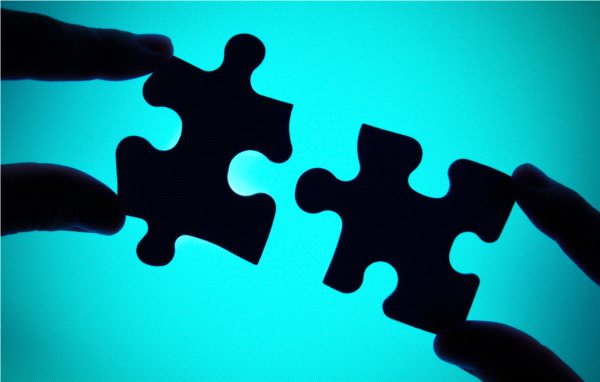
One Piece Flow
Każde przedsiębiorstwo produkcyjne z założenia nastawione jest na uzyskanie maksymalnego zysku w określonych warunkach rynkowych, uwarunkowanego przez branżę w jakiej działa, skalę produkcji, działania konkurencji, wykorzystywaną technologię. Przyjęta metoda produkcji...
Mówiąc o organizacji produkcji w aspekcie przepływów, technologii przemieszczania dobrze jest pamiętać o prostej rzeczy – sposób produkcji wyrażający się ilością i rodzajem operacji technologicznych oraz czasem ich trwania, usytuowaniem stanowisk (gniazd obróbczych) pracy wymuszających marszruty przemieszczania materiałów oraz tzw. robót w toku jest ściśle powiązany ze sposobem realizacji zadań zaopatrzenia (zakupów) we wszystko, co niezbędne do pojawienia się wyrobu gotowego.
Metody organizacji produkcji
Biorąc pod uwagę wszystkie uwarunkowania związane z możliwością prowadzenia biznesu polegającego na produkcji dóbr konsumpcyjnych oraz środki produkcji w chwili obecnej literatura przedmiotu opisuje znane metody organizowania procesów produkcyjnych, do których należą: stacjonarna – polega na alokacji środków pracy oraz pracowników wokół położonego przedmiotu lub kiedy przemieszczanie tego przedmiotu jest małe; niepotokowa – podział procesu na poszczególne operacje oraz wykonywanie każdej operacji na całej partii wyrobów; potokowa – zadania wykonywane w sposób ciągły, progresywny bez przerw związanych z okresami oczekiwania, czas poszczególnych operacji winien mieć jednakową długość; procesowa – przemysł chemiczny (przetwórstwo tworzyw sztucznych).
Funkcjonowanie na rynku wielu podmiotów stosujących identyczne technologie, produkujących produkty o porównywalnych parametrach wymusza podejmowanie działań pozwalających jeśli nie na powiększanie udziału w rynku, to przynajmniej na utrzymanie dotychczasowych klientów i poziomu zysku. Te działania mieszczą się w szeroko pojętej logistyce, tzn. działania pozwalające na osiąganie przewagi konkurencyjnej w zakresie efektywności przemieszczania dóbr w całym łańcuchu dostaw, ze szczególnym uwzględnieniem logistyki produkcji, a mamy tu na myśli nie tylko nowe podejście, ale i wykorzystywanie już znanych nam koncepcji organizacji produkcji, dzięki którym najzwyczajniej oszczędzamy czas, zmniejszając zapasy, uwalniamy kapitał, zmniejszamy zapotrzebowanie na powierzchnię. Krótko mówiąc nasze działania mają prowadzić do wzrostu efektywności funkcjonowania przedsiębiorstwa produkcyjnego w otoczeniu rynkowym.
Działania te są szczególnie istotne, gdy na horyzoncie pojawiają się problemy ze sprzedażą naszych wyrobów – rośnie konkurencja, spada siła nabywcza potencjalnych, ale i obecnych klientów, pojawia się zjawisko nazywane przez niektórych kryzysem gospodarczym, przez innych jedynie spowolnieniem. Różne są metody radzenia sobie z tymi problemami. Jednym ze sposobów jest realizacja zasady przepływu jednej sztuki – one piece flow.
Dla niektórych firm dopiero wizja utraty rynku czy zmniejszenia sprzedaży staje się przyczyną stosowania tej skądinąd znanej metody produkcji, dla innych natomiast jest to chleb powszedni, a w chwili pojawienia się spowolnienia następuje jedynie silniejsza potrzeba doskonalenia, poszukiwania kolejnych obszarów wzrostu efektywności działalności.
