
Prelegentka zachęcała gości do wskazywania problemów jakie napotykają na polu logistyki, gdyż UPS stara się znaleźć na nie odpowiedź. Zaprezentowała przykłady szytych na miarę rozwiązań, które spełniają wymagania specyficznych branż – farmaceutycznej, motoryzacyjnej i retail. Podkreśliła też jak duże znaczenie dla gospodarki polski mają firmy produkcyjne.
Pani Matusiewicz zaznaczyła, że producenci powinni skupiać się na swoim core businessie, a nie tracić czas na rozwiązywanie problemów pojawiających się w łańcuchu dostaw. Rozwiązaniem tych trudności najszybciej znajdą eksperci z branży logistyki. Rozwiązania UPS pozwalają zapewniają producentom skuteczne sprowadzanie towaru od zagranicznych kontrahentów, dystrybucję gotowego produktu i zaawansowaną obsługę posprzedażową. Wystąpienie zakończyła prezentacja filmu na temat małego producenta silników do paralotni i innych rozwiązań dla awiacji indywidualnej, który dzięki współpracy z UPS importuje swoje wyroby na cały świat.
Ułatwić wybór
Adam Błuś, prezes wydawnictwa Eurologistics, zachęcał gości konferencji do udziału w bardzo ciekawym projekcie – transportowych i logistycznych spotkaniach handlowych między firmami produkcyjnymi i handlowymi a dostawcami usług transportowych i logistycznych. Prelegent przedstawił genezą powstania tej platformy i korzyści, jakie wynoszą z nich prelegenci.
Nie ma wątpliwości, że firmy produkcyjne będą coraz szerzej korzystać z outsourcingu zadań logistycznych. Jednak poszukiwania i wybór partnerów w tej dziedzinie wiąże się z wieloma problemami. Dotarcie do wiarygodnych partnerów, których oferta odpowiada zapotrzebowaniu przewoźnika, wymaga wielu poszukiwań i odbycia licznych spotkań, które często kończą się bezowocnie.
Organizowane przez Wydawnictwo Eurologistics oraz czasopismo Truck&Business Polska spotkania mają na celu umożliwienie nadawcom dotarcie do ponad 100 dostawców usług transportowych jednego dnia i ich wstępną weryfikację. Bezpośredni kontakt z dostawcami pozwala na szybkie zdobycie istotnych informacji, producenci uczestniczący w spotkaniach mogę też rozbudować swoją bazę danych i przeprowadzić benchmarking rynku. Prelegent zaprosił wszystkich zainteresowanych na przyszłoroczne edycje spotkań.
Przemysł 4.0 bez tajemnic
Na wystąpienie Luca Wintjesa czekali wszyscy. Senior Vice President Sales Europe z Bosch Rexroth AG podczas fascynującej prelekcji podzielił się swoją bogatą wiedzą na temat koncepcji Przemysł 4.0, oraz wkładu z Bosch Rexroth w jej rozwój.
Prelegent na wstępie wskazał na gwałtowny rozwój nowych technologii, a dzięki kontaktom z czołowymi światowymi mógł uchylić rąbka tajemnicy i opowiedzieć o kilku niezwykłych produktach, których jeszcze nie ma rynku, a które będę prezentować niezwykle zaawansowane rozwiązania. Podkreślił przy tym, że wdrożenie zasad Przemysłu 4.0 jest niezbędne, aby móc wytwarzać tak wyrafinowane produkty.
Kilka minut zostało poświęconych profilowi firmy Bosch i jej dywizji – Bosch Rexroth. Niemiecki koncern działa na wielu polach, zaś Bosch Rexroth odpowiada za rozwiązania napędów i kontroli i działa głównie w branży motoryzacyjnej, aplikacji mobilnych, przemyśle maszynowym i branży energii odnawialnych. Rexroth dostarcza rozwiązania automatyki także dla fabryk rodzimego koncernu i dysponuje tym sposób znakomitym danymi zwrotnymi, dzięki którym może doskonalić swoje rozwiązania. Bez wątpienia jest to jednak z najważniejszych, jeżeli nie najważniejsza światowa firma dostarczają rozwiązania dla przemysłu.
Pan Wintjes przeszedł następnie do opisania elementów stanowiących podwaliny Przemysłu 4.0 – gwałtownego rozwoju komunikacji między ludźmi a przedmiotami, oraz narodzin Internetu Rzeczy i Internetu Usług. Inteligentne budynki, Uber wypierający taksówki, smart shopping – te rozwiązania, wiążące strumienie wartości już znamy. Przemysł jest kolejnych obszarem, dla którego wszechobecne powiązania będą miały ogromne znaczenie. Prelegent podkreślił, że wpływ Przemysłu 4.0 na światową produkcję będzie ogromny, ale też nieprzewidywalny – na razie mamy narzędzie, lecz nie wiemy nawet, jakie problemy będzie ono rozwiązywać.
Przemysł 4.0 to podstawa czwartej rewolucji przemysłowej i uczestnicy konferencji mogli zobaczyć, jak wyglądały jej poprzednie wcielenia – mechanizacja, elektryfikacja i cyfryzacja. Przemysł 4.0 to też nazwa oficjalnego programu wspieranego przez niemiecki rząd. Pan Wintejs przyznał, że nie lubi oficjalnej definicji i zawsze podkreśla w niej tylko jedną rzecz – idącą za zmianami indywidualizację produkcji pod potrzeby klienta. Po wprowadzeniu Przemysłu 4.0 w życie przejdziemy od łańcucha wartości dodanej do sieci wartości dodanej.
