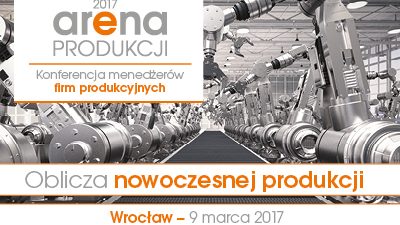
Czwarta edycja konferencji Arena Produkcji – a druga we Wrocławiu – już za nami. Z nieukrywaną dumą możemy ogłosić kolejny sukces na polu integracji środowiska produkcji i szerzenia wiedzy na temat najlepszych praktyk w zarządzaniu przedsiębiorstwem. Ponad 200 uczestników, reprezentujących mniej i bardziej znane firmy produkcyjne działające w Polsce, nie mogło się nudzić.
Tradycyjnie już postawiliśmy na bardzo szeroki zakres tematyczny wystąpień. Prelekcje łączyło hasło „Oblicza nowoczesnej produkcji”. I choć tematy bywały mocno zróżnicowane, okazało się, że w większości z wystąpień rzeczywiście można znaleźć wspólny mianownik.
Optymalizacja logistyki wewnętrznej
Anna Weydmann-Kwiatkowska, Lider Zespołu Lean Manufacturing, rozpoczęła Arenę Produkcji od prezentacji przykładów optymalizacji logistyki wewnętrznej w firmie Arjhuntleigh. Arjohuntleigh, należące do Gettinge Group, oferuje rozwiązania dla pacjentów z ograniczoną mobilnością. Łóżka, materace przeciwodleżynowe czy podnośniki mają zapewnić chorym komfort i bezpieczeństwo. Arjohuntleigh Polska posiada fabrykę w Komornikach pod Poznaniem, a portfolio produktów tego zakładu jest sukcesywnie powiększane.
Firma od lat korzysta z narzędzi Lean Management w procesach doskonalenia operacji. Prelegentka szczegółowo przedstawiła przebieg optymalizacji procesu produkcji podnośnika Carino, którego wytwarzanie fabryk w Komornikach przejęła z zamkniętego zakładu w Szwecji. Zespół optymalizacyjny rozpoczął prace od identyfikacji czynności przynoszących wartość oraz wskazania źródeł marnotrawstwa. Logistyka produkcji okazała się jednym z jego największych źródeł – operatorzy na początku zmiany dużo czasu poświęcali na przekładanie dostarczanych komponentów ze skrzyniopalet do kuwet, chodzenie po części czy przekładanie stelaży, dla których nie było dedykowanych miejsc odkładczych.
Aby usprawnić sytuację, do transportu wewnętrznego przygotowane zostały wózki z kuwetami na detale, oraz specjalne zaprojektowane duże wózki na stelaże. W efekcie tych zmian i przeprojektowania layoutu, operatorzy nie tracili już czasu na zbędne przepakowywanie, dzienna wydajność wzrosła o 12%, zaś udział czynności dodających wartość w procesie produkcyjnym wzrósł do 74%.
Sukces tego projektu skłonił zachęcił zespół wdrażający Lean do dalszych usprawnień. Optymalizację logistyki wewnętrznej przeprowadzono na linii produkcyjnej wózków LG/Akron. Dużym sukcesem okazał się pomysł na zmianę opakowań dostarczanych paneli. Dostawca przystał na rezygnację z opakowań foliowych i zaczął dostarczać elementy w specjalnych, kartonowych wypraskach. W efekcie nie tylko oszczędzono czas potrzebny na rozpakowywanie paneli w fabryce, ale też wskutek likwidacji foliowego opakowania zanotowano korzyści ekologiczne.
Komunikacja ważniejsza od narzędzi
Dariusz Kacperczyk i Michał Żelichowski z EQ System poprowadzili drugie wystąpienie. Reprezentanci dostawcy zaawansowanych rozwiązań IT dla produkcji podzielili się swoimi refleksjami na temat sposobów, w jaki firmy produkcyjne powinny zmieniać swoje podejście do prowadzenia operacji, aby stać się naprawdę nowoczesnymi przedsiębiorstwami.
Dariusz Kacperczyk przekonywał zebranych, że warto patrzeć na doświadczenia innych, gdyż po spojrzeniu z odpowiedniej perspektywy okazuje się, że procesy we wszystkich firmach produkcyjnych są takie same. Stwierdził też, że Przemysł 4.0 to idea, która dotknie wszystkich producentów i na dłuższą metę nie ma od niej ucieczki. Jednak kluczem do wdrażania wszelkich nowoczesnych rozwiązań jest umiejętność uzyskania wewnętrznej synergii w przedsiębiorstwach.
