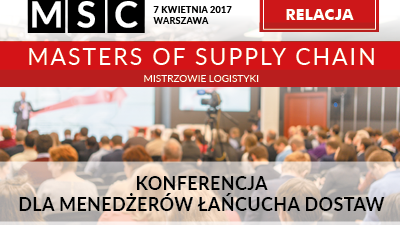
Masters of Supply Chain, nowa konferencja w portfolio wydarzeń Wydawnictwa Eurologistics, z miejsca okazała się hitem. Trudno się dziwić, bowiem program wydarzenia, będący pokłosiem badania Supply Chain Designer, był wyjątkowo bogaty. Goście konferencji mogli zapoznać się z nagrodzonymi, najlepszymi projektami usprawnień w łańcuchach dostaw oraz co najważniejsze poznać stojące za nimi osoby – czyli Mistrzów Logistyki.
Pomysł eksportowy
Po przedstawieniu przez organizatorów genezy konferencji, głos zabrał Grzegorz Kiedrzyn, Supply Chain and Innovation Director i Członek Zarządu w firmie Knauf. Pan Grzegorz opowiadał o procesie poszukiwania i wdrażania innowacji w swojej firmie, oraz o platformie Ideabook, która jest jego kręgosłupem.
Powstanie programu opartego na kreatywności pracowników i zespołów w Knauf było efektem chęci wykorzystania naturalnej tendencji pracowników do narzekania. Zamiast bezowocnie wyrażać swoją frustrację, zostali oni zachęceni do zgłaszania swoich pomysłów na poprawę sytuacji. Celem programu było nie tylko usprawnienie procesów czy poszukiwanie oszczędności. Pracownicy, widząc, że ich pomysły są wykorzystywane i doceniane mogli spełniać jedną z najważniejszych potrzeb psychologicznych – zyskać poczucie wartości.
Programy sugestii pracowniczych funkcjonują w wielu firmach, lecz Knauf wyróżnia się tutaj dzięki zastosowaniu platformy Ideabook. Za jej pomocą pracownicy mogą zgłosić swój pomysł, ale też ocenić i skomentować inne pomysły. Właśnie powszechność i dostępność platformy – z myślą o niej w obszarze produkcyjnym postawiono dostępne dla wszystkich pracowników infokioski – decydują o jej sile. Kluczowym elementem jest też bank wiedzy, do którego trafiają wszystkie pomysły, które nie są wykorzystywane, ale mogą okazać się cenne w przyszłości.
Autorzy najlepszych pomysłów są nagradzani na corocznej, wewnętrznej gali. Sposoby na docenianie pracowników są jednak także inne. Pan Grzegorz pokazał np. projekt nowej palety, która dzięki mniejszej ilości użytych surowców dała Knaufowi duże oszczędności. Aby docenić jej twórców, nazwa palety wywodzi się z ich nazwisk.
Ideabook, pomysł polskiego oddziału Knauf, jest doceniany i eksportowany do kolejnych krajów. Najlepszą nagrodą są jednak opinie samych pracowników, którzy cieszą się z samego faktu, iż ich pomysł został wdrożony i nie potrzebują kolejnych nagród.
Delphi modeluje sieć
Paweł Łaszczak, Supply Chain Optimization Supervisor EMEA i Tomasz Kalemba, Advanced Logistics Engineer, reprezentowali firmę Delphi. Przedstawili oni projekt modelowania sieci dystrybucji części zamiennych w Europie Centralnej i Wschodniej, który zaowocował przeniesieniem centralnego magazynu firmy z Warszawy do Wrocławia.
Delphi jest wiodącym światowym dostawcą rozwiązań elektronicznych i technologii systemowych. Polska stanowi dla koncernu niezwykle istotną lokalizację. Jak zdradzili prelegenci, to właśnie w centrum inżynieryjnym w Krakowie rozwijane są technologie dla samochodów autonomicznych, które będą przyszłością motoryzacji.
