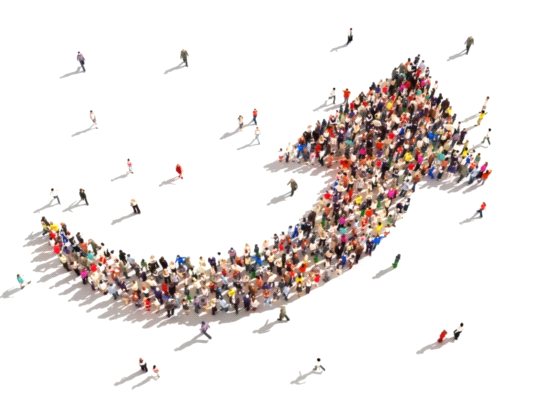
Dobrze myśleć i dobrze zarządzać
Wertując nowe pozycje książkowe, odwiedzając konferencje czy też śledząc wieści ze świata przemysłu, możemy być niemal pewni, iż natrafimy na liczne odniesienia do Lean Thinking. Jeśli jeszcze nie wiemy, jakie są podstawy tej rewolucyjnej filozofii zarządzania, warto uzupełnić...
Termin Lean Thinking rozpowszechnili James P. Womack i Daniel T. Jones, wydając w 1996 roku książkę pod tym samym tytułem. Womack i Jones stworzyli podwaliny światowej ekspansji Lean Manufacturing dzięki swojemu bestsellerowi “Maszyna która zmieniła świat”, lecz nie zaprzestali drążenia tematu. Lean Thinking – termin występujący w języku polskim jako „Odchudzone myślenie” lub „Szczupłe myślenie” – rozszerza zagadnienia związane z nowoczesnymi metodami zarządzania produkcją, opracowanymi w japońskich przedsiębiorstwach.
To nie jest sposób zarządzania
Szukając informacji na temat Lean Thinking łatwo jest dojść do mylnego wniosku, iż filozofia ta, mająca na celu likwidowanie marnotrawstwa, wiąże się tylko z zagadnieniami zarządzania przedsiębiorstwami produkcyjnymi. Rzeczywiście, odchudzone myślenie ma swoje korzenie w przemyśle motoryzacyjnym, lecz możemy stosować je w odniesieniu do każdej działalności, nie tylko biznesowej. Elementy tej filozofii doskonale sprawdzają się w pozornie niereformowalnych organizacjach, jak administracja publiczna czy służba zdrowia. Odchudzone myślenie z powodzeniem można wprowadzić do banalnych, codziennych czynności.
Lean Thinking wymaga jednak kompletnej zmiany mentalności wszystkich pracowników firmy, nie może być ono podejmowane w ramach krótkotrwałego programu redukcji kosztów. Przyjęcie założeń odchudzonego myślenia musi być trwałe, tylko w ten sposób można osiągnąć pełne korzyści z jego stosowania.
Głównym celem Lean Thinking jest stworzenie jak najlepszych produktów przy jednoczesnej eliminacji muda – czyli marnotrawstwa – we wszelkich działaniach. Zalety wynikające z unikania strat w firmie już na pierwszy rzut oka są oczywiste. Jednak szczupłe myślenie opiera się na procedurach, które przeobrażają cały proces działania przedsiębiorstwa i traktują problem systemowo, wykorzystując wszelkie możliwości na likwidację marnotrawstwa. Dzięki tej filozofii, wyzwalany jest pełen potencjał maszyn i pracowników.
Zaczynamy od końca
Wszelkie działania w ramach Lean Thinking rozpoczynane są od końca, czyli od określenia wartości produktu. Dlaczego od końca? Rzeczywistą wartość produktu może bowiem zdefiniować tylko końcowy odbiorca. Producent tworzy wyrób lub wykonuje usługę, jednak to klient stwierdza, czy jego potrzeby zostały zaspokojone. Lean Thinking stawia wartość na pierwszym miejscu, to jej mają być podporządkowane prace rozwojowe, procesy technologiczne, decyzje o zakupach nowych maszyn czy zmiany personalne. Ignoruje się dotychczas istniejącą bazę i technologie.
Pierwszym krokiem odchudzonego myślenia ze strony przedsiębiorstwa jest zatem próba jak najdokładniejszego ustalenia, czym dokładnie jest wartość. I to na niej należy się koncentrować, podejmując decyzje w sprawie zmian zachodzących w procesach. Sprawy idą lepiej, jeśli skupiamy się na produkcie, a nie na urządzeniach i organizacji.
