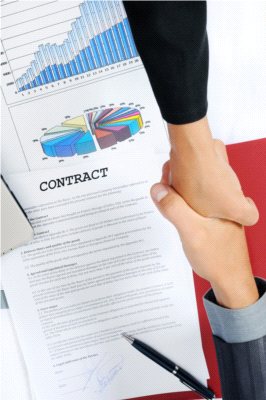
Outsourcing kontroli jakości
Na końcowy efekt w postaci produktu o wysokiej jakości składa się wiele czynników: wykwalifikowana kadra, odpowiednie zaplecze logistyczne, wysokiej jakości komponenty dostarczane do montażu. Ich osiągnięcie ułatwiają firmy outsourcingowe proponujące usługi związane z kontrolą...
Każde przedsiębiorstwo, które chce konkurować zarówno na rynku polskim, jak i za granicą, musi sprostać coraz większym wymaganiom stawianym przez klientów. Dotyczą one takich obszarów jak: jakość, logistyka, gwarancje czy też elastyczność w realizacji zamówień. Już nie same koszty wytwarzania i finalna cena produktu wpływają na zainteresowanie klientów, ale także relatywnie krótki czas reakcji przedsiębiorstwa na wydarzenia na rynku, zrozumienie i spełnienie oczekiwań klienta oraz umiejętność natychmiastowego dostosowania się do wahań liczby zamówień. W związku z tym wśród firm produkujących czy to samochody, sprzęt AGD czy produkty FMCG poszukuje się innowacyjnych rozwiązań w zakresie zarządzania zasobami ludzkimi i procesami produkcyjnymi, które finalnie zagwarantują „gotowy wyrób” o odpowiednich parametrach i właściwościach.
Firmy specjalizujące się w kontroli jakości aktywnie uczestniczą w procesie rozwoju dostawców i mobilizowaniu ich do poprawy jakości swojej produkcji
Poszukiwany outsourcing
Coraz częściej wybierane są rozwiązania proponowane przez firmy wyspecjalizowane w kontroli jakości. Firmy świadczące tego typu usługi stają się strategicznymi partnerami biznesowymi firm produkcyjnych, gwarantującymi bezpieczeństwo, elastyczność i redukcję kosztów. Popyt na outsourcing kompleksowych rozwiązań w zakresie kontroli jakości rokrocznie rośnie. Większość firm działających m.in. na rynku Automotive dąży do uelastycznienia swojego biznesu tak, aby szybciej i łatwiej reagować na czynniki zewnętrzne i ograniczyć niepotrzebne koszty.
Rola firmy outsourcingowej
Przed każdym dostawcą komponentów stawiane są bardzo wysokie wymogi jakościowe. Łatwo ich nie spełnić, a to generuje spore koszty. Wystarczy nagły wzrost zamówień, niestabilność procesu czy błąd operatora, aby proces produkcyjny się skomplikował. W sytuacji gdy klient otrzymuje niezgodną dostawę, z której części i komponenty nie mogą zostać użyte w dalszym procesie montażowym, zakład produkcyjny musi liczyć się z ryzykiem zatrzymania linii montażowej ze względu na brak pewności co do jakości komponentów. Tutaj ważną rolę odgrywają zewnętrzne firmy zajmujące się kontrolą jakości, m.in. selekcją, naprawą i sortowaniem części, komponentów oraz wyrobów gotowych do montażu. Klient–zakład montujący w sytuacji kryzysowej oczekuje od dostawcy natychmiastowej reakcji i rozwiązania problemu. Wówczas dostawca ma możliwość posiłkowania się taką firmą outsourcingową, której zleci przeprowadzenie selekcji w celu zabezpieczenia ciągłości produkcji swojemu klientowi.
Popyt na outsourcing kompleksowych rozwiązań w zakresie kontroli jakości rokrocznie rośnie
Standardowy czas, jaki firma outsourcingowa potrzebuje na przystąpienie do pracy, nie przekracza nawet 60 minut. Jest to czas, w którym inspektorzy jakości pod nadzorem wyznaczonego koordynatora przystępują do wykonania selekcji, kontroli czy też naprawy części. Warto podkreślić, że taka usługa jest wykonywana na podstawie sporządzonej przez zainteresowane strony tzw. specyfikacji kontroli. Po wykonaniu powierzonego zadania dostawca oraz jego klient otrzymują szczegółowy raport o wynikach przeprowadzonej kontroli, a wadliwe części zostają odseparowane i zabezpieczone tak, aby nie przedostały się na linię produkcyjną.
