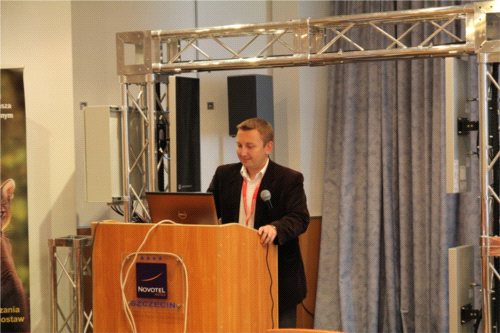
Inwestycja w oszczędności
O co pytają nasi konkurenci – na to pytanie chciałby znać odpowiedź chyba każdy menedżer. Pomoc dla rozwikłania tej zagadki zaoferowali już nie po raz pierwszy przedstawiciele Quantum Software, organizując seminarium logistyczne.
Miejscem był Szczecin, nic dziwnego więc, że jeden z istotnych elementów stanowiła tematyka związane z procesami odbywającymi się na styku lądu i wody. Wiele mówiono jednak również o procesach kompletacji towaru i planowaniu transportu – w aspekcie systemów IT i nie tylko.
Spotkanie było skierowane do menedżerów zarządzających łańcuchami dostaw, produkcją, logistyką, transportem oraz do szefów działów produkcji, magazynów i transportu. Co więcej, wiedzę można było uzyskać za darmo.
– Klienci zazwyczaj pytają nas co zrobić, by logistyka kosztowała mniej, bo stanowi ona istotny element dla budżetu. Chcą w oparciu o określone systemy, moduły, rozwiązania zyskać przewagę nad konkurentami. Ile zaoszczędzą przy zastosowaniu naszych produktów? Wszystko zależy od indywidualnych cech danego podmiotu gospodarczego. W firmach mających uporządkowaną logistykę, z doświadczonym menedżerem, który wypracował określone schematy działania, to oszczędności rzędu 5-10 procent. Jednak nie brakuje przedsiębiorstw, gdzie zyski sięgają nawet 60 procent. Dlatego że pewne procesy są u nich „zapuszczone koncepcyjnie”, nie ma systemów, stosowane rozwiązania nie sprawdzają się. Wtedy mamy duże pole do popisu – mówi Tomasz Mandziej, dyrektor ds. handlu Quantum Software.
Problemy i błędy
– Kompletacja jest najważniejszym ogniwem procesu magazynowego i miejscem największej optymalizacji pracy magazynierów. Ma wpływ na zadowolenie klientów i świadczy o poziomie naszego przedsiębiorstwa. I zaczyna się już w momencie dostawy towaru do magazynu – mówi Piotr Krawczyk, SCE Solutions Sales Executive Quantum Software.
Jednak kompletacja towaru w magazynie urasta do rangi problemu. Ma to związek z czynnikami organizacyjnymi jak i ekonomicznymi.
Czynniki organizacyjne. Trzeba tutaj zwrócić uwagę między innymi na coraz krótszy czas realizacji zamówienia klienta i zwiększający się wolumen przepływów towarowych. Obecnie mamy do czynienia z trendem zmierzającym w kierunku realizacji zamówień w trybie just in time. Do tego dochodzą kwalifikacje operatorów magazynowych, związane poniekąd z występującą permanentnie rotacją personelu. Jednym z tego przejawów stanowią błędy w wydaniach, a to pociąga za sobą nakłady na obsługę reklamacji/zwrotów.
Czynniki ekonomiczne. Konkurencyjność, elastyczność realizacji zamówień, zadowolenie klienta z poprawnych dostaw, rentowność magazynu, minimalizacja strat, usprawnienie przepływu informacji w relacji dostawca – magazyn – klient.