Tymczasem, jak zauważył pan Dariusz, niezwykle często widoczne jest niezrozumienie procesów pomiędzy poszczególnymi działami w firmie produkcyjnej. Co więcej zdarza się, że jeden wydział produkcyjny nie wie nawet, czym zajmuje się drugi. Bez przełamania tych barier nie ma szans na wdrożenie zasad nowoczesnej produkcji.
Potwierdzał to Michał Żelichowski, który w swojej części mówił o znaczeniu komunikacji w rozwoju przedsiębiorstw. Nie uda się wykorzystać zaawansowanych technologii, jeżeli nie towarzyszy im postęp organizacyjny w firmie. Dlatego też nowe narzędzia nie zawsze są rozwiązaniem problemów. Przykładem tego była sytuacja w Strauss Cafe, które zamiast nowego systemu informatycznego potrzebowało zmiany organizacji pracy, w czym pomogło EQ System.
Roboty i efektywność
Michał Ochański z firmy Comau podzielił się w uczestnikami swoim spojrzeniem na kwestię robotyzacji przedsiębiorstw produkcyjnych w Polsce. Comau to lider rynku robotów, zaś wystąpienie pana Michała obfitowało w filmy, które prezentowały szereg ciekawych aplikacji robotów.
Prelegent sporo miejsca poświęcił statystykom i zwrócił uwagę na ogromną różnicę w gęstości robotyzacji między Polską a Niemcami, ale też na wyraźny dystans, jaki dzieli nas pod tym względem od Czech czy Słowacji. To oznacza, że jesteśmy bardzo zapóźnieni na tym polu, ale zarazem mamy duży potencjał do rozwoju. Okazało się też, że jeżeli chodzi o inne branże niż motoryzacyjna, to wcale nie wypadamy aż tak źle na tle południowych sąsiadów.
Inwestycje w roboty będą jednak konieczne – przesądza o tym szybkie starzenie się społeczeństwa oraz konieczność nadążania z najszybciej rozwijającymi się gospodarkami. Do 2030 roku utrzymywać się będą silne wzrosty w zapotrzebowaniu na żywność czy produkty, zaś pozycje liderów przemysłowych mogą się zmieniać.
Pan Michał pokrótce omówił rodzinę robotów Comau i wskazał ich rosnącą popularność w takich aplikacjach jak spawanie czy paletyzacja. Na koniec kilka słów poświęcił robotom współpracującym, które mogę przynieść rewolucję w automatyzacji procesów produkcyjnych.
Wyeliminować straty
Tomasz Sczepura, reprezentant firmy Dachser mówił podczas swojego wystąpienia o poszukiwaniu efektywności w logistyce. Pan Tomasz wielokrotnie odnosił się do poprzednich wystąpień, w których regularnie gościło słowo marnotrawstwo. Prelegent zachęcał, aby eliminować je nie tylko w fabrykach, ale w całych łańcuchach dostaw.
Pan Tomasz zauważył, że straty najczęściej generowane są na styku poszczególnych ogniw łańcucha dostaw. Dlatego też Dachser, w swojej koncepcji inteligentnej logistyki, skupia się na ograniczaniu kosztów pośrednich oraz spełnianiu oczekiwań każdego z działów partnera biznesowego. Każdy z tych nich wymaga innych informacji, każdy z działów ma szalenie różne oczekiwania, cele a przez to i potrzeby, stąd wpasowanie się bezpośrednio w te komórki gwarantuje opracowanie rozwiązań niespotykanych w skali makro.
Prelegent przestawił autorski system transportowy Dachsera, oparty o 2-poziomowe kontenery wymienne BDF. Wykorzystanie licznych punktów przeładunkowych – Eurohubów – zapewnia szybkie dostawy dzięki omijaniu ograniczeń, związanych z czasem pracy kierowców. Chlubą firmy jest wysoce rozwinięty system IT i całkowita eliminacja papierowych dokumentów przewozowych.
Narzędzia Przemysłu 4.0
Podczas konferencji nie mogło zabraknąć choć kilku słów o koncepcji Przemysłu 4.0. Daniel Oszczęda z firmy Balluff przybliżył zebranym swoje spojrzenie na możliwe zmiany w światowym przemyśle oraz rolę, jaką odegra w nich zaawansowana automatyka.
