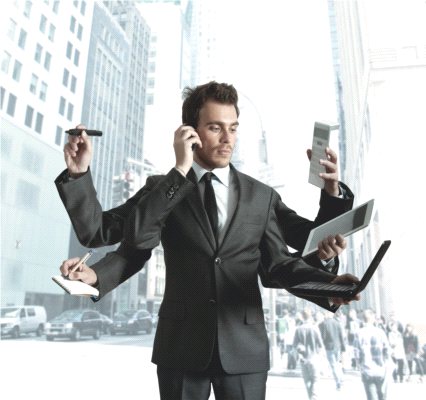
Efektywność płynąca z Kaikaku
Marnotrawstwo to słowo w sposób oględny wyrażające negatywne działania, które nie powinny być wykonywane. Idea eliminacji marnotrawstwa wywodzi się ze stworzonej w latach 90-tych koncepcji „Lean Management” czyli odchudzonego wytwarzania.Mnie osobiście bardzo przypadła do gustu...
Mnie osobiście bardzo przypadła do gustu definicja marnotrawstwa bazująca na prostym podziale wszystkich działań, które muszą zostać podjęte, aby dostarczyć określone dobro klientowi finalnemu. Jeśli z punktu widzenia klienta działanie dodaje jakąś wartość, to jest produktywne i właściwe, w przeciwnym wypadku jest zbędne i określane mianem marnotrawstwa. Wbrew pozorom nie ma tu większego znaczenia, czy owo dobro jest produktem czy usługą. Idea jest ważna i łatwa do dopasowania dla obu grup. Jako że artykuł ten dotyczy linii montażowej, na której wytwarzane są produkty, skupię się bardziej na pierwszej grupie, czyli na produktach.
Unikać pułapek
Kluczem do zrozumienia idei marnotrawstwa jest zdefiniowanie wartości z punktu widzenia klienta finalnego. Należy jednak uważać, aby nie dać się złapać w pułapkę, gdyż np. jaką wartością dla klienta kupującego i spożywającego mleko jest jego opakowanie? Jednakże bez niego nie udałoby się dostarczyć produktu klientowi, poza tym bardzo często stanowi ono element marketingowy, który dostarcza impuls do dokonania transakcji, tak więc, mimo iż nie stanowi ono wartości w sensie rozumienia dostarczanego produktu, jest elementem niezbędnym i niemożliwym do wyeliminowania. Takie właśnie elementy w metodologii odchudzonego wytwarzania nazywane są marnotrawstwem typu drugiego i mimo znikomej wartości dla klienta nie mogą zostać do wyeliminowane. Kolejną pułapką, w którą często sam wpadam, jest próba eliminacji marnotrawstwa w czynnościach, które tak naprawdę nigdy nie powinny być wykonywane. Znakomicie pasuje tu maksyma jednego z prekursorów Lean mówiąca, że ”Najgorzej jest robić efektywnie rzeczy, które nigdy nie powinny być wykonane”.
Kilka dróg rozwoju
Kiedy przystępujemy do eliminacji marnotrawstwa, stajemy przed trudnym wyborem sposobu, w który będziemy działali. Osobiście wyróżniam dwie drogi – procesową oraz projektową. Obydwie drogi wbrew pozorom nie są do końca alternatywne i mogą być uruchomione równolegle. Różnica pomiędzy nimi jest tożsama z różnicą pomiędzy procesem a projektem – ten pierwszy nie ma swojego końca, przez co nazywany jest ciągłym doskonaleniem, ten drugi ma jasno zdefiniowany początek i koniec oraz co jeszcze ważniejsze, cel, który powinien zostać osiągnięty. W ideologii odchudzonego wytwarzania najczęściej spotykaną definicją obydwu dróg jest Kaizen i Kaikaku. Proces ciągłego doskonalenia nie daje tak spektakularnych efektów w krótszym okresie czasu, jednakże jest niezmiernie ważny i istotny z punktu widzenia kreowania kultury przedsiębiorstwa, a w szczególności wszystkich jego pracowników. O procesie ciągłego doskonalenia można by napisać kilka kolejnych artykułów, jednakże w niniejszym postaram się skupić na konkretnym projekcie optymalizacyjnym, który miałem okazję prowadzić w jednej z firm produkujących materace.
Zmniejszyliśmy ilość produkcji w toku o siedemdziesiąt procent
Wiedzieć, gdzie się podąża
Każdy projekt zaczyna się zwyczajowo od zdefiniowania jego celów. Jest to jeden z najbardziej kluczowych elementów w każdym projekcie, dlatego że to poprzez cel definiowane są wszystkie czynności, które w ramach danego projektu będą wykonywane. Często miałem do czynienia z menedżerami, którzy prosili mnie o optymalizację procesów wytwórczych stwierdzając kolokwialnie: „zrób projekt na tej linii i zoptymalizuj ją”. Jest to podejście szalenie niebezpieczne, bo nie daje osobie prowadzącej projekt punktu wyjścia do jakiegokolwiek działania. Filozofie Lean Manufacturing, SixSigma czy TOC stały się ostatnio tak popularne, że wiele firm złapało się w pułapkę „robienia Lean”, bo wszyscy tak robią. Przed rozpoczęciem jakiegokolwiek przedsięwzięcia bardzo ważne jest odpowiedzenie sobie na pytanie o jego cel. Dla mnie osobiście najlepszym przykładem definicji celów jest zrównoważona karta wyników.
