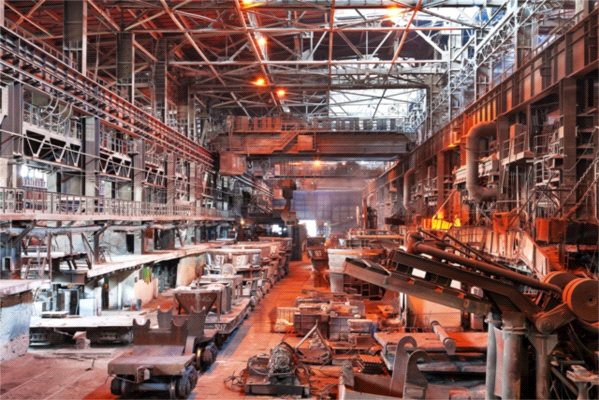
Poprawa wskaźnika OEE
Istotną rolę w fabrykach odgrywa odpowiednie zarządzanie maszynami. Obejmuje ono zapewnienie bezawaryjnej pracy maszyn nie tylko w sensie indywidualnym, ale i w zakresie kompleksowych linii technologicznych. Zazwyczaj uwzględnia się przy tym wskaźnik OEE (ang. Overall Equipment...
Za pomocą wskaźnika OEE porównuje się efektywność różnych środków produkcji lub efektywność konkretnej maszyny w określonym przedziale czasowym. Poprawa tego wskaźnika to oczywiście korzyści finansowe dla fabryki. Warto przyjrzeć się nieco bliżej wskaźnikowi OEE i zwrócić uwagę na fakt, że stanowi on wypadkową trzech wskaźników. Są to: dostępność, wykorzystanie i jakość.
Dostępność jest to stosunek czasu operacyjnego do planowanego czasu produkcji Dostępność obniżana jest przez awarie oraz przyjęte metody przezbrajania. Na OEE składa się również wykorzystanie , czyli stosunek czasu dostępnego do rzeczywistej pracy. I tak, jeżeli maszyna ma dostępny określony czas na pracę, to wskaźnik wykorzystania pokazuje ile faktycznie udało się go wykorzystać. Przy obliczaniu OEE kluczową rolę odgrywa też jakość. Stanowi ją stosunek liczby dobrych i wadliwych produktów wytworzonych przez maszynę.
Marnotrawstwo
Założeniem wszelkich działań, w tym poprawiających wskaźnik OEE, jest eliminowanie marnotrawstwa. Ważne pozostaje bowiem usunięcie wszelkich elementów, które podnoszą koszty produkcji bez wnoszenia do niej użytecznego wkładu. W pierwszej kolejności za kluczową stratę można uznać nadprodukcję, czyli produkowanie więcej niż jest potrzebne lub za wcześnie. Strata to również zbędny ruch, a więc nadmierne przemieszczanie się pracowników związane ze złą organizacją stanowisk pracy. Warto zwrócić również uwagę na oczekiwanie będące długim okresem bezczynności ludzi, maszyn, części czy też materiałów. Stratą jest zbędny transport, a więc przemieszczanie elementów, części i półwyrobów w sposób częstszy, niż jest to konieczne. Mówiąc o marnotrawstwie należy mieć na uwadze zbędne zapasy, czyli sytuacje, gdy zbyt wiele materiałów oczekuje na kolejne etapy w procesie produkcji oraz zbyt wiele jest wyrobów gotowych. Kolejnym przykładem marnotrawstwa jest zbędna obróbka i wykonywane w jej ramach niepotrzebne ruchy. Za straty uznaje się wady wyrobów, a także błędy dotyczące informacji, dostaw i dokumentacji.
Po pierwsze: TPM
Istotnym narzędziem poprawy współczynnika OEE jest Total Productivity Maintenance (ang. Globalne Zarządzanie Utrzymaniem Ruchu) będące jednym z narzędzi zarządzania Lean Management. Celem TPM jest zapewnienie maksymalnej dostępności najważniejszych urządzeń. Koncepcja TPM została opracowana przez JIPM (Japan Institute of Plant Maintenance) w celu wsparcia japońskich firm. Za główny cel TPM uznaje się uzyskanie poziomu trzech zer, czyli zero: awarii, braków i wypadków przy pracy.