Zdaniem Piotra Krawczyka, SCE Solutions Sales Executive Quantum Software na etapie kompletacji występuje wiele błędów. I wymienia:
Błędy systemowe:
– niedostosowanie typu regałów do składowanego asortymentu
– źle dobrany sprzęt magazynowy
– brak systemu klasy WMS
– słabe kwalifikacje kadrowe w magazynie
Błędy operacyjne:
– Łamanie zasad FEFO/FIFO
– nieprzestrzeganie dat ważności, best before… itd.
– traktowanie dostaw jako pożeracza czasu
– słaba kontrola pracy operatorów magazynowych
– nieprzejrzysty system raportowania lub jego brak
– Moim zdaniem błąd strategiczny stanowi traktowanie kompletacji jako generatora kosztów a nie fazy magazynowania mającej największe pokłady optymalizacji wydajności całego magazynu – dodaje P. Krawczyk z Quantum Software.
Modele kompletacji
Współczesna kompletacja staje przed wieloma wymaganiami. To między innymi setki parametrów związanych z różnorodnością asortymentu: numery seryjne, partie, daty ważności, towary wielkogabarytowe, nietypowe, drobnicowe, zmiennowagowe, świeże, sezonowe, akcyzowe, podlegające cleniu, ADR`y, itp. Do tego dochodzą parametry dotyczące specyfiki pracy magazynu – strefy kompletacji, odkładcze, taśmociągi, regały karuzelowe, wózki systemowe, foliarki, kompletacja falowa, co-packing, grupowanie/dzielenie zleceń, zarządzanie priorytetami i kolejnością zleceń, łączenie/dzielenie wysyłek, itp.
Poza tym pakowanie (parametry nośnika wysyłkowego, układanie i zabezpieczenie towaru na nośnikach), etykietowanie, termin realizacji zlecenia, stosowanie kodów zewnętrznych/odbiorców, unikanie błędów podczas pobierania towarów z półek podczas kompletacji, minimalizacja zwrotów/reklamacji, maksymalne wykorzystanie zasobów, elastyczne reagowanie na zmiany, cross-docking.
Piotr Krawczyk z Quantum Software wspominał również o modelach kompletacji. W tradycyjnych magazynach najczęściej stosowany jest model „Człowiek do towaru”. Wykorzystywane są terminale radiowe lub wydruki. Następuje optymalizacja ścieżki zbiórki magazyniera. Można wtedy stosować metodę multi-klient/multi order picking. „Towar do człowieka” występuje zwykle w sytuacji obsługi sieciowej przy wykorzystaniu terminali radiowych oraz automatyki magazynowej. Następuje optymalizacja ruchów wózków widłowych oraz obsługa miksów na obszarze kompletacji zamiast w alejkach regałowych.
Z kolei „kompletacja mieszana” występuje zwykle w magazynach automatycznych. Implikuje zalety metody PBS w połączeniu z PBL. Pozwala na redukcję etatów kosztem instalacji układnic, zapewnia największą precyzję wydania, a także szybkość przygotowania nośników zbieranych. Człowiek pełni rolę operatora stacji przeładunkowej/kompletacyjnej. Jest jednak droga w stosowaniu.
Obawa przed nadzorem
Dobór metody kompletacji zależy między innymi od rodzaju asortymentu i jego wartości, czasu dostawy od złożenia zamówienia, współczynnika komisjonowania, częstotliwości zleceń, organizacji przyjmowania i realizacji zleceń. Ale nie tylko. Trzeba wziąć także pod uwagę czynniki organizacyjne – powierzchnie magazynową, wymagania odbiorców, kadrę pracowniczą i jej kwalifikacje, posiadane narzędzia informatyczne. Istotne są również czynniki ekonomiczne: koszt inwestycji w systemy automatyki, koszty błędów w wydaniach i powiązanych z tym reklamacji/zwrotów, koszt utrzymania pozycji rynkowej – radzi Krawczyk Quantum Software.
