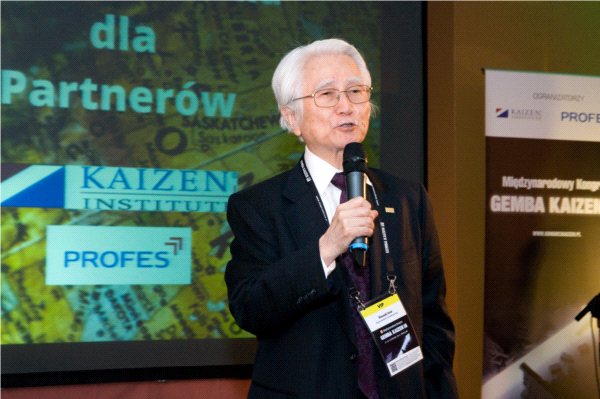
Kaizen to DNA Toyoty
Z Masaaki Imai, światowym guru ciągłego doskonalenia Kaizen, rozmawia Przemysław Ozga.Jak definiuje Kaizen guru ciągłego doskonalenia, Masaaki Imai?
Stary paradygmat Kaizen mówi, że zawsze istnieje lepsza droga, aby wykonać dane zadanie, pracę. Nowa definicja Kaizen,...
Jak definiuje Kaizen guru ciągłego doskonalenia, Masaaki Imai?
Stary paradygmat Kaizen mówi, że zawsze istnieje lepsza droga, aby wykonać dane zadanie, pracę. Nowa definicja Kaizen, według mnie, to ciągłe doskonalenie każdego elementu organizacji, począwszy od małych stopniowych udoskonaleń, skończywszy na wielkich strategicznych udoskonaleniach. Kaizen to stan umysłu, paradygmat nie pozwalający cieszyć się z tego, co zastajemy danego dnia i to nie tylko w firmie, ale również w życiu prywatnym. Ciągłe doskonalenie powinno angażować wszystkie osoby w przedsiębiorstwie, od prezesa po podstawowych pracowników. Top management nie może traktować narzędzi Kaizen jako coś wyłącznie przeznaczonego dla pracowników linii produkcyjnej. Do obowiązków menedżerów należy właściwa postawa przejawiająca się w okazywaniu odpowiedniej determinacji we wdrażaniu technik ciągłego doskonalenia oraz ustanowienia długofalowej strategii na tym polu, ponieważ Kaizen jest długofalowym wyzwaniem.
Dostosowanie linii produkcyjnej do gwałtownych wahań popytu nie jest dla szczupłej organizacji problemem
Przed większością firm produkcyjnych stoją trzy podstawowe zadania: zaprojektowanie produktu, wyprodukowanie go oraz sprzedanie. W wielu z tych przedsiębiorstw top management, interesując się m.in. procesami projektowania, technologiami, inżynierią, zaniedbuje mniej „spektakularną” produkcję. Menedżerowie często uważają, że produkcja to nie ich obowiązek, mają ważniejsze sprawy na głowie. Taka postawa sprawia, że cierpi na tym cała firma. Menedżer, jak już wspomniałem, powinien być szczególnie zaangażowany w doskonalenie wszystkich procesów swojej firmy, winien wykorzystywać metodę Gemba Kaizen.
Jak ważne miejsce w całej filozofii Lean zajmuje Kaizen?
Lean zaczyna się od Kaizen i z biegiem czasu angażuje wszystkich pracowników danej organizacji. Toyota jest firmą, która pod względem mentalnym kładzie największy nacisk na Kaizen spośród wszystkich japońskich firm. Można powiedzieć, że Kaizen to DNA Toyoty. Eiji Toyoda mawiał, że jeśli wejdziesz do fabryki Toyoty, poczujesz Kaizen w powietrzu, będziesz nim oddychał.
Czy szczupła produkcja może być remedium na trudne czasy rynkowe?