Polska jest kluczowa dla Delphi z punktu widzenia logistyki i głownie o tym mówiliśmy podczas konferencji. Firma w sposób centralny zarządza swoją logistyką i zakupami. Projektując sieć dystrybucji sieci części zamiennych jako priorytet traktowano skrócenie czasu przesyłki do klienta, lecz pamiętano przy tym o utrzymaniu kosztów w ryzach. Wydajna logistyka miała przełożyć się na wzrost sprzedaży w rejonie EMEA.
Podczas przygotowywania projektu pierwszym krokiem było zdefiniowanie jego zakresu oraz wybór partnerów, z którymi prowadzona będzie współpraca. Podstawową metodą wykorzystywaną w symulowaniu i wyborze nowej lokalizacji było modelowanie oparte na wyważonym środku ciężkości. Prelegenci przestrzegli przy tym, aby podczas tworzenia modelu bardzo ostrożnie podchodzić do danych historycznych, które często naszpikowane są błędami.
W wyniku ścisłej współpracy z dostawcami usług logistycznych, opracowane zostało rozwiązanie, pozwalające wymagającym niemieckim klientom otrzymywać części zamienne w ciągu 24 godzin od złożenia zamówienia przy zachowaniu kosztów na poziomie pozwalającym uzyskać przewagę konkurencyjną. Wrocław okazał się też lepszym miejscem od Warszawy ze względu na zmieniający się rynek pracy w Polsce.
Nowe technologie w zasięgu ręki
Robert Goncerz z firmy SKK podczas Masters of Supply Chain podjął się przeglądu nowych technologii w zarządzaniu łańcuchami dostaw i zastanawiał się, czy inwestycje w tego typu rozwiązania mogą się szybko zwrócić. Prelegent zwrócił uwagę na coraz większy poziom zaawansowania nowych produktów. Konieczność zastosowania w wyrobie wielu różnych surowców skutkuje rozproszeniem łańcucha dostaw, przez co coraz trudniej jest nim zarządzać.
Podstawą zrozumienia procesów zachodzących w łańcuchach dostaw jest jego analiza, oparta o trzy poziomy – zarządzanie, procesy i kompleksowość. Prelegent omówił pokrótce każdy z nich, a następnie przeszedł do kwestii oceny rentowności wdrożeń rozwiązań, mających na celu poprawę efektywności łańcuchów dostaw. Pan Robert zwrócił uwagę na to, że nowe technologie są coraz tańsze, a pozwalają na wyeliminowanie takich problemów jak wzrost kosztów produkcji, brak możliwości reakcji na zmiany rynku czy rosnące zapasy.
Szczególnie dużą rolę grają tu rozwiązania mobilne, oparte o system Andorid. Dzięki powszechności smartfonów pozwalają one na automatyzację czy śledzenie procesów przy niskim progu wejścia. Jeden standard działania aplikacji ułatwia pracę deweloperom i gwarantuje zgodność wielu rozwiązań. Warto także zwrócić uwagę na rozwój systemów wymiany danych opartych o EDI czy też coraz bardziej zaawansowane i powszechne systemy wizyjne.
Pan Robert wskazał też możliwości dedykowanych do poszczególnych operacji urządzeń przenośnych oraz wymienił przykłady rozwiązań, w których najlepiej sprawdzą się systemy głosowe. Zaawansowana automatyzacja procesów produkcyjnych i logistycznych odpowiada z kolei potrzebom Przemysłu 4.0, zaś optymalizacja działań ma celu poprawę wydajności działań przy krótkich seriach produkcyjnych. Na koniec prelegent postarał się rozwiać mity, jakie towarzyszą inwestycjom w nowe technologie.
Sposób Coca-Coli
Katarzyna Piątkowska, Country Supply Chain Services Manager w Coca-Cola HBC Polska, przybliżyła gościom konferencji tajniki strategii rozwoju łańcucha dostaw, opartej o budowanie wartości razem ze swoimi klientami. Prelegentka na wstępie przyznała, że chce zainspirować uczestników wydarzenia do podobnych działań, gdyż partnerskie podejście to najlepsza droga do ciągłego rozwoju.