Bosch Rexroth opracowuje rozwiązania zgodne z założeniami Przemysłu 4.0 i już wdraża je w życie. Koncern posiada 250 fabryk na całym świecie i wdrożył już 50 pilotażowych rozwiązań Połączonego Przemysłu. Prelegent zaprezentował kilka zaawansowanych rozwiązań stosowanych przez Boscha. Szczególną uwagę poświęcił wdrożeniu platformy Open Core Engineering – dzięki niej klienci mogą dowolnie modyfikować wdrożone u siebie systemy automatyki i sterowania. Pan Wintjes zdradził, że pomysł otwarcia danych dla klientów miał w zarządzie firmy wielu przeciwników, lecz ostatecznie decyzja ta okazała się sukcesem – platforma Open Core Engineering otrzymała prestiżową nagrodę Hermes Award 2013.
Szczytowym rozwiązaniem na polu Przemysłu 4.0 jest prototyp linii produkcyjnej przyszłości działający w Homburgu i wykorzystujący szereg rozwiązań, łączących w sieć pracowników, produkty i maszyny. Najważniejszym elementem wystąpienia było jednak stwierdzenie, że na razie widzimy tylko 10% możliwości, jakie niesie za sobą Przemysł 4.0 – ale nie wiemy też, w jakim kierunku ta idea nas poprowadzi.
Czarownica, diabeł i anioł
Przedostatni punkt programu miał niezwykłą formułę. Zamiast prelekcji, obejrzeliśmy przedstawienie, które przygotował zespół firmy DSL – Aleksandra Balwierczyk, Szymon Rutz, Łukasz Salawa, Lech Szczeciński i Grzegorz Zaworski, pod wodzą Dariusza Siwka.
Występ miał przybliżyć zebranym kwestię planowania popytu. Intryga toczyła się w firmie produkującej suszone czerwone buraczki, która stanęła przed zadaniem skorelowania swoich możliwości produkcyjnych i stanu zapasów oraz potrzeb rynku. Mogliśmy przyglądać się jak na przestrzeni roku rzekomo znakomity plan zawodzi na całej linii, magazyny to są przepełniona a to puste, a końcu do gry wchodzą siły nieczyste – czarownica i diabeł. Na szczęście był też anioł.
Humorystyczny charakter tego wystąpienia nie przesłonił faktu, jak dramatycznie potrafią rozmijać się plany z rzeczywistością. Dariusz Siwek w podsumowaniu zachęcił gości konferencji do zwracania uwagi na każdy szczegół w planowaniu popytu. Gdyby zaś ktoś nie dostrzegał diabła, który tkwił w tych szczegółach, ekipa DSL chętnie w tym pomoże.
Co z naszą produkcją?
Podsumowaniem całodziennych wykładów była debata, poświęcona tajnikom sukcesów działających w Polsce firm produkcyjnych i roli automatyzacji w rozwoju naszych fabryk. Wzięli w niej udział Dawid Majchrzak, kierownik działu technicznego Hilding Anders Polska, Rafał Majka, dyrektor IT w Organika SA, Daniel Oszczęda, dyrektor ds. marketingu i jakości Balluff oraz Przemysław Kędzierski, analityk biznesowy MRPII z BPSC.
Paneliści nie kryli, że zasoby ludzkie stanowią bardzo istotny czynnik sukcesów polskich fabryk. Inwestycje zagraniczne przyciągają do nas niskie koszty pracy, lecz polscy pracownicy są też niezwykle solidni i zaangażowani. W niektórych rejonach kraju zaczynają być już jednak widoczne niedobory kadr.
Nie można też zapominać o tym, że Polska to duży rynek, co ma znaczący wpływ na rozwój działań produkcyjnych. W podsumowaniu debaty jej uczestnicy przyznali, że jeżeli chodzi o poziom zaawansowania technologicznego i organizacji pracy, od zachodnich fabryk dzieli nas jeszcze pewien dystans, wynikający m.in. z braków kapitałowych czy pewnego konserwatyzmu we wdrażaniu automatyki. Można mieć jednak nadzieję, że będzie on się zmniejszał.
Niezwykle intensywny dzień zakończył się więc pozytywnym akcentem. Serdecznie dziękujemy wszystkich uczestnikom konferencji za przybycie, szczególnie cieszyły nas liczne pytania zadawane niemal po każdym wystąpieniu.
Podziękowania kierujemy także pod adresem partnerów Manufacturing Summit: firm Balluf, Bosch Rexroth, Organika, BPSC, UPS, Hilding Anders, Delta Trans, wrh global Polska, SIMPLE, Quantum Software, Emtor, Yale, Amsort, Rohlin Suus i Arjohuntleigh.
Galerię zdjęć z wydarzena można znaleźć na stronie Logistyki Produkcji
Galeria zdjęć do artykułu
Pliki do pobrania
zarejestruj się by uzyskać bezpłatny dostęp do materiałów z konferencji. W ten sposób dbamy o polepszanie jakości naszych usług i dostarczanych do Ciebie materiałów. Rejestracja oznacza akceptację aktualnej polityki prywatności.