Transport wewnętrzny produkcji w toku oraz większości surowców został w pełni zautomatyzowany
W przypadku opisywanego projektu był jeden cel główny – zwiększenie efektywności procesu o 30 procent poprzez zmniejszenie pracochłonności koniecznej do wykonania produktu. Dodatkowo sponsor projektu zażyczył sobie wyeliminowania wózków widłowych z produkcyjnej powierzchni hali, co miało znacząco zwiększyć bezpieczeństwo osób tam przebywających oraz poprawić wskaźniki jakości produkowanych wyrobów o 15 proc. W rozpatrywanym przypadku sytuacja była dość klarowna, ponieważ proces był dobrze znany i opomiarowany. Znaliśmy wskaźnik produktywności, wyrażany w postaci ilości roboczogodzin przypadających na wyprodukowanie jednej sztuki wyrobu gotowego, jak i wskaźnik jakościowy opisujący wartościowo poziom braków generowanych przez proces.
Metodologie prowadzenia projektów
Po zdefiniowaniu celów: projektu należy wybrać metodologię prowadzenia projektu, jest ich naprawdę dużo (PRINCE2, DMAIC, PMP, PDCA itp.), a ich wybór zawsze pozostaje po stronie kierownika projektu. Osobiście w zależności od czasu trwania projektu, stopnia jego skomplikowania oraz celów, jakie mamy osiągnąć, preferuję trzy metodologie: DMAIC – dla projektów, w których czas nie jest bardzo istotny, a zrozumienie procesu jest niskie, PDCA w przypadku kiedy mamy bardzo mało czasu na osiągnięcie celu, oraz wspomniane wyżej autorskie rozwiązanie bazujące na PMP – w projektach, które nie łapią się pod oba powyższe kryteria.
Przeprojektowanie procesów
W opisywanym przykładzie pomimo dużej znajomości procesu zdawaliśmy sobie sprawę, że nie uda nam się osiągnąć zakładanych celów poprzez optymalizację istniejącego rozwiązania. Postawiliśmy więc na re-inżyniering czyli zdefiniowanie procesu na nowo od samego początku. Takie bardzo komfortowe założenie niestety nie zdarza się zbyt często, ponieważ zwykle wymaga dość dużych nakładów inwestycyjnych w nowe urządzenia i rozwiązania techniczne oraz narzuca dłuższy okresu trwania projektu. Zawsze jednak zalecam rozważenie takiego rozwiązania, gdyż może się okazać, że ilość środków niezbędnych do zbudowania procesu od nowa jest mniejsza niż ta potrzebna na jego modernizację. To naprawdę duża satysfakcja dla specjalisty od procesów produkcyjnych, móc wykorzystać swoje dotychczasowe doświadczenia i wiedzę, aby wykreować idealny proces produkcyjny od samego początku.
Przed takim właśnie przedsięwzięciem stanęło grono specjalistów i technologów. Dało nam to możliwość eliminowania marnotrawstwa już w fazie projektowania procesu. I to właśnie ten proces chciałbym troszkę przybliżyć.
Dzięki umieszczeniu etykiety RFID w każdym produkcie już na początku procesu produkcyjnego, mamy możliwość śledzenia tych produktów w całym procesie produkcyjnym
Harmonia produkcji z popytem
Zanim zaczniemy projektować lub doskonalić proces produkcyjny, należy zadać sobie istotne pytanie o to, jakie zdolności produkcyjne ma on generować. Po co nam proces generujący tysiące produktów, których nikt nie chce kupić lub bardzo efektywny proces, który jednak nie jest w stanie zaspokoić popytu generowanego przez rynek? Całość tego przedsięwzięcia można streścić prostym wskaźnikiem – Czas Taktu – jest to wyrażony w jednostce czasu (sekundy, minuty, godziny) popyt na produkt. Dopiero kiedy go znamy, możemy przystąpić do definicji procesu. Bardzo ważne jest w momencie projektowania procesu wytwórczego zdefiniowanie gamy i wariantów produktów możliwych do wytworzenia w procesie. W tym momencie stajemy przed trudnym dylematem: efektywnie czy elastycznie? To pytanie, na które warto spojrzeć, uwzględniając dłuższy horyzont czasowy.
Proces produkcyjny to zwykle szereg czynności koniecznych do wykonania w celu przekształcenia surowca wejściowego w produkt finalny. W przypadku produkcji materaca większość tych czynności zależna jest od pracownika i jego umiejętności. Aby ograniczyć czas niezbędny do ich wykonania, postanowiliśmy postawić na automatyzację.
