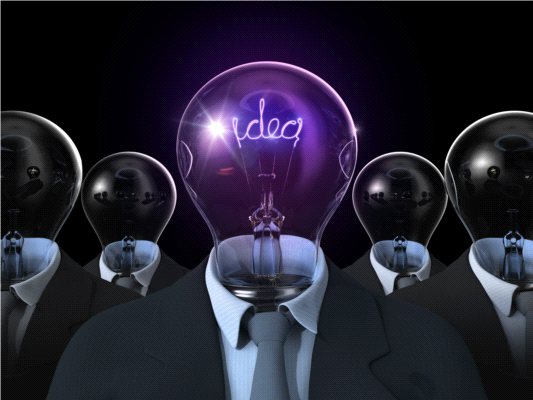
Efekt góry lodowej
Kontynuując nasze rozważania na temat systemów ciągłego doskonalenia, zanim przejdziemy dalej, postawimy w tym miejscu kropkę nad „i” i zastanowimy się, o jakim modelu zarządzania mówimy. Jeżeli pod uwagę brana jest działalność handlowa, usługowa czy produkcyjna, to właśnie...
Wyobrażając sobie idealny model zarządzania produkcją, trzeba dokładnie zastanowić się, jaki powinien on być. Mówi się, że są to procesy tak zorganizowane, aby przynosić tylko wartość dodaną – elastyczne, bezbłędne, bezpieczne i tanie w utrzymaniu. Czy gdzieś to osiągnięto? Wydaje się że tak – Toyota wyznaczyła taki model. Ale czy jest on ostateczny? Oczywiście, że nie. Nowe technologie, w tym platformy społecznościowe, powoli zmieniają postrzeganie organizacji pracy. Ciągle jednak większość zakładów produkcyjnych jest osadzona w taylorowskim modelu z intuicyjnym sposobem zarządzania. Efekt? Wysokie koszty zarządzania. Należy stwierdzić z przykrością, że uczelnie wyższe niestety oferują wiedzę o niskiej jakości, w oderwaniu od praktyki i, mimo wprowadzania różnych programów wspieranych z funduszy unijnych mających na celu połączenie wysiłków uczelni i przemysłu, proces ten nadal się utrzymuje. Druga strona medalu to menedżerowie wykształceni w zupełnie innych kierunkach lub wręcz bez wykształcenia, zarządzający intuicyjnie procesami produkcyjnymi. Wiele osób zaciekawi pewnie fakt, że model organizacji naszych zakładów nie zmienił się od rewolucji przemysłowej i wzorowany jest ciągle na organizacji armii pruskiej. Zainteresowanych odsyłam do bardzo ciekawego wykładu Pana profesora A. Blikle wygłoszonego podczas międzynarodowej konferencji 6Sigma we Wrocławiu.
Jak wieloma obszarami należy zarządzać? Bezpieczeństwo, organizacja pracy, autonomiczne i profesjonalne utrzymanie ruchu, logistyka, nowe uruchomienia, środowisko, a do tego sterowanie jakością, zarządzanie stratami, ukierunkowana poprawa czy wreszcie rozwój kompetencji personelu – jak widać, jest to prawdziwe wyzwanie.
Kierujemy czy koordynujemy?
Producenci chcący stworzyć model szczupłej produkcji w swoich fabrykach najczęściej tworzą komórkę organizacyjna występującą pod nazwą Lean, Kaizen itp. lub zatrudniają inżyniera „ciągłego doskonalenia” (cokolwiek by to miało znaczyć). Jaka w takim razie jest rola takiej osoby w organizacji? Właściwie istnieją dwa sposoby zarządzania – kierowanie i koordynowanie. Na czym polega różnica? Kierownik zarządza/kieruje zasobami ludzkimi, będąc jednocześnie ich przełożonym dyscyplinarnym. Co to znaczy? Może wydawać polecenia, a w razie ich nie wykonania ma do dyspozycji narzędzia, które może w określonej sytuacji użyć, chcąc zastosować sankcje. Tutaj właściwie jest sprawa jasna i intuicyjnie wiadomo, że kierować jest dużo łatwiej niż koordynować. Czym w takim razie jest koordynowanie? W tym wypadku nie istnieje prosta zależność dyscyplinarna. Co w takim razie robić? Sprawa wydaje się skomplikowana, jednak są na to sposoby. Koordynator ma za zadanie kierować grupą ludzi, aby osiągnąć założone cele, w tym wypadku: wdrożenie systemu ciągłego doskonalenia, który ma działać. Dodając, że zazwyczaj jest to grupa kierowników poszczególnych obszarów, czyli osób, które stoją na stanowisku, że wiedzą lepiej, pracują dłużej i właściwie nie mają czasu na takie rzeczy. Sytuacja staje się nieciekawa i frustrująca, ale tylko pod warunkiem, że do końca nie wie się, jak koordynować.