Nie wszystkie firmy jednak jeszcze rozumieją jak ważny jest proces kompletacji. – Nadal w rozmowach z firmami spotykamy się z pewnymi barierami. Takim najpoważniejszym jest moim zdaniem pewna blokada psychiczna, wręcz strach ludzi przed tym, że użytkowaniem sytemu informatycznego. To obawa przed nieznanym, lecz także niezadowolenie z wprowadzenia narzędzia kontroli. Bo tak właśnie postrzegane są nierzadko systemy – nie jako narzędzie optymalizujące i wspierające ich pracę, ale czynnik nadzoru, czuwający nad każdym krokiem i czynnością – mówi Piotr Krawczyk z Quantum Software.
Zapotrzebowanie popytu
Distribution Resources Planning (DRP) to określanie popytu na zapasy w jednostkach organizacyjnych przedsiębiorstwa, zajmujących się dystrybucją. System dostrzega relacje pomiędzy firmą a otoczeniem w obrocie towarowym, zapewnia jego elastyczność wobec zmian na obsługiwanych rynkach, koncentruje się na możliwości szybkiego reagowania podmiotu gospodarczego na zmiany wielkości popytu.
– Wszelkie decyzje odnoszące się do wielkości dostawy oraz terminu jej realizacji zależą od producenta, przy czym ich dobór uzależniony jest głównie od ostatecznego terminu realizacji danego zlecenia – mówi Krzysztof Piotruk, doradca ds. systemów logistycznych w Quantum Software. DRP może być wykorzystywany do planowania i harmonogramowania transportu, częstotliwości wysyłek, maksymalizacji wykorzystania objętości/wagi środków transportu, budżetowania, planowania powierzchni składowania.
Jak mówi Piotruk, prognoza zapotrzebowania/popytu na dobra tworzona jest poczynając od poziomu najniższego (np. punkty sprzedaży detalicznej), a kończąc na poziomie najwyższym (np. magazyn fabryczny). Dane wyjściowe dla każdego poziomu są danymi wejściowymi dla poziomu następnego. Zapotrzebowanie oszacowane dla najwyższego poziomu dystrybucji może służyć jako dane wejściowe przy opracowywaniu harmonogramów produkcji.
Planowanie transportu
Decyzję o wysłaniu dostawy do klienta warunkuje między innymi minimum logistyczne, wyrażone w złotych oraz analiza czy transport dotrze do klienta przed zamknięciem przez niego sklepu. Ważną rolę odgrywa wybór pojazdu. Musimy przeanalizować jak wielki samochód potrzebujemy do wykonania danej trasy – zarówno pod względem dopuszczalnej masy całkowitej jak i przestrzeni ładunkowej, bo skorzystanie ze zbyt dużego auta generuje niepotrzebne koszty. Należy przy tym wziąć pod uwagę ograniczenia związane z warunkami technicznymi występującymi w poszczególnych punktach dostawy oraz czas trwania trasy (ilość punktów dostaw, stopień utrudnień wydłużających czas realizacji dostawy do punktu odbioru). Do tego dajmy ewentualną potrzebę skorzystania z pojazdu wysoce specjalistycznego (np. chłodnia).
Analizie należy również poddać kryteria kolejności wysyłania samochodów w trasy. – Najpierw realizujemy punkty najbardziej oddalone od obiektu magazynowego. Tej zasadzie towarzyszy inna – im bardziej oddalony punkt dostawy tym potrzebujemy większy samochód (promień wywozu). Weźmy również pod uwagę, czy zaopatrzenie następuje bezpośrednio z Centrum Dystrybucji klienta czy poprzez cross-dock, okna czasowe dostaw u nabywców usługi, rodzaj wysyłanego towaru – wiadomo, że im świeższy tym szybciej musi dotrzeć do celu – opowiada K. Piotruk z Quantum Software.
Aby zminimalizować opóźnienia dostawy w razie pików zamówieniowych, towar może być dostarczony samochodem większym (pojemność, d. m. c.), ale jest dzielony na dwa różne auta w celu zmieszczenia się w oknach czasowych dostawy u klienta.