Aby mówić o zasadzie przepływu jednej sztuki – pojedynczej części – dobrze byłoby przytoczyć koncepcje zarządzania produkcją, które legły u podstaw budowy tego systemu produkcji.
Szczupłe zarządzanie
Lean Management to metoda mająca na celu podniesienie efektywności gospodarowania przedsiębiorstwem w zmieniających się warunkach rynkowych (zwiększenia się konkurencji, spadku dochodów itd.). LM jest metodą zakładającą ciągłe poprawianie organizacji, rozwiązań technicznych i ekonomicznych w samym przedsiębiorstwie, jak również w kontaktach z partnerami biznesowymi, szczególnie dostawcami.
U podstaw tej koncepcji leży system JiT w zakresie dostaw surowców, części i podzespołów niezbędnych do pojawienia się wyrobu gotowego, oraz zasady związane z ciągłym doskonaleniem jakości i wydajności pracy.
W zakresie samej produkcji efektem stosowania LM jest eliminacja wszystkich czynności nie dodających wartości oraz tworzenie warunków do ciągłego przepływu – czyli podniesienie procesów produkcji na poziom, w którym nie będzie miejsca na przerwy, marnotrawstwo i poprawki. Aby móc osiągnąć taki poziom efektywności i jakości produkcji, należy stosować rozwiązania, wynikiem których jest upraszczanie samych procesów produkcji, a więc wprowadzanie modułowości wyrobów na całej linii technologicznej, tzw. efektu ssania, czyli pojawia się zamówienie, rozpoczyna się przepływ, dotyczy to przede wszystkim przepływów między stanowiskami pracy – wymaga to również wyrównywania czasów przezbrajania maszyn i pamiętania o maksymalnym skracaniu tych czasów, a same operacje technologiczne mają być jak najprostsze – znany z Systemu Produkcyjnego Toyoty kanban.
Działania podejmowane w ramach Lean Management kładą duży nacisk na doskonalenie współpracy z dostawcami
Działania podejmowane w ramach Lean Management kładą duży nacisk na doskonalenie współpracy z dostawcami, którzy muszą się legitymować szeroko pojętą niezawodnością, tzn. na sto dostarczonych części 100 procent jest jakościowo właściwych, części są dostarczane wtedy, kiedy są potrzebne.
Jak w szwajcarskim zegarku
Przykładem doskonałej współpracy z dostawcami może być nie tylko podręcznikowa Toyota, ale np. Dell czy sieć Wall–Mart. Warto przytoczyć tu przykład Della, gdzie między samym zakładem produkcyjnym a dostawcami pojawia pośrednie ogniwo – kontraktowy operator logistyczny, którego zadaniem jest dostarczanie odpowiedniej ilości i asortymentu podzespołów do produkcji na podstawie otrzymywanych zamówień od producenta. Aby to było jednak możliwe, producenci podzespołów, a jest ich wielu, pomijając 50-procentowy udział Foxconn’a, mają dostęp do planów produkcji i dostarczają swoje komponenty z wyprzedzeniem, ale nie do zamawiającego, lecz do operatora logistycznego. Producent płaci za części z chwilą użycia ich do produkcji. Taki sposób działania wymaga również doskonalenia procedur produkcyjnych, zaopatrywania, u samych dostawców, a więc strumień wartości wykracza poza przedsiębiorstwo produkcyjne. Nie wszyscy niestety sobie na to pozwolić – jest to jednak przykład bardzo efektywnego ekonomicznie działania.
Zwinne wytwarzanie
Drugą koncepcją będącą niejako odpowiedzią na Lean Management jest koncepcja Agile Manufacturing – zwinne wytwarzanie. Jest to koncepcja, która pojawiła się w USA. U jej podstaw legła potrzeba stworzenia takiego sposobu produkcji, który efekt skali zamienia na tzw. total flexibillity, czyli możliwość osiągnięcia całkowitej elastyczności w odpowiedzi na napływające zamówienia odbiorców, co osiąga się poprzez obniżanie wolumenu produkcji w asortymencie, stosowaniu modułowości, współpracy z odbiorcami w zakresie konfigurowania zamawianego wyrobu (koncepcja bierze swój początek w przemyśle motoryzacyjnym), ścisłej, ale i partnerskiej współpracy z dostawcami.
Przepływ jednej sztuki
Obie te koncepcje, a szczególnie pierwsza czyli tzw. Lean Management, pozwoliły na „zaprojektowanie” metody produkcji nazwanej „Zasadą przepływu jednej części” – One Piece Flow.