Prof. H. Yamashina twierdzi, że w dobrze zarządzanym przedsiębiorstwie można zidentyfikować co najmniej 30 procent marnotrawstw
Grunt pod działanie
Po pierwsze, koordynator musi stworzyć pewien umowny regulamin na samym początku swojej działalności, czyli umówić się z członkami zespołu na pewne zasady, np.: zadania są wykonywane w terminie i raportowanie następuje zaraz po ich wykonaniu, spotkania są obligatoryjne i obecność na nich jest obowiązkowa, itd. Drugim krokiem jest stworzenie kanałów eskalacji w wypadku nie dotrzymywania zasad przez członków zespołu, na które się umówiono. W tym wypadku należy zdobyć bezwzględne poparcie osoby najbardziej decyzyjnej w zakładzie, co więcej, ta osoba musi w sposób jasny dać do zrozumienia całej organizacji, że jest to dla niej ważny projekt, i nie realizowanie zadań może mieć negatywne konsekwencje. Teraz sprawa wydaje się być dużo łatwiejsza.
Czy wiemy na co się decydujemy?
Nie tak dawno menedżer podejmujący nowe stanowisko dyrektora jakości w prywatnej firmie posiadającej kilka fabryk, produkującej dla przemysłu motoryzacyjnego na Śląsku, zwrócił się do mnie z zapytaniem o wdrożenie ISO TS 16949 i ISO 9001, gdyż zarząd jego firmy koniecznie chce mieć oba certyfikaty. ISO TS właściwie jest zbudowany na normie 9001 plus pięć pewnych elementów, czyli automatycznie zdobywając certyfikat na zgodność z normą ISO TS spełniamy wymagania ISO 9001. Nadmienić należy, że skoro ISO 9001 to przedszkole, to TS 16949 powiedzmy – gimnazjum. W tym wypadku o tyle sprawa jest jasna, że jest to norma i cała ścieżka certyfikacji jest znormalizowana . Kto w takim razie ma wytłumaczyć to zarządowi? Wiedza stanowi klucz do sukcesu.
Szyte na wymiar
System powinien być dopasowany do danego zakładu, czyli jego wielkości, charakteru działalności itd. Osoby nie znające do końca tematyki bardzo często upierają się przy jednym narzędziu np. Lean w postaci VSM (mapowania strumieni wartości), jakby było to jedyne lekarstwo na bolączki firmy. Jeżeli mówimy o profesjonalnym podejściu do budowy takiego sytemu, powinniśmy zaczerpnąć szerszej wiedzy, skorzystać np. z wiedzy konsultantów. Takie systemy również można projektować dla specyficznych potrzeb zakładu, w innym razie, biorąc cały inwentarz danego podejścia, możemy albo w ogóle nie wystartować, tzn. zatrzymać się na działaniach 5S, albo zbudować monstrum, które pod własnym ciężarem się zawali.
Osoby nie znające do końca tematyki bardzo często upierają się przy jednym narzędziu np. Lean w postaci VSM (mapowania strumieni wartości), jakby było to jedyne lekarstwo na bolączki firmy
Przede wszystkim myślenie
Co więc z ciągłym doskonaleniem? Ponieważ te zasady jak dotąd nie dają się znormalizować, sprawa wydaje się o wiele trudniejsza. Cała idea ciągłego doskonalenia opiera się na redukcji marnotrawstwa, co często jest związane z pewną filozofią, sposobem myślenia. Należy to podkreślić, powtarzać, gdyż Zachód mówi często o technikach, narzędziach, metodach, a Japończycy, mistrzowie Lean, uczą o myśleniu i zawsze to słowo akcentują. Więc „myślenie”, a co za tym idzie, postawa i zaangażowanie.