Kolejnym zadaniem, które czeka na nas podczas realizacji zasad Lean Thinking, jest mapowanie strumienia wartości. Należy zidentyfikować kompletny zespół czynności, składający się na tworzenie danego produktu. Błędem jest w tym przypadku zajmowanie się tylko działaniami prowadzonymi w naszej firmie. Strumień wartości rozpoczyna się od pozyskania surowców, a kończy w momencie dostarczenie klientowi towaru. Mapowanie musi zatem obejmować także dostawców surowców czy podzespołów, oraz sieć dystrybucji i sprzedaży.
Poszukiwania muda
Mapowanie strumienia wartości ma na celu wychwycenie marnotrawstwa – muda – występującego na drodze tworzenie produktu. Prowadzone działania dzielone są na trzy kategorie:
- – działania tworzące wartość
- – działania nie tworzące wartości, lecz konieczne do wykonania ze względu np. na istniejące
- możliwości technologiczne (nazywane są one muda pierwszego typu)
- – działania nie oferujące żadnej wartości i możliwe do natychmiastowego wyeliminowania (muda
- drugiego typu).
Wyniki mapowania strumienia wartości w przedsiębiorstwach zarządzanych w tradycyjny sposób są często szokujące. W skrajnych przypadkach tylko 5% działań tworzy wartość produktu, a nawet 60% przeznaczonych jest do natychmiastowego wyeliminowania. W prostym przykładzie produkcji śrub, wartością są tylko procesy obróbki – toczenia, cięcia czy gwintowania, wykonywane bardzo szybko, na maszynach o dużej wydajności. To dzięki nim klient otrzymuje interesujący go produkt.
Do muda pierwszego typu zaliczamy działania związane np. z kontrolą jakości czy też obróbkę wykonywaną przez zewnętrzny zakład. Proces galwanizacji śruby jest wartością, ale konieczność transportu do innego przedsiębiorstwa stanowi marnotrawstwo. Muda drugiego typu to wszelkie okresy oczekiwania na kolejne procesy obróbki, zdublowane czynności, zbędne ruchy pracowników, nadmierne zapasy, niepotrzebny transport. Zazwyczaj udaje się o połowę zmniejszyć ilość wadliwych produktów trafiających do klienta, eliminacja marnotrawstwa zmniejsza także ilość wypadków przy pracy.
Natychmiastowa eliminacja muda drugiego typu daje szybkie i bardzo odczuwalne korzyści dla przedsiębiorstwa. Prócz ograniczenia nakładów finansowych związanych z czasem przerobu, magazynowaniem, zarządzaniem zapasami, zbędnym transportem; zazwyczaj udaje się o połowę zmniejszyć ilość wadliwych produktów trafiających do klienta. Eliminacja marnotrawstwa zmniejsza także ilość wypadków przy pracy. Womack i Jones określają ten efekt mianem premii kaikau. Już mamy duże korzyści, ale to dopiero początek szczupłego myślenia.
Wszystko płynie
Trzecim krokiem działań Lean Thinking, podejmowanym po wyeliminowaniu marnotrawstwa, jest stworzenie przepływu. To wyjątkowo trudny krok dla typowych zakładów produkcyjnych, bowiem wymaga zupełnie innego podejście do wykonywanych zadań. Przez lata pokutowało przekonanie, iż prace należy dzielić na wydziały, zajmujące się kolejno partiami wyrobów. Maszyny były silnie obciążone, pracownicy mieli zajęcie, lecz system był mało elastyczny i generował duże marnotrawstwo ze względu na oczekujące partie wyrobów. Praca maszyn musi być podporządkowana tworzeniu wartości, a nie samemu procesowi produkcyjnemu.
Szczupłe myślenie, skupiające się na wartości, dokonało rewolucji w tym podejściu. Produkcja przepływowa podporządkowana jest produktowi, a nie procesowi. Zmniejszone partie i ustawienie maszyn w gniazda produkcyjne umożliwia płynną obróbkę wyrobu – czyli w podejściu Lean Thinking przepływ wartości – na kolejnych stanowiskach, bez oczekiwania, czyli bez marnotrawstwa. Optymalnie wykorzystywane są też zasoby ludzkie, pracownicy są wszechstronnie szkoleni, dzięki czemu mogą wykonywać szereg czynności, zamiast – jak w tradycyjnym modelu – podobną czy nawet większą ilość pracy, nie przekładającej się jednak na wartość. Przepływ obejmuje cały strumień wartości, a zatem płynnie realizowane są też zadania projektowania, zamawiania, transportu i dystrybucji. Droga od surowca do gotowego wyrobu, dostarczanego klientowi, przebiega bez zakłóceń i przestojów.