Kontrola krok po kroku (4 podstawowe etapy)
Etap I – PRZYJĘCIE ZLECENIA
Do obsługi każdego klienta przydzielony jest koordynator. Osoba ta jest odpowiedzialna za przyjęcie zlecenia do realizacji oraz za przystąpienie do rozpoczęcia akcji w ciągu 60 minut od momentu powiadomienia przez klienta. Krótki czas reakcji ma za zadanie wyeliminować ryzyko zatrzymania linii montażowej klienta ze względu na brak zgodnych komponentów lub opóźnianie wysyłki w przypadku, gdy przedmiotem zlecenia są wyroby gotowe – czyli produkt finalny przeznaczony na wysyłkę do odbiorcy. Koordynator wspólnie z klientem ustala szczegółowe kryteria i wymagania co do danego zlecenia. Na podstawie otrzymanych wytycznych koordynator wypełnia specyfikację kontroli.
Etap II – REALIZACJA ZLECENIA
Po ustaleniu szczegółów zlecenia koordynator pobiera komponenty/detale do kontroli i we wskazanym miejscu rozpoczyna efektywną pracę wraz z odpowiednio dobraną liczbą kontrolerów. W przypadku wątpliwości odnośnie sposobu wykonania zlecenia lub pojawienia się nieprzewidywalnych okoliczności (np. wykrycie kolejnej wady) następuje konsultacja z klientem bądź czasowe przerwanie realizacji zlecenia, aż do momentu wyjaśnienia niezgodności.
Etap III – ZAKOŃCZENIE ZLECENIA
Bezpośrednio po wykonanym zleceniu następuje przekazanie klientowi komponentów/detali. Każda partia elementów po kontroli jest odpowiednio oznaczona, aby późniejsza ich identyfikacja nie sprawiała trudności.
Etap IV – RAPORTOWANIE WYNIKÓW
Po zakończeniu zlecenia klientowi zostaje przedstawiony raport dzienny. Dokument zawiera szczegółowe informacje dotyczące efektów przeprowadzonego zlecenia (ilości skontrolowane z podziałem na części zgodne i niezgodne, Pareto wad, itp.). Dodatkowo wyniki wszelkich prac wykonywanych dla klientów wprowadzane są do systemu raportowania on-line EXTRANET. Dzięki temu każdy klient (jak również dostawca, jeśli zlecenie realizowane jest na jego rzecz) otrzymuje login i hasło dostępu, które umożliwiają wgląd w wyniki zleconych prac i ich bieżący monitoring przez 24h/dobę via Internet.
Korzyści jest wiele
Lista korzyści ze współpracy z firmą outsourcingową znacznie wykracza poza działania doraźne. Po pierwsze, zewnętrzny partner zapewnia kompleksową obsługę związaną ze świadomym sterowaniem jakością procesu produkcyjnego. Bardzo często zdarza się tak, że wyniki jego pracy stanowią pierwszą szczegółową analizę wadliwości produkcji, która jak każde odstępstwo od normy, musi zostać opisana, a następnie wyeliminowana. Po drugie, praca wykonywana przez „kontrolerów jakości” pozwala dostawcom uniknąć ogromnych kosztów związanych z błędnie zrealizowanym zamówieniem klienta. Istotne jest również to, że firmy specjalizujące się w kontroli jakości aktywnie uczestniczą w procesie rozwoju dostawców i mobilizowaniu ich do poprawy jakości swojej produkcji, co przekłada się wprost na dostarczenie zgodnych ze specyfikacją jakościową części na linię produkcyjną. Wprowadzenie systematycznego monitoringu jakości pozwala na ochronę przed konsekwencjami błędów ludzkich i materiałowych.
Popyt na outsourcing rośnie
Outsourcing kontroli jakości części i komponentów popularność zdobywa nie tylko na rynku Automotive, co potwierdza m.in. różnorodność realizowanych projektów przez Exact Systems. Wśród głównych odbiorców naszych usług są dostawcy i poddostawcy dla przemysłu motoryzacyjnego oraz producenci samochodów. Jednak rokrocznie nasz portfel uzupełniamy o zakłady zajmujące się produkcją wielkoseryjną w branży elektronicznej, AGD. Od pewnego czasu także branże kosmetyczna oraz farmaceutyczna są zainteresowane współpracą i transferem naszych doświadczeń z sektora motoryzacyjnego. Warto także podkreślić, że z usług polskich firm outsourcingowych korzystają już nie tylko polskie zakłady produkcyjne. Rozwijającą się polską bazą kontroli jakości coraz częściej zainteresowane są firmy działające na rynkach zagranicznych.