Obserwacje pozwoliły zdefiniować 8 podstawowych marnotrawstw, które w połączeniu z filozofią Kaizen stały się podstawą, punktem wyjścia powstania „Lean Thinking”. W zupełnie innej kulturze wzrastała idea Six Sigma, która również stała się podstawą budowy systemu opartego o metodykę DMAIC, gdzie wszelkie decyzje podejmowane są na podstawie liczb, danych, faktów.
Droga TPS – od czego zacząć
Wróćmy jednak do naszego modelu TPS (Toyota Production System). Co więc jest potrzebne w zakładzie, co wybrać, aby osiągnąć sukces? Rozpoczynając przygodę z World Class Manufacturing, szybko można się zorientować, że jest to właściwie kwintesencja TPS. Poszukujący mogą znaleźć tu wszystkie do tej pory poznane sposoby, metody, narzędzia, zamykając w jedną całość odpowiedzi na każde nurtujące pytanie dotyczące zarządzania czy optymalizacji produkcji. Co więcej, idąc dalej widzi się logiczną całość działań, które wpływają, zazębiają się czy wreszcie uzupełniają wzajemnie po to, by zakład mógł rozwijać się harmonijnie.
Co stanowiłoby więc bazę wyjściowa do projektowania systemu wg modelu WCM w wydaniu japońskim, który obejmuje swym zasięgiem wszystkie obszary, a co za tym idzie, problemy całej organizacji?
Punkt wyjścia do projektowania systemów stanowi pytanie, z czym mamy tak naprawdę największy problem w organizacji i co chcielibyśmy poprawić. Musimy również sobie odpowiedzieć, czy chcemy w sposób usystematyzowany zarządzać tymi problemami czy po prostu ad hoc od przypadku do przypadku zajmować się nimi dopiero wtedy, gdy nas naprawdę zabolą.
Marnotrawstwa są wszędzie
Tak naprawdę zarządzamy tylko tym, co widzimy lub nam się wydaje, że zarządzamy, a co z całą resztą? Pan prof. Leszek Balcerowicz powiedział: „Wygląda na to, że jedyną receptą powinny być cięcia wydatków. (…) Niestety tam, gdzie brakuje pieniędzy, tam jest marnotrawstwo. Nie mówmy więc o cięciu wydatków, ale o cięciu marnotrawstwa”. To zdanie idealnie można odnieść do sposobu zarządzania produkcją i stanowi również podstawę systemów ciągłego doskonalenia.
Pytanie czy kierownicy uświadamiają sobie, jakie koszty ponoszą w związku z marnotrawstwami, które pojawiają się w zakładzie? Jest tego bardzo dużo w każdym zakładzie, mimo że na pierwszy rzut oka tego nie widać. Prof. H. Yamashina twierdzi, że w dobrze zarządzanym przedsiębiorstwie można zidentyfikować co najmniej 30 procent marnotrawstw. Pytanie ile można zidentyfikować marnotrawstw tam, gdzie się nimi nie zarządza, zostawiam Czytelnikom.
Kiedyś prezydent koncernu Panasonic, Konosuke Matsushita, powiedział: „To my zwyciężymy, przegra zaś przemysłowy zachód; nie bardzo możecie temu zaradzić, ponieważ przyczyny waszej przegranej są w was. Wasze firmy są zbudowane według modelu Taylora, gorzej, wasze głowy są też tak zbudowane”. No cóż, musimy się zmieniać.
W dalszej części spróbujemy rozwinąć tematykę marnotrawstw odnosząc się do historycznego swoistego joint venture japońsko-amerykańskiego, bez którego nie powstałby w takim kształcie system produkcji Toyoty, a co za tym idzie, nie mielibyśmy wzorców, z których moglibyśmy czerpać wiedzę doskonaląc zarządzanie.