Prelegent zaznaczył, że wdrażanie rozwiązań Przemysłu 4.0 jest kluczowe, jeżeli polskie przedsiębiorstwa chcą utrzymać kontakt ze światową czołówką. W światowym rankingu konkurencyjności produkcyjnej opracowanym przez Delloite, Polska zajmuje aktualnie 15 miejsce. Prognozy na rok 2020, oparte na tempie rozwoju wykorzystania nowych technologii, wskazują jednak na spadek naszego kraju na 16 pozycję. Tymczasem Czechy zyskają kilka pozycji, zaś co warte uwagi, Chiny, opierające swoją potęgę na taniej sile roboczej, stracą pozycję lidera na rzecz USA.
W produkcji przyszłości kluczową rolę grać będą analityka predyktywna, zaawansowane materiały i inteligentne fabryki. Prelegent zwrócił uwagę na fakt, iż koszty dostępu do nowych technologii nieustannie spadają, przez co tym bardziej warto się nimi zainteresować.
Tymczasem np. tylko 1/4 przedsiębiorstw działających aktualnie w Polsce przedsiębiorstw na szerszą skalę wykorzystuje technologię RFID. Pan Daniel przedstawił jej możliwości, na przykładzie monitorowania stanu narzędzi skrawających, monitorowania form odlewniczych, śledzenia przepływu czy systemu e-Kanban.
Przepływ w VELUX-ie
Inga Róźycka i Mateusz Forlita przybyli na Arenę Produkcji z firmy VELUX, aby przestawić przykład reorganizacji dostaw w namysłowskiej fabryce koncernu. Podstawą projektu było poszukiwanie optymalnego przepływu, podporządkowany zaś został mu cały plan przebudowy fabryki.
VELUX produkuje okna dachowe, lecz pani Inga, która rozpoczęła prelekcję, podkreśliła, że firma poprzez swoje produkty dostarcza ludziom światło, świeże powietrze a co za tym idzie lepsze warunki do życia. Koncern obecny jest w 40 krajach, zaś w 17 z nich ma fabryki. Firma zatrudnia około 9500 osób, z czego około 3500 w Polsce. Polskie fabryki zlokalizowane są w Gnieźnie, Namysłowie oraz Wędkowach koło Tczewa, zaś dla firmy szczególnym powodem do dumy są liczne nagrody za zaangażowanie w zadowolenie i bezpieczeństwo pracowników.
Pani Inga w swojej pracy nie skupia na optymalizacji pracy tylko zakładu produkcyjnego, ale patrzy na jego rolę w całym łańcuchu wartości. Gdy VELUX postanowił przebudować swoje modele biznesowe i radykalnie skrócić czas między zamówieniem a dostawą, jednocześnie zwiększając ilość wariantów oferowanych produktów oraz stawiając na redukcję kosztów w łańcuchach dostaw, takie podejście doskonale się sprawdziło.
Aby osiągnąć zakładane cele, sięgnięto po narzędzia Lean Manufacturing. Prelegentka zaznaczyła jednak, że w procesie identyfikowania wartości nie skupiano się tylko na poszukiwaniu marnotrawstwa. Duży nacisk położono również na wskazanie silnych stron firmy, które stanowiły fundament pod nowy plan przepływu.
Pan Mateusz opowiedział o szczegółach projektu rozbudowy fabryki i reorganizacji dostaw. Najważniejszym elementem było zespolenie procesów logistycznych i produkcyjnych w ramach jednej hali magazynowo-produkcyjnej. Ciężarówki w dostawami wjeżdżają teraz do jej wnętrza, co prócz korzyści dla przepływu wpłynęło pozytywnie na aspekty ekologiczne. Dostawy na stanowiska produkcyjne realizowane są just-in-time, z wykorzystaniem ścieżki mleczarza. Goście konferencji poznali też kilka praktycznych przykładów zastosowanych rozwiązań.
Pani Inga zakończyła wystąpienie prezentacją efektów projektu. Jak zaznaczyła, opracowanie twardych wskaźników jest kluczowe przy raportowaniu przebiegu wdrożenia do zarządu. Przestrzegła jednak, aby nie wpaść pułapkę myślenia silosowego oraz kierowania się wybiórczymi KPI i podkreśliła, że zawsze najważniejsi są ludzie, gdyż bez ich nadzwyczajnego zaangażowania i pomysłowości nie da się bowiem osiągnąć nadzwyczajnych wyników.