Należy podkreślić, że cele TPM realizuje się za pomocą dwóch obszarów: człowieka i maszyny. W odniesieniu do człowieka, TPM ma za zadanie zwiększenie efektywności pracowników poprzez podniesienie poziomu ich umiejętności i wiedzy. W efekcie pracownicy bardziej angażują się w swoją pracę, a co za tym idzie, są w stanie w sposób samodzielny podejmować należyte decyzje. W odniesieniu do maszyn – działania pracowników powinny koncentrować się na utrzymaniu maszyn i urządzeń w stanie wysokiej dostępności w taki sposób, aby dział utrzymania ruchu otrzymywał od operatorów informacje o stanie całego parku w celu zaplanowania działań. Poprzez dobre poznanie maszyn operatorzy wraz z pracownikami utrzymania ruchu i technologami opracowują projekty ulepszeń (pomysły Kaizen), mające na celu ułatwienie konserwacji lub usprawnienie maszyn. Służby utrzymania ruchu przechodzą z reakcyjnej na predykcyjną obsługę maszyn, dzięki czemu rośnie dostępność maszyn oraz ich niezawodność, co bezpośrednio zmniejsza koszty wytwarzania i tym samym powiększa zyski przedsiębiorstwa.
Po drugie: SMED
Za ważne narzędzie poprawy wskaźnika OEE uznaje się SMED (Single Minute Exchange of Die). Jest to zarówno nazwa metody szybkiego przezbrajania, jak i metodologii osiągania czy też wdrażania tej metody. SMED jest elementem tzw. kompleksowych systemów zarządzania (operacyjnego), takich jak Total Productive Maintenance czy System Produkcyjny Toyoty (szczupłe zarządzanie, Lean Manufacturing).
W metodzie krótkiego przezbrojenia ważne jest, aby jak najwięcej czynności wykonać poza samą maszyną, w czasie gdy ona jeszcze pracuje. Na przykład jeśli przezbrojenie polega na wymianie matrycy lub formy oraz podgrzaniu jej, to wstępne podgrzewanie należy urządzić przed wymianą. Jeśli trzeba wymienić dysze na stelażu i wyregulować je, to należy zrobić to na stelażu zapasowym, wcześniej, aby można było zatrzymać maszynę tylko na krótki czas wymiany całego uzbrojonego stelaża. Oprócz tego zwraca się uwagę, aby gdzie tylko to możliwe zastosować mocowanie „jednym ruchem”. Na przykład zatrzaski zamiast śrub (do mocowania osłony itp.). Podobnie – uchwyt bagnetowy z wykrojnikami czy innymi końcówkami roboczymi.
Po trzecie: wspomaganie narzędziami informatycznymi
Nowoczesne zarządzanie utrzymaniem ruchu nie obejdzie się bez narzędzi informatycznych. Oprogramowanie tego typu pozwala na kompleksową obsługę parku maszynowego. Zgłaszanie awarii z linii produkcyjnej nie tylko przebiega szybko, ale i jest w pełni zautomatyzowane. Istotna cecha nowoczesnych systemów CMMS to elastyczność konfigurowania. To właśnie dzięki niej oprogramowanie jest ściśle dostosowane do potrzeb użytkowników. Ważna pozostaje możliwość integracji systemów CMMS z innymi aplikacjami przemysłowymi klasy SCADA, MES czy też ERP. Na szczególną uwagę zasługuje szybki dostęp do informacji dotyczących konkretnego urządzenia czy też maszyny. Tym sposobem przed przystąpieniem do prac pracownik utrzymania ruchu zapoznaje się z dokumentacją techniczną. Z pewnością przydatna jest możliwość prześledzenia historii zgłoszeń serwisowych i działań podjętych celem ich rozwiązania. Na uwagę zasługuje tworzenie harmonogramów prac remontowych i okresowych przeglądów maszyn.
W działach utrzymania ruchu z pewnością przydadzą się funkcje, dzięki którym są przechowane informacje o przebytych przez pracownika szkoleniach, a także nabytych uprawnieniach i kwalifikacjach. Można wtedy podczas prac związanych z harmonogramowaniem przydzielać właściwych pracowników do odpowiednich zadań. Kierownictwo fabryki zyskuje dostęp do obszernych raportów, z których wynika szereg informacji o najczęściej występujących awariach.