Choć samej marki nie trzeba nikomu przedstawiać, pani Katarzyna wyjaśniła, jaką rolę w strukturach koncernu pełni Coca-Cola Hellenic Bottling Company. Jest to czołowy rozlewca napojów w systemie Coca-Cola, działający na terenie 28 krajów. W Polsce firma posiada 3 zakłady produkcyjne i 16 magazynów, ale choć debiut marki w naszym kraju miał miejsce jeszcze w 1957 roku, pierwszą fabrykę w Radzyminie otwarto dopiero w 1992 roku.
Jak podkreśliła prelegentka, siła marki Coca-Cola daje jej możliwość budowania dojrzałego łańcucha dostaw. Dojrzałość to dla firmy przede wszystkim dialog z klientami, dzięki którego obie strony zyskują wartość dodaną, zaś u podwalin kooperacji stoją partnerstwo i przywództwo.
Działania partnerskie obejmują wspólne planowanie działań, dzielenie się innowacyjnością i najlepszymi praktykami, indywidualne podejście do potrzeb klienta w ramach programu Implant oraz dbałość o najwyższą jakość współpracy i doskonałość operacyjną. Działania na rzecz przywództwa to z kolei zapewnienie przez Coca-Colę wiarygodności działań, wpieranie odwagi do wprowadzenia zmian, inspirowanie klientów i zachęcanie do budowy kultury organizacyjnej.
Pana Katarzyna podkreśliła, że budowa łańcucha dostaw z klientami to nie projekt, lecz ciągły proces, który ulega modyfikacjom, ale posiada niezmienny fundament. Zaś najważniejszym elementem w budowie wspólnej wartości są ludzie, którzy wstają zza biurka i zaczynają działać. Coca-Cola pamięta też o tym, że nie wszystkie rozwiązanie sprawdza się u wszystkich klientów, oraz o tym, że każdy uczestnik łańcucha dostaw musi wypracowywać zyski.
Tajniki budżetu logistycznego
Krzysztof Bobiński, Head of Supply Chain CEEG w firmie Panasonic, pokazał w jaki sposób można wykorzystać Sales&Operational Planning w procesie tworzenia budżetu logistycznego. Jeden z największych producentów elektroniki za rok będzie świętować 100-lecie istnienia i dostarcza szerokie portfolio elektroniki użytkowej ale też np. baterie do samochodów elektrycznych czy panele słoneczne.
Ponieważ w naszym rejonie Panasonic nie posiada zakładów produkcyjnych, a wyroby pochodzą z różnych fabryk, w S&OP nie włączono planu produkcji. Proces projektowania budżetu logistycznego zakłada jednak, iż zadaniem logistyki jest wsparcie sprzedaży, zaś sam budżet powinien być związany ze strategią całej firmy, elastyczny i transparentny. Proces jego tworzenia musi być sformalizowany i dokładnie określić relacje pomiędzy poszczególnymi działami.
Prelegent przyznał, że istnieje droga na skróty – budżet można obliczyć opierając się na wartości zeszłorocznych obrotów. Jednak oparcie się na zaawansowanym S&OP daje znacznie lepsze rezultaty. Jedną z zalet tego procesu jest fakt, iż nie wymaga on wyspecjalizowanych narzędzi – Panasonic korzysta tylko z Excela, za pomocą którego przygotowuje plan budżetu i śledzi jego realizację.
Wymagana są za to dokładne dane. Należy wyznaczyć osobę, która będzie w stanie wyciągnąć z planu sprzedaży najważniejsze informacje i przekazać je we właściwym terminie. W przypadku Panasonica są to ilość sprzedanych wyrobów (którą można łatwo przeliczyć na objętość wysyłek) oraz wartość sprzedaży, za pomocą której zakłada się w budżecie stałą stawkę na zlecenia oraz koszty ubezpieczenia.
Pan Krzysztof pokazał, jak od planu sprzedaży należy przejść do kosztów logistyki, a następnie ocenić realność zaplanowanego budżetu. I tutaj już przedają się dane historyczne – znaczące różnice w stosunku do lat poprzednich wskazują na konieczność sprawdzenia obliczeń. Na koniec prelegent wskazać pięć punktów kluczowych dla sukcesu wdrożenia S&OP.