Zadaniem kontraktowego operatora logistycznego Della jest dostarczanie odpowiedniej ilości i asortymentu podzespołów do produkcji na podstawie otrzymywanych zamówień
Przepływ jednej sztuki (One Piece Flow) jest metodą przepływu pojedynczej sztuki bez zatrzymywania, w sposób ciągły między kolejnymi operacjami technologicznymi lub też między odbiorcami i dostawcami – skala makro – wydziały, zakłady pracy. Inaczej jest to przepływ, którego podstawowym artefaktem jest brak zapasów między kolejnymi operacjami technologicznymi bądź realizowanie dostaw w ramach zasady JiT – w odróżnieniu od tzw. kolejkowania, czyli wytwarzania na tzw. bufor – zapas między kolejnymi operacjami technologicznymi lub też realizowanie dostaw w ilości przekraczającej potrzeby (bo sprzedający dyskontuje ilość). Na marginesie należy dodać, że metoda kolejkowania wymaga zwiększonych potrzeb powierzchni, dodatkowych manipulacji, a także wydłuża czas międzyoperacyjny (czas, w którym nie dodajemy wartości).
Warunki wdrożenia
Odnosząc się jedynie już do samych zasad i organizacji produkcji, a ściślej mówiąc sposobu przemieszczania „robót w toku” przez kolejne etapy przetwarzania, wszyscy, którzy biorą pod uwagę możliwość wdrożenia tego rodzaju metody przepływu, pamiętać muszą zaplanowaniu możliwie optymalnego – najbardziej ekonomicznego – przepływu z uwzględnieniem jego kosztów oraz dostosowaniu jednostki ładunkowej – transportowej do rodzaju transportu wykorzystywanego na linii technologicznej, i do odległości przepływu.
Rozpatrując w skali mikro – przepływ np. surowców z magazynu do hali produkcyjnej, gdzie nastąpi ich przetwarzanie – za jedną sztukę przyjmujemy np. opakowanie zbiorcze materiału, którego ilość winna wynikać ze specyfiki samego materiału, jak również norm jego zużycia. Może to być również, i o tym właściwie tu mowa, przepływ rzeczywiście jednej sztuki przez kolejne etapy przetwarzania między gniazdami obróbczymi linii technologicznej, aż do momentu pojawienia się wyrobu gotowego.
Dla pełniejszego wyjaśnienia w One Piece Flow warto przypomnieć, że funkcjonują tu także dostawy tzw. JiS (Just In Sequence) – inaczej dostawy w sekwencji produkcyjnej, czyli transportu kuwety, kosza, palety, pojedynczego opakowania z częściami montażowymi itp., w zależności od rodzaju materiału, branży firmy, sposobów dostaw. Rozpatrywanie takiego rodzaju przepływu dotyczyć może oczywiście tylko swoistych metod organizacji produkcji z wyłączeniem produkcji potokowej, technologii procesowych. Można je stosować w branżach, gdzie wyrób gotowy jest efektem produkcji montażowej (dobrym przykładem może być produkcja urządzeń powstających na liniach montażowych, gdzie etapy przetwarzania to „dokładanie” kolejnych elementów z zachowaniem właściwej kolejności ich montażu – np. produkcja aut).
Po co implementować?
Bez względu na sytuację rynkową, biorąc pod uwagę wymuszony branżą i skalą sposób produkcji już na etapie projektowania fabryki, a związku z tym i przebiegu samych procesów produkcyjnych, pojawiać się powinien taki sposób przemieszczania robót w toku, który generuje powstawanie minimalnych zapasów, minimalne potrzeby powierzchni, a tym samym wpisuje się w efektywność prowadzenia działalności gospodarczej. Takie działanie uwarunkowane jest bez wątpienia jakością zarządzania. To od szefostwa firmy, decyzyjnych pracowników i komórek organizacyjnych zależy, czy w określonych warunkach rynkowych, przyjętej organizacji przedsiębiorstwa i wskaźnikach służących do porównywania planów z osiągniętymi wynikami firma osiąga maksymalny zysk z prowadzonej działalności.
W życiu przedsiębiorstwa pojawić się zawsze może taki czas, w którym zacznie spadać sprzedaż, w którym przedsiębiorstwo zacznie tracić klientów, a zyski zaczną spadać. Może się okazać, że na rynku pojawili się nowi „gracze”, którzy na wejściu stosują nie zawsze etyczne reguły biznesowe (dumping), a może produkcja tego samego kosztuje ich po prostu mniej. Poza różnymi innymi zewnętrznymi przyczynami mającymi wpływ na sytuację przedsiębiorstwa na rynku szczegółowa analiza funkcjonowania może doprowadzić do następujących wniosków: ilość zapasów robót w toku jest niepokojąco duża – bo np. produkujemy na magazyn; czas, jaki upływa od pojawienia się materiałów, podzespołów na linii technologicznej do chwili pojawienia się wyrobów gotowych, jest długi – wąskie gardła, różny rytm stanowisk, jakość materiałów, jednostki transportowe, ładunkowe itp.; produkujmy tylko na zamówienie; branża, rodzaj produkowanych wyrobów pozwala na wdrożenie metody „przepływu jednej sztuki”.
Pamiętając o ścisłym powiązaniu sfery zaopatrzenia ze sferą produkcji, wzajemnym przenikaniu się działań obu tych sfer, jasno należy stwierdzić: przyjęty sposób, metoda produkcji wymusza stosowne działania zaopatrzenia – działania jednej i drugiej sfery muszą współgrać, w przeciwnym razie końcowy efekt poszukiwania wzrostu efektywności w sferze samej produkcji nie przełoży się na efektywność całego przedsiębiorstwa. Obie te sfery muszą być zintegrowane.
Integracja łańcucha dostaw
Na zakończenie rozważań o OPF warto dodać, że metodę tę można stosować z powodzeniem w makroskali, a dotyczyć będzie np. dostaw między przedsiębiorstwami. W tym przypadku dostawca ma dostęp do planu i harmonogramu produkcji producenta i swoje materiały i surowce dostarcza wtedy, kiedy są potrzebne, a producent płaci wtedy, kiedy zużyje je w produkcji – nakłada się tu kolejne pojęcie, a mianowicie integracja zarządzania w łańcuchu dostaw.
Przykład – z którego nie należy korzystać
Producent rozdzielnic niskiego napięcia zatrudniający około 100 osób, a więc przedsiębiorstwo zaliczyć można do średnich, nie brak mu zamówień na swoje wyroby, nie narzeka.
W zakładzie funkcjonuje około 15 stanowisk, na których realizowana jest produkcja: pojawia się obudowa, która następnie wypełniana jest przekaźnikami, stycznikami, bezpiecznikami, wyłącznikami, przekładnikami prądowymi, licznikiem – są to elementy modułowe – modułowe elementy pojawiają się w różnych rozdzielnicach, w różnych ilościach i odmianach w zależności od konkretnego zamówienia. Można rzec, że jest to przykład pasujący do zastosowania metody „przepływ jednej sztuki”. I rzeczywiście tak się to odbywa, do stanowiska dostarczane są elementy – moduły, które należy zamontować w obudowie, nie widać wąskich gardeł, mimo niekoniecznie zsynchronizowanych czasów między kolejnymi stanowiskami. Byłoby wszystko w należytym porządku, gdyby nie sposób funkcjonowania sfery zaopatrzenia, o której z całą pewnością można powiedzieć, że jej działanie nie jest zintegrowane z samą produkcją. W magazynie podzespołów i materiałów znajduje się niestety taka ich ilość, która przekracza (w niektórych asortymentach wielokrotnie) aktualne potrzeby wynikające z zamówień i planu produkcji. Pracownicy odpowiedzialni za tę sferę uważają, że tak jest dobrze, ponieważ jak pojawi się zamówienie na konkretną rozdzielnicę, to niezbędne moduły już znajdują się w magazynie, poza tym firma dostaje opust na kupowane ilości. Jednak nikt nie zadał sobie trudu, nie dokonał analizy związanej z ilością zamawianych materiałów i podzespołów pod konkretną rozdzielnicę, aby rozpoczynać procedury zakupów dopiero wtedy, gdy pojawi się zamówienie i dopasować wolumen pod napływające zamówienia. Tym bardziej, że nie ma prawie żadnych kłopotów z zamawianiem podzespołów. Nikt w firmie nie pokusił się o próbę zintegrowania sfery produkcji ze sferą zaopatrzenia – a nie należy zapominać, że dopiero takie działanie pozwoli na stwierdzenie, że wdrożenie metody przepływu jednej sztuki przyczyniło się do obniżenia kosztów prowadzenia działalności przedsiębiorstwa.