Wózek się ciągnie, a nie pcha
Zyski po wykonaniu pierwszych kroków Lean Thinking są znaczące, lecz największe zalety tej filozofii dopiero się ujawniają. Po upłynnieniu strumienia wartości możliwe jest wdrożenie zasady wyciągania, czyli prowadzenia działań dopiero w momencie, gdy występuje na nie zapotrzebowanie. Inicjatorem wyciągania zawsze jest klient. To on zgłasza potrzebę, którą można zaspokoić tworząc wartość. Lean Thinking wyklucza tworzenie nadmiernych zapasów, bez istniejącego na nie zapotrzebowania, bowiem nie stanowi to wartości. Taki produkt czy usługa to po prostu muda, i to według klasyfikacji to najpoważniejsze. Tradycyjnie działające przedsiębiorstwa nawet jeśli zdołają sprzedać istniejące zapasy, często zmuszone są do obniżania ceny co generuje straty.
Zgłoszenie potrzeby przez klienta inicjuje proces wyciągania produktu do sklepu od dystrybutora, od producent do dystrybutora, podzespołów od poddostawcy do producenta, surowców z huty do poddostawcy. Szczupłe myślenie narzuca stosowanie wyciągania w każdym punkcie strumienia wartości – np. toczenie detalu jest rozpoczynane dopiero wtedy, gdy kolejne stanowisko wiercenia zgłosi zapotrzebowanie na ten element. A pojawiło się ono dlatego, gdyż na końcu strumienia wartości jest już klient, który chce nabyć ten produkt.
Same korzyści dla klientów
Ponieważ na wcześniejszych etapach wdrażania Lean Thinking wyeliminowane zostały przestoje, zbędne zapasy czy niepotrzebny transport, a gniazda produkcyjne są optymalnie ustawione, reakcja na wyciąganie przez klienta produktu następuje szybko, co zapewnia zadowolenie odbiorcy. Realizacja zamówień może zostać skrócona z kilku dni do kilku godzin. Badania wskazały, że zapotrzebowanie odbiorców na wyroby firm, działające według zasad Lean Thinking staje się bardziej stabilne, co dodatkowo ułatwia planowanie produkcji.
Gwałtownie zostaje też skrócony okres wprowadzenia do produkcji nowego asortymentu – w skrajnych przypadkach z kilku lat do kilku miesięcy. Przedsiębiorstwa stosujące zasady szczupłego zarządzania nie muszą martwić się kwestią sprzedania wyprodukowanych już produktów starego typu i wykorzystania istniejących zapasów, gdyż są one minimalne. “Odchudzone” maszyny można szybko i niższym kosztem przezbroić, zaś wszechstronnie wyszkoleni i zaangażowani pracownicy łatwo wdrożą się w nowe obowiązki.
W nieskończoność ku doskonałości
Udane wdrożenie czterech pierwszych kroków szczupłego myślenia sprawia, że piąty krok – dążenie do doskonałości – następuje samoczynnie. To efekt interakcji, jaka zachodzi między określeniem wartości, wyeliminowaniem strat, wprowadzeniem przepływu i zasady wyciągania. Kroki te są ze sobą ściśle powiązane i wzajemnie się napędzają, Menadżerowie wdrażający Lean Thinking zauważają, iż coraz mocniejsze wyciąganie wartości powoduje odnajdywanie kolejnych muda. Eliminowanie nowo odkrytego marnotrawstwa owocuje poprawą przepływu i usprawnia wyciąganie. Coraz dokładniej określana jest również wartość. Filozofia Lean Thinking określa takie nieustanne działania do udoskonalenia procesu mianem Kaizen.