Od planu do wykonania
Dawid Majchrzak, Project Manager w Hilding Anders Polska, zaprezentował z detalami imponujący projekt generalnego remontu fabryki materacy w Murowanej Goślinie. Jego przygotowanie i realizacja pokazały, że przywiązanie uwagi do szczegółów oraz właściwy dobór i zaangażowanie zespołu projektowego skutkują znakomitymi efektami.
Konieczność dokonana remontu, będącego bohaterem wystąpienia, wynikała z planu strategicznego firmy Hilding Anders. Fabryka pomimo przejścia na system czterozmianowy była już na granicy swoich możliwości produkcyjnych, tymczasem zamówienia nieustannie rosły i według prognoz w 2015 roku zakład nie byłby już w stanie zaspokoić zapotrzebowania. Kolejnym wyzwaniem, przed którym stanęli autorzy projektu było rozwiązania problemu przeciążenia głównych dróg transportowych.
Celem było zwiększenie zdolności produkcyjnych aż o 100%, skrócenie długości dług transportowych o 15-25% i zwiększenie pojemności magazynu surowców o 10-15%. Tak znaczący wzrost wydajności wymagał oczywiście zakupu nowej linii produkcyjnej, ale pojawił się problem – gdzie znaleźć na nią miejsce w sytuacji, gdy projekt nie zakłada rozbudowy zakładu? Największym wyzwaniem było jednak uniknięcie ograniczenia zdolności produkcyjnych podczas trwania projektu.
Rozwiązaniem był re-inżyniering layoutu całej firmy. Pan Dawid zaprezentował wprowadzone zmiany, obejmujące reorganizację i zmniejszenie ilości centrów produkcyjnych, przebudowę magazynów i stworzenie nowej drogi transportowej. Przy okazji tego projektu postanowiono zautomatyzować systemy transportowe materacy i palet.
Ze względu na duże wymagania zarządu – przebudowa nie mogła zakłócić wysyłki produktów do klientów oraz nie mogła być realizowana w trakcie wysokiego sezonu (lipiec-wrzesień) – przygotowano trzy scenariusze działań. Choć zdecydowano się na optymalną wersję, która zapewniał szybki przebieg prac a zarazem spełnienie wymagań projektu, scenariusze alternatywne pozwalały na podjęcie właściwych działań w razie wystąpienia odchyłek od planu.
Pan Dawid podkreślił jak dużą rolę grał w sukcesie przedsięwzięcia czynnik ludzki. Często w takich przypadkach członkowie projektu muszą dzielić swoje dotychczasowe zadania z udziałem w pracach nad remontem. Tymczasem zarząd Hilding Andres pozwolił oddelegować pracowników w całości do prac nad projektem. Zapewniło to ich pełne zaangażowanie, zaś ich umiejętności okazały się kluczowe przy przygotowaniu i realizacji przebudowy.
Jakość przede wszystkim
Michał Gębicz, Customs and Distribution Project Manager w firmie Lumileds Poland S.A., zaprezentował projekt poprawy jakości dostaw, realizowany przez jego firmę. Lumileds Poland sięga tradycją do przedwojennej fabryki żarówek w Pabianicach, a od 2015 roku należy do Philipsa. Firma skupia się na produkcji innowacyjnych żarówek dla branży Automotive, w technologii ksenonowej i halogenowej, zaś wyroby z Pabianic w 95% stanowią części zamienne.
Strategia firmy zakłada maksymalny naciska na jakość wyrobów i usług dostarczanych dla klientów. Z tego powodu, Lumileds nie tylko rygorystycznie kontroluje proces produkcji, ale też wymaga od przewoźników, aby zagwarantowali maksymalne bezpieczeństwo ładunków podczas transportu oraz realizowali dostawy w wymaganym czasie. Tymczasem logistyka jest wyjątkowo skomplikowana – Lumileds wysyła bardzo niewielkie, łatwe do uszkodzenia przedmioty, a ponadto właściwie nigdy nie korzysta z przewozów FTL. Zdarza się też, że do jednego klienta trafia jedna sztuka wyrobu.