Jakie zatem zalety zyskuje się wdrażając system CMMS? Przede wszystkim na uwagę zasługuje optymalizowanie nakładów ponoszonych na infrastrukturę przemysłową. Nie bez znaczenia pozostaje zredukowanie zasobów magazynowych w zakresie części zamiennych. Ważne jest też efektywne zarządzanie personelem technicznym oraz osiągnięcie wysokiej sprawności systemów technologicznych. Niewątpliwa zaleta to również zminimalizowanie ilości awarii oraz innych nieplanowanych zdarzeń. Na uwagę zasługuje przy tym redukcja kosztów administracyjnych.
Co jeszcze?
Mówiąc o poprawie wskaźnika OEE, warto wspomnieć o obsłudze autonomicznej (ang. Autonomous Maintenance). Polega ona na przekazaniu operatorom odpowiedzialności za sprawne działanie maszyn. Przy wdrażaniu obsługi tego typu w pierwszej kolejności należy zadbać o to, aby maszyny były czyste. Chodzi przede wszystkim o pozbycie się wszystkich drobnych nieprawidłowości, które są wykryte podczas czyszczenia. Niejednokrotnie pomocna przy tym okazuje się metoda 5S. Zwraca się uwagę na wyeliminowanie przyczyn zanieczyszczeń. Ważne pozostaje również skrócenie czasu trwania czyszczenia i smarowania oraz opracowanie standardów w tym zakresie. Powinny one stanowić wytyczne do zagwarantowania efektywnej obsługi maszyn. Przyda się utworzenie harmonogramu dla zadań okresowych.
W następnej kolejności wprowadza się podstawowe przeglądy. Istotną rolę odgrywa przy tym zapoznanie operatorów, najlepiej poprzez szkolenie, z instrukcjami przeglądów. Podczas przeglądów powinny być wykrywane nawet najmniejsze nieprawidłowości w pracy maszyn.
Kolejny etap przewiduje wprowadzenie przeglądów autonomicznych. Przydatne rozwiązanie stanowią listy kontrolne działań w tym zakresie. Ważne jest bowiem wyeliminowanie podwójnej kontroli. Do podniesienia skuteczności przeglądów z pewnością przyczyni się kontrola wizualna i standaryzacja. Ostatni etap ma na celu stworzenie spójnego, a zarazem kompleksowego systemu zarządzania obsługi autonomicznej. Bierze się przy tym pod (wpisać: pod) uwagę politykę i cele firmy.
Podsumowanie
Za podstawowe narzędzie doskonalenia zarówno całych organizacji, jak i wybranych jej procesów, w tym związanych z utrzymaniem ruchu, uznaje się cykl Deminga. Jest on także określany jako cykl PDCA (ang. Plan-Do-Check-Act) lub cykl P-D-S-A (ang. Plan-Do-Study-Act) lub po prostu jako koło Deminga. Narzędzie to stanowią chronologicznie uporządkowane działania, które są typowe dla układu sterowania ze sprzężeniem zwrotnym. Pierwszym działaniem jest planowanie, czyli określenie działań niezbędnych do otrzymania efektu najwyższej jakości. Następny etap przewiduje wdrożenie działań zgodnie z przyjętym planem. W cyklu Deminga istotną rolę odgrywa ocena wykonania. Jest to sprawdzenie skuteczności zrealizowanego planu również pod kątem jego dalszej poprawy. Ostatni, , czwarty etap to doskonalenie procesu oraz zainicjowanie pomysłów do kolejnego planu. Tym sposobem koło Deminga zamyka się, tworząc proces ciągłego działania, a co najważniejsze, doskonalenia.
Mówiąc o infrastrukturze przemysłowej warto zwrócić uwagę na stopień wykorzystania (ang. utilization), a także liczbę oraz rodzaj przestojów (ang. downtimes). Nie bez znaczenia pozostaje monitorowanie postępu realizacji zleceń produkcyjnych w stosunku do przyjętych planów.
Damian Żabicki