Gospodarka obiegu zamkniętego
Koncepcja gospodarki okrężnej była punktem wyjścia dla wystąpienia Łukasza Manowieckiego z firmy Philips Lighting Poland. Prelegent zastanawiał się, jaką rolę w koncepcji tej grają energooszczędne systemy oświetlenia LED oraz jakie wynikają z niej korzyści ekonomiczne i wizerunkowe.
Nie ulega wątpliwości, że na kształt biznesu wpływa szereg globalnych trendów. Wzrost populacji, kurczące się zasoby naturalne oraz cyfryzacja życia powodują, że potrzebujemy więcej energii, lecz jednocześnie musimy dążyć do jej oszczędzania. Raport JLL wskazuje, że w przemyśle największym wyzwaniem są rosnące koszty transportu, ale rosnące koszty energii stanowią już niemal taki sam problem jak nacisk, który odbiorcy przykładają do skracania lead time.
Fabryki muszą też pamiętać o konieczności poprawy warunków i komfortu pracy, ograniczeniu ryzyka wypadków i przestojów, konieczności adaptacji do zmieniających się wymagań oraz ograniczenia kosztów bieżących. Ważną rolę grają poprawa wydajności i rentowności, minimalizowanie nakładów inwestycyjnych oraz zmniejszenie negatywnego wpływu na środowisko naturalne.
Ewolucja w kierunku gospodarki obiegu zamkniętego to nasilający się trend. Philips w swojej działalności produkcyjnej wpisuje się w jej założenia i namawia do tego inne firmy. Przykładem tego jest oferta „Światło jako usługa”, w której odbiorcy nie muszą przejmować się inwestycjami w infrastrukturę czy jej doborem.
Dane dla produkcji
Janusz Geisner z firmy BPSC zajął się podczas Areny Produkcji tematem kompleksowego monitorowania procesów produkcyjnych. BPSC, firma o 29-letniej tradycji, specjalizuje się w dostarczaniu klientom zaawansowanych rozwiązań informatycznych i ma już na koncie 1500 zrealizowanych projektów wdrożeniowych, zaś z ich systemów korzysta 140 tys. końcowych użytkowników.
Ponieważ dla firm produkcyjnych niezwykle istotne jest pozyskiwanie wiarygodnych i bieżących danych, prelegent najwięcej miejsca poświęcił prezentacji możliwości systemu MES. Pozwala on na monitorowanie procesu wytwarzania we wszystkich fazach produkcji, gromadzenie i przechowywanie pełnej informacji dotyczącej procesu produkcji, rejestrację kompletnej historii wyrobów czy łatwy dostęp do jakościowych i kosztowych wskaźników opisujących proces produkcji.
Efektami wdrożenia MES są efektywne planowanie produkcji i wykorzystanie zasobów przedsiębiorstwa, możliwość podejmowania decyzji w czasie rzeczywistym, możliwość łatwego prekonfigurowania procesu produkcyjnego czy też poprawa organizacji i jakości produkcji. Prelegent zaprezentował też szczegółowe poszczególne składowe systemu, zaś na końcu prezentacji można było zapoznać się z przykładami rejestrowanych danych.
Nowoczesna intralogistyka
Jacek Zduniak z firmy SSI SCHÄFER zaprezentował niezwykle ciekawe przykłady rozwiązań, poprawiających efektywność składowania wewnątrzmagazynowego. SSI SCHÄFER powstało w 1937 roku, zaś jego pierwszym flagowym produktem był pojemnik o charakterystycznym i ergonomicznym kształcie, szeroko kopiowany przez konkurencję. Dziś to producent i dostawca rozwiązań intralogistycznych, posiadający kilka fabryk w Europie i oferujący przygotowanie projektu składowania i transportu wewnętrznego od A do Z.
Podczas prezentacji poznaliśmy szeroką gamę produktów SSI SCHÄFER dla magazynu i produkcji. Są wśród nich m.in. regały półkowe, antresole, regały montażowe przepływowe, regały przejezdne czy regały windowe, oferujące duże możliwości składowania przy wykorzystaniu małej powierzchni. Największy zainteresowanie wzbudziły jednak zaawansowane systemy automatycznego transportu wewnętrznego – Autocruiser i Weasel.