Ustalenia wąskiego gardła
Po znalezieniu odpowiedzi na wszystkie powyższe pytania oraz po określeniu ram czasowych przeszliśmy do fazy koncepcyjnej, w której szereg specjalistów opracowywał koncepcję procesu produkcyjnego. W tej właśnie fazie najistotniejsze było zdefiniowanie sobie wartości produktu z punktu widzenia klienta oraz postawienie kilku dodatkowych wymagań, które proces miał spełniać.
Po pierwsze, postanowiliśmy już od początku zastosować wywodzącą się z teorii ograniczeń koncepcję wąskiego gardła i zaprojektować je w miejscu, które naszym zdaniem jest najodpowiedniejsze. Za miejsce takie uznaliśmy operację, której pracochłonność jest najwyższa, a tym samym generuje największy koszt. W sumie w zaprojektowanym procesie produkcyjnym mieliśmy do wykonania około 15 operacji, które podzielić można było na 5 grup – pikowanie blatów, przygotowanie produkcji, szycie pokrowca, montaż materaca oraz pakowanie. Z założonego czasu taktu wyliczyliśmy, że aby wykonać określoną ilość wyrobów, niezbędne będzie ustawienie około 50 stanowisk pracy, z czego 50 proc. przypadało na grupę: szycie pokrowca. To właśnie ta grupa stanowisk została wybrana do pełnienia zaszczytnej roli wąskiego gardła. Proces miał być zaprojektowany tak, aby ten element nigdy nie cierpiał na przestoje, dlatego wszelkie operacje go poprzedzające oraz po nim następujące zostały zaprojektowane tak, aby ich moce produkcyjne nieznacznie przewyższały te zdefiniowane w wąskim gardle. Element ten posłużył nam także jako stymulator całego procesu, to przez niego uruchamiane jest każde zlecenie produkcyjne. Ze względu na dużą różnorodność wykonywanych operacji oraz szeroki wachlarz kombinacji ich czasów, do sprawdzenia funkcjonalności koncepcji oraz do zdefiniowania poziomów produkcji w toku zapewniających płynną pracę posłużyliśmy się narzędziem do symulacji procesów. Niestety oprogramowanie to nie należy do najtańszych, natomiast z czystym sumieniem polecam chociażby wynajęcie firmy, które taką analizę zrobi, gdyż dzięki niej w błyskawicznym tempie otrzymuje się odpowiedzi na wiele istotnych pytań i dodatkowo ma się możliwość przetestowania procesu w skrajnych sytuacjach.
Inwestycje w automatyzację
Drugim istotnym kryterium była eliminacja wszelkiego rodzaju marnotrawstwa oraz zastąpienie możliwie największej ilości niemożliwych do wyeliminowania prac przez automatykę. Dlatego właśnie wszelki transport wewnętrzny produkcji w toku oraz większości surowców został w pełni zautomatyzowany. Wyeliminowane zostały wszelkie czynności związane z podnoszeniem lub odkładaniem produktów oraz zautomatyzowaliśmy wszelkie czynności związane z depaletyzacją surowców oraz paletyzacją wyrobów gotowych i transportem pomiędzy magazynami. Dodatkową zaletą automatyzacji operacji było zwiększenie powtarzalności wykonywanych operacji. A w przypadku etykietowania automatyzacja wyeliminowała plagę pomyłek związanych z przyklejeniem błędnej etykiety.
Potrzebny MES
Po zaprojektowaniu samego procesu stanęliśmy przed dylematem jego zarządzania. Stopień skomplikowania procesu stawiał pod znakiem zapytania sterowanie procesem bez dodatkowego wspomagania ze strony oprogramowania. Po rozważeniu wszelkich możliwości postanowiliśmy wdrożyć system klasy MES, tzn. system zarządzania procesem produkcyjnym, będący pomostem pomiędzy systemem klasy ERP a fizycznymi stanowiskami i maszynami na hali produkcyjnej. Dzięki umieszczeniu etykiety RFID w każdym produkcie już na początku procesu produkcyjnego, mamy możliwość śledzenia tych produktów w całym procesie produkcyjnym. Dało nam to możliwość automatycznego balansowania produkcji w toku pomiędzy istniejącymi stanowiskami oraz pociągnęło za sobą dodatkową zaletę w postaci pełnej informacji o przebiegu procesu dla każdego istniejącego produktu.
Dzięki założeniu wykorzystania filozofii odchudzonego wytwarzania, SixSigma oraz teorii ograniczeń powstał proces, który nie dość, że spełniał wszelkie kryteria celów, to dawał dodatkowe benefity. Udało nam się skrócić trzykrotnie czas przepływu produktu przez cały proces. Zmniejszyliśmy ilość produkcji w toku o siedemdziesiąt procent.
Projekt od momentu rozpoczęcia do pełniej implementacji zajął dwa lata. Dał on nam jednak bardzo dużo wiedzy, w jakim kierunku powinniśmy zmieniać nasze procesy, aby pozostały konkurencyjne na istniejącym rynku.