Należy pamiętać, że system oparty na szczupłej produkcji jest doskonały nie tylko podczas dobrej koniunktury, ale również, gdy nastają trudne czasy. Wysoka elastyczność systemu produkcyjnego Toyoty pozwala podczas recesji dopasować się do nowych warunków, przez co nawet przy dużym spadku popytu produkcja samochodów jest nadal rentowna. Dostosowanie linii produkcyjnej do gwałtownych wahań popytu nie jest dla szczupłej organizacji problemem, ponieważ produkcja opiera się jedynie na aktualnych zamówieniach klientów. Dzięki temu Toyota posiada wiedzę o rynku, która w przypadku niespodziewanych spadków lub wzrostów obrotów pozwala szybko dostrzec i wyciągnąć wnioski z niepokojących tendencji ekonomicznych. Tak było na przykład w latach siedemdziesiątych, gdy nadeszła ogólnoświatowa recesja. Toyota była wówczas pierwszą firmą, która to zauważyła i zareagowała ograniczeniem mocy produkcyjnych w swoich fabrykach. Później, po pierwszych oznakach ożywienia, firma jako pierwsza zaczęła zwiększać moce wytwórcze. Taka racjonalizacja nie była możliwa w przypadku innych firm, które miały wiele niesprzedanych samochodów, mnóstwo procesów w toku niedopasowanych do aktualnych zamówień, gdyż tradycyjne firmy motoryzacyjne, takie jak General Motors czy Ford, opierają produkcję o prognozy sprzedaży, a nie o bieżące zamówienia.
W swoich wystąpieniach i książkach robi pan wyraźny podział na firmy tradycyjne i Lean.
W dzisiejszym świecie istnieją dwa rodzaje firm. Pierwsze z nich nazywam firmami tradycyjnymi. Typowym przedstawicielem przedsiębiorstwa tradycyjnego jest obecnie General Motors. Drugi rodzaj firm praktykuje techniki Kaizen i są te firmy w swym działaniu Lean. Taką właśnie organizacją jest Toyota.
Jakie różnice może pan wskazać pomiędzy dwoma modelowymi przykładami obu typów organizacji?
Tradycyjne firmy wykorzystują maksymalne zasoby: to jest surowce, materiały, przestrzeń, pieniądze, najdroższe maszyny, do minimalnej produkcji. Przez minimalną produkcję rozumiem tutaj minimalne wymagania klienta. Na tym polu firma Lean stanowi odwrotność tradycyjnego przedsiębiorstwa. Dominują w niej minimalne zasoby i surowce wykorzystywane do produkcji maksymalnie dopasowanej do wymagań klienta. Jak łatwo zauważyć, koszt operacyjny w firmach tradycyjnych jest o wiele wyższy.
Kolejną różnicą jest fakt, że firma Lean nastawiona jest na wytwarzanie jak najlepszej możliwej jakości. Ułatwieniem w tym przypadku jest przypisywanie w szczupłej firmie mniejszej ilości ludzi do danego procesu, a mniejsza ilość ludzi oznacza mniejszą liczbę potencjalnych błędów do popełnienia. Lean jest warunkiem zwiększenia jakości. Co dalej?
Należy pamiętać, że system oparty na szczupłej produkcji jest doskonały również na trudne czasy
W tradycyjnym modelu przedsiębiorstwo nastawione jest na tworzenie wartości dla akcjonariatu, gdyż to właśnie akcjonariusze są pojmowani jako główni klienci. Nacisk położony jest tym samym na finanse, osiąganie maksymalnych zysków w krótkim okresie czasu. W takiej firmie pracownicy postrzegani są jako koszty stałe. Jakakolwiek redukcja kosztów dokonywana jest poprzez ich cięcia, dodatkowo, jakość i koszt nie są ze sobą powiązane, nie są kompatybilne. Skala firmy tradycyjnej opiera się na paradygmacie: większy i szybszy znaczy lepszy – przedsiębiorstwo robi wszystko, aby rosnąć, stawać się coraz większe. Traktowane jest to jako warunek osiągania większych zysków, warunek sukcesu. Takie przedsiębiorstwo, w odróżnieniu od organizacji Lean, dopuszcza większe zapasy. W nastawieniu na zmiany dominuje brak elastyczności wobec zróżnicowanego rynku.