Drogą do spełniania polityki jakościowej był projekt jakości dostaw E2E, do współpracy w którym zaproszono przewoźników. Firma korzysta ze wskaźnika PPM, czyli ilości zamówień zareklamowych na 1 milion dostaw i wlicza do niego nawet braki niezasadne. Lumileds dąży do uzyskania PPM w 2017 roku na poziomie 700.
Prelegent na przykładzie znakomitej współpracy z firmą Dachser pokazał, jak duże zaangażowanie operatora logistycznego może wpłynąć na szybką poprawę jakości dostaw. Goście konferencji mogli się przekonać, jakie problemy najczęściej występowały i w jaki sposób można je wyeliminować, wprowadzając standardy postępowania. Warto podkreślić, że Lumileds pozwolił kierowcom przewoźnika samodzielnie decydować o wstrzymaniu transportu w razie zauważenia problemów z towarem, co dowodzi wielkiego zaufania wobec Dachsera.
Efektem projektu było zwiększenie świadomości w sieci Dachser i zebranie dużo większej ilości informacji o poszczególnych uszkodzeniach towarów. To z kolei pozwoliło podjąć środki zaradcze, a w efekcie obniżyć ilość zawracanych przesyłek i uzyskać PPM zgodny z założeniami.
Korzyści dla wszystkich
Dariusz Krasoń, Logistics Manager w firmie Carlsberg, mówił podczas Masters of Supply Chain o tym, jak Carlsberg rozumie proces Customer Collaboration i jak współpraca z klientami wpływa na procesy logistyczne w samej firmie. Jeden z największych producentów piwa na świecie funkcjonuje już od 170 lat, zaś w Polsce ma trzy browary oraz trzy centra dystrybucyjne.
Czym jest Customer Collaboration dla Carlsberga? To przejście od nieregularnych lub regularnych interakcji, ale nie zawartych w biznesplanie obu firm do zestawu wspólnych inicjatyw, które wykraczają poza standardową działalność operacyjną i cechują się rachunkowością i celami wspólnymi dla obu firm. Prelegent zaznaczył, że możliwe korzyści z tego procesu w podejściu długoterminowym są ogromne.
Pan Dariusz wskazał cztery kroki prowadzące do wypracowania efektywnej współpracy. Pierwszym z nich jest właściwa komunikacja i relacje z klientem, dzięki czemu jesteśmy w stanie określić obszary, o których warto rozmawiać. Następnie należy rozpocząć prace nad koordynacją i weryfikacją danych z obu firm. Trzeci krok to wspólna budowa modelu optymalizacji biznesowej. Na końcu można zaś już przejść do budowy wspólnych planów biznesowych.
Prelegent zaprezentował metody i narzędzia jakich warto użyć, na każdym z tych etapów. Wskazał też kilka obowiązkowych jego zdaniem elementów, jak transparentność operacji czy weryfikacja i analiza danych.
– Krok czwarty, joint business plan, to trochę jak ta konferencja – zauważył pan Dariusz. Budowa współpracy klientami wymaga czasu, zaangażowania, konsekwencji i inwestycji. Należy też pamiętać, że Customer Collaboration to decyzja, która musi dawać korzyści zarówno nam, jak i klientom. Nie muszą to jednak być tylko korzyści finansowe.
Zastrzyk inspiracji
Ogromna dawka wiedzy i inspiracji oraz możliwości spotkania się z najlepszymi menedżerami w kraju odpowiadały za sukces – to najważniejsze elementy Masters of Supply Chain, które pozostaną w pamięci jego uczestnikom. Dziękujemy wszystkim za przybycie i już nie możemy doczekać się kolejnej edycji. Zaś największe ukłony kierujemy w stronę naszych Partnerów – firm SKK, BIT Logistics, Theusled, Knauf, Delphi, Coca-Cola, Panasonic, Hilding Anders, Lumileds i Carlsberg.
Galeria zdjęć do artykułu
Pliki do pobrania
zarejestruj się by uzyskać bezpłatny dostęp do materiałów z konferencji. W ten sposób dbamy o polepszanie jakości naszych usług i dostarczanych do Ciebie materiałów. Rejestracja oznacza akceptację aktualnej polityki prywatności.