Autocruiuser to wciąż stosunkowo prosty – ale dzięki temu łatwy do rozbudowy – system transportu pojemników, oparty na układzie szyn i automatyce sterującą ruchem i miejscami postoju. Waesel, rozwinięcie Autocruisera, to już rozwiązanie z rewolucyjnymi możliwościami adaptacji. Trasę dla wózków transportujących pojemniki tworzą ścieżki, układane na podłodze. Dzięki temu system Waesel zajmuje wyjątkowo mało miejsca i może być poprowadzony w miejscach, gdzie nie zmieszczą się tradycyjne przenośniki. Jest też bardzo odporny na uszkodzenia ścieżek prowadzących, zaś zaawansowana automatyka wyklucza możliwość kolizji z innymi elementami systemu.
3M szuka synergii
Przemysław Paździorek, reprezentant 3M – jednej z najbardziej innowacyjnych firm świata, zagościł na Arenie Produkcji, aby opowiedzieć o metodach zarządzania wykorzystywanych przez koncern. Pan Paździorek jest dyrektorem jednej z wrocławskich fabryk koncernu i pokazał jak działa opracowana przez koncern metodologia Lean Six Sigma.
3M to światowy gigant w szeregu dziedzin, ale produkcja to kluczowy element operacji firmy. 1/3 platform technologicznych oraz 1/4 patentów zgłoszonych przez firmę dotyczy obszaru produkcji. W Polsce operacje produkcyjne prowadzone są w Rabce, Janinowie i Wrocławiu. Ta ostatnia lokalizacja jest dla firmy najważniejsza – w stolicy Dolnego Śląska powstał superhub produkcyjny, zaś powierzchnia zakładów regularnie wzrasta.
Six Sigma to podejście statystyczne, którego zadaniem jest usprawnienie jakości produktów, poprzez doskonalenie realizowanych operacji. Lean Manufacturing stawia z kolei na eliminację marnotrawstwa i skupienie się na wartości dostarczanej do klienta. 3M w 2004 roku zaczęło wdrażać Six Sigma, zaś dwa lata później dołączyło do niego Lean.
Synteza tych dwóch metod pozwala wykorzystywać efekt synergii. Lean zapewnia eliminację zbędnych procesów na etapie produkcji, zaś te, które pozostały, są udoskonalane za pomocą statystycznego podejścia Six Sigma. Jak zauważył prelegent, nawet niekorzystane procesy łatwiej jest kontrolować, gdy z pomocą Six Sigma ustabilizujemy ich zachowanie.
Zdaniem pana Paździorka, najważniejsze we wdrażaniu innowacji jest regularne zbieranie pomysłów i ocenianie postępów, wyznaczanie realnych celów i organizacja spotkań otwierających i zamykających projekty. Prelegent zachęcał też, aby odwrócić wewnątrz firmy tradycyjny przepływ informacji i decyzji. Aby zapewnić sprawne działanie programów doskonalenia operacji, zarząd powinien otrzymywać jak najwięcej informacji z najniższych stanowisk, zaś pracownicy produkcji być zachęcani do podejmowania samodzielnych decyzji.
Efektywność energetyczna i przepisy
Bogdan Ślęk z Philips Lighting Poland podjął temat utrzymania konkurencyjności i wyzwolenia potencjału wzrostu polskich przedsiębiorstw w kontekście priorytetowego traktowania efektywności energetycznej. Zmiany w przepisach i coraz ostrzejsza polityka Unii Europejskiej w obszarze ochrony środowiska sprawiają, że kwestie te są wyjątkowo istotne dla przedsiębiorstw produkcyjnych.
Intencje UE nie budzą wątpliwości. Pakiet środków przygotowany przez KE ma na celu utrzymanie konkurencyjności Unii Europejskiej w czasach, gdy przejście na czystą energię zmienia światowe rynki energii. Propozycjom urzędników przyświecają trzy cele – efektywność energetyczna powinna być traktowana jako priorytet, należy dbać o uczciwe traktowania konsumentów, zaś Europa powinna być liderem na polu energii odnawialnej.
Prelegent podkreślił, że efektywność energetyczna powinna być traktowana jako źródło energii samo w sobie, gdyż jest niewyczerpalna i wszędzie dostępna. Gdzie jednak jesteśmy na tym polu? Aktualnie dyrektywy wskazują, że do 2020 roku kraje członkowskie powinny poprawić swoją efektywność energetyczną o 20%. Już wiadomo, że ten cel jest nieosiągalny, lecz urzędnicy chcą zaproponować, aby do 2030 osiągnąć poprawę o 30%. Tym razem nie miałoby to być już zalecenie, a twardy wymóg.