Kryteria ustawiania kolejności punktów dostawy na trasie dotyczą między innymi okien czasowych dostaw do klientów, ich ważności, ustaleń indywidualnych czynionych w przypadku dużego wolumenu zamówienia lub zatowarowania.
Stan transportu
Na seminarium nie zabrakło tematyki bezpośrednio związanej z portami. Zdaniem Anny Ksepko-Jensen z firmy Akpol przyszłość obsługi logistycznej portów należy do systemów informatycznych co wymaga od firm inwestycji. Na przykład w BTP w Świnoujściu wdrożono Qguara, dzięki któremu czynnik ludzi został ograniczony do minimum.
Ksepko-Jensen narzekała również na stan polskiego transportu… – Jestem pozytywnie nastawiona do kolei, ale muszą w niej zajść wielkie zmiany. Jak ufać tej gałęzi, skoro podczas przewozu 1200 ton towaru, 150 ton ginie po drodze z powodu awarii wagonów?! I w dodatku nie można ich zlokalizować. Albo w trakcie ładowania, 30 procent wagonów okazuje się niesprawnych? Marnotrawiona jest infrastruktura jeśli chodzi o szyny, za dużo mamy spółek kolejowych – opowiadała A. Ksepko-Jensen.
Teoretycznie najtańszym sposobem transportu jest żegluga śródlądowa, lecz w Polsce to bardzo trudna kwestia, choć Szczecin ma dobre połączenia wodne z innymi krajami europejskimi. Kolejny wniosek prelegentki dotyczył faktu, że porty muszą się nastawić na przyjmowanie coraz większych statków.
Waga wagi
O możliwościach nowoczesnych systemów ważących mówił Dariusz Glina z firmy Automatyka Serwis. Ciekawe rozwiązanie stanowi na przykład system ważenia pojazdów transportu drogowego, który może być banalnie prosty w obsłudze. Kierowca otrzymuje identyfikator RFID i wjeżdża na wagę. System wykonuje praktycznie całą pracę – posiada czujnik prawidłowego położenia pojazdu, czytnik RFID do identyfikacji i zważenia auta, wyświetlacze wielkogabarytowe, kamery wykonujące zdjęcia podczas ważenia. Transmisja danych następuje przez Ethernet. Z sali pojawiło się pytanie o wagi osiowe. – Jest ona obarczona wielkim błędem, więc nie oferujemy tego typu wag – mówi Dariusz Glina z Automatyka Serwis.
Dogrywka jeszcze w tym roku
Tomasz Mandziej, dyrektor ds. handlu Quantum Software
– Zgodnie z naszym trybem działania, po seminarium przeprowadzamy dodatkowe zajęcia – „Qroadshow”. Na podstawie ankiet wypełnionych przez uczestników spotkania, na kolejne, tym razem planowane w Szczecinie w tym roku, dobieramy informacje o elementach systemów, które wzbudziły największe zainteresowanie i pokazujemy je w sposób bardziej szczegółowy.
WMS to konieczność
Piotr Krawczyk, SCE Solutions Sales Executive Quantum Software.
– W przypadku systemów WMS nie ma mowy o jakiś rewolucjach, bo są one dojrzałe. Lecz oczywiście cały czas się zmieniają i posiadają szereg funkcjonalności, jakich kiedyś nie miały. Przystosowujemy je między innymi pod kątem przepisów jak i wymogów stawianych przez Unię Europejską. Systemy angażują nie tylko magazynierów, lecz również cały łańcuch dostaw począwszy od biura obsługi klienta aż po kierowców. Można więc śmiało powiedzieć, że zdecydowanie wyszły poza obszar magazynu. Ich wpływ na organizacje zaczyna być coraz większy. Obecnie WMS nie jest wdrażany dla prestiżu, czy pokazania statusu firmy. Przeciwnie, przedsiębiorstwa zajmujące się magazynowaniem bez niego są wręcz traktowane jak relikty poprzedniej epoki. Szczególnie jeśli firma posiada swoje magazyny.