W przedsiębiorstwach Lean oczywiście akcjonariusze są ważni, ale jeszcze ważniejsza jest satysfakcja klienta. Kluczową rolę gra rozwój procesów operacyjnych odbywający się w długim czasie poprzez wdrażanie kolejnych technik, takich jak Jidohka, Kaizen, JIT, itd. Wymienione przez mnie narzędzia wymagają od firmy cierpliwości. W szczupłych firmach pracownicy traktowani są jako środki trwałe, redukcja kosztów osiągana jest dzięki właściwemu zarządzaniu, przy wdrażaniu technik Lean i osiąganym dzięki temu efektom. Koszty będą szły w dół ze względu na realizację żądań klientów odnośnie wysokiej jakości i niskich cen, przy czym oba czynniki muszą być kompatybilne. Rozmiar, wielkość oraz szybkość działania organizacji Lean są adekwatne do istniejących warunków rynkowych. Taka firma, w odróżnieniu od tradycyjnych organizacji, dąży do jak największej redukcji zapasów. I w końcu, co nie mniej ważne: jedną z głównych różnic pomiędzy organizacjami Lean i tradycyjnymi jest wysoka elastyczność tych pierwszych wobec nagłych zmian i zróżnicowań rynkowych.
Wielokrotnie podkreśla pan znajomość z Taiichi Ohno. Na czym polegał sukces jego koncepcji produkcji? Jak wyglądała słynna droga, która doprowadziła do powstania Toyota Production System?
Zanim Taiichi Ohno stworzył Toyota Production System, nie istniało pojecie Lean – był jeden system produkcji samochodów: amerykański Forda. System ten oparty był na masowej produkcji: zaawansowane maszyny wykorzystywały efekt skali w celu obniżenia kosztu pojedynczego produktu. W owym czasie produktywność amerykańskiego przemysłu była w przybliżeniu dziewięciokrotnie wyższa niż japońska. Wynalezienie sposobu produkcji było dla Toyoty jednym z warunków przetrwania firmy po przegranej wojnie. W firmie stwierdzono wówczas, że jeśli Toyota nie osiągnie poziomu amerykańskiego w przeciągu trzech lat, koncern nie będzie miał szans na przetrwanie. Recesja, która przyszła do Japonii, sprawiła, że zakłady Toyoty oparte na amerykańskim systemie produkcyjnym popadły w kłopoty finansowe m.in. ze względu na zbyt duże zasoby. Stworzone w tym czasie w Japonii konsorcjum bankowe było gotowe wesprzeć Toyotę w trudnym okresie rynkowym, stawiało jednak pewien niepodważalny warunek: znaczną redukcję personelu. Toyota na to przystała.
Mając mniej pracowników pod sobą, Taiichi Ohno zrozumiał, że produktywność nie leży wyłącznie w maszynach, ale również w ludziach. Jako menedżer zarządzający pięciuset pracownikami zaczął obserwować ich pracę i zauważył wiele niedodających wartości czynności wykonywanych podczas procesów produkcyjnych. Doszedł do wniosku, że aby zwiększyć produktywność, jeden człowiek powinien obsługiwać więcej maszyn. Podczas przeprowadzanych testów wszystkie działania i aktywności niedodające wartości stopniowo eliminowano. Okazało się, że jeden operator może obsługiwać trzy, a później cztery maszyny, pod warunkiem ich właściwego ustawienia. Tak powstała koncepcja Multiplay Machine Handling.
Następnie Taiichi Ohno dostrzegł, że każda z maszyn wykazuje inne tempo pracy, nakazał więc operatorom obsługę maszyn różnego typu, przeznaczonych do niejednorodnych procesów. Zmieniono jednocześnie flow, czyli przepływ produkcji; wprowadzono jednolite, zsynchronizowane takty procesowe, dzięki czemu zmniejszono ilość ludzi potrzebnych na danym odcinku linii średnio z piętnastu do dwóch. Taka była geneza Toyota Production System.
Od czego ma zacząć polska firma produkcyjna, która zdecyduje się na przyjęcie filozofii Lean?
Proszę pamiętać, że w trakcie powstawiania systemu produkcyjnego Toyoty nie było trenerów od Kaizen, książek o Lean i składających się na nie technikach, a wszystkie wspomniane rozwiązania powstawały na żywym organizmie. Teraz firmy mogą korzystać z narzędzi stworzonych przez Ohno w przeszłości, ale najpierw muszą koniecznie określić swoje najpilniejsze cele i zadania, ponieważ nie istnieje jedna prosta odpowiedź na wszystkie problemy, jakie napotyka firma.