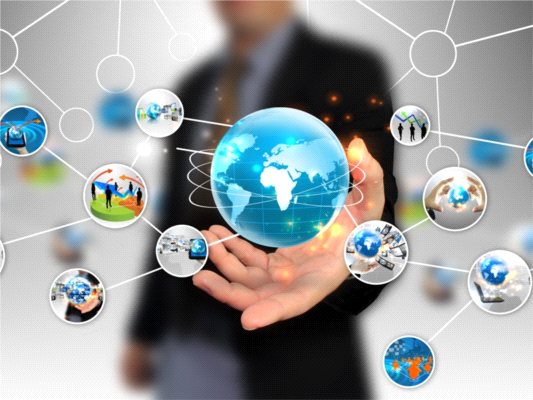
Światowe rozwiązanie
World Class Manufacturing (WCM) stanowi kompleksowy system zarządzania, który dąży do maksymalnego ograniczenia strat i marnotrawstwa w przedsiębiorstwie. Nie mniej ważne jest przy tym podnoszenie wydajności, jakości i bezpieczeństwa procesów wytwórczych.System World Class...
System World Class Manufacturing zakłada eliminowanie nieefektywności w postaci postojów, awarii, błędów i wypadków. Kluczową rolę odgrywa przy tym zaangażowanie całej załogi niezależnie od szczebla w strukturze organizacyjnej.
Elementy World Class Manufacturing
W zasadzie system World Class Manufacturing bazuje na metodach Kaizen/Lean Management. Stąd też jako elementy składowe wymienia się kompleksowe utrzymanie parku maszynowego TPM (Total Productive Maintenance), kompleksowe zarządzanie jakością TQM (Total Quality Management) oraz kompleksową kontrolę jakości TQC (Total Quality Control). Ważnym elementem WCM jest kompleksowa inżynieria przemysłowa TIE (Total Industry Engeenering), dostawy JIT (Just in Time) oraz 5S czyli optymalna organizacja miejsca pracy. Zwraca się przy tym uwagę na identyfikację strat w efekcie rozwinięcia kosztów (Cost Deployment) będącą analizą strat i macierz QA (identyfikacja miejsca powstania i wykrycia wady jakościowej). W World Class Manufacturing stawia się na pracę zespołową i działania w kierunku systematycznego rozwiązywania problemów.
Narzędzia systemu
World Class Manufacturing opiera się na szeregu narzędzi, których używa się podczas tradycyjnego rozwiązywania problemów jakościowych; oraz działań wchodzących w skład Lean Management. I tak też warto zwrócić uwagę na krzyż bezpieczeństwa stanowiący narzędzie szybkiej wizualizacji. Krzyż bezpieczeństwa wywiesza się w miejscu widocznym, gdzie każdy pracownik może sprawdzić czy jego praca wykonywana jest w sposób bezpieczny. Dla profilaktyki kluczową rolę odgrywa zachowanie zielonego koloru krzyża. Każde znajdujące się na nim żółte i czerwone pole oznacza, że trzeba podjąć działania zmierzające do wyeliminowania zagrożeń oraz zapewnienia warunków bezpieczeństwa pracy.
Mówiąc o narzędziach World Class Manufacturing należy wspomnieć o S-Tag. Narzędzie to pozwala na sygnalizowanie zagrożeń bezpośrednio na stanowisku pracy. Specjalna kartę wystawiają jednostki produkcyjne, kierownik zmianowy oraz lider lub operator danej linii. Kierownik wprowadza kartę do systemu SAP i jest ona przesyłana do działu utrzymania ruchu. W następnej kolejności dyspozytor po otrzymaniu karty wysyła pracownika na miejsce, gdzie występuje zagrożenie BHP celem usunięcia niezgodności. Data zamknięcia karty jest wpisywana nie wcześniej niż po usunięciu zagrożenia. Kluczowe miejsce zajmuje zgłoszenie dyspozytorowi, że zadanie wykonano po czym jest ono zamykane w systemie SAP.
W zakresie technicznym system opiera się na dziesięciu filarach obejmujących podział kosztów, ciągłe doskonalenie, poprawę i kontrolę jakości, autonomiczne utrzymanie oraz profesjonalne utrzymanie.
Zastosowanie znajdują również karty AM-Tag. Za pomocą kart tego typu zgłaszane są usterki i nieprawidłości zauważonych przez operatorów na maszynach i urządzeniach, które obsługują na własnych stanowiskach pracy. Należy podkreślić, że w praktyce zastosowanie znajdują dwa rodzaje kart AM-Tag – czerwona oraz niebieska. I tak też kartę niebieską wystawia się wtedy, gdy operator linii jest w stanie samodzielnie rozwiązać problem, natomiast karta czerwona znajduje zastosowanie jeżeli potrzeba pomocy odpowiedniego specjalisty.
Stosowane metody
Poka-Yoke to metody, które pomagają operatorom uniknąć pomyłek podczas wykonywania pracy. Chodzi przede wszystkim o wyeliminowanie w czasie pracy przestojów spowodowanych np. wyborem nieodpowiednich części, ich pominięciem lub odwrotnym zainstalowaniem. Poka-Yoke są coraz szerzej stosowane w przemyśle jako element strategii „zero błędów”, czyli wbudowywania jakości w proces zamiast kontrolowania jej na końcu procesu.
Istotną rolę odgrywa metoda 5S, gdzie zakłada się, że stanowisko, które nie jest odpowiednio zorganizowane, może być jedną z podstawowych przyczyn wzrostu kosztów produkcji. Stąd też kluczową rolę odgrywa porządek przyczyniający się do poprawy jakości oraz wydajności produkcji.