Coraz mocniejsze wyciąganie wartości powoduje odnajdywanie kolejnych muda. Eliminowanie nowo odkrytego marnotrawstwa owocuje poprawą przepływu i usprawnia wyciąganie. Liczy się tutaj nie sama doskonałość, bowiem jej całkowite osiągnięcie nie jest możliwe, ile ciągłe dążenie do doskonałości. Wszyscy zaangażowani, od pracowników, przez zarząd, po dostawców i kooperantów po wdrożeniu zasad szczupłego myślenia zaczynają zdawać sobie sprawę, iż stopniowe zmniejszanie nakładu pracy, eliminowanie usterek, ograniczenie czasu i potrzebnego miejsca będzie trwać w nieskończoność. Widoczna poprawa konkurencyjności na rynku, warunków pracy, zmniejszenie ilości wad i wypadków dadzą jednak motywację do działań Kazien.
Myśleć szczuple do końca
Stosując metody Lean Thinking można wpaść w pułapkę i zatrzymać się na działaniach Kaikau, czyli wyeliminowaniu głównych źródeł marnotrawstwa po zmapowaniu strumienia wartości. Firma już odczuła znaczące zyski, zaś dojście do piątego kroku wymaga długotrwałych starań. Logicznym wydaje się, iż dążenie do doskonałości małymi kroczkami nie da takich efektów finansowych, jak znaczące zmiany wprowadzone podczas Kaikau.
Logika po raz kolejny nie idzie jednak w parze z filozofią Lean Thinking. Womack i Jones na podstawie udokumentowanych przypadków wskazują, że doskonalenie osiągane dzięki Kaizen zazwyczaj powoduje ponowne podwojenie wydajności w ciągu 2-3 lat. Przede wszystkim towarzyszy temu jednak także zmiana mentalności załogi i zarządu, widzących efekty ciągłych zmian.
Siła pracowników
Wdrażając metody Lean Thinking menedżerowie muszą uwzględnić znaczenie pracowników w tym procesie. To oni wykonują pracę, tym samym tworząc wartość. Na stanowiskach pracy najłatwiej zauważyć źródła marnotrawstwa i je eliminować. Zarząd musi zatem zacząć uważnie słuchać pracowników, uwzględniać ich komentarze i odpowiadać na głosy krytyki.
Obawy załogi przed zmianami, jaką niesie ze sobą przejście na nowe zasady działania firmy, są naturalne. Aby je przełamać, niezbędne staje się nieustanne informowanie o celach, jakie przyświecają zmianom oraz prezentowanie efektów. Zyski z wdrażania szczupłego myślenia muszą znać także kooperanci wchodzący w skład strumienia wartości.
Pracownicy widząc, że ich postulaty są brane pod uwagę, a posady nie są zagrożone, zaadoptują filozofię Lean Thinking. Działania Kaizen ze strony załogi można promować, nagradzając zgłaszane usprawnienia. Jeszcze jednym kluczowym elementem Lean Thinking w stosunku do pracowników jest
odpowiednie umiejscowienie ich w organizacji oraz szkolenia zwiększające kwalifikacje. Dzięki temu zapewnione jest utrzymanie przepływu wartości w przypadku okresowo zwiększonego zapotrzebowania na pracę, z powodu większych zamówień czy urlopów. Lepiej wyszkolony pracownik będzie stanie elastycznie zareagować na sytuację w firmie.
Lean Thinking w opiece medycznej
Pomysły na zastosowanie Lean Thinking w opiece medycznej podkreślają, że nie jest to tylko filozofia związana z produkcją – wystarczy poszukać analogii, aby przenieść odpowiednia działania do innej dziedziny. Powszechnie występujący schemat wyspecjalizowanych zakładów opieki medycznej odpowiada tradycyjnemu podejściu do wytwarzania produktu, zaś pacjenci oczekujący w kolejkach do kolejnych specjalistów obrazują produkty oczekujące na obróbkę. Zgromadzenie specjalistów z różnych dziedzin w jednym budynku umożliwi pacjentowi przechodzenie przez zespół działań bez długiego oczekiwania – a zatem mamy przepływ wartości, jaką jest poprawa stanu zdrowia. Dostosować należy też wielkość kartotek, narzędzi i laboratoriów i udostępnić je wszystkim zespołom lekarskim. Skłonienie personelu do poszerzanie kwalifikacji zwiększy ilość problemów, jak uda się rozwiązać w trakcie jednej wizyty. Proces wyciągania ma się z kolei rozpocząć przez zaangażowanie pacjenta w proces leczenia.