W Polsce efektem unijnych dyrektyw jest System Białych Certyfikatów, wymagający od przedsiębiorców uzyskania świadectwa efektywności energetycznej. Od 1 października 2016 obowiązuje nowe ustawa – pan Ślęk przedstawił najważniejsze zapisane w niej zmiany, m.in. przejście na ciągły nabór wniosków, obliczenie efektu energetycznego na podstawie energii finalnej i możliwość zgłaszania planowanych przedsięwzięć. Opłata zastępcza w 20017 roku wzrosła do 1500 zł/toe i co roku będzie waloryzowana o 5%.
Prelegent wskazał zrealizowane przykłady projektów modernizacji oświetlenia jako znakomite źródło ograniczania metod zużycia energii i emisji CO2. Na koniec na poznaliśmy historię firmy Philips w Polsce oraz sukcesy we wdrażaniu zasad Lean Management.
Kaizen pod ziemią
Niesztampowy tytuł (Kaizen kołem się toczy. Jak filozofia ciągłego doskonalenia kształtuje sposób interpretowania informacji) i niesztampowy początek – tak wyglądała ostatnia prelekcja w programie Areny Produkcji 2017. Wygłosił ją Konrad Zaręba, konsultant Kaizen Institute i Menedżer Procesu Strategicznego Planowania Zasobów Ludzkich KGHM Polska Miedź.
Temat ciągłego doskonalenia regularnie przewija się w tematyce naszych konferencji. Nigdy wcześniej nie przestawialiśmy jednak jego wykorzystania w kopalni. Pan Konrad rozpoczął jednak od sięgnięcia w daleką przeszłość i zaproponował porównania postaw Pretorian i Zwiadowców w starożytnym Rzymie jako reprezentantów dwóch różnych filozofii działania. Następnie odniósł się do sprawy Alfreda Dreyfusa, oskarżonego niesłusznie o szpiegostwo pod koniec XIX wieku i zaprezentował postawę Georgasa Piqueta, który walczył o rehabilitację Dreufusa po jego skazaniu. Dowody świadczące niewinności Dreufusa, Piquet zdobył dzięki systematyczności, która kilkadziesiąt lat później stała się podwaliną metody PDCA.
Odbicie tego typu działań prelegent dostrzegł podczas realizacji projektu doskonalenia dostaw na terenie kopalni Polkowice-Sieroszowice. Zarząd nie dowierzał, że uda się usprawnić działanie logistyki w pionie mechanicznym, w sytuacji, gdy jego centralnym punktem jest podziemny magazyn. Tymczasem wykorzystanie schematu PDCA, sięgnięcie po kreatywność pracowników i pozwolenie im na własne doskonalenie stanowisk pracy – przy założeniu, że będą będą nieuniknione – stanowiło drogę do sukcesu.
Uczestnicy konferencji przekonali się, że także w kopalni może sprawdzać się realizacja transportu w pętli mleczarza oraz zobaczyli jak wyglądają podziemne supermarkety, których funkcjonowanie jest podobne do tych spotykanych na halach produkcyjnych. Pan Konrad podkreślił, że w procesach ciągłego doskonalenia zawsze trzeba zaczynać od przekazania pracownikom niezbędnej wiedzy – nie można bowiem zakładać, że wszyscy wiedzą, co to jest np. 5S. Kluczowe jest także stworzenie wizji przyszłości, aby było wiadomo, do jakiego stanu docelowego należy dążyć.
Cenny networking
Sesji planarnej Areny Produkcji towarzyszyła część networkingowa. Ten niezwykle udany element pozwolił na zorganizowanie spotkań między prelegentami, uczestnikami, licznymi ekspertami i partnerami konferencji. Cieszymy się, że każdemu organizowanemu przez nas spotkaniu towarzyszy tak gorąca wymiana opinii i uwag i mamy nadzieję, że pozyskane kontakty zaowocują w przyszłości.
Serdecznie dziękujemy wszystkim uczestnikom konferencji za przybycie i spędzony z nami czas. Głębokie ukłony składamy partnerom konferencji, bez których Arena Produkcji nie mogła by się odbyć. Z niecierpliwością czekamy na kolejną edycję wydarzenia!
Zdjęcia z wydarzenia można znaleźć na stronie logistyka-produkcji.pl
Galeria zdjęć do artykułu
Pliki do pobrania
zarejestruj się by uzyskać bezpłatny dostęp do materiałów z konferencji. W ten sposób dbamy o polepszanie jakości naszych usług i dostarczanych do Ciebie materiałów. Rejestracja oznacza akceptację aktualnej polityki prywatności.