W myśl 5S przyjęło się wyróżniać poziomy organizacji stanowiska pracy. Pierwszy z nich 1S (z jap. Seiri) stanowi eliminowanie zbędnych materiałów, zgodnie z zasadą: „wyrzucić co niepotrzebne”. Następny poziom to 2S (z jap. Seiton). Na tym etapie kluczową rolę odgrywa takie zorganizowanie przestrzeni roboczej, aby umożliwić jak najłatwiejsze korzystanie z niej. Należy tutaj zadbać o należyte segregowanie narzędzi i materiałów. Kolejny etap uwzględnia wyczyszczenie wszystkiego, co znajduje się na stanowisku pracy, zgodnie z 3S (z jap. Seiso). Należy zadbać przede wszystkim o odnowienie stanowiska roboczego. W praktyce realizowanie zasady czystości to zazwyczaj utrzymywanie nienagannego porządku. W następnej kolejności należy zadbać o traktowanie wcześniejszych zasad w kategorii codziennego nawyku, co jest zadaniem 4S (z jap. Seiketsu). Ostatnią zasadę stanowi samodyscyplina czy 5S (z jap. Shitsuke). Warto zwrócić uwagę na fakt, że wdrażane standardy nie zawsze muszą być realizowane. Istotną kwestię stanowi zatem stworzenie atmosfery propagującej te zasady. Konieczne jest więc przeprowadzenie okresowych kontroli pozwalających na ocenę stanowiska pracy.
Metoda 5 WHY w ramach World Class World Class Manufacturing pozwala na wykrywanie przyczyn problemów. Warto zwrócić uwagę na fakt, że 5 WHY zastosowanie znajduje głównie przy ustalaniu podstawowej przyczyny problemu. Odpowiedzi udzielone na pytanie „dlaczego” są pomocne przy zrozumieniu problemu, w efekcie czego przyczyna powstawania jest zazwyczaj prostsza do zrozumienia. Zastosowanie tej metody pozwala również na zastanowienie się dlaczego problem nie został zauważony. W pierwszym etapie kluczową kwestię stanowi przede wszystkim zebranie informacji dotyczących konkretnego problemu. Pamiętać należy, że im więcej zostanie zebranych danych, tym bardziej podnoszą się szanse na właściwe zidentyfikowanie przyczyn problemu. Warto zatem zwrócić uwagę na to co się stało, kiedy oraz jaka jest skala problemu. Nie mniej istotne pozostaje również określenie stopnia zagrożenia powstałego w wyniku wystąpienia problemu. Kolejny krok uwzględnia powstanie grupy roboczej. Z pewnością uwzględnienie w schemacie działań osób dysponujących licznymi i wartościowymi informacjami o problemie przyczyni się do zwiększenia skuteczności 5 WHY.
Z pewnością uwzględnienie w schemacie działań osób dysponujących licznymi i wartościowymi informacjami o problemie przyczyni się do zwiększenia skuteczności 5 WHY.
Ważnym narzędziem World Class Manufacturing jest 4M. Za jego pomocą zyskuje się możliwość nie tylko wytypowania ale i pogrupowania czynników i przyczyn wywołujących określony skutek. Przyczyny te zazwyczaj grupuje się w czterech obszarach: człowiek (Man), materiał (Material), metoda (Method) oraz maszyna (Machine). Niejednokrotnie zastosowanie znajduje dodatkowe „M” chociażby w postaci pomiarów (Measurements), środowiska (Mother Nature – matka natura) oraz zarządzania (Management). Należy podkreślić, że narzędzie 4 M bardzo często jest wykorzystywane na etapie sporządzania wykresu przyczynowo-skutkowego Ishikawy. Tym sposobem zyskuje się narzędzie analizy problemu.
Z kolei OPL (One Point Lesson) stanowi narzędzie, które przeznaczone jest do przekazywania ważnych informacji w krótkim czasie. Lekcje tego typu zazwyczaj tworzone są przez kierowników i specjalistów zmianowych oraz specjalistów liniowych. Zaletą OPL jest przede wszystkim bardzo szybkie zapoznanie się pracowników chociażby z nowymi ulepszeniami lub informacjami pomagającymi w obsługiwaniu procesu technologicznego.
Narzędziem World Class Manufacturing jest również analiza EWO – Emergency Work Order. Narzędzie tego typu uwzględnia się bezpośrednio po ustaniu awarii, bowiem po upływie czasu wiele istotnych informacji może ulec utracie. Stosując EWO rejestrowane są dane statystyczne dotyczące awarii oraz rejestruje się przebieg interwencji. Ważna jest przy tym możliwość wskazania przyczyny źródłowej awarii, działania koniecznego do wyeliminowania przyczyny źródłowej oraz działań koniecznych do utrzymania rozwiązań w czasie.
Filary WCM
World Class Manufacturing opiera się na filozofii system TPS (Toyota Production System) oraz założeniach Lean Manufacturing. WCM znalazł zastosowanie chociażby w zakładach należących do koncernu Fiat.
W zakresie technicznym system opiera się na dziesięciu filarach obejmujących podział kosztów, ciągłe doskonalenie, poprawę i kontrolę jakości, autonomiczne utrzymanie oraz profesjonalne utrzymanie. Nie mniej ważne jest przy tym zarządzanie urządzeniami, rozwój kadr, środowisko, a także BHP, obsługa klienta i logistyka.
World Class Manufacturing to również 10 filarów menedżerskich w postaci zaangażowania zarządu, jasnego określenia celów, stworzenia ogólnego planu realizacji projektu oraz przydzielenia zasobów ludzkich. Kluczowe miejsce zajmuje zaangażowanie całej załogi, ukierunkowanie załogi na osiągnięcie poprawy, określenie terminów i budżetu oraz określenie konkretnego, planowanego